Learn about the critical role of maintenance management in the power and energy industry, and how CMMS can be used
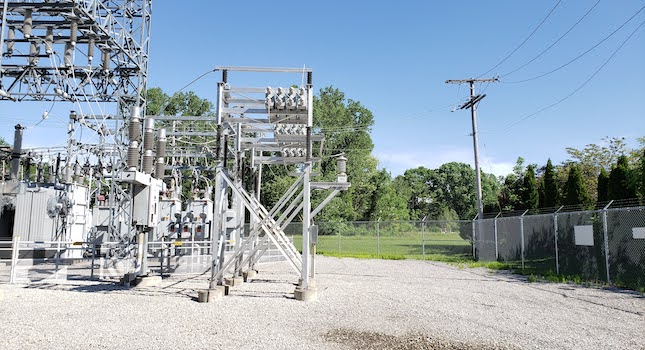
Learning Objectives
- Understand the significance of maintenance in the power and energy industry.
- Appreciate the role of computerized maintenance management system (CMMS) software in this industry.
- Identify maintenance challenges, and how CMMS can help anticipate them.
CMMS insights
- Plant managers should know the importance of maintenance in ensuring uninterrupted energy services and maximizing energy output.
- The article highlights the integration of CMMS with SCADA systems, preventive maintenance strategies, smart inventory management and analytics-driven decision-making as ways to enhance efficiency and reduce energy consumption in the industry.
Maintenance isn’t just important, it’s crucial across all sectors involved in generating, consuming and distributing energy. Energy companies are often at the forefront of maintenance practices, using computerized maintenance management system (CMMS) software to keep operations smooth. Renewable energy production requires top-notch maintenance to balance profitability and sustainability. Companies engaged in wind, solar or geothermal energy prioritize CMMS to optimize their production tools.
Power plants, the engine rooms of the U.S. energy supply, demand meticulous maintenance to keep them humming. Whether fueled by coal, nuclear reactions or water, power plants need continuous maintenance to ensure safe and efficient energy production. Power plant maintenance engineers oversee this intricate dance of maintenance tasks to meet industry standards. Swift problem resolution is vital, as unaddressed issues can escalate into emergencies.
Power plant maintenance includes corrective and preventive measures, covering equipment like gas-powered turbines and boilers. The goal is to maintain optimal plant load factor, which measures a plant’s capacity use and its contribution to the grid.
Renewable energy, particularly wind power, offers a clean alternative to traditional sources. Yet, the substantial costs associated with manufacturing and maintaining wind turbines pose challenges. Maintenance expenses for a megawatt of wind power can range from $42,000 to $48,000. Keeping these towering turbines in peak condition is key to managing costs.
Wind turbine maintenance involves regular lubrication of components like gearboxes and bearings. Technicians perform regular checks on the connections between blades and systems. Many turbines use predictive maintenance, sending alerts when maintenance is due. Given the heights at which these technicians work, safety remains paramount.
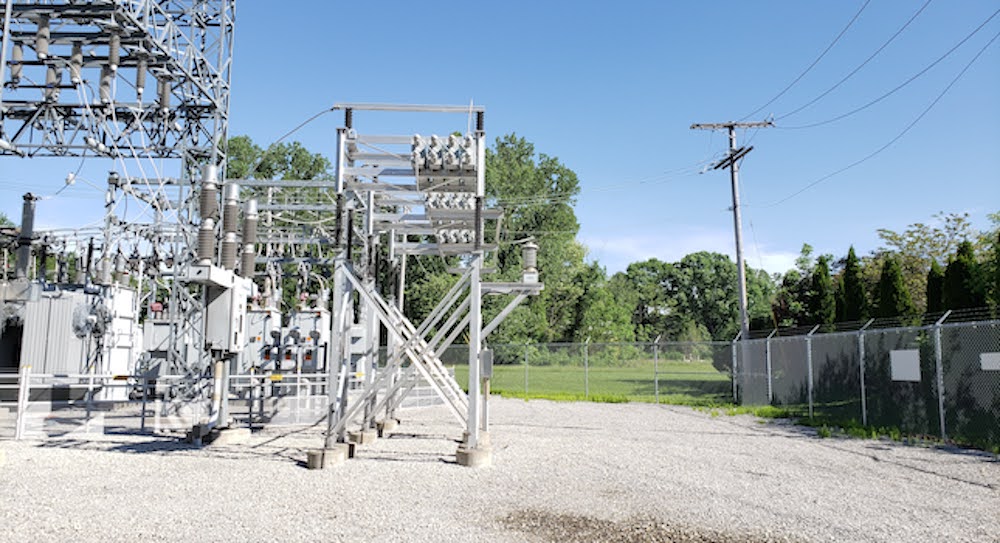
Power and energy maintenance challenges
The power and energy sector confronts unique maintenance challenges. Safety, regulatory compliance and equipment monitoring are at the forefront.
