The use of industrial Internet of Things (IIoT) predictive maintenance technology is becoming increasingly important for businesses that rely on rotating equipment such as motors, pumps and fans

Learning Objectives
- Understand the basics of industrial internet of things (IIoT) predictive maintenance and its potential benefits for businesses that rely on rotating equipment.
- Learn about the risks and costs associated with unplanned downtime due to equipment failure and how IIoT predictive maintenance can help prevent these issues.
- Explore common questions and hesitations associated with adopting IIoT predictive maintenance solutions and learn strategies for overcoming these concerns and making a strong business case for implementing this technology.
Predictive condition monitoring insights
- Predictive condition monitoring technology can help companies avoid costly unplanned downtime, increase productivity and safety and improve the return on investment for their maintenance programs.
- This article will explore the benefits of industrial internet of things predictive condition monitoring for maintenance programs, address common questions and hesitations that customers may have and provide insights on how businesses can integrate this technology into operations.
Maintaining equipment is essential to ensure optimal performance, reduce downtime and avoid costly repairs. Traditionally, maintenance programs have relied on periodic inspections and reactive repairs, resulting in lost productivity and increased costs. However, with the advent of industrial internet of things (IIoT) predictive condition monitoring, businesses can now use data to proactively identify potential issues and address them before they result in downtime.
Current maintenance programs and risks of unplanned downtime
Many businesses still rely on periodic inspections and reactive repairs as their primary maintenance strategy. This approach is time-consuming and inefficient, as it requires shutting down equipment and manually inspecting components. In addition, it is not always effective at identifying potential issues before they cause downtime, leading to lost productivity and increased costs.
Unplanned downtime due to equipment failure is a major risk for businesses, resulting in lost revenue, decreased productivity and increased repair costs. For example, a motor failure can result in the shutdown of an entire production line, causing delays and lost revenue. The longer the equipment remains offline, the greater the cost to the business. In addition, reactive repairs are typically more expensive than proactive maintenance, as they require emergency repairs and expedited shipping of replacement parts.
Three benefits of adding predictive condition monitoring
IIoT predictive condition monitoring can help businesses address these risks by proactively monitoring equipment and identifying potential issues before they cause downtime. By adding smart devices to equipment such as motors, pumps and fans, businesses can collect real-time data on equipment performance and use advanced analytics to identify potential issues before they cause equipment failure. This proactive approach can result in significant cost savings, increased productivity and extended equipment life.
1. Enhancing maintenance teams to be more responsive: IIoT predictive condition monitoring can enhance the responsiveness of maintenance teams by providing real-time data on equipment performance. This data can help teams identify potential issues and address them before they result in downtime, reducing the need for reactive repairs and emergency shutdowns. In addition, the use of advanced analytics can help maintenance teams prioritize their workload and focus on the most critical issues, improving efficiency and reducing downtime.
2. Extending the life of equipment: IIoT predictive condition monitoring can help businesses extend the life of their equipment by identifying potential issues before they result in equipment failure. By proactively addressing issues such as vibration, temperature and fluid levels, businesses can reduce wear and tear on equipment and avoid costly repairs. In addition, the use of predictive maintenance can help businesses schedule repairs and replacements at a time that is most convenient, reducing downtime and lost productivity.
3. Return on investment (ROI) for condition monitoring devices: While the initial investment in IIoT predictive condition monitoring devices may seem significant, the long-term ROI can be significant. By reducing downtime, avoiding emergency repairs and extending the life of equipment, businesses can save money in the long run. In addition, the use of predictive maintenance can help businesses optimize their maintenance schedules, reducing the need for periodic inspections and reactive repairs. This can result in significant cost savings and increased productivity.
