Like basketball, businesses need everyone to work together to achieve the same goal and improve the company. A five-step continuous improvement cycle can help.
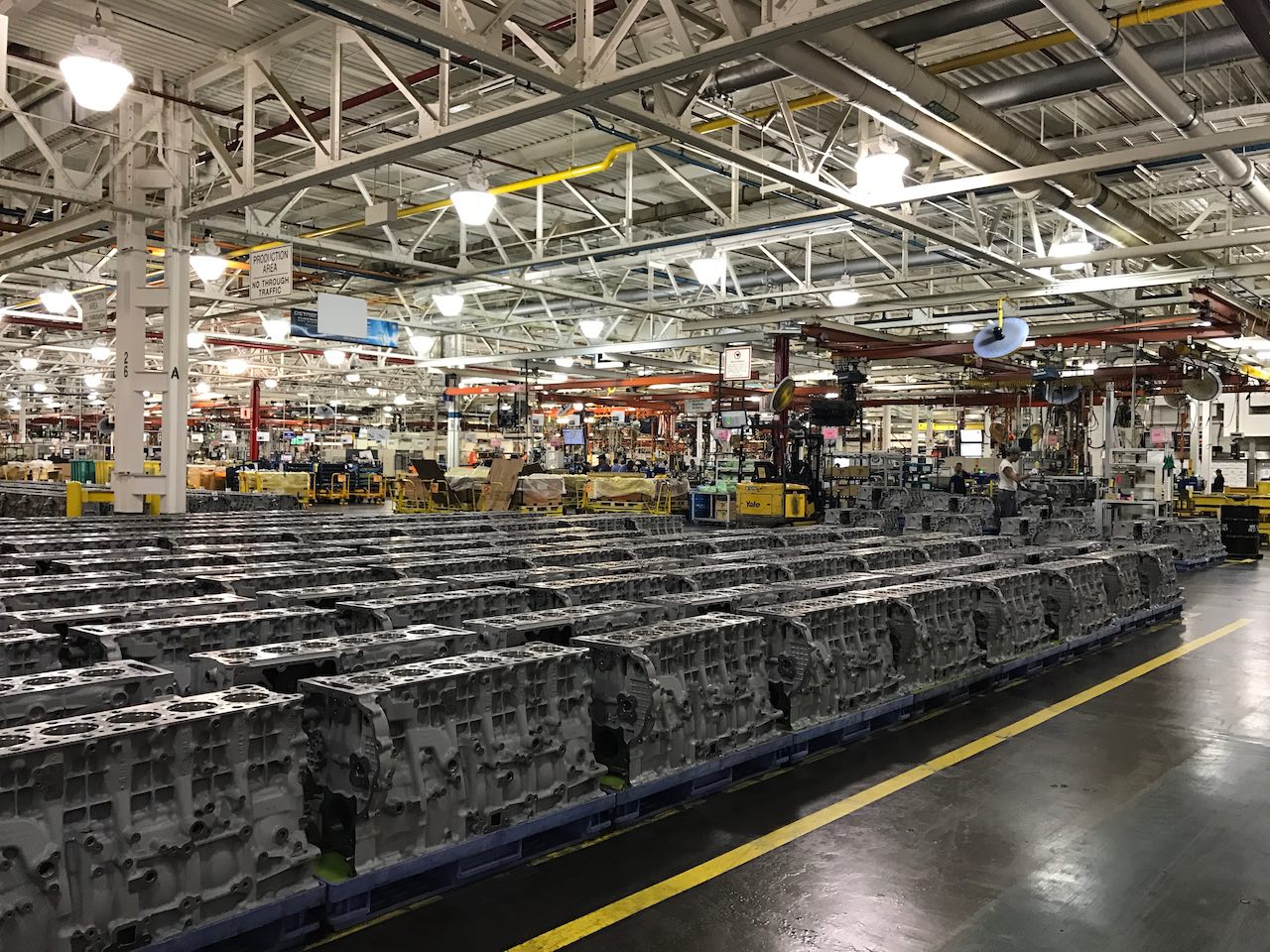
Summer is a great time for a pick-up game of “5 on 5” basketball. When playing a game of “5 on 5” in basketball, the key to success is for the team to work well together, utilize the strengths of each player and repeatedly work their process as defined by the coach.
As the process is repeated over and over again through the course of the season, the really great teams “develop a chemistry” which is something that is unseen and unquantifiable, but which gives the team an edge over its competition that leads to success.
The same is true in the business world if a company wants to improve and succeed.
A business team needs to work well together, utilize the strengths of each of the team members and use a process that is repeated over and over. The following continuous improvement cycle used repeatedly will lead to a new “chemistry” within the organization so that the culture begins to change to one of continuous improvement.
The 5-step continuous improvement cycle
Creating a continuous cycle is a hard journey, but breaking it down and taking it one step at a time (and taking each part one step at a time) will be rich and rewarding for companies.
Step 1: Define
-
Identify the target process
-
Organize and empower an improvement team
-
Describe the issues, concerns or opportunity
-
Collect current performance data
-
Create a process map
Step 2: Identify
-
Identify the process customers and suppliers
-
Define the process inputs and outputs
-
Define the process requirements
-
Identify wastes and value-added activities
-
Generate a list of potential improvements
Step 3: Select
-
Establish desired performance goals
-
Prioritize the potential solutions
-
Establish the selection criteria
-
Select the best solution(s)
-
Define the desired process
Step 4: Implement
-
Develop an action plan to achieve the goals
-
Develop process performance metrics
-
Document the solutions(s)
-
Test the changes
-
Implement per the action plan
Step 5: Evaluate
-
Establish ongoing feedback
-
Measure progress per the action plan
-
Compare results with desired performance goals
-
Determine corrective actions that need to be taken
-
Repeat the cycle to define new opportunities
The key to really being successful using this process is the very last step – going back to the beginning and looking for new opportunities. Without this, it is a one-time change, not continuous improvement. All too often, companies declare victory when a change is complete and sit back for the new status quo to set in rather than taking another look at things to find more opportunities.
Key Benefits of Process Improvement
By using this cycle on a formal basis over and over as problems or opportunities are addressed in the organization, inherent use of the cycle will begin to occur since people will become accustomed to it and the culture of the organization will begin to embrace the idea of continuous improvement.
This resulting chemistry that begins to develop will be unseen and unquantifiable but will provide an edge for the organization so that it can succeed within itself and against the competition.
Whether a company is going down the path of Lean enterprise performance, implementing an enterprise resource planning (ERP) business system, or making improvements in some part of the organization, this five-step cycle can be quite valuable.
It can be a quick blitz to accomplish a focused task or a longer term assignment that is making a more significant change in the organization. Regardless, this 5-step process provides the structure needed for making the improvement.
Ultra Consultants, a CFE Media content partner, is a leading independent research and enterprise solutions consulting firm serving the manufacturing and distribution industries throughout North America. Ultra delivers enterprise technology expertise and process management to drive business performance improvement for their clients. This article originally appeared on Ultra Consultants’ blog.