From oil sampling, vibration analysis and connected devices, predictive maintenance done as part of the system’s regular service schedule can keep a compressed air system running efficiently.
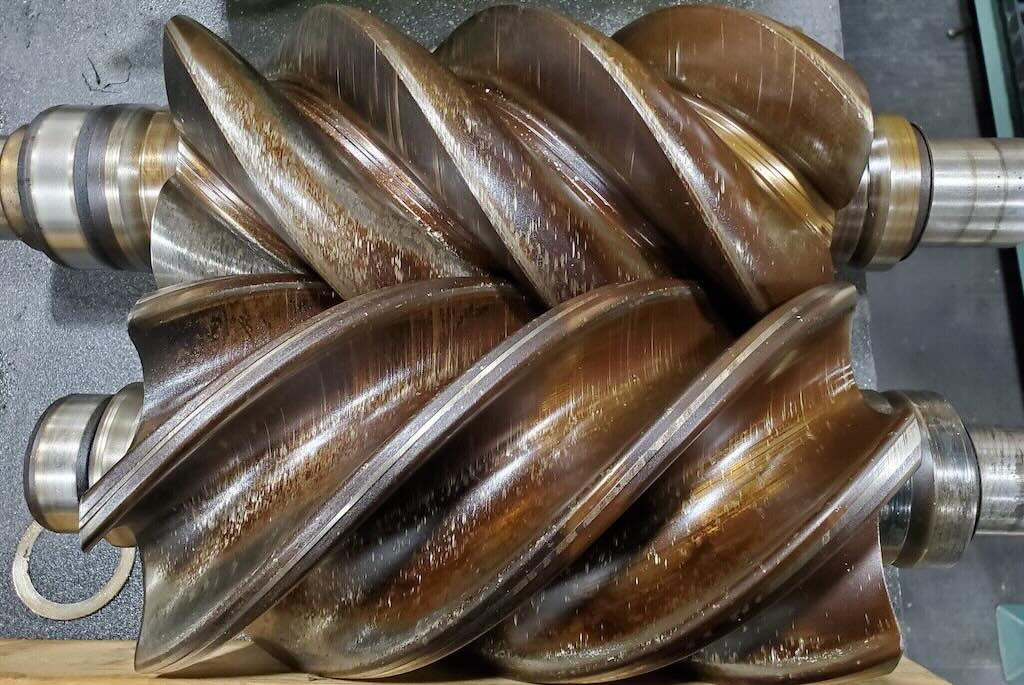
Learning Objectives
- Learn how predictive maintenance tools can be part of a compressed air system’s regular maintenance.
- Understand what a service tech looks for on a regular service call and the types of predictive maintenance that is performed during regular service calls including oil sampling and vibration analysis.
- Learn how analyzing data trends from samples taken during routine maintenance can help reveal the health and efficiency of a compressed air system preventing downtime.
Predictive maintenance insights
- Keeping a compressor in optimal condition requires regular maintenance and condition monitoring, which are essential for plant uptime and efficiency.
- Using data from regular system service and remote monitoring enables predictive maintenance, helping to prevent breakdowns and ensure reliable compressor operation.
- Technicians gather and analyze various data points, such as oil sampling and vibration analysis, to build a predictive maintenance program that minimizes unplanned downtime and extends compressor lifespan.
Reliability in a compressed air system is essential. Keeping a compressor in good running condition is key to plant uptime and efficiency. Regular maintenance and condition monitoring is required to ensure a compressed air system remains in good working order.
Predictive maintenance offers the opportunity to stay ahead of issues that can lead to breakdowns. Using data gathered from the compressor through regular system service and remote monitoring can provide insight into compressor condition and drive the preventive maintenance that ensures reliable compressor operation.
When technicians perform regular system checks, they are interpreting a spectrum of data points to build a comprehensive assessment of the compressed air system’s health. It’s important to understand what happens during a service calls, how the data is gathered and how the information is used in predictive maintenance to keep the system running smoothly.
What happens during a typical compressed air system service call
When a service technician is called to a job site to perform preventive maintenance on an air compressor, they will start by servicing the compressor in accordance with manufacturer guidelines. For an oil flooded rotary screw compressor, this often includes air and oil filters, compressor fluid, and separator elements based on hours of operation.
While attending to the manufacturer’s prescribed maintenance items, the technician also will inspect other machine systems for proper operation. This is a great time to review the compressor cooling system for proper air or water flow and check operating temperatures to confirm proper operation. Regulators and control valves also should be inspected.
