Many safety and productivity risks in material handling are being averted through the adoption and integrating of IIoT technologies.
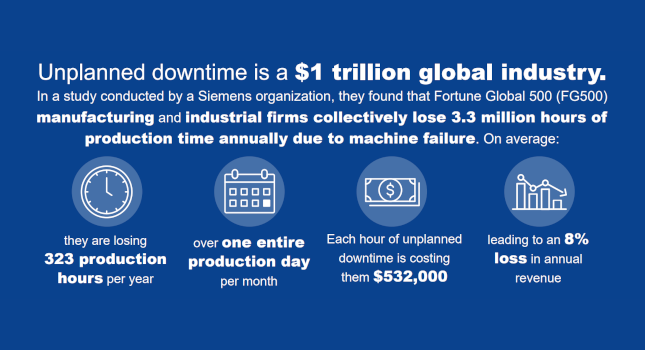
Predictive maintenance insights
- Realtime data and remote monitoring benefits include enhanced equipment reliability, reduced downtime and improved analytics-driven decision-making.
- The integration of IIoT technologies optimizes maintenance strategies for more efficient material handling operations.
Material handling involves the short-distance transportation of materials within manufacturing, warehousing and distribution settings. For decades, this industry has depended on manual labor and equipment. However, through emerging technologies, many safety and productivity risks are being averted through the adoption of semi and fully-automated equipment.
According to a 2018 MHI Annual Report, investment in automation and robotics for material handling will result in an increase from a current 34% adoption rate to a 73% adoption rate within the next five years. This includes automated mobile robots and automated conveyor systems for sorting, picking, packing and palletizing applications. With new processes and technology come new maintenance strategies. Optimizing these strategies is crucial for the success of your team’s productivity and overall safety.

The cost of unplanned downtime
The below stats are staggering and relative across organizations of all shapes and sizes. And revenue loss is not the only impact being made; 70% of workplace injuries occur during reactive maintenance. Due to these economic factors, a culture of expediting maintenance to get a plant back up and running as soon as possible often results in injuries due to unpreparedness. Maintenance teams are applied pressure to work quickly, which can result in ignoring their training, safety codes, and human error. These risks can be mitigated with a culture that adopts predictive maintenance solutions that allow maintenance teams to be more prepared and more secure with their planning and execution of tasks.
Automated conveyor systems maintenance
The continuous flow of conveyors enables materials to be transported over relatively long distances. However, the stress put on these mechanical machines over such lengths of time can result in a breakdown when least expected. Troubleshooting can be a tedious and arduous task as pinpointing the exact location of failures is difficult.
Due to the continuous demand for uptime, the machinery is known to be subject to wear and tear on critical points like bearings and, in many cases, can be overly maintained due to breakdown fears. In the event of a breakdown, an organization faces a considerable loss of production due to unplanned downtime. Delays in getting the machinery back up and running often occur due to unpreparedness and a lack of replacement parts. Furthermore, personnel safety is at much greater risk during events of reactive maintenance.
Within the materials handling space, IIoT opportunities for automated conveyor systems have the potential to house integrated intelligent devices to monitor critical failure points. These devices can not only share data insights about impending failures but can also support worker safety by preventing a reactive maintenance scenario. Instead, maintenance teams are well-equipped and better prepared to execute and prioritize their tasks.