Pneumatic and hydraulic controls are critical to the manufacturing industry, and implementation requires careful consideration of safety and maintenance requirements
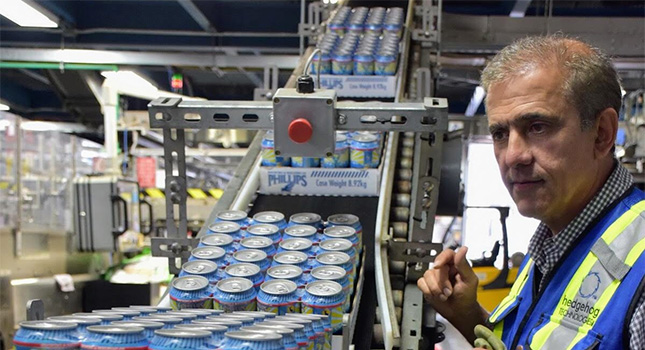
Learning Objectives
- Learn how a “find and fix” mentality can mobilize workers to identify electrical safety hazards before they become problematic.
- Know why you cannot skimp on equipment safety checks.
- Understand how training and communication play a critical role in putting a culture of electrical safety into action.
Maintenance insights
- Hydraulic and pneumatic systems play a large role in manufacturing processes and plants.
- Without ongoing maintenance and replacement of hydraulics and pneumatics, systems and plants would shut down, crippling a supply line or business.
Pneumatic and hydraulic controls have a variety of applications for the manufacturing industry. Part movement and manipulation, cooling, shaping and forming can be automated with continued advancements in digital communication and control.
Furthermore, new opportunities to take advantage of hydraulics and pneumatics have presented themselves with ongoing technological advances in the field. As these technologies become more prevalent in manufacturing, it is important to consider the safety, regulation and maintenance requirements of these systems to ensure safe and efficient operations.
Safety considerations
Pneumatics and hydraulics play a critical role in many manufacturing processes and as such, it is critical to understand the risks of these systems so that they can be addressed properly. One of the key safety considerations is the potential for fluid leaks. Pneumatic systems rely on compressed air and leaks can lead to sudden changes in pressure that can cause equipment failure or even injury to workers.
To minimize these risks, it is recommended to use high-quality components, particularly for hose fittings and couplings and to implement regular inspections of these components to identify and repair leaks before they pose a hazard.
Pneumatic controls typically use highly compressible gasses, such as air or nitrogen, which can rapidly expand when released to the surroundings in the event of a leak. This risk can be reduced by implementing a fail-safe to shut down the system in the event of a sudden pressure loss. However, it is important to understand the risks of pressurized fluids before implementing a pneumatic system in a manufacturing plant.
Pneumatics safety and maintenance
The low compressibility of hydraulic fluids helps to make these systems safer to work with at high pressures. While pressure is less of a concern with hydraulics, fluid leaks can still cause harm to both workers and the environment. A leak in a hydraulic line could result in injury to workers caused by exposure to a toxic substance and the fluid may seep into the ground or evaporate, causing an environmental hazard.
Similar to pneumatics, the use of high-quality equipment combined with regular inspection will reduce the risk of leaks. An additional mitigation strategy is to create physical barriers, such as troughs that will act to catch and contain any fluid that may leak out of hydraulic lines.
Another safety consideration is the potential for system failure; pneumatics and hydraulics rely on pressurized fluid to operate and a loss of pressure can cause equipment to stop working or malfunction. A common mitigation strategy for system failures is to implement redundancies, which are backups for critical components that allows for the system to continue working while a failed component is replaced, reducing the risk of injury and minimizing downtime.
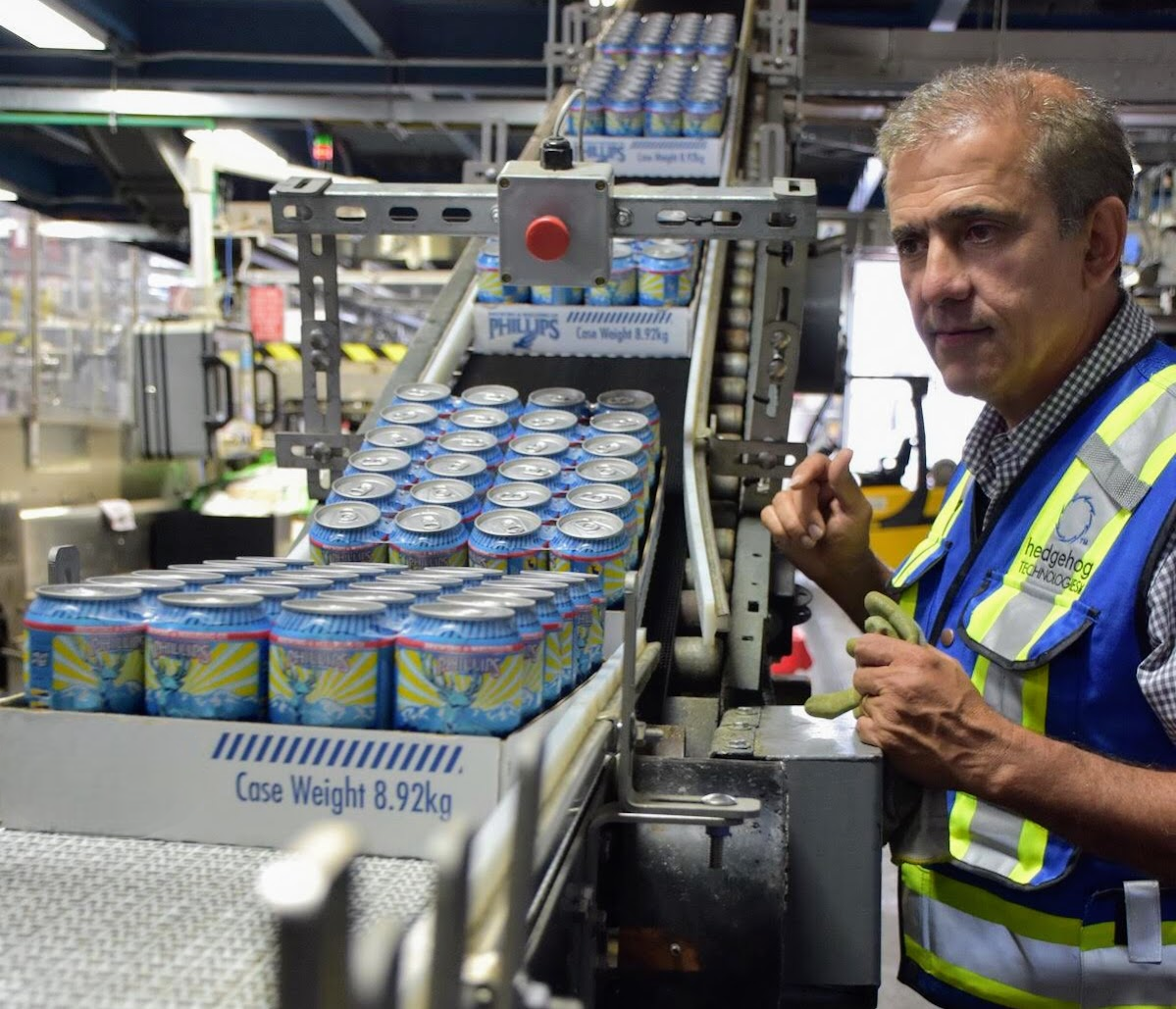
It is also important to consider the potential for physical harm when working with pneumatic and hydraulic systems. These systems are often implemented to move large objects quickly and precisely and as a result they can generate large amounts of force over short intervals. Entrapment is a potential risk in this situation; clothing or limbs can be caught in the moving parts of the mechanism, which can cause serious injury or death.