Preventive maintenance service calls also provide the opportunity to gather important, predictive data from the compressor system. Most compressor manufacturers recommend regular oil sampling to monitor both fluid, and compressor air end condition. Vibration data also can be periodically collected to establish a historical trend of the rotating component condition. A best practice is to oil sample and collect vibration data twice per year, but also be sure to follow manufacturer guidelines for compressors within the warranty period. This also is a good practice to continue even after a warranty has expired.
Many modern air compressors are controlled by microprocessors that will store operating parameters including alarm and fault histories, operating hours and start stop history and compressor load profile. It is considered a best practice during service visits for the service technician to record key information from the machine controller and, when available, download a report from the compressor controller to store with the service records.
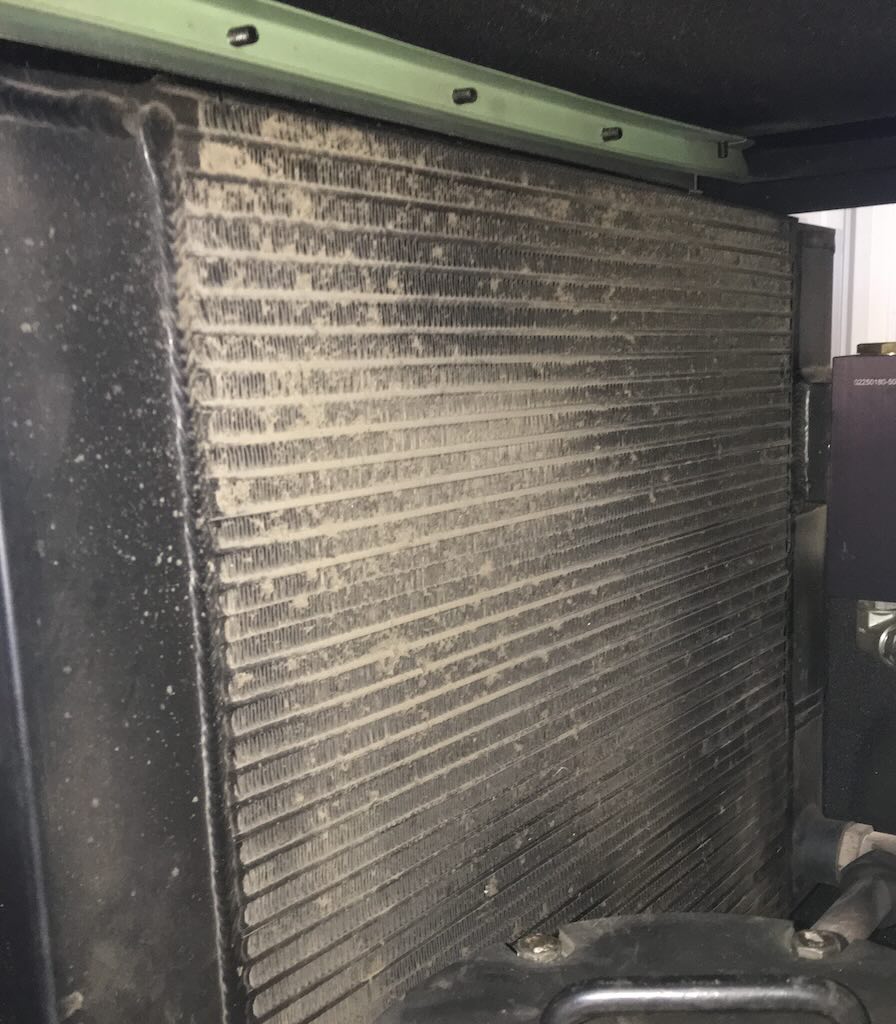
Automated monitoring and system management benefits
Compressor manufacturers recognize the importance of system monitoring and offer options to provide operators real time views of compressor performance — outside of a regular service call. Internet-based systems can transmit operating data to cloud-based systems that presents data for facilities technicians to monitor and review. These systems are often accessed through a portal maintained by the compressor manufacturer and can be packaged in with preventive maintenance agreements.
Modern production operations have the option to integrate building management systems to control systems and monitor critical operations. Compressor controllers can provide communication options through standard protocols such as Modbus and BACnet. By connecting to the compressor controller, systems integrators can provide plant management systems with information on compressor run status, maintenance alerts, warnings and faults and even offer remote start/stop controls in between service calls.
