Preventive maintenance is a better way of preventing equipment breakdowns before they cause problems on the plant floor.
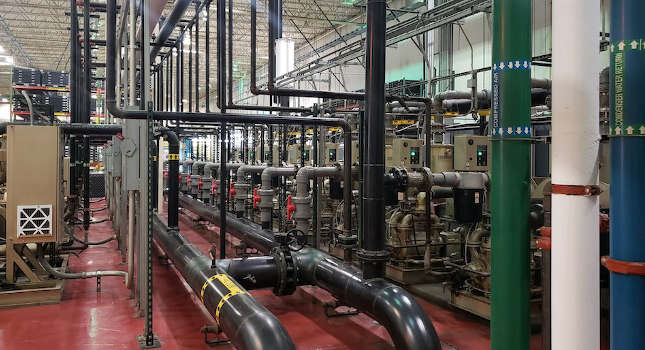
Preventive maintenance is a better — and, perhaps more importantly, actually possible — way of preventing equipment breakdowns before they wreak havoc. It’s all enabled by preventive maintenance software, which is a whole lot simpler to get your hands on than an Delorean.
Let’s take a look at preventive maintenance: what it means, why it’s important and how to do it the right way.
Preventive maintenance fundamentals
First things first: What do we mean when we say preventive maintenance?
At its core, preventive maintenance is exactly what it sounds like: a planned maintenance method based on preventing equipment breakdowns or other asset management issues before they arise. Of course, you can’t stop every problem, so preventive maintenance is just one part of a complete maintenance management approach. You’ll also want to make room for the other members of the maintenance family: reactive maintenance and predictive maintenance.
Here’s how these three siblings stack up:
Reactive maintenance is the oldest kid in the family and represents a somewhat outdated break/fix approach. Essentially, you’re reacting to breakdowns by scheduling a maintenance work order or otherwise moving to get things back online. While reactive maintenance deserves a spot in your overall maintenance management approach, it shouldn’t be your only method because it can quickly become wasteful.
Preventive maintenance is the middle sibling. It’s a step above reactive maintenance in the proactivity department. Think of it this way: A reactive approach would be to help people pay for car repairs after accidents in a dangerous intersection, while a preventive approach is to put in a new stop sign — and naturally, the latter makes more sense. Of course, it’s important to know when and where to implement this particular solution to get the best return on investment (ROI); simply put, you want to minimize the number of breakdowns you have to react to in the first place.
Predictive maintenance is the youngest — the “hip” one who’s up-to-date on all the latest tech and uses frankly indecipherable slang. As the name suggests, this approach is all about predicting equipment or asset issues and performing the right maintenance work at the right time. With this kid on your side, you’ll see all kinds of benefits to your asset management and maintenance operations. Just like its siblings, though, there’s a time and place for predictive maintenance; it’s not the kind of solution you can (or should) deploy at every turn.
The takeaway here is that preventive maintenance is a big deal — and more than worthy of a place in your digital transformation journey. After all, other efforts to digitize your plant won’t mean much if you’re still living in the stone age of maintenance management, right? Trust us: Your equipment, maintenance work teams and even your budget will thank you.
How not to do preventive maintenance
Now that you know what preventive maintenance is, how it compares to its siblings and why it’s just one part of a planned maintenance program, let’s take a look at how not to do it.
That’s right: Just like most things in life, there’s a wrong way to do preventive maintenance. In fact, there are a few wrong ways. To further complicate matters, there’s not even a “right” way to compare against — a preventive maintenance program should be designed to fit your plant, which means there’s not necessarily a rulebook to follow for every maintenance task or facilities management question.
Luckily, it’s not too difficult to avoid significant preventive maintenance pitfalls. You just have to know what to look for:
Time-based maintenance
In some cases, you might be right when scheduling maintenance work based on how much time has passed since your equipment’s last checkup. However, if your entire approach is to perform service just because time has elapsed, you’re doing preventive maintenance the wrong way.
Generally speaking, it’s often smarter to build your maintenance schedule around a usage measurement like mileage, cycles or rotations. Even placing a work order based on hours of run-time is better than writing “maintenance” on your calendar every three months “just because.”
The best approach is to have an indicator of wear and tear — something that helps you predict upcoming equipment issues and plan your maintenance scheduling accordingly. Naturally, that’s where predictive maintenance and preventive maintenance team up to help you navigate work order management, maintenance costs and more.
Manual processes
Here’s a secret: Any time manual processes are the keystone of your equipment maintenance, inventory management or facility management, something is probably wrong. That’s because manual processes are outdated, inefficient and usually unnecessary. Of course, robots aren’t stealing our jobs any time soon — but we can certainly hand off every tedious, repetitive maintenance task that only serves as another opportunity for human error.
More importantly, the idea of preventive maintenance is to make your life easier, your equipment more reliable and your planned maintenance more efficient — not to add extra work to your plate. Simply put, if manual processes are taking over your plant, you know something’s gone sideways in your preventive maintenance program.