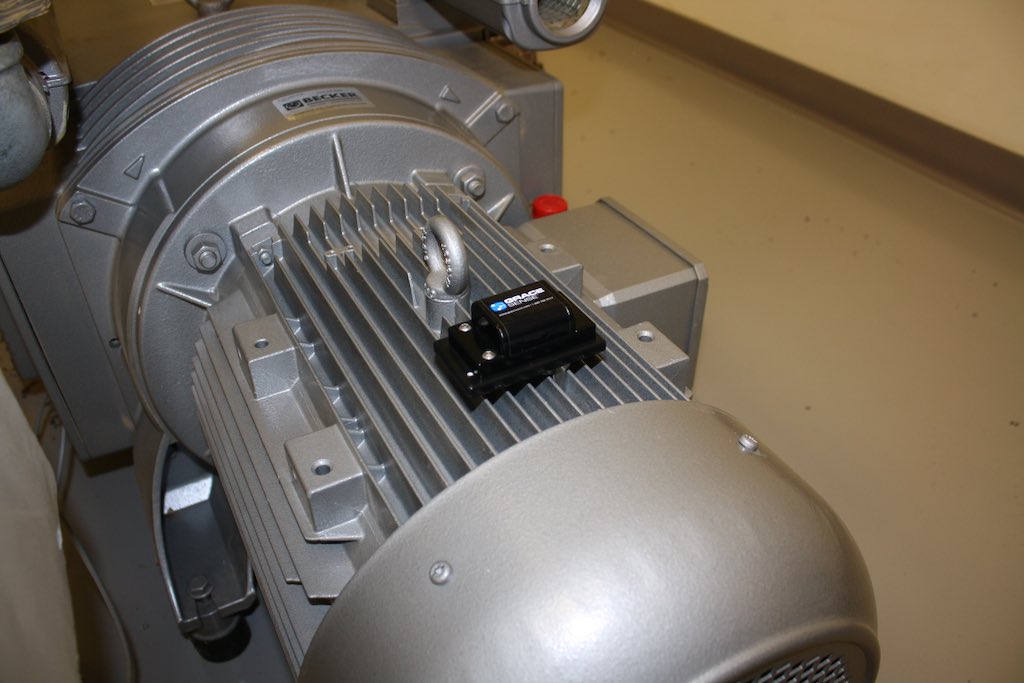
Common misconceptions about IIoT predictive condition monitoring
Despite the benefits of IIoT predictive condition monitoring, some customers may still have concerns or misconceptions about the technology. Common concerns include cost, complexity and reliability issues.
-
Addressing cost concerns: The initial investment in IIoT predictive condition monitoring devices can be significant, but the long-term ROI can be significant. By reducing downtime and extending the life of equipment, businesses can save money in the long run. In addition, many IIoT predictive condition monitoring solutions offer flexible pricing models, allowing businesses to scale their investment as needed. This can help businesses to manage their costs and ensure that they are only paying for what they need.
-
Addressing complexity concerns: Some businesses may be hesitant to adopt IIoT predictive condition monitoring due to concerns about complexity. However, many IIoT solutions are designed to be easy to install and use, with minimal technical expertise required. In addition, many solutions offer user-friendly interfaces and dashboards that provide real-time insights into equipment performance. This can help businesses to quickly identify potential issues and take proactive measures to prevent downtime.
-
Addressing reliability concerns: Reliability is a key concern for businesses when it comes to adopting IIoT predictive condition monitoring. However, many IIoT solutions are designed with reliability in mind, using advanced analytics and machine learning algorithms to detect potential issues before they become critical. In addition, many solutions offer redundancy features, ensuring that data is always available even in the event of a system failure.
Overcoming implementation challenges
While IIoT predictive condition monitoring can provide many benefits for businesses, it is important to recognize that there may be challenges associated with implementing these solutions. Here are some key challenges businesses may face and how they can be overcome:
-
Integration with existing systems: One of the biggest challenges businesses may face is integrating IIoT predictive condition monitoring solutions with their existing systems. To overcome this challenge, it is important to choose a solution that is compatible with your current infrastructure. Many IIoT solutions offer application programming interfaces and other integration tools that can help streamline the integration process.
-
Data management: Another challenge businesses may face is managing the large amounts of data generated by IIoT predictive condition monitoring solutions. To overcome this challenge, it is important to have a clear data management strategy in place. This may include setting up automated data collection and analysis processes, as well as investing in data storage and analysis tools.
-
Training and adoption: Finally, businesses may face challenges related to training and adoption. While IIoT predictive condition monitoring solutions are designed to be easy to use, it is important to ensure that maintenance teams are trained on how to use them effectively. This may include offering training sessions and providing ongoing support to ensure that teams are comfortable using the new technology.
In addition to these challenges, it is important to recognize that IIoT options are not a one-size-fits-all solution. It is important to work with a provider who can help select the right solution for specific needs and provide ongoing support as needed. While there may be challenges associated with implementing these solutions, these can be overcome with the right strategy and support. By choosing the right solution and working with a provider who can offer ongoing support, businesses can maximize the benefits of IIoT and gain a competitive edge in today’s rapidly changing industrial landscape.
