This webinar focused on how to avoid costly, unplanned downtime by leveraging condition monitoring in a reliability plan.
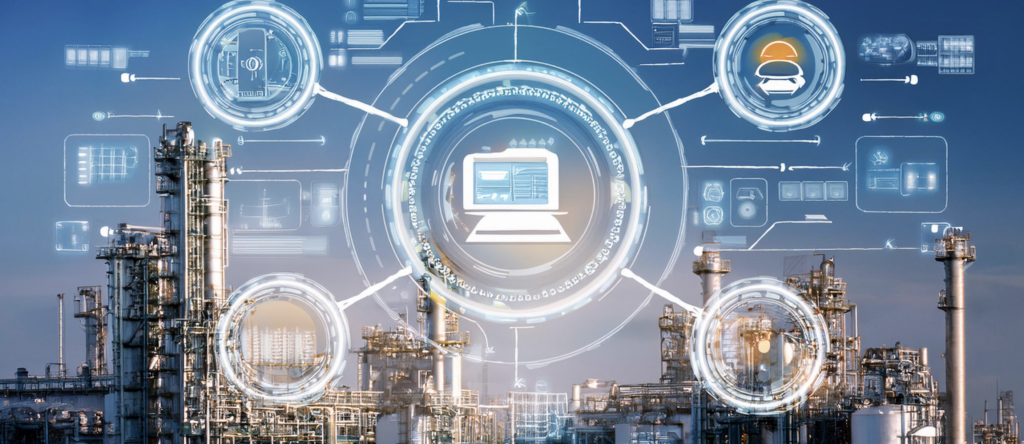
Learning Objectives
- What is condition monitoring, also known as predictive maintenance, and what are the most common technologies?
- Learn about condition monitoring and its techniques and benefits.
- Understand the most common failures (program, management and equipment) and how condition monitoring can alleviate those issues.
- Understand the upfront costs and challenges on the design side and the importance of designing for reliability.
- How to collect data, analyze trends and detect anomalies to provide measurable ROI and actionable information.
In this webinar, John Cray, principal consultant, Life Cycle Engineering, and Witt Parrish, senior mechanical engineer, SSOE Group, explore the shift from manually managed usage-based maintenance to more condition-based or predictive maintenance. Cray and Parrish presented information and case study examples during the October 16, 2024, webinar “Predictive maintenance: What is condition monitoring, and is it a good choice?”
In this article, they address some of the questions that were not answered during the webcast.
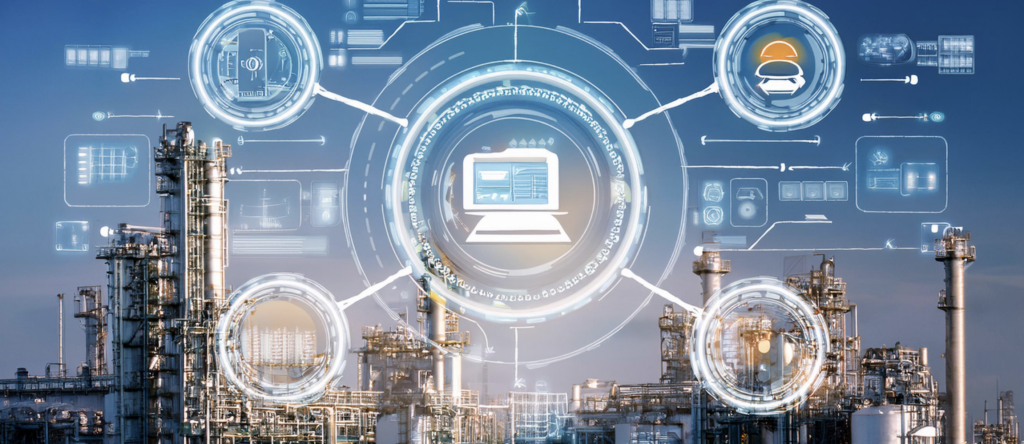
Question: How does condition monitoring apply to electricity and pneumatic efficiency?
Energy meters/power monitoring measure power consumption, power quality, and can detect deviations.
