Artificial intelligence (AI) can help enhance predictive and preventive maintenance in manufacturing, but it’s important for users to know which types are appropriate based on the setting and need.
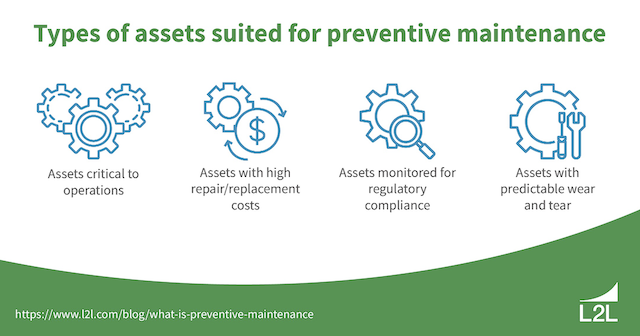
Learning Objectives
- Understand why maintenance is important to a manufacturing facility and how much it costs annually overall.
- Know the difference between predictive and preventive maintenance and when to apply one over the other.
- Understand how data and artificial intelligence (AI) can improve maintenance regardless of which one is used.
Predictive and preventive maintenance insights
Implementing AI-powered predictive and preventive maintenance helps manufacturers avoid unplanned downtime, which costs the industry $50 billion annually, by monitoring and maintaining equipment proactively.
Predictive maintenance extends equipment lifespan and reduces spare parts storage, while preventive maintenance relies on regular schedules, both essential for optimizing manufacturing operations and cost-efficiency.
Keeping equipment up and running safely is no small feat, especially considering the costs associated with maintenance and downtime. Unplanned downtime costs manufacturers an estimated $50 billion every year, which means the right approach to maintenance can make or break a business. But waiting for total equipment failure and fixing it with reactive maintenance isn’t a sustainable solution. This can lead to missed quotas during key manufacturing cycles, shortened lifespans of critical equipment, and overworked maintenance technicians.
To stay one step ahead of potential equipment failure, manufacturers should implement a combination of predictive and preventive maintenance. As AI-powered technology becomes more widely accessible, it’s enhancing maintenance processes across the board. Let’s explore what these approaches entail, the equipment best suited for each, and how optimizing them via AI-powered connected workforce technology can maximize factory uptime.
What is predictive maintenance?Â
Predictive maintenance helps manufacturers stay ahead of necessary repairs by monitoring asset and component conditions in real time. With system-generated data triggering repair notifications, teams can jump in to perform maintenance once sensors, programmable logic controllers (PLCs) and other applications notify them that a part of their equipment is failing or about to fail. It’s a smart, artificial intelligence (AI)-based way to let engineers know when equipment needs repairs.
Predictive maintenance happens in three key phases.
-
Inspection: These are processes users go through on a regular basis to monitor the condition of the machine’s components. Frequent inspections may include vibration, temperature and oil analyses. Another approach involves real-time monitoring of things like pressures, flow rates, and temperatures via measuring devices attached to the equipment itself.
-
Direction: New predictive maintenance platforms are able to use real-time data analysis to give organizations quicker decision-making capabilities. Once enough data is accumulated from regular inspections, it’s time to decipher what that information means. What are the failure criteria for this equipment? Establish parameters based on past performance history, manufacturer recommendations, and thorough failure mode and effects analysis (FMEA) to build the inspection criteria.
-
Corrective actions: Define a maintenance plan for this equipment based on the data analysis and set parameters. Adhere to the plan and complete the maintenance needed during strategically planned downtime. AI-powered software can assist here by analyzing this data and making proactive recommendations for corrective actions.
Predictive maintenance offers many benefits to an organization. First, it cuts down on costs by prolonging the asset’s life and reducing the need for spare parts storage. Instead of cluttering the warehouse with extra components, predictive maintenance inspections allow companies to order parts as needed when potential problems are detected. Furthermore, when inspections are performed during normal runtime or equipment is monitored in real time, companies save on labor costs associated with production downtime.
