Predictive maintenance is a powerful tool to keep the noise down with roller bearings and can reduce costly repairs.
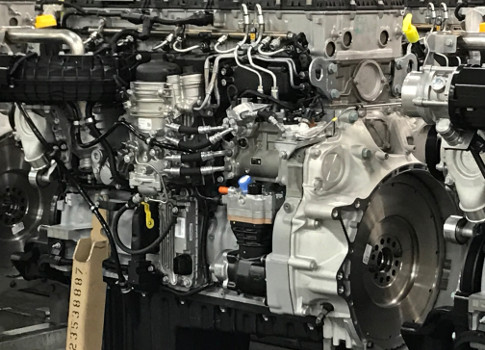
Ask any maintenance technician about roller bearing issues, the typical problems they’ll cite range from contamination, electrical damage, and misalignment to improper lubrication, vibration, and fatigue. These can lead to costly downtime and the potential for other problems in the equipment.
Traditional methods such as inspecting bearings during operation, checking for signs of excessive heat, and listening for abnormal buzzing, chatter, squeaks, and hum can uncover a problem. Bearings also periodically can be removed for closer inspection and to check for flaked inner and outer rings, scratches, or cracks on the roller and face, and roughened or discolored surfaces. Another step uses condition monitoring tools such as thermal cameras, digital tachometers, handheld vibration sensors, and electrical discharge sensors to determine the operating condition of bearings.
Another toolset
The application of predictive analytics adds very powerful tools to our toolbox. Combining condition-monitoring and predictive maintenance methods can find the earliest stages of damage and reduce operating costs. Rather than shutting down equipment for scheduled preventive maintenance routines, maintenance can be planned to match convenient schedules and improve reliability.
Condition monitoring catches potential problems at an early stage. Predictive maintenance provides the added advantage of using sensors, machine learning, and advanced algorithms to detect faults and predict failure. Sensors monitor specific aspects of the system and generate data used by analytics software to assist with making maintenance decisions. For example, sensors attached to bearing brackets monitor vibrations while analytics search for deviations that indicate the loss of tactile strength.
Connecting to the Industrial Internet of Things (IIoT) through apps enables access to historical baseline data while building the statistical and trend analyses that point to why and where problems occur and what actions are needed. Predictive maintenance methods include using apps provided by bearing manufacturers for real-time vibration monitoring, frequency analysis, bearing speed ratio checks, and envelope spectrum tests.
Vibration monitoring
Rolling elements, inner raceways, outer raceways, and cages produce complex vibration signatures. Predictive maintenance tools measure different characteristics of vibration over time and compare changes with known levels of vibration. Established pre-alarm and alarm levels within the analytics software indicate a change in bearing condition as vibrations impact inner and outer raceways.
Frequency analysis
Roller bearings generate distinctive characteristic frequencies during normal operation. When damage—such as spalling—occurs, the amplitude of those frequencies decreases and broadband noise increases. Predictive maintenance tools look at patterns within harmonic frequencies, frequency sidebands, and time waveform data to provide earlier, more reliable fault detection.
Bearing speed ratio
Predictive maintenance tools also can monitor the bearing speed ratio or the ball pass frequency divided by the shaft rotational frequency to indicate changes in bearing operating performance. For example, excessive lubrication or insufficient loading can cause skidding that decreases the ratio below normal values. Higher-than-normal bearing speed ratios indicate excessive loading, excessive internal clearance, or poor lubrication.
Envelope spectrum tests
Bearings can fail in a short time span. Envelope spectrum tests detect early damage in rolling element bearings by extracting high frequency bursts of energy caused by a rolling element hitting a fault. Removing and analyzing frequency components that match a corresponding time signal of vibration measurement detects vibrations that may become masked by other vibrations and noise within the system.
Sensors and analytic software cannot change out parts or substitute for human decision-making. However, predictive maintenance tools can encourage proactive behaviors by indicating problems well in advance of a catastrophic failure. Automating maintenance analysis also allows you to focus on optimizing workflows and increasing system reliability.
Scott Moeller is product manager of bearings, seals, and accessories at Motion Industries. He has over 30 years of industry experience, including employment with The Torrington Company, Cooper Bearings, Rexnord Industries, and RBC Bearings.