Equipment upgrades are dependent on a well-developed plan that can help companies make informed data-driven decisions that will contribute to a company’s business goals.
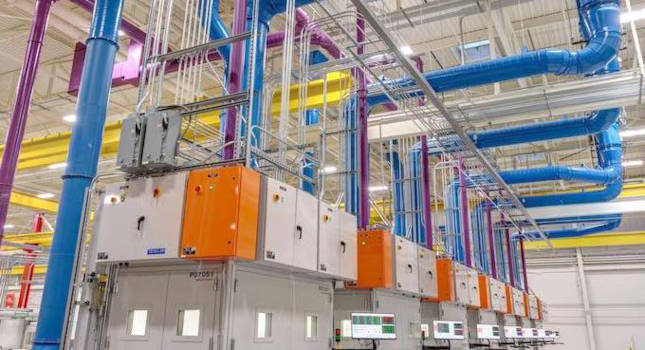
Test equipment insights
- When businesses only upgrade equipment that fails or shows wear, they miss opportunities to improve testing capabilities.
- There is an increased need for better and more automated equipment as manufacturers are dealing with supply chain and labor challenges.
Upgrading test equipment and systems for research and development (R&D) testing or end-of-line production quality testing is an art and a science.
Managers of development and testing labs, as well as manufacturing facilities, face ever-expanding markets, pressure from competition, emerging technology and regulatory requirements, which can lead to companies needing upgrades.
Add budgetary constraints, time and resource demands, and the expertise to integrate enhancements while keeping normal operations running smoothly and the job can be overwhelming. These and other factors comprise the need for a balancing act to accomplish equipment upgrades in a strategic way that supports key business goals.
The solution is twofold: Create a well-developed plan for equipment upgrades to provide the framework required to make data-driven decisions that contribute to the overall business goals of the organization and encourage an innovative mindset to drive cutting-edge solutions.

Upgrades are a constant
When businesses only upgrade equipment that fails or shows wear, they miss opportunities to improve testing capabilities. R&D and production testing equipment are a central consideration when developing new products, increasing throughput, improving efficiency or automating processes.
Effective R&D and production testing means gathering the right data to make informed design and business decisions. The need to upgrade stems from business growth objectives to boost productivity. It can make testing environments safer, improve facility layout or increase market share in a particular sector.
For example, if a piece of equipment is performing slower than the rest of the line, that piece of equipment can result in a high degree of manual intervention, inadequate safety features that create a risk of operator injury, bottleneck testing processes and make collection of test data unreliable. Every impact reduces testing quality and product quality. Equipment upgrades are central to meeting the needs of a growing business and to instigate business growth.
These broader business goals are often reflected in changes to regulatory requirements that mirror shared industry objectives. For example, California voted yes on the Advanced Clean Cars II proposal in August 2022 to augment the state’s already growing zero-emission vehicle market and robust motor vehicle emission control rules to meet increased emissions standards.
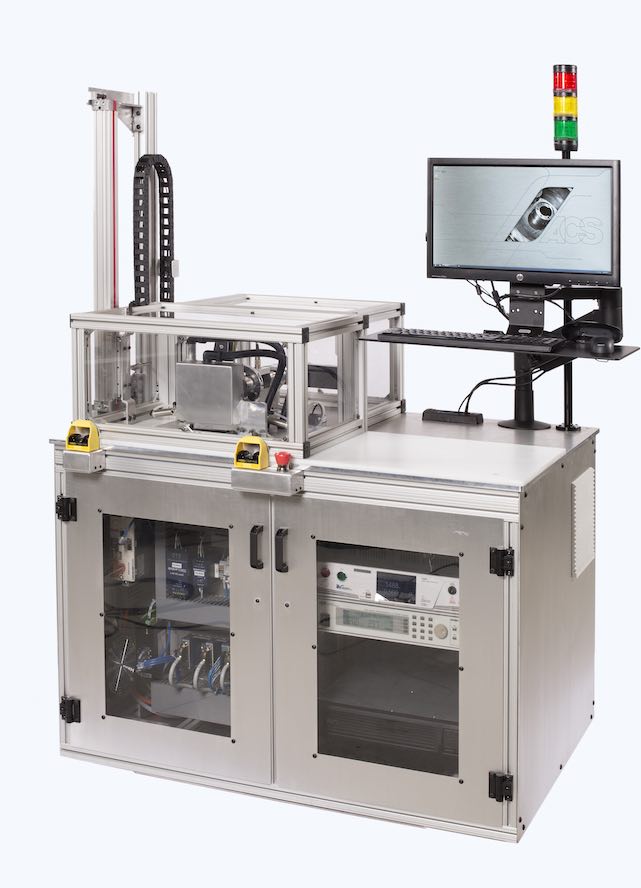
By 2035, California aims for all new passenger cars, trucks, and SUVs sold in the state to be zero emissions. While some experts are critical of the state’s ability to address these goals, its approval paves the way for net-zero commitments across all industries to turn these goals into real action.