Predictive maintenance works best when installed in critical, high-value machines. Consider every piece of equipment onsite: If this specific piece of equipment fails, how much do you stand to lose when it’s taken out of commission?
Installing predictive maintenance software won’t provide much value if the asset it’s monitoring isn’t suitable. For example, if a company is keeping tabs on a large fan in one of the curing units. It’s a comparatively cheap piece of equipment performing a relatively low-value task, which means the cost of predictive maintenance might not be practical.
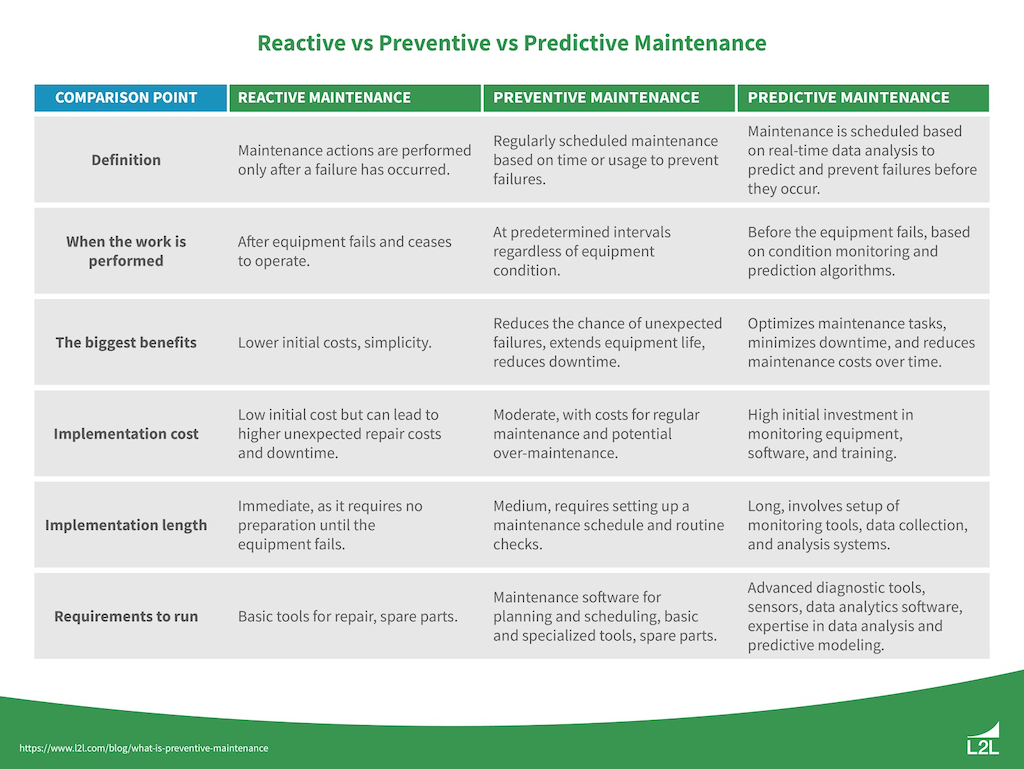
On the other hand, complex systems, large-scale machinery and safety-critical equipment would be better suited for a predictive maintenance program. For other assets, users will want to consider implementing preventive maintenance.
What is preventive maintenance?Â
Preventive maintenance is all about being proactive. This strategy relies on regular, scheduled maintenance efforts to prevent unexpected failures and breakdowns. These systems are quite common today due to their low cost and ease of implementation, but many facilities desperately need to streamline their approach with the help of digital technology.
Preventive maintenance is especially crucial for industries that rely on complex and expensive machinery like manufacturing. In practice, it involves adhering to a systematic schedule based on usage metrics or a predetermined timeline. Common applications include:
-
Lubrication
-
Cleaning
-
Inspections
-
Adjustments
-
Part replacements
-
Calibration
-
Testing
-
Software updates
-
Electrical system checks
-
Safety checks.
There are two main types of preventive maintenance and both require thoughtful planning and detailed documentation of maintenance history to ensure future success. Most manufacturers will use a combination of the two based on the needs and operating conditions of different assets.
