Earn trust and show the benefits in building a case for CMMS.
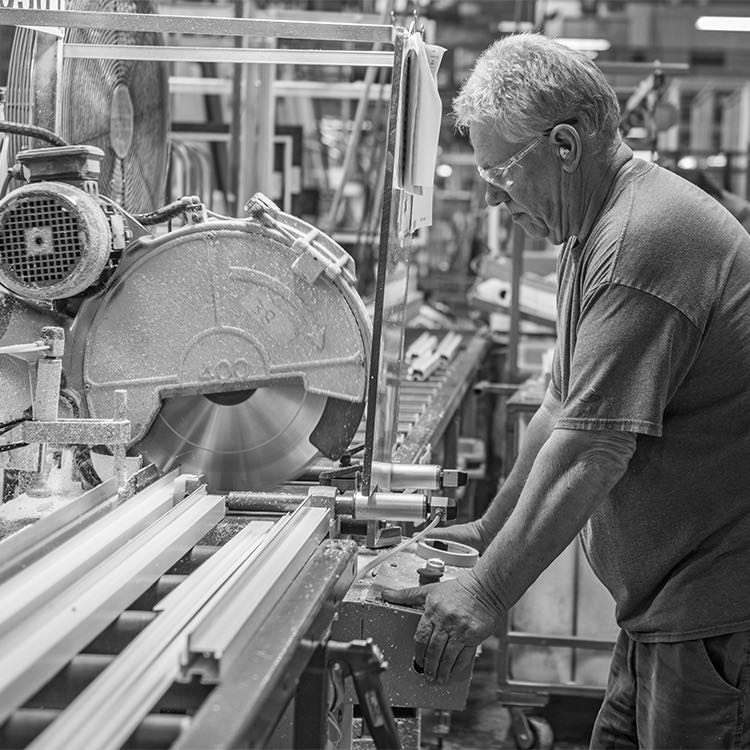
Shifting a manufacturing facility steeped in traditional maintenance practices to one centered on proactive maintenance strategies can be challenging. Obstacles such as costs, lack of knowledge regarding the Industrial Internet of Things (IIoT) and failed past initiatives sometimes block pathways. Often it comes down to the human factor to hinder the journey or make it a success. Two industry leaders share how they successfully implemented proactive maintenance initiatives utilizing a computerized maintenance management system (CMMS).
Managing cultural change at PGT Industries
PGT Custom Windows and Doors (PGT), a leading manufacturer of impact-resistant windows and doors, recently began using a CMMS to maximize and manage its asset portfolio. Capturing data, gathering inventory information, preparing the data inputs from the various sources and training key team members were the first places the maintenance and reliability team started.
Just one year later, Bruce Wesner, senior director of engineering services, and the PGT lead teams have seen significant results, including increased productivity, improved uptime and reduced costs. Admittedly, however, transitioning to the new system did not happen overnight.
“They needed to capture data and information so that it could be fed to our reliability engineering team, Wesner said. “Then, it could be used to perform reliability analytics and help us understand where we needed to focus our time and attention.”
Personnel were accustomed to letting assets run to fail. With more than 2,300 employees at the PGT Venice, Florida operation, including over 60 tradespeople, communicating the benefits of the CMMS and the implementation plan was crucial to the goal of operational reliability.
By actively involving all levels of personnel, Wesner and his teams gained the momentum needed.
“The key factors in getting folks engaged is having these two things in place from the beginning,” Wesner said. “You have to have executive support to make it important, and partnerships within the organization to make it move.”
Since the successful implementation, plans have been set in motion to advance to a condition-based monitoring program at the Venice plant. The organization is preparing to bring other sites on-board.
“Trust is a big part of cultural change,” Wesner summarized. “I think our biggest obstacle to adopting new practices was the lack of awareness and understanding of the different ways of doing things.”
Removing roadblocks – Pratt & Whitney
Pratt & Whitney, a market leader in aerospace design and manufacturing, also began its reliability journey by adopting a CMMS. The organization had outgrown the existing system which required excessive administrative overhead, causing 12- to 24-hour delays in creating corrective work orders. To obtain initial buy-in for the new CMMS, operations and maintenance manager Bruce Gallagher and reliability engineer Jason Vorce requested an onsite visit from a CMMS senior consultant to demonstrate the system.
The consultant showed the leadership team how the CMMS could be used to assign work order priorities based on criticality, as well as maximize uptime and greatly improve processes. Pratt and Whitney wanted a system flexible enough to adapt to its specific needs, including managing work orders and ensuring the availability of parts, yet intuitive and easy-to-use. The CMMS Gallagher and Vorce chose could do all of this and more.
The team won approval from leadership and began installation.
“If you keep showing them the benefits, they will eventually outweigh the ‘no’s’,” Vorce said. “If one person says ‘no,’ find someone else to remove that roadblock and go around it. Find someone above them or next to them that can say ‘maybe.’ Just keep grinding it out.”
Since bringing the system online, Pratt and Whitney has seen solid, quantifiable results. In one instance, when using the system to manage inventory, it was estimated that the organization saved more than $100,000 and potentially months of downtime simply because the right parts were on hand when needed.
“We’re eliminating a lot of the wrenching, so to speak, because we’re able to use the predictive side of things,” Gallagher said. “It’s like having your first kid. You don’t know what it’s going to look like, but then when you see the results, when looking at the reports, it’s amazing.”
Gallagher feels like the program is solid, and he looks forward to it being scaled.
“Our GM invited some people to our Lansing, Michigan site to see the CMMS presentation,” Gallagher added. “Several VPs from various plants took the demo back with them and from there it went to the president of the company. He was very impressed.”
A commitment to change
In a recent McKinsey & Company survey, executives across industries were asked to choose which factor impacted major change outcomes the most. Out of the more than 2,000 respondents, 67% chose “clear organization-wide ownership of and commitment to change across all levels” as the number one reason new initiatives succeed.
Involving all participants in a change management plan from the beginning, not only allows them to feel ownership in and a commitment to the maintenance reliability quest, but also to feel valued and integral to its success. The same human factor that poses a threat to success also ensures success when managed appropriately.