Using Red Kynar PVDF reduces extra maintenance costs and unexpected downtime
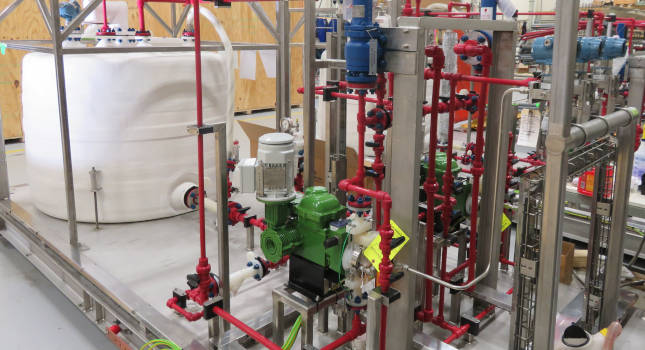
Evaporative cooling tower systems are commonly found throughout many industries including petroleum refineries, chemical manufacturing, metal processing, rubber processing, glass manufacturing and textile manufacturing. A cooling tower is a type of heat exchanger that reduces the temperature of water by bringing it in contact with air to facilitate evaporation and the highly efficient rejection of heat. Cooling towers are open to the atmosphere and frequently to sunlight, so they must withstand UV radiation and other environmental factors including microbiological activity, which can adversely affect tower components. Using polyvinylidene fluoride (PVDF) can help with sunlight resistance.
Microorganisms
Cooling tower location, relative to potential sources of contamination, can contribute to system-wide microbiological activity. Oil, process contamination and phosphates contaminating water are all vital nutrients contributing to the feeding of microorganisms.
To maintain efficient heat transfer and minimize corrosion potential, it is essential to control microbial activity. Basic control strategy most commonly employs what are termed oxidizing biocides such as sodium hypochlorite, “stabilized” bromine, chlorine dioxide and a few others.
Bacteria will populate in cooling tower water, the number of freely circulating, planktonic organisms being but a small fraction of bacteria found on surfaces, sessile organisms. Sessile organisms secrete an extracellular polymer to link bacterial cells together to form an elastic film or coating, better known as slime. Slime trap particulates harbor both living and dead bacteria and can grow into a complex community known as biofilm. Biofilm has an insulating effect on heat transfer and clogs piping reducing flow rates.
Biofilm
If left to grow out of control, biofilm will support a multitude of organisms producing metabolic bi-products and various enzymes that initiate and drive corrosion. Biofilms also prevent corrosion inhibitors and oxygen from reaching base metal and overcoming what is termed microbiologically influenced corrosion (MIC). They can attack the entire water containment system.
Along with bacterial slime formers, other growths such as algae can create additional problems such as clogging orifices within the system. Living and dead biomatter and algae provide additional nutrients to a wide array of microorganisms i.e., fungi, mold and protozoa. They increase the risk of harboring pathogenic organisms such as Legionella. Managing the bacteria below a certain level will maintain the intended operation of the cooling tower and maintain a generally healthy environment.
Treatments and PVDF
An effective treatment to reduce microbiological activity would be the use of sodium hypochlorite. However, sodium hypochlorite feed systems present their own challenges due to the chlorine component, which is corrosive to many common fluid handling systems. The Peters Table references the chemical resistance of plastic and metal piping under pressure with water treatment chemicals that are used to treat microbiological activity (1). Red Kynar PVDF can be found as a material of construction for these sodium hypochlorite feed systems for that reason, with a wide array of fluid handling components available. Figure 1 shows an example of different types of Red Kynar PVDF ball valves.