Using data to monitor trends and drive predictive maintenance
There are many data points that tell the overall story of the compressed air system, and various means by which those data points can be obtained (remote monitoring, vibration analysis and oil sampling). By analyzing this data and using the information to monitor and track trends, a technician can begin developing a predictive maintenance program to keep the compressor performing and avoid unplanned downtime.
In oil sampling, the samples collected during routine service will show the progression of fluid degradation over time among other information. Compressor fluids also have varying life expectancies under normal conditions based on base stock and additive packages. Compressor run profiles and environmental conditions can lead to reduced fluid life expectancies in some situations. There are several things to learn from an oil sampling including:
-
pH levels that suggest warning signs of corrosive wear of bearings.
-
Acid number (AN) to indicate the remaining useful life of the fluid. Oil oxidation causes acidic byproducts to form. High acid levels can indicate excessive oil oxidation or additive depletion and can lead to corrosion of internal compressor parts.
-
Viscosity to measure the resistance of a fluid to flow at a specific temperature. A higher viscosity may indicate higher operating temperature.
-
Fourier transform infrared (FTIR) spectroscopy provides molecular information including additives, fluid breakdown products and external contamination. This test determines the parts per million (ppm) of wear metals and lubricant additive metals in the oil sample. Wear metals are those that originate from an internal component of the compressor.
-
Water levels, which can identify leaks.
-
Inductively coupled plasma (ICP) spectroscopy measures and quantifies elements associated with wear, contamination and additives.
By monitoring fluid sample results and tracking fluid condition progression, fluid maintenance can be scheduled before sample reports return a critical result that can lead to mechanical damage in the compressor system. Compressor fluid that is out of specification for acidity, pH or viscosity can cause premature wear to rotating (bearings) and sliding (valves) components that reduces the compressor’s longevity.
While it’s not necessary to gather compressor vibration data with every service visit, establishing a base line for each machine can show the starting point for overall condition of the rotating components. A vibration specialist will analyze the raw data from the vibration monitoring equipment and provide a report detailing abnormalities and actionable recommendations. By watching the rate of change over time, the condition of motor and air end bearings, as well as couplings can be reviewed and acted on as necessary where trends show accelerated degradation. Maintenance and repair of these components based on vibration reporting can be scheduled ahead of significant damage and subsequent failure.
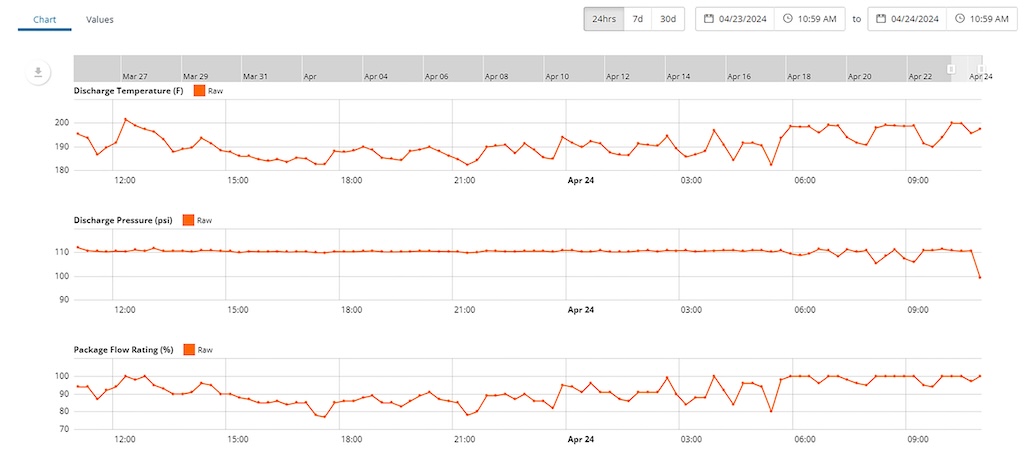
Sizing, location and load impacts
Not every compressed air system is perfectly sized and operates at peak efficiency. Production demands can change over time, compressors are purchased within allocated budgets meaning installations are often necessary in less-than-ideal environmental conditions. Most compressors run best when running fully loaded with minimal cycles and start/stop scenarios. Since this is not always possible, using information from the compressor controller to understand run conditions can help determine appropriate maintenance schedules.
Compressors sized for peak demand may accumulate a higher number of load cycles due to varying plant operations. While this is normal, it is important to monitor the total number of cycles to be sure the compressor is tuned appropriately for the system. While there is not a set standard for the number of load cycles, the lower the better.