Naturally, “real action” requires new testing capabilities for the automotive industry, battery, and power markets, and connected industries. California’s mandate accelerates a mass shift into the electric vehicle age, making it clear how integral equipment upgrades can meet new R&D equipment requirements while keeping steady production going. It’s no surprise electric vehicle sales are on course to hit an all-time high this year and automotive manufacturers are in a race to keep up.
In most cases, business objectives and regulatory requirements are only one part of a bigger picture when it comes to equipment upgrades. The effectiveness of R&D and production testing equipment is also impacted by outside forces, including geopolitical unrest, a globally disrupted supply chain, labor shortages, evolving technology, sustainability initiatives and changing regulations. These factors shape the growing need for R&D testing and production equipment and systems upgrades.
Accelerated by the pandemic, supply and labor crises have instigated further development and investment in automation technologies. For example, robot orders, a leading indicator for all automation equipment, increased 40% in the first quarter of 2022, and were up 21% overall in 2021, according to the Association for Advancing Automation, driving the industry to an estimated value of $1.6 billion.
The shift to automated or automation-augmented equipment is necessary for many companies to meet high demand in a disrupted marketplace, but still requires ongoing engineering resources for maintenance and improvement. These drivers push vast and rapid equipment upgrade needs across many industries, making a strategic upgrade planning process essential to stay ahead of the competition.
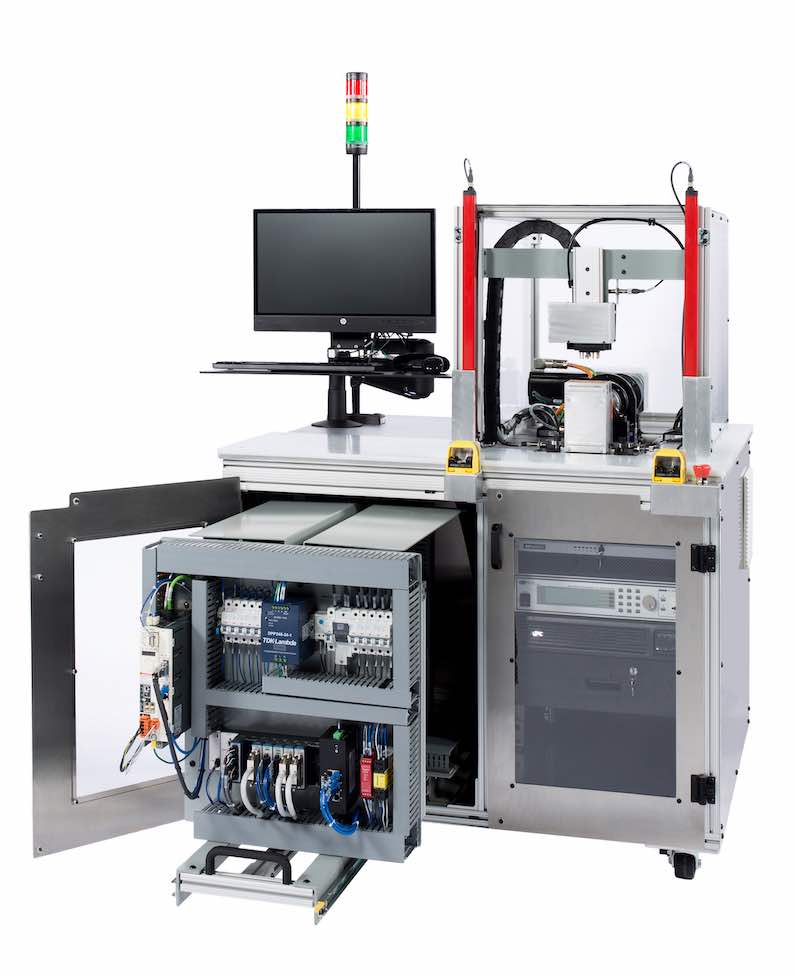
Planning for equipment upgrades
It’s a delicate balance to integrate new technologies and equipment upgrades in a way that addresses external pressures, scalable business growth goals, and customer needs. R&D testing equipment is expensive, so longevity matters when making initial investments. Companies want to ensure they get the most out of what they paid for. But simply waiting for a piece of equipment to break down can result in even greater costs for businesses if production or testing comes to a complete halt.