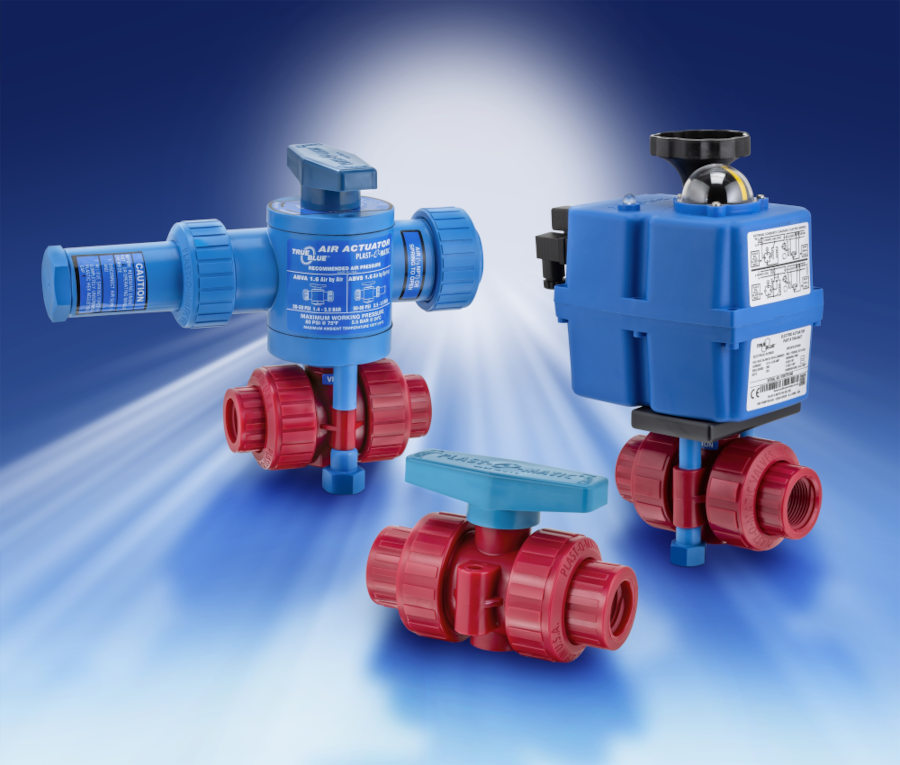
Feed systems
For over 30 years, AmeriChem Systems, Inc. (ASI) has manufactured corrosion resistant custom fabricated systems that are individually engineered to fit customer needs. Their experience of fabricating industrial equipment provides customers cost‐effective solutions in all manufacturing disciplines.
ASI manufactures sodium hypochlorite feed systems that inhibit the growth of algae and bacterial species in cooling towers. According to Dan Wagner, President of ASI, “Modular chemical feed systems have become the preferred choice of our customers and the end users. These engineered, packaged systems reduce installation time at the site by up to 50%; and simplify start-up and commissioning activities, as the systems are fully functional tested at the manufacturing facility.”
Red Kynar PVDF construction
The feed system is fabricated with all wetted materials in Red Kynar PVDF construction. For piping, Red Kynar PVDF 700 series compound contains a small amount of pigment for opaqueness to UV radiation. Red Kynar PVDF has many years of utility in the chlorine handling industry as piping, fittings, pumps, tanks and vessels.
Over years of use, Kynar PVDF has proven excellence for sunlight resistance. In applications involving the combination of sunlight and chlorine, the addition of red pigment in the Kynar 700 PVDF extends the life of the piping by acting as a UV block to keep the contained chemical stable. The system, seen in Figure 2 shows a system engineered by AmeriChem Systems, Inc. using Red Kynar PVDF in all contact surfaces.
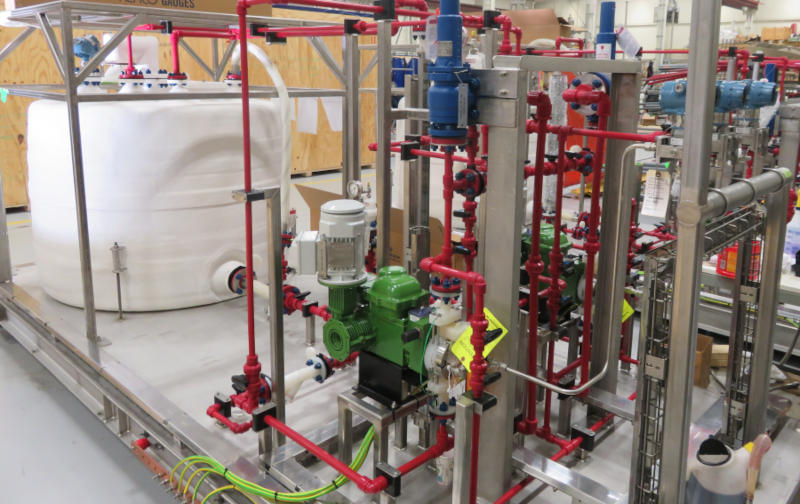
One example of the use of a Red Kynar PVDF 12.5% sodium hypochlorite feed system was a design by FDH JV (Fluor, Daewoo, Hyundai joint venture) for an installation at a chemical facility in Kuwait. The designer and the end user contracted AmeriChem Systems Inc. for advice on the best way to verify their evaporative cooling tower system was free of microbiological activity.
