Some things to think about when it comes to reliability.
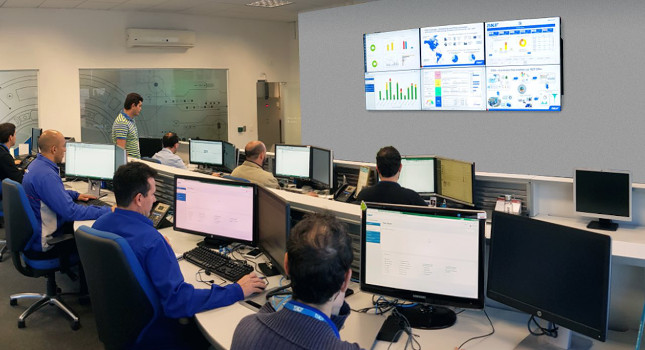
To maximize productivity while lowering operational and maintenance costs, plants must attain the right performance from their rotating equipment to meet business objectives and give companies a competitive edge.
Optimizing a rotating equipment maintenance program may seem like a daunting task. However, the competitive advantages gained from reduced unplanned downtime, increased productivity and higher profitability, while lowering the total cost of ownership of a machine’s lifecycle, make the exercise well worth the effort. Let’s look at some steps that will help optimize rotating equipment performance within a strategic maintenance program.
Assess your current program
The process of setting up any program begins with conducting a thorough assessment of existing operations and practices. Assessments can be done using internal resources or by a third party. There are advantages and disadvantages to either option.
Questions to ask before conducting a risk assessment include:
- Do you have the internal resources, expertise and time to benchmark the different plants within the company?
- What money can be appropriated to conduct the test by either internal or external resources?
- How quickly can the assessment be conducted so that improvement action items can be assigned?
Whether companies conduct the assessment internally or with an outside partner, an integrated risk-assessment strategy starts with understanding how equipment is currently performing and what improvements can be made to attain and maintain optimal performance.
The exercise will help to gain insight and information that will not only maximize the performance of equipment, but also overall equipment effectiveness (OEE), plant profitability, competitiveness, plant safety and maintenance program efficiency.
The process of rotating equipment maintenance programs focuses on basic care, precision maintenance, condition monitoring and lubrication management.
Basic care, early awareness
A basic care program enables operators to accurately and consistently record, trend, store, communicate and act upon process and inspection data. Automating these tasks ensures consistency, accuracy and timely communications that enhance production and maintenance strategies.
Maintenance managers have a large group of machines to look after and may not have the capacity to follow a precision maintenance processes. At the same time, equipment maintenance is becoming more complicated due to ongoing technological advancements and stricter environmental and safety laws that are placing more pressure on these functions.
Recognizing a manager’s need for supplemental resources, internally and externally administered training programs should be executed for companies to achieve their maintenance goals. A well-run precision maintenance and training program will have a major impact on maximizing the service life of rotating equipment.
For example, at the core of most rotating equipment is a bearing. An accepted rule of thumb is that 99.5% of all bearings do not achieve their useful life. Bearing life is impacted by the way it was mounted, aligned, lubricated, maintained, operated, dismounted and analyzed through previous condition monitoring. By applying the right maintenance practices, you can considerably extend your bearing’s service life and increase plant productivity and efficiency.
Condition monitoring
Avoid unplanned downtime by detecting and diagnosing impending machine failures. Applying condition monitoring and data visualization, plant managers can proactively find and diagnose problems before they have an effect. This allows plant managers to better organize and prioritize repairs, too.
The keys to a successful condition monitoring program include knowing:
- What to listen for
- How to interpret it
- When/how to put this knowledge to use
This enables the repair of problem components before they fail. Not only does it help plant personnel reduce the possibility of catastrophic failure, but it also allows companies to order parts in advance, schedule personnel and plan other repairs during the downtime.
Condition monitoring is an important element in the maintenance strategy of most major industrial plants. The process involves measuring physical parameters that indicate a machine’s health. Departures from normal are detected and analyzed with corrective actions. Understanding what parameters to measure and how to apply this to machine life-cycle management is where new value is discovered.
A multitude of technologies are used to detect the health of rotating equipment. The challenge most companies face today is understanding what to do with all the data they have collected. Vibration data may go to one group of people, oil analysis data to another, thermographic images to another, process data to another, basic care to another and so on.
The Industrial Internet of Things (IIoT) is rapidly changing how fast and how much process and machine data is available, as well as how cost-effective it is. The digitalization of technology is opening the doors for maintenance and operations managers to rethink how they can become more efficient and effective in their roles. Their struggle, however, continues to be how to interpret the data to make actionable decisions to ultimately avoid unplanned downtime and assure equipment is available to fulfill orders in a profitable way.
In addition to emerging technologies, companies are challenged with recruiting, training and retaining the next generation of plant engineers. As a result, companies are evaluating how the cloud, big data and wireless devices will transform how machines are operated, managed and maintained.
Lubrication management
The historical rule of thumb is that the percentage of lubricated-related rotating equipment failures is nearly 50%. Not using the right type of lubrication, the right amount or at the right time are three of the primary reasons for lubrication-related failure. Contamination from improper sealing systems and moisture egress are also contributing factors. A properly conducted assessment of existing lubrication practices, maintenance history and equipment failures will provide insight into gaps and opportunities for improvement.
Solutions range from operators/technicians performing scheduled walk-arounds with grease guns to cannister-mounted systems (calibrated to dispense a specific amount at a specific frequency) or a fully automated recirculating lubrication system that removes foreign particulate and moisture from the lubricant.
The more sophisticated systems have flowmeters that can be manually or remotely adjusted to compensate for changes in machine speed, load and temperatures. Feedback can be sent to the operators and condition monitoring teams to gain more insight into the health of the plant’s rotating equipment so that decisions can be made around production and maintenance planning.
Eliminate recurring failures
So, what differentiates a good rotating equipment maintenance program from a great one? The ability of a program to not just prevent and identify pending machine failures, but also the ability to eliminate their occurrence or reoccurrence. This becomes a challenge to many organizations even though they feel they have many of the necessary components in place.
Whether a company elects to address the elimination of reoccurring failures internally or with a partner, it is important to administer a method for identifying and fixing root causes by connecting disparate technologies and rotating equipment expertise.
A well-designed system should provide access to insights from various sources, offer better interpretation of analytics, improve lubrication and spares management and move towards a performance-based approach.
It’s critically important to apply the right solution in the right way so the problem doesn’t reemerge in the future. Processes and procedures should be built with this in mind, ensuring that today’s repairs last through tomorrow and beyond.