From introducing wooden pallets to incorporating Lithium ion batteries, near-100-year-old Raymond Corp. moves the materials that define the e-commerce era.
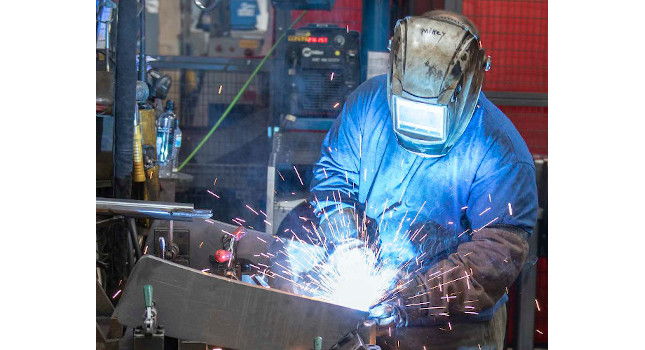
When Americans think of Raymond Corp. of Greene, NY, they probably think of it as a premier maker of electric lift trucks.
Nevertheless, although Raymond Corp. has been around since 1922, its biggest moment might have been in 1939 when the company designed and patented what we know today as the double-faced wooden pallet. On November 7th of that year, George Raymond, Sr., and employee William House were granted a patent for the first hydraulic hand pallet truck, to be used in unison with the double-faced wooden pallet.
Today, as a total warehouse solution provider, Raymond Corp. is part of history, having introduced the first power-driven narrow aisle material handling truck in 1951; the first microprocessor-controlled lift truck in North America in 1986; and, in 2017, Raymond Corp. introduced the first lift trucks powered by the Lithium ion battery.
Plant Engineering magazine is pleased to recognize Raymond as its 2019 Top Plant.
Raymond Corp. also is part of Toyota Industries Co. In partnership with its Columbus, IN, sister plant it produces both Raymond- and Toyota-branded product for North America markets.
Raymond Corp. began its near century-long journey in 1922 when George Raymond Sr. purchased a foundry in Greene, NY. Raymond’s production facility at corporate headquarters today encompasses more than half a million square feet. Production strategies include the Toyota Production System, with Kaizan lean manufacturing maintenance strategies and Six Sigma.
Nearly 1800 employees work at the production facility, near 800 of them dedicated to production, more than 100 exercising maintenance functions, and about 150 in management. About 23% of employees carry associate’s degrees, 18% bachelor’s degrees and 7% masters, with more than 50% percent having at least a high school diploma.
Finally, with e-commerce become such a force in the purchase and delivery of goods, warehousing square footage keeps growing. So much industry growth challenges the material handling industry to do more.
“We partner with Amazon,” said Michael Field, chief executive officer, Raymond Corp. “We’ve responded with innovations that use the forklift as a platform. Our automation solutions drive productivity and our energy solutions power the equipment. The intelligent forklift is an enabler of material handling and labor related information. It determines that the right person is driving the right forklift at the right time. It knows how they’re driving and how the truck is wearing with the usage.”
Make-to-order paradigm
Speaking with Field, and with Tony Topenick, Raymond Corp. senior director of operations, it’s clear they are proud of the company and its success. They and their teams execute a modular, make-to-order model, that at least potentially, could produce millions of different combinations.
According to Topenick, 2-D wireframe computer-aided design (CAD) was introduced in the engineering department in the early 1990s. But it was in the mid-1990s that cutting and other machine tools, coupled with 3D parametric CAD, led to a real paradigm shift “in terms of creating machine tool paths and minimizing downtimes, as well as increase in yield and minimization of scrap.”
Orders are entered into Raymond Corp.’s enterprise resources planning (ERP) from the dealerships where the equipment is sold. On the plant floor, “We balance the system by scheduling for welding and assembly. After kitting it’s a fully pull system. The details of parts requirements are executed using electronic Kanban to replenish in real-time.”
Field adds, “It’s a very lean, clean environment for make-to-order and make-to-demand production and approaching single-piece flow.”
Given the Greene, NY, facility’s size and production growth, some of the challenges it faces, the company says, include the following:
- Larger departmental head count results in coverage challenges for management
- Varying skill and experience levels among team members, a challenge that diminishes over time as members stabilize
- New production processes, equipment, materials, procedures and quality requirements emerge due to technology advances and customer demands
- Volume/throughput goals pressure production space and cycle times.
