Solutions for condition monitoring are coming from all directions as manufacturers try to streamline supply chain operations.
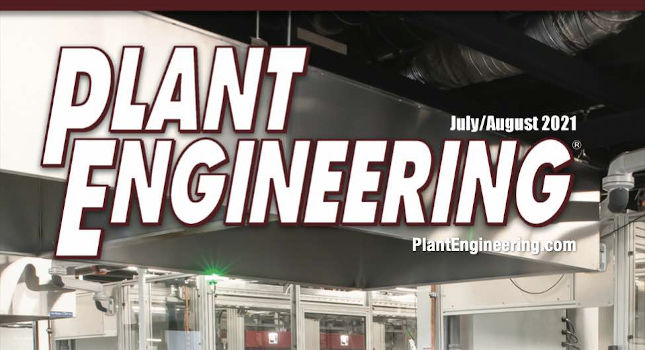
In late July, the New York Times said supply chain disruptions caused by the pandemic will extend well into the first half of 2022. Shipping containers are reported backed up in China’s ports, on ships waiting to dock in U.S. ports, in temporary storage on the west coast and in rail yards in Chicago.
For automation and IT suppliers, everyone wants to get going again but the return to live events has been hesitant. In the meantime, virtual events and Zoom calls make up the difference.
Solutions for condition monitoring are coming from all directions: equipment and device makers, automation and software companies, and even bearing technology suppliers. Schaeffler Group USA manufactures high-precision components and systems for powertrain and chassis applications, as well as rolling and plain bearing solutions.
Schaeffler’s OPTIME consists of wireless, battery-powered vibration sensors, a cellular gateway and an app to visualize the resulting data. This information captured by sensors is analyzed using proprietary algorithms that draw on Schaeffler’s technical expertise, its extensive library of physical models developed and refined over decades, and the experience in condition monitoring Schaeffler gets from its bearing servicing operations.
Slicing and spicing
Monte Zweben is the CEO and co-founder of Splice Machine. Splice Machine bills itself as the real-time AI company. Years ago, at the end of the ERP boom, Zweben was chairman and CEO of Red Pepper Software, a pioneer in the category of advanced planning and scheduling, which was eventually bought by PeopleSoft.
What’s different today compared to back then, Zweben recently said, is the power of distributed computing. “With Red Pepper, all the data was brought into memory. Today, with cloud computing, enormous computational resources are available much more elastically.”
On a recent Voices in AI podcast, Zweben explained how Splice Machine is distinct, saying that operational AI requires three fundamentally different computational workloads. It requires machine learning algorithms, including deep learning. Good data, cleansed and transformed, is needed so machine learning algorithms can make sense of it. You also need operational computing workloads running the applications.
Splice Machine brings all three together in one integrated data platform, Zweben explained. A SQL relational database management system can run applications at petabyte scale, integrated with analytical workloads that can analyze data—even in real time. Instead of taking data out of the data platform and sending it to machine learning algorithms, Splice Machine puts the machine learning algorithms in the data platform natively.
Whole lot a shakin’
Plant Engineering recently attended the virtual launch of the Fluke 3562 vibration sensor system. With the possibilities inherent in the Industrial Internet of Things (IIoT), the importance of vibration analysis to machine condition monitoring is a big topic.
To get beyond route-based maintenance inspections, said Tyler Evans, director of product management at Fluke Reliability, “connected reliability is what’s needed.”
Together, the Fluke 3563 Analysis Vibration Sensor and the 3562 Screening Vibration Sensor offer a total vibration monitoring solution for all a company’s machine assets, wirelessly and with battery-less technology.