For example, a compressor running in a process with consistent demand may experience three-to-four load cycles per hour. However, a compressor that operates in a process with varying demand over short periods can see a much higher number of cycles per hour. A compressor with a higher number of load cycles can require more frequent maintenance of regulators, valves and other control system components to address wear and ensure reliable operation.
Compressors often operate in dusty or dirty conditions. Debris and other particles can accumulate on filters and heat exchangers, resulting in less efficient operation. In severe cases, air flow can become entirely obstructed. High operating temperatures can break down compressor fluids that lead to reduced fluid life and accumulate on heat sinks that increase operating temperatures of electrical components. Compressors should be monitored for consistent temperatures in range of the manufacturer guidelines. When temperatures start to rise, it’s time to inspect the fluid levels, heat exchangers, thermostatic valves and package filtration.
Warning and fault history for the compressor can also provide a preview of impending problems. Many compressors utilize sensors that measure oil filter differential pressure, air filter pressure drop, and other critical operating parameters. When these parameters fall outside of the acceptable operating ranges, the compressor controller will present a warning or fault (depending on severity) to alert the operator.
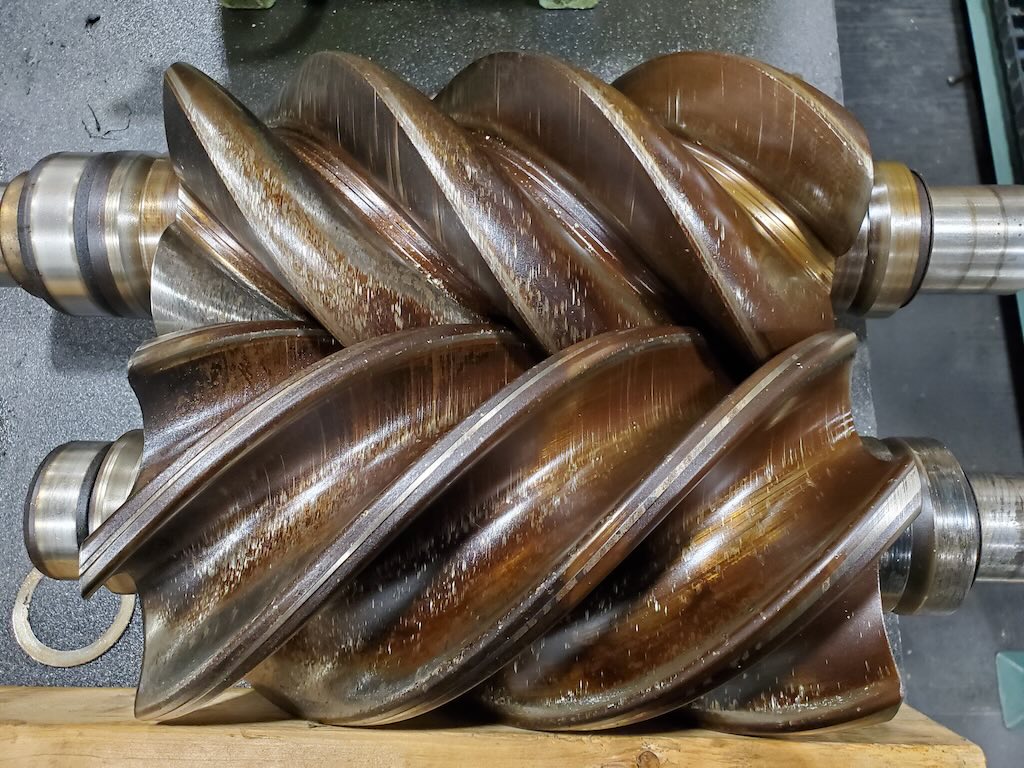
Setting appropriate maintenance schedules
Air compressor manufacturers will prescribe preventive maintenance guidelines based on typical operating conditions, but they don’t fit all situations. Predictive maintenance leans on historical operating data and equipment observations unique to each compressor system to drive proactive maintenance scheduling, which may evolve as production demands change. By monitoring operating parameters and analyzing data collected from the compressor, service providers can put together predictive maintenance programs that address key service points before they lead to problems or breakdowns.
Regular and predictive maintenance offers many benefits including a more efficient and reliable compressed air system. By leveraging different data analytics sources, predictive maintenance empowers organizations to detect and address potential issues before they escalate and cause unplanned downtime — or worse. With all this information available, these so-called “routine” maintenance checks are, in fact, an indispensable component of a well-performing compressed air system.