The vision thing
According to Field and Topenick, Raymond Corp. set a plant vision for 2020. The vision for manufacturing was to optimize the truck build process and develop fundamental automated structures that deliver improved product quality and reduced man hours per truck (improving both throughput and overall plant capacity). With an eye toward innovative developments in the IT space, the process would ensure any new equipment was Internet of Things (IoT) ready.
Progressive total productive reliability would be enabled to improve overall equipment effectiveness (OEE) dynamics. To this end, the business created a strategy that would increase Raymond’s capability to internally process sheet metal components and access fiber laser technology, automated machining, offline programming systems and, in order to maximize these investments, automated material handling.
These investments have delivered, or will deliver by the end of 2020, a 30% increase in rail machining capacity, have improved the capability to insource previously outsourced production hours of plate and sheet component production and have enabled a 30% increase in the time press brakes bend parts. This is a huge advantage in terms of expansion and capability.
Automation of the repair process has reduced machine downtime, providing for more throughput speed and reducing product time to market.
Similar themes factor in the implementation of a new mast rail manufacture process, which encompasses an automated rail machining line, automated mast weld fixturing and an automated robotic weld cell. This process represents about $4.2 million of expenditure and has resulted in the ability to grow capacity for manufacturing in order-picker trucks by 100% over the manual processes in place prior to the installation. Through the re-visioning of the plant and realigning footprints to this 2020 vision, plant capability is today 125 trucks per day.
Maintenance & quality
Raymond Corp. has implemented Total process reliability (TPR), with operators performing smaller, frequent routine maintenance tasks to avert large, time-consuming failures and repairs. In piloting this process, overall equipment effectiveness (OEE) for one CNC lathe machine was increased by 20% within four months. Facilities maintenance implemented infrared testing on critical equipment to save facility downtime by detecting loose electrical connections, elevated bearing temperatures and other failing electrical components producing excessive heat.
A computer maintenance management system (CMMS) is used to request and purchase production machine consumables and maintenance parts, track equipment history, generate preventive and predictive maintenance work requests, track and record equipment downtime, log history of equipment failures and track facility assets.
The Raymond Corp. is committed to building quality products while providing and maintaining a comfortable operating environment for its employees. This commitment reduces risk for personal injury and property damage through the promotion of employee safety awareness, responsibility and emergency preparation.
In addition, Raymond focuses on building the confidence of its lift truck operators by reinforcing desired behaviors. Raymond maintains environmental and security systems for the protection of all employees, property, equipment and the environment. Raymond maintains a health and safety program that develops and trains managers, supervisors and employees on safe working practices and procedures.
Topics include hazard recognition and control, hygiene, general housekeeping, and off-the-job safety and wellness. Training begins with the new employee orientation program and is enhanced through Safety Dojo interactive training, on-the-job training, communications from the EHS team, and on-going safety training. Each month, the EHS team hosts safety meetings with supervisory personnel at various levels, to share safety information from the prior month. Risk assessments are conducted by reviewing standard work instructions, observing employee performance and discussing the activities with line management and support groups. Each identified hazard is scored and corrective action is recommended.
Part of a community
Raymond Corp. pays attention to manufacturing safety and education issues as they define and represent its role and standing in the community. Raymond implemented robust safety training and management processes to address the challenges. To measure its progress, Raymond developed a comprehensive data collection, reporting and recognition program for achieving safety milestones. Program elements include:
- Monthly environmental, health & safety (EHS) meetings for management groups, from assistant team leaders to executives
- Metrics that include comparisons among divisions within the company and against current national standards for similar companies
- Ergonomic continuous improvement recognition and awards, whereby, the monthly drawing winner receives a certificate and cash award.
Raymond strives to recruit and identify the best talent to fill positions ranging from administrative and executive roles to welding and manufacturing positions. Raymond is committed to building and maintaining a strong, dynamic workforce through continual training and development. All new hires participate in an employee orientation program, with additional training provided depending on the employee’s position and role.
Raymond believes that education and training are vital to the growth of the company. Its employees believe their success is a tribute to the distinctive corporate culture, which emphasizes and values customer focus, innovation, professional excellence, teamwork and taking a global perspective.
Training for Raymond employees comes in a variety of ways:
- Safety and compliance training is ongoing and occurs at regular intervals. This training may include anything from a truck operator, fire extinguisher, crane and hoist training to code-of-conduct training.
- Development training courses are open to all employees to assist in increasing their skills and knowledge for their current position, as well as to provide guidance for career advancement.