Tech overload
It’s tempting to over-invest in technology. After all, so many tech tools promise to be the end of asset management troubles, work order woes and planned maintenance frustrations — who wouldn’t want to have as many of those solutions as possible?
The truth, however, is that “tech overload” can quickly turn ROI into R-O-bye. That’s right: Too much technology drains your budget, hurts your efficiency and can even make it more difficult to clearly and accurately make decisions about preventive maintenance task distribution, downtime mitigation, spare part management and more.
Of course, that’s not to say that technology is the enemy; tech for tech’s sake is the enemy. Before you start adding sensors and other devices to make predictive and preventive maintenance possible, you need a foundation that will facilitate reactive, preventive and predictive maintenance as necessary.
That’s where preventive maintenance software comes in.
Preventive maintenance software saves the day
It’s easy to get intimidated by all those pitfalls, right? At this point, you might be thinking it would be easier to just find that ‘81 Delorean.
Lucky for you, preventive maintenance software is here to save the day.
Preventive maintenance software like a computerized maintenance management system (CMMS) is the foundation you need to avoid those pitfalls. It may not be a rulebook — remember, there’s only one “right” way to implement a predictive maintenance program, and that’s whatever works for your plant — but it does act as a guardrail to keep you from falling into traps like over-investment in technology.
How is that possible? Well, it all comes down to the concept of digital transformation. When you utilize the right kind of preventive maintenance software or maintenance management software, you’re essentially restructuring your approach from the ground up — and along the way, you’re building preventive maintenance right into your factory’s DNA. As you digitize other elements of your workflows, you’ll be able to base every decision on what worked for preventive maintenance, thanks to that software you chose to invest in from the very beginning. Plus, with no more preventive maintenance scheduling issues or maintenance activity madness, you’ll be able to focus on other things — like asset essentials or production efficiency.
Sound too good to be true? It’s not — and here are a few preventive maintenance software benefits that prove it:
- Transparency: To ensure that asset and maintenance activity tracking is accurate and efficient, you need visibility into every moving piece. Preventive maintenance software gives you this top-down view, allowing you to leverage transparency and make every maintenance connection count via better, more informed decisions.
- Simplicity: There’s a lot of data involved with asset management, maintenance operations and all the other things you do to keep your equipment up and running. With preventive maintenance software, you’ll have a centralized database where you can organize, analyze and utilize this information — even from your mobile device.
- Efficiency: If preventive maintenance is all about making your life easier, preventive maintenance software is what enables that improvement. This software is designed to help maintenance activities waste less time and money while improving equipment performance and other asset management stats.
- Optimization: When should you automate a task, and when should you leave it in the capable hands of your maintenance operations team? Where is predictive maintenance necessary, and where would effective preventive maintenance suffice? How much tech do you actually need? To answer all these questions and end up with a well-optimized plant, you need preventive maintenance software.
Four methods for choosing preventive maintenance software for your plant
Now that we’ve sold you on the concept, it’s time to deliver a little bad news: Not all preventive maintenance software is created equal. That means it’s up to you to choose the right software for your plant.
But how do you do that? Where do you start when you’re still trying to figure out the right time for reactive maintenance, or how much tech is too much tech?
Simple: Look for the signs of good preventive maintenance software. Here are a few to get you started:
1. Real-time data capture
If you really want to know when a work order is necessary or what the best maintenance approach is, you can’t base your decisions on yesterday’s information. You need up-to-the-second data that will give you a complete, precise view of what’s going on with your equipment.
For that reason, the best preventive maintenance software has the capability to capture and display data in real-time — and not just from machines. The software should also make it easy to review user-generated data right next to equipment stats and asset management information, giving you all the facts you need to make preventive maintenance a breeze.
2. Automated notifications
What good is a preventive maintenance system if it’s not drawing your attention to relevant insights? Preventive maintenance software should have automated notifications that trigger in response to specific events. Some software can even generate and send an automatic work order depending on your specifications, cutting out the need for a middle man and saving time, money and resources in the process.
3. Consistent visibility
Real-time data capture is an important step in being able to know which preventive maintenance measures are necessary. However, unless that visibility is consistent and constant, you won’t know which solutions led to which results, or which problems merit your focused problem solving resources — and, eventually, you’ll be relying exclusively on reactive maintenance or manual processes again. That’s why it’s crucial for preventive maintenance software to include data analysis capabilities, enabling you to learn from your decisions and prevent even more equipment failures or asset downtime in the future.
4. Improvement framework
One way to think about preventive maintenance is “the creation of new best practices.” Of course, that doesn’t mean much if you’re unable to standardize your new approach across the entire plant — so your preventive maintenance software should allow you to share insights, solutions and best practices with everyone. It should also include a framework for future improvements; after all, even a best practice might be strengthened once your teams get ahold of it.
This originally appeared on L2L’s website. L2L is a CFE Media and Technology content partner.