In designing this system, for long-term maintenance free service, ASI, FDH JV and the facility owner decided to use Red Kynar PVDF Schedule 80 piping components joined by the socket fusion method. The material selection was made due to the excellent chlorine resistant nature of Red Kynar PVDF. For this one-inch piping system, the joining method of socket fusion was chosen because this type of lap joint gives a strong leak free and supportive connection.
ASI has experience fabricating chemical piping delivery systems from one half inch (1/2”) to four inch (4”) diameter in Red Kynar PVDF. Choosing Schedule 80 thickness determined by iron pipe size (IPS) gives an extra degree of safety by having a thicker wall pipe than may be used in a general chemical environment. Figure 3 shows a red pipe socket fused to a fitting.
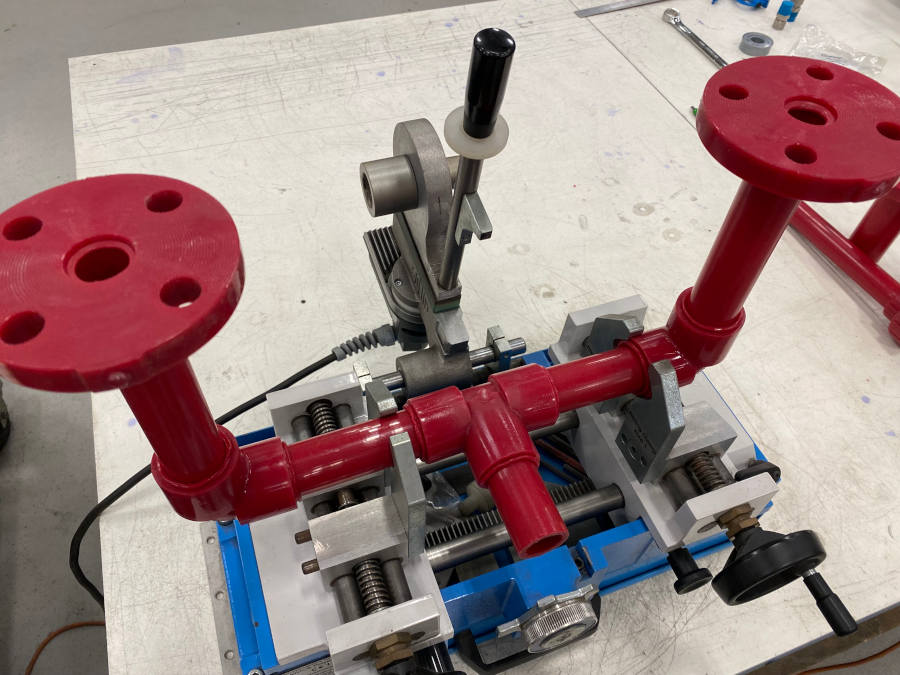
The installation for the sodium hypochlorite line in the hot and sunny Middle East environment has given trouble free service for six years and is still in service in 2022. Arkema gives a 200F (93C) rating for Red Kynar PVDF in 12.5% sodium hypochlorite service. This provides a good degree of safety factor for outdoor installations subject to high temperature swings.
The owners believe that by using Red Kynar PVDF instead of a typical metal system that they have avoided extra maintenance costs and unexpected downtime. Other options, such as exotic metals, may have performed well but at a much higher expense than the easily designed polymer system made from Red Kynar PVDF.