Ultrasonic leak detectors identify compressed air leaks that are too small to be audible. Also, certain sounds emanating from high-voltage electrical equipment. Additionally, condition monitoring allows for timely maintenance, which keeps equipment operating closer to its peak performance without parasitic losses due to increased resistance, air leakage or increased friction or wearing in rotating equipment.
Question: What are the ways to overcome the lack of instrumentation?
There are a number of brands of triaxial sensors that can also be used to transmit to a data collection software source. Several condition monitoring technologies such as vibration, thermography and ultrasonic all have walk-around data collectors/analyzers.
Question: How do we define condition monitoring for a paper manufacturing plant? Does this term include vibration analysis, infrared inspection, ultrasonic testing, electrical panels thermography, etc.?
Condition monitoring technologies are applicable to a wide range of industries including paper. Certainly vibration, thermography and ultrasonic all have application, especially in the paper industry. The new advanced AI software analysis is applicable as well.
Question: How can condition-based monitoring (CBM) help to find the root cause of failure?
CBM monitors changes in condition on a variety of asset types and components. Repeatedly finding condition deviations after each correction / repair is a great lead to conduct a root cause analysis (RCA). CBM can find misalignment for example, it takes RCA to determine why the misalignment keeps showing up after proper correction.
Question: The details of certification have been provided on vibration and thermography. Please provide certification details on the ultrasound testing, lubrication and oil analysis and acoustic emission testing.
Ultrasound Testing and Acoustic Testing: Mobius Institute Board of Certification (MIBoC): Provides independent ultrasound certification in alignment with ISO 18436-8.
Society for Tribologists and Lubrication Engineers (STLE): Provides certifications such as the Certified Lubrication Specialist (CLS) and Oil Monitoring Analyst (OMA)
There are a number of third-party (non-lubricant suppliers) organizations and labs that provide training and certification.
Question: Any resources available for optimizing predictive maintenance programs?
There are a number of consulting firms that specialize in setting up training for new programs, likewise can audit existing programs. Prefer to not promote one over another.
Question: In an industrial setting, how do you draw the line between conditioning monitoring of larger versus smaller assets?
There are many factors to consider, three as follows:
- Criticality rating relative to consequence of failure, such as safety, environment, loss of production
- Single point failure versus in line spare
- Cost of repair
Large, complex machines that are run to failure will cost more to repair than a simple ANSI pump.
Question: Operating companies developed extensive databases of analytics, incident records, etc. EPC companies claim design expertise. Who should drive design evaluation?
Coupling design knowledge with operating experience jointly to make good business decisions is the ideal approach. An owner with good data on their process and facilities operation will know what is working and where they would like to improve in their process. Owner expectations, requirements, and standards should be communicated early in a capital program or project. Engineering, procurement, and construction (EPC) companies can offer valuable experience from other projects that the owner may not have considered to offer new and innovative ideas to the project. It can be advantageous for the owner to delegate the design process to an EPC company that specializes on the process of building or renovating facilities and new installations, so the owner can focus on the process of production, sales, and distribution of their product. Coupling the owner’s and EPC’s experiences can lead to a better outcome than either one alone, as long as there is clear communication of needs and expectations.
Question: What are your thoughts on applying multiple approaches within a facility? Some assets are a fit for CBM or PdM, others are a fit for predictive maintenance and perhaps some assets even are okay to run to failure. How do you decide which approach for each asset?
First, develop a criticality ranking tool that takes into account consequence of failure; such as safety, environment, loss of production, cost of repair, etc.
Develop a maintenance strategy for assets with criticality rating suggested below:
- Top 5% to 10% of critical assets
- 51 to 90 – 95%
- 26-50%
- 0-25%
The top 5% to 10% should receive the maximum application which can be two or more CBM technologies coupled with the appropriate PM. Suggest the 51% to 90-95% utilize standard CBM and PM based on OEM recommendations. The remaining amount can be PM and run to failure.
Question: What is the life span of the sensors used for CBM? And what maintenance program is provided for these sensors?
Searching product literature from several suppliers provided answers ranging from 3 to 5 years depending on the demand on the sensor. Either PM them such as replace batteries every X years or run to failure (stop transmitting).