Planning for upgrades should be a calculated, fundamental and continuous part of the maintenance process. Companies can’t react to outside forces and compliance standards and expect to maintain market share. Consistent planning for equipment upgrades ensures businesses can implement improvements that address internal operational needs and customer needs, extending the facility’s overall lifespan. Strategic planning starts with acknowledging when an upgrade is necessary. It demands deliberate alignment from business leaders, engineers, facility managers, operators, and stakeholders informed with their roles and expertise in mind.
It’s part and parcel that equipment upgrade planning will require an adaptive, solutions-oriented mindset to effectively react to inevitable changes, supply or construction challenges, and reoriented goals. This is where a balance of art and science is necessary for equipment upgrade planning. It demands the structural and scientific knowledge to develop realistic upgrade plans alongside the innovative and adaptable thinking that makes upgrade planning an art.
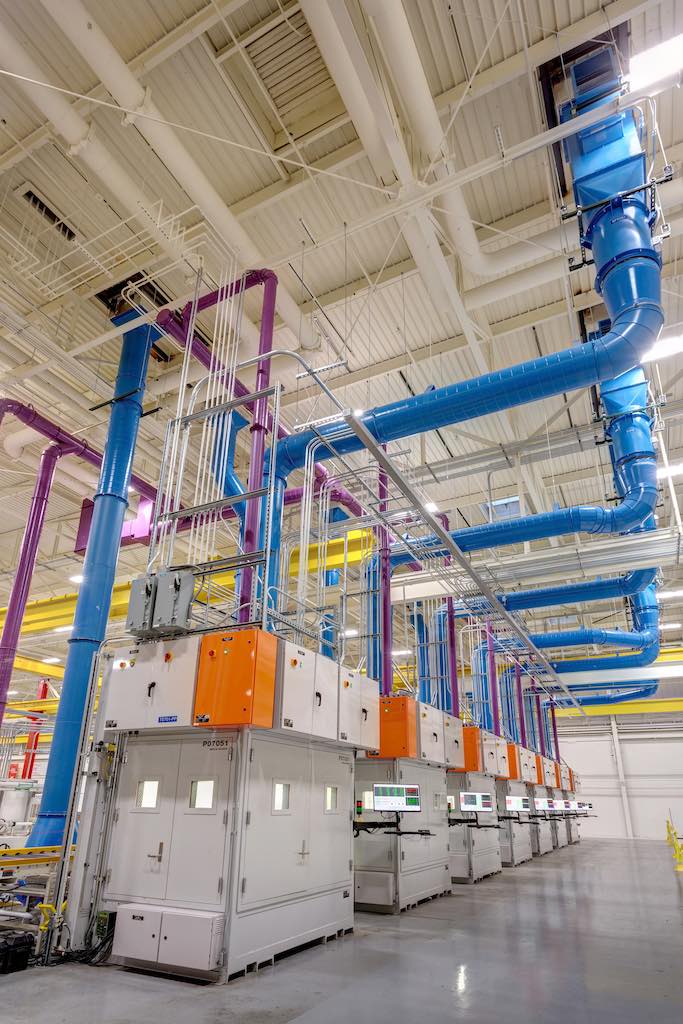
The science of equipment upgrades
Identification of the key business and technical drivers is the first step in making a strategic plan. This might include increased market share in a particular industry, improved throughput to meet high demand, or competitive advantages through new technology. These high-level, data-driven objectives are central to establish a clear vision providing value to the business. Industry metrics, technology assessment, evaluation of suppliers, budget development, age of the facility, and even company culture all play a role in the decision-making process.
Close and early collaboration between test and design functions drive product quality. When planning for equipment upgrades in a testing facility, it’s vital to start with a thorough understanding of the product being tested, whether an engine, appliance, or component.
From there, articulate how the item is tested, how it will be tested and the data desired from the test. The designer can assess the necessary steps to upgrade equipment for the system to effectively test and collect the desired data. It’s also important for designers to evaluate and articulate the mechanical systems the equipment will need and ensure it can accommodate them.
The equipment may have special requirements to operate, such as electrical power, steam, or chilled water. Plans will look different whether adding upgrades to an existing space or developing a draft for a new construction. From there, design demands the precision to make concepts into realistic outcomes.
Here’s an example of using science when upgrading equipment. A lawn care equipment manufacturer required a test system at the end of their production line to verify quality. A test system was created that utilized the latest laser and encoder technology to check blade and wheel speed and direction. In order to provide good data on these attributes, the system was developed to utilize an automated transfer conveyor to direct mowers to one of two test stations. For these systems to integrate seamlessly, the team communicated and aligned capability goals with precise design.