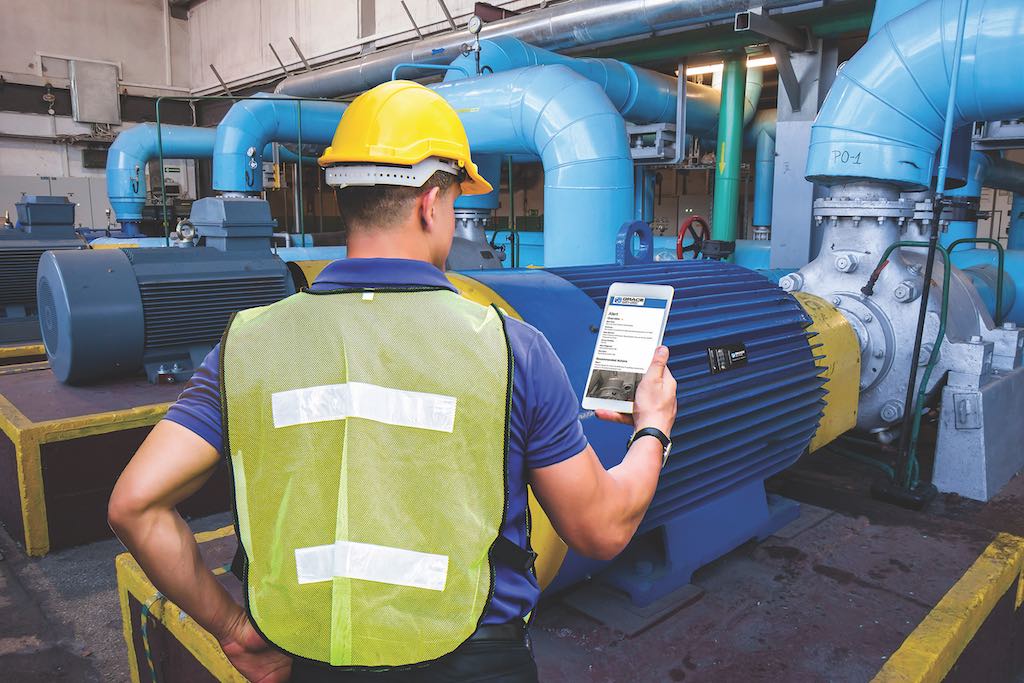
The ROI of IIoT predictive maintenance
The benefits of IIoT predictive maintenance go beyond just preventing downtime and extending the life of equipment. These solutions can also have a significant impact on safety and productivity. Here are some statistics that demonstrate the ROI of IIoT predictive maintenance:
-
Improved safety: According to a study by the National Safety Council, workplace injuries cost businesses more than $161 billion per year. By adopting IIoT predictive maintenance, businesses can reduce the risk of equipment failure and associated accidents, improving overall workplace safety.
-
Increased productivity: Downtime caused by equipment failure can have a significant impact on productivity. According to a study by Aberdeen Group, unplanned downtime can cost businesses up to $260,000 per hour. By preventing downtime through IIoT predictive maintenance, businesses can increase productivity and reduce the risk of lost revenue.
-
Cost savings: Finally, IIoT predictive maintenance can provide significant cost savings for businesses. According to a study by Deloitte, companies that implement predictive maintenance can expect to see a 10%-20% reduction in maintenance costs, a 20%-25% reduction in equipment downtime and a 5%-10% increase in production capacity.
These statistics demonstrate the significant ROI that IIoT predictive maintenance can provide for businesses. By preventing downtime, improving safety, increasing productivity and reducing costs, businesses can gain a competitive edge in their industry and improve their bottom line.
IIoT can be a powerful tool for preventing equipment failure, improving safety and increasing productivity. By leveraging advanced analytics and machine learning algorithms, these solutions can detect potential issues before they become critical, enabling businesses to take proactive measures to prevent downtime. In addition to the benefits of preventing downtime, IIoT predictive maintenance can provide significant cost savings, improving the overall ROI of these solutions.
By choosing the right solution and working with a provider who can offer ongoing support, businesses can maximize the benefits of IIoT predictive maintenance and gain a competitive edge in today’s rapidly changing industrial landscape.
IIoT will provide businesses with a proactive approach to maintenance, enabling them to identify potential issues before they result in downtime. By enhancing the responsiveness of maintenance teams, extending the life of equipment and providing a strong ROI, IIoT predictive condition monitoring can help businesses to reduce costs, increase productivity and improve overall performance. Despite concerns about cost, complexity and reliability, many IIoT solutions are designed to be easy to use and reliable, providing businesses with a simple, stress-free integration process. By adopting IIoT predictive condition monitoring, businesses can gain a competitive edge, ensuring that their operations are running smoothly and efficiently.