Safe and steady energy production: Facilities like nuclear plants must maintain stringent safety procedures to operate smoothly. Compliance with regulations, like those from Occupational Safety and Health Administration, Environmental Protection Agency and Federal Energy Regulatory Commission, is important.
Vigilant equipment monitoring: Compared to nuclear plants, wind farms demand more frequent equipment monitoring. Preventive maintenance schedules must be meticulously planned, adapting best practices from other industries.
Navigating regulatory terrain: Keeping up with evolving regulations, considering the rapid technological changes in the field, presents its own set of challenges.
Ways to use CMMS to reduce energy consumption
CMMS systems provide a powerful solution to the challenges faced by the power and energy sector. Integrating CMMS with supervisory control and data acquisition (SCADA) systems streamlines maintenance operations. Real-time data from SCADA systems triggers automatic work order creation, ensuring swift response to issues. CMMS also enhances asset availability by enabling more preventive maintenance, fostering optimal asset health.
The maintenance trifecta — control, monitor and predict — guides power plant maintenance. CMMS records inspection data, supports real-time equipment monitoring and enables predictive maintenance planning. This proactive approach minimizes downtime and maximizes asset reliability.
Using smart technologies and advanced CMMS
Implementing preventive maintenance plans is another energy-saving measure. Such strategies ensure equipment remains in peak condition, reducing energy consumption and related costs. With an advanced CMMS, teams can easily devise preventive maintenance plans and automate scheduling and notifications.
Optimized inventory management avoids energy waste and reduces expenses. Efficient data collection and analysis facilitate better control over spare parts, ensuring timely availability without excess stock.
Advanced CMMS features allow for in-depth analysis of maintenance tasks, identifying those consuming the most energy. This insight enables strategic scheduling during off-peak hours, minimizing energy expenses.
Accurate data collection on machine operations empowers maintenance managers to identify and address trends impacting energy consumption. Incorporating Internet of Things (IoT) sensors for data collection adds a new dimension to efficient maintenance practices.
CMMS for integration and interoperability
CMMS software operates as a central hub for maintenance management, but its true potential is unlocked when integrated seamlessly with other critical systems within an organization. Integration with enterprise resource planning (ERP) software allows for a more holistic view of operations. Data synchronization between CMMS and ERP systems ensures that maintenance activities align with broader organizational goals and financial planning.
Moreover, integrating CMMS with IoT devices and sensors provides real-time insights into equipment health. These connected devices continuously gather data on various parameters such as temperature, pressure and performance. CMMS leverages this data to trigger work orders, enabling proactive maintenance and reducing the risk of unexpected breakdowns.
Mobile accessibility and field work
In an industry where field operations are paramount, ensuring that maintenance personnel have easy access to crucial information on the go is vital. Modern CMMS solutions offer mobile applications that empower maintenance teams in the field. Technicians can access work orders, equipment manuals and historical maintenance data directly from their mobile devices.
This mobile accessibility accelerates the maintenance process. Field technicians can update work order statuses, input maintenance data and order parts in real time, improving efficiency and accuracy. Additionally, they can capture images or videos of equipment issues, aiding in better diagnosis and streamlined communication with the maintenance team.
Remote monitoring and predictive maintenance
The combination of CMMS and IoT technology enables remote monitoring of equipment. IoT sensors installed on machinery continuously collect and transmit data to the CMMS. Advanced analytics within the CMMS process this data to predict when maintenance is needed, allowing for a shift from reactive or scheduled maintenance to predictive maintenance.
Predictive maintenance can significantly reduce downtime and maintenance costs. By identifying issues before they escalate into major problems, organizations can plan maintenance activities during scheduled downtimes, maximizing asset availability and productivity.
Energy efficiency monitoring with CMMS
CMMS, when equipped with energy management capabilities, becomes a powerful tool for monitoring and optimizing energy consumption. By integrating energy monitoring devices and systems into the CMMS ecosystem, organizations can collect data on energy usage across various assets and processes.
This data can then be analyzed to identify energy-intensive equipment or operational practices. Armed with this insight organizations can make informed decisions to optimize energy consumption, reduce costs and align with sustainability goals by implementing energy-efficient measures.
The power and energy sector’s pursuit of efficient maintenance mirrors the energy it generates — it’s all about finding the most productive way forward. CMMS software emerges as a powerful ally, fostering reliability, safety and sustainability in our energy landscape.