Here are five basic tips that everyone could be applying to increase productivity and achieve more ‘bang for their buck’ when it comes to steam systems.
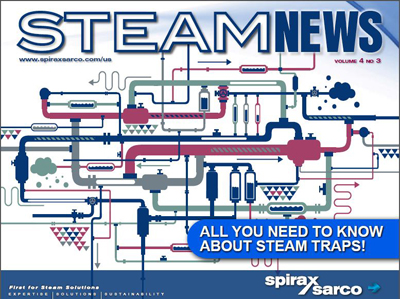
Steam systems are generally efficient and reliable. Organizations that use steam come in all shapes and sizes, from industrial facilities and office buildings to hospitals and universities. But these days they all have one thing in common, and that’s the need to make every penny count. There are five basic tips that everyone could be applying to increase productivity and achieve more ‘bang for their buck’.
1. Water Supply to Steam Systems
The basic starting point for any efficient steam system is a clean water supply. Raw water can contain a whole range of impurities, and any number of these can have a negative impact on the performance of steam systems. The most common impurities in raw water include dissolved solids and gases, suspended solids and scum-forming substances. The damage they cause typically falls into three categories:
-
Corrosion is the biggest issue with dissolved gases, especially oxygen and carbon dioxide in the form of carbonic acid. In fact, if carbonic acid and oxygen are present, then the rate of corrosion rises by about 10%. Meanwhile, sodium hydroxide can cause caustic cracking and metal failure.
-
Deposits are another challenge and tend to build up if the alkalinity of the feedwater is not controlled. For example, a layer of deposits just one millimeter thick can reduce boiler efficiency by 10%, disrupting effective heat transfer.
-
Foaming can be caused by a build-up of total dissolved solids (known as TDS) in the boiler. Foam forms in the space between the water surface inside the boiler and the steam off-take. This initially causes problems in the boiler, where it makes it tricky to gauge the water level, but it can also lead to carryover of boiler water into the steam distribution system, where it can interfere with heat transfer and cause waterlogging.
Effective water treatment tackles these problems at source. The traditional approach uses water softening supplemented by chemical treatment. More recently, reverse osmosis (RO) is also becoming increasingly popular. RO forces water through a semi-permeable membrane to strip out nearly all the contaminants. The resulting pure water will have had 98-99% of its salts removed.
2. Correct Boiler Control in Steam Systems
Having the right controls is a crucial ingredient in the optimization of any steam system. Level controls ensure sufficient water is fed to the boiler to meet demand. Lower water levels mean the heating surfaces could become exposed and the boiler would overheat. Too high, and water could be sucked into the steam, leading to poor quality steam that could impair heating or production efficiency and increase the risk of waterhammer.
Better boiler controls deliver major savings, especially in the area of boiler blowdown. Boiler blowdown periodically ejects water from a boiler to prevent the build-up of contaminants, with two varieties: side blowdown (to control total dissolved solids) and bottom blowdown (to control sludge in the bottom of the boiler). It’s essential to deliver clean, dry steam, but it’s potentially very wasteful. Switching from manual opening of the blowdown valves to automatic blowdown controls can deliver a rapid return, paying for itself in a matter of months.
3. Effective Heat Transfer in Steam Systems
Whether steam is used to drive an industrial process or provide heating and hot water, effective heat transfer is critical for almost every installation. So the most efficient heat exchangers should be a priority. Traditional shell-and-tube calorifiers look increasingly outdated compared to more efficient, compact alternatives. Plate heat exchangers typically improve energy efficiency by around 6-10%, simply by reducing radiation heat losses from their surfaces. These compact systems can be so responsive that some of them can tailor their output on-demand.
4. Condensate Recovery in Steam Systems
Condensate contains roughly 20% of steam’s energy, which makes it a particularly valuable resource. Most systems could achieve a condensate recovery rate of 75- 80%, thus saving thousands of dollars a year in energy alone. Using hot condensate to heat the boiler feedwater means the boiler has less to do in converting the water to steam and every 43°F boost in boiler feedwater knocks 1% off a typical boiler energy bill. Any condensate return to the boiler feedtank reduces the need for blowdown, helping to lower the energy lost during the blowdown process. When it comes to condensate recovery, each steam system is different and only a technical assessment and cost saving calculation can determine the payback of a particular project. However, typically the payback is between one and two years, with some measures paying for themselves in weeks.
5. Service and Support of your Steam System
With the much-discussed skills gap affecting many organizations, and in-house assets and maintenance personnel facing increasing demands on their time, calling on specialists to provide service and support for the steam system can be the most realistic, cost-effective route to maximize productivity.
Many of the measures described within this article are either low or no-cost and even when a significant upfront investment is needed, you really should start seeing the benefits almost immediately.
Content provided by Spirax Sarco, originally published in Steam News. Edited by Anisa Samarxhiu, Digital Project Manager, CFE Media, [email protected]