-
Cycle-based preventive maintenance: This approach is dictated by how many production cycles an asset has gone through. It serves machines based on how much they’re used rather than following a time-bound schedule. By tracking metrics like products made or hours active, teams can prevent excessive wear and tear, reduce excessive maintenance, and optimize resource allocation. An AI-powered connected workforce platform can track production and maintenance data automatically to make this process seamless within one system. Examples include scheduling a robotic arm for maintenance after it completes 80,000 cycles or checking packaging equipment for wear after it has sealed 50,000 boxes.
-
Calendar-based preventive maintenance: This approach is determined by standard calendar dates. Repairs begin after a set amount of time has passed, whether that’s daily, weekly, monthly, or yearly. The exact interval will depend on the tool in question, how frequently it’s used, its operating conditions, and existing regulations from governing bodies. For example, safety equipment like fire extinguishers and emergency lights need to be checked and tested every six months to comply with safety regulations. Meanwhile, HVAC systems may need to be serviced annually in preparation for their peak usage seasons.
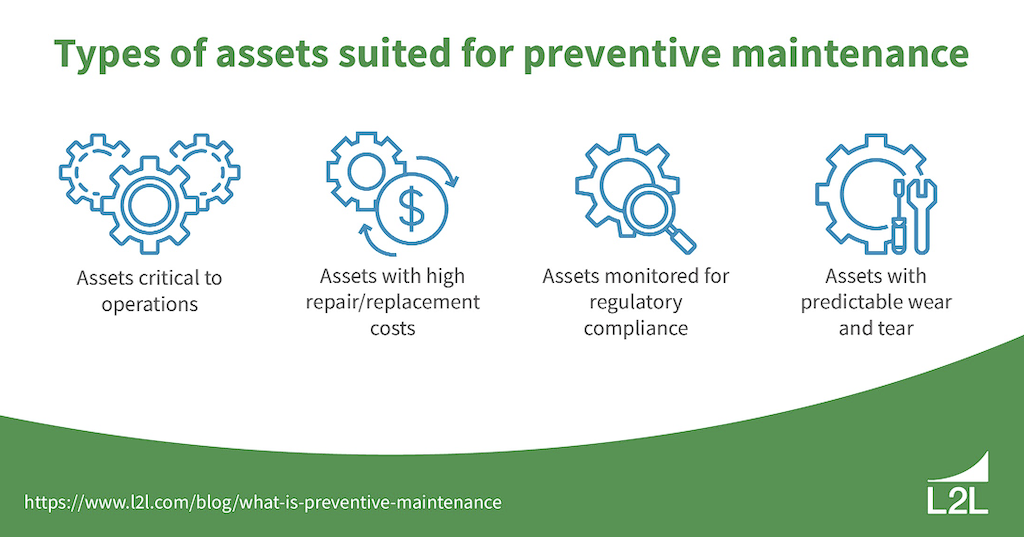
Companies need a strategic approach to get the most out of preventive maintenance. Identify and prioritize assets based on their production impact — focus on the equipment that would cause the biggest operational disruptions or safety hazards. The assets best suited for preventive maintenance are those critical to operations and monitored for regulatory compliance. Assets with high repair or replacement costs and predictable wear and tear are suitable candidates, as well.