- Individual departments sponsor special training sessions to develop the unique skills and knowledge required for their specific department, such as computer software skills, machine operation or production and inventory management.
- Leadership and mentoring programs are offered to individuals who demonstrate leadership potential. In addition to internal training opportunities, Raymond offers a generous tuition aid plan that allows the employees to pursue a college education with little cost to the employees, other than their dedication and time.
The education angle
In enabling continuing education for its workforce, Raymond uses several next-gen learning tools including the Raymond virtual reality simulator.
The Raymond virtual reality simulator makes it easier for lift truck operators to more readily understand what a material handling job entails, by providing early exposure in a virtual environment on a truck using the actual controls. The opportunity to learn through virtual reality is especially timely as e-commerce demands show no signs of slowing down — and those demands skyrocket leading up to the holiday season.
This type of education is especially helpful during a time when there are more manufacturing jobs available than there are workers to fill those positions. The instruction also is pertinent for seasonal and temporary employees who may have no prior experience and need to learn as quickly as possible.
Raymond Corp. works closely with various colleges, trade schools and high schools to recruit local talent. Additionally, Raymond Corp. attends the SkillsUSA National Competition each year, promoting careers in manufacturing. Raymond Corp. also hosts National Manufacturing Day, Engineering Day and Raymond Day events at corporate headquarters each year, inviting students from the STEM fields to tour the facility and partake in learning experiences. Raymond also works closely with local organizations to find the best talent for available positions. Raymond recognizes the value in such partnerships, which benefits the business and the industry.
Raymond Corp. safety & maintenance statistics
- Number of lost-time accidents in 2018 : 8
- Number of lost-time accidents in 2019 to date : 5
- Number of OSHA Recordables in 2018 : 87
- Number of OSHA Recordables in 2019 to date : 40
- Number of hours of safety training per employee per year : 80
- Percentage of operating budget spent on maintenance in 2018 : 4%
- Percentage of operating budget spent on maintenance in 2019 to date : 5%
- Percentage of unplanned downtime : 19%
Environment & utilities
Top Plant 2020 award winner Raymond Corp. strives to preserve and protect the environment in all aspects of its business.
The Raymond Corp.’s manufacturing facilities in Greene, New York, and Muscatine, Iowa, are ISO 14001 Multi-Site registered.
Overall energy use in 2018-2019 fiscal year was such that greenhouse gas emissions at the Greene, New York, manufacturing facility were increased by 4.3% (measured as quantity emitted per unit produced at the facility). The manufacturing facility in Muscatine, Iowa, reduced greenhouse gas emissions 19%.
- Percentage of operating budget spent on energy in 2018: 3%
- Percentage of operating budget spent on energy in 2019 to date: 2%
- Percentage of energy expense saved in 2018: 18%
- Percentage of energy savings forecast for 2019: 2%
Electrical & lighting
Recent events related to sound management of electrical power and lighting include the following:
- Re-lamping projects increased the efficiency of energy use for lighting at the facilities
- Computer-controlled heating, ventilation and air conditioning (HVAC) systems guarantee efficient use of energy
- Parking/walkway lighting upgraded to high-efficiency, long-life LED bulbs and fixtures, reducing Kilowatts per hour by 25%
- Factory lighting upgrade – elimination of fluorescent lamps in favor of LED technology thereby reducing energy consumption
- Equipment Power Management – instituted a program whereby significant energy consuming equipment is reviewed for energy savings opportunities, and placards are affixed to equipment to assure proper on/off management.
Water use
- Reduced water use by < 1% in 2018-2019 fiscal year gallons of water used per 100 direct-labor hours worked) at Raymond Greene o This measurement method accounts for both “personal” and “process” use of water
- Reduced flush volume on 138 fixtures by 10%, saving approximately 1,035 gallons per day or 269,000 gallons per year
- New building additions were equipped with water saving toilets and fixtures and some existing lavatories have been remodeled with water conserving fixtures
- Chemical products used in the powder paint system washer, and for general maintenance cleaning, are mixed via metering resulting in both chemical and water savings
- Where appropriate, process wastewater that ultimately is discharged to the village sewer system is reused for flushing commodes, average 9,247 gallons/month reused.
Compressed air
Over the past several years, the air compressors and associated air supply system have been reengineered with state-of-the art variable speed compressors to promote conservation of electricity and reduce associated greenhouse gases from the electric utilities.