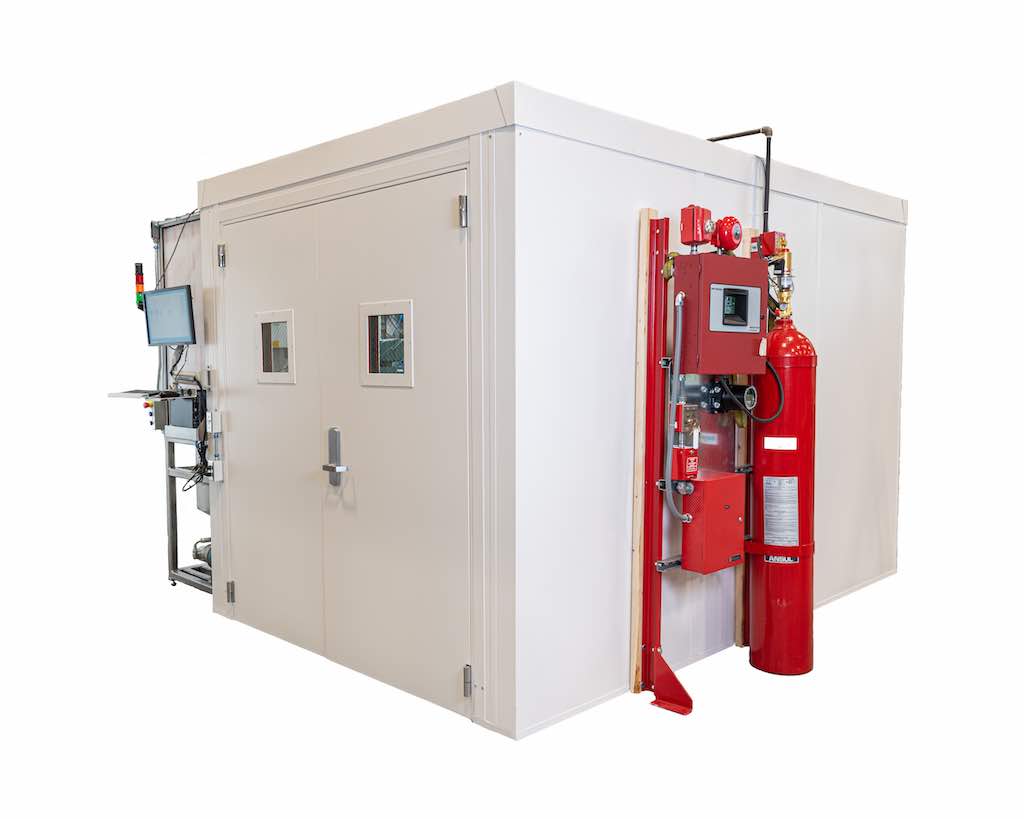
The art of equipment upgrades
Past experiences, collected data, and proven principles can create the proper foundation for a strategic plan, but creative thinking is central to upgrades. An engineer’s perspective is always informed by realistic scientific outcomes, but with the creativity to invent and innovate. It takes creative thinking to fit overarching testing goals into budget, space, or resource constraints. When new materials, technologies or R&D goals arise, their integration solutions must be developed from the ground up, requiring innovation rather than protocols to fit into existing spaces or designs. That’s one reason why equipment upgrade planning is often an iterative process. Innovation demands experimentation, which can feel risky sometimes.
By acknowledging the need for iterations in design, however, the design process can be divided into sensible, strategic steps informed by operational goals, engineering capabilities, and overall business objectives, including compliance and product needs. It’s an art to balance the widespread and varied demands of a business and offer a solution that integrates all of these. Establish a clear vision from the start and invite new perspectives and novel ideas to initiate positive change.
For example, when a customer needed to meet U.S. military test protocols for a genset with capabilities that allowed for the physical pushing of buttons on a power generator while it was operating during a test, traditional solutions didn’t fit. In-person operators would have been unsafe, and the space couldn’t accommodate a physical robot. As an innovative solution, a custom-developed, pneumatically-actuated fixture was installed to activate individual buttons. By considering equipment upgrades as an art, it’s possible to bring new ideas to the table beyond the standard approach. In this case, the unique fixture delivered on operational goals while operating at a lesser cost with less complexity and space being taken up.
Take a proactive approach
As technology evolves, marketplaces change, and new regulatory requirements come and go, the demands for R&D and production testing equipment upgrades can emerge for many reasons. Developing a strategic plan requires a proactive mindset that takes into consideration both the art and science of equipment upgrades. Data-driven research and precise design provide the structure for upgrades that support operational needs, product improvement, and overall business goals.
It’s important to resist the urge to drive every decision solely based on a standard or traditional approach. Innovative thinking and an adaptable mindset create opportunities to discover new solutions to lower cost, improve efficiency, or deliver a superior performance. By striking a balance of science and art that integrates intuitive insights with key data, equipment upgrades will propel facility and business goals forward.