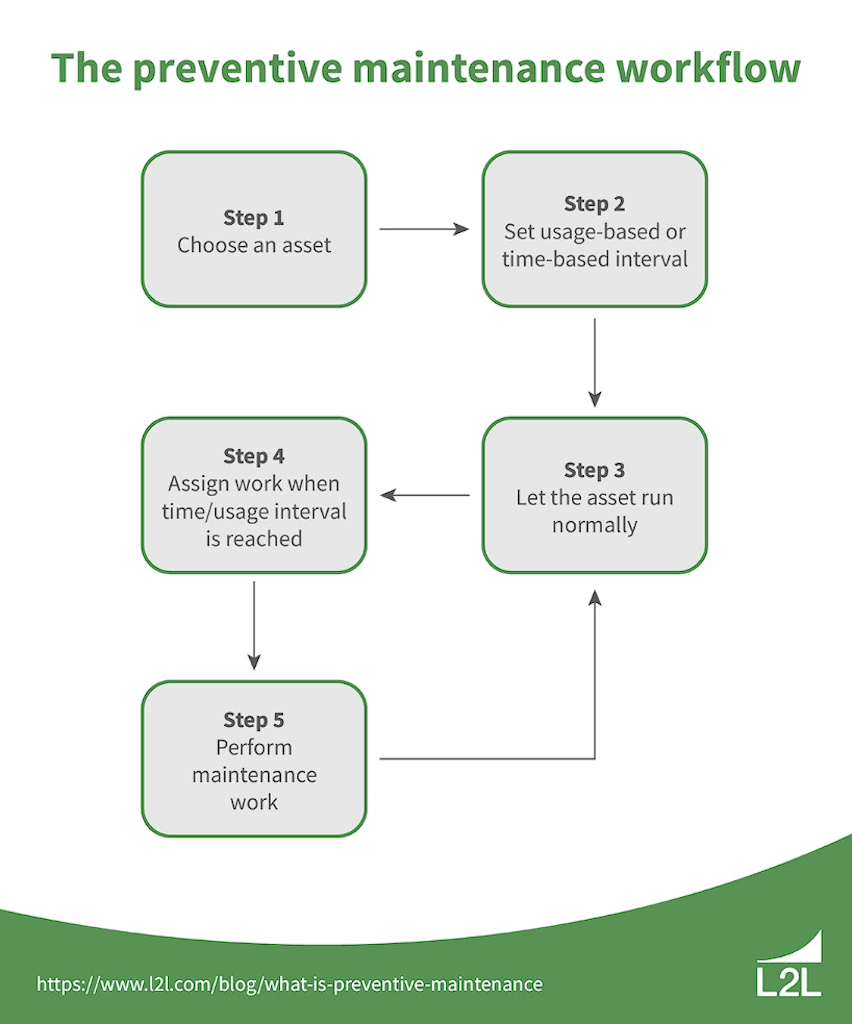
Once it’s decided on which equipment qualifies for the type of maintenance create a plan complete with tailored schedules, procedures and checklists for each asset. Implementing preventive maintenance software can help users keep track of what needs to be done and execute on standardized procedures. Maintenance teams need to be adequately trained on and equipped with the right tools and parts to complete the tasks they’re assigned. Introducing the proper software is one such method to ensure they’re set up for success, and it’ll allow for a deeper analysis of the information and data at hand.
Unlocking the power of data for better maintenance
Data is the best defense we have against unplanned downtime and repair costs. Knowing exactly what, when and how to perform maintenance on equipment is vital, but keeping track of all this information without the assistance of software is nearly impossible in today’s digital-first environment.
AI-powered connected workforce platforms with predictive and preventive maintenance software baked in have emerged as a solution. Such platforms empower skilled trades with the information they need to act efficiently and effectively by giving them the ability to plan, schedule, run, and track maintenance activities through a centralized system.
By notifying technicians when a piece of equipment needs to be inspected, this technology helps ensure maintenance tasks are completed on time and correctly before the asset breaks down.
Consolidating machine and equipment data within a single dashboard gives maintenance technicians easy access to information, the tools and parts they need, and any important operator notes. The right AI-driven platform won’t just send automatic notifications or capture data in real time; it also will give technicians the ability to analyze trends for better decision-making, ultimately improving the plant’s processes and productivity while reducing technician frustration.
While there’s no surefire way to guarantee equipment will never break down unexpectedly, manufacturers can cover their bases with a methodical combination of predictive and preventive maintenance. And by supplementing these efforts with AI-powered software rather than relying solely on manual processes and documentation, leaders can implement transparent and efficient maintenance procedures for every piece of equipment in operation.
Reactive maintenance will always be necessary to some extent, but manufacturers can cut down on their need to play catch-up by investing in tools that enable a reliable blend of predictive and preventive maintenance.