Workers must be trained to properly use and maintain pneumatic systems to minimize the risk of injury. Proper training, including hands-on training with the specific pneumatic systems in use, can help workers to understand the potential hazards and take the necessary steps to stay safe. This can include training in following the proper safety guidelines and regulations, using proper protective equipment and following lockout/tagout procedures to prevent accidental activation of equipment during maintenance or repair.
Maintenance requirements
While safety considerations are critical to the successful implementation of hydraulic and pneumatic control systems, it is also important to consider the maintenance requirements of these controls during their design and installation.
Poorly maintained pneumatics and hydraulics will be more prone to failures, any of which can create a potential hazard in the plant. The first consideration in this vein is regular inspection of components. With a proper inspection plan, leaks and jams can be spotted before they become an issue and repaired.
Other maintenance considerations for pneumatic and hydraulic controls are:
-
Lubrication: Pneumatic equipment requires regular lubrication to ensure proper operation. Without proper lubrication, components will undergo increased wear and can seize, causing further damage and requiring lengthy shutdowns to repair or replace. The lubrication schedule should be based on the manufacturer’s recommendations and the specific conditions of the manufacturing plant.
-
Cleaning: Pneumatic equipment should be kept clean to ensure proper operation. This includes removing dust and debris from the equipment and cleaning the air filter. Excessive dust on or around the moving parts of pneumatics can make its way into the seals and cause a leak or premature failure.
-
Replacement of worn or damaged parts: Worn or damaged parts should be replaced as soon as possible to ensure that the system is operating safely and efficiently. If damaged parts are left unrepaired, they can cause further damage leading to more expensive repairs down the line.
-
Air filter replacement: Regularly replace the air filter to ensure that the compressed air is clean and free of debris. Clean air is essential to the proper operation of pneumatics, as dust can clog valves and damage seals.
-
Monitor the pressure: The pressure in the pneumatic system should be checked regularly to ensure that it is at the correct level. Modern pneumatics typically make use of real-time pressure monitoring through programmable logic control. If pressure is too low, the system may act with too little force or too slowly to perform its task effectively. If the pressure is too high, it can result in lines, valves and seals leaking.
-
Check for leaks: Regularly check for leaks in the system and repair them as soon as they are detected. As discussed above, leaks in pneumatics and hydraulics can cause several safety and maintenance issues throughout the plant.
-
Keep accurate records: Keeping accurate records of the maintenance performed on the pneumatic system will help ensure that all necessary maintenance is performed on schedule.
-
Follow manufacturer’s recommendations: Always follow the manufacturer’s recommendations for maintenance, including lubrication, cleaning and replacement of parts.
A proactive approach to system inspection and maintenance can save a plant on more costly repairs caused by faulty equipment in the future, as well as protect workers from injuries caused by failures. Implementing these practices early and working with the manufacturer to determine the best approach will ensure the best performance and value to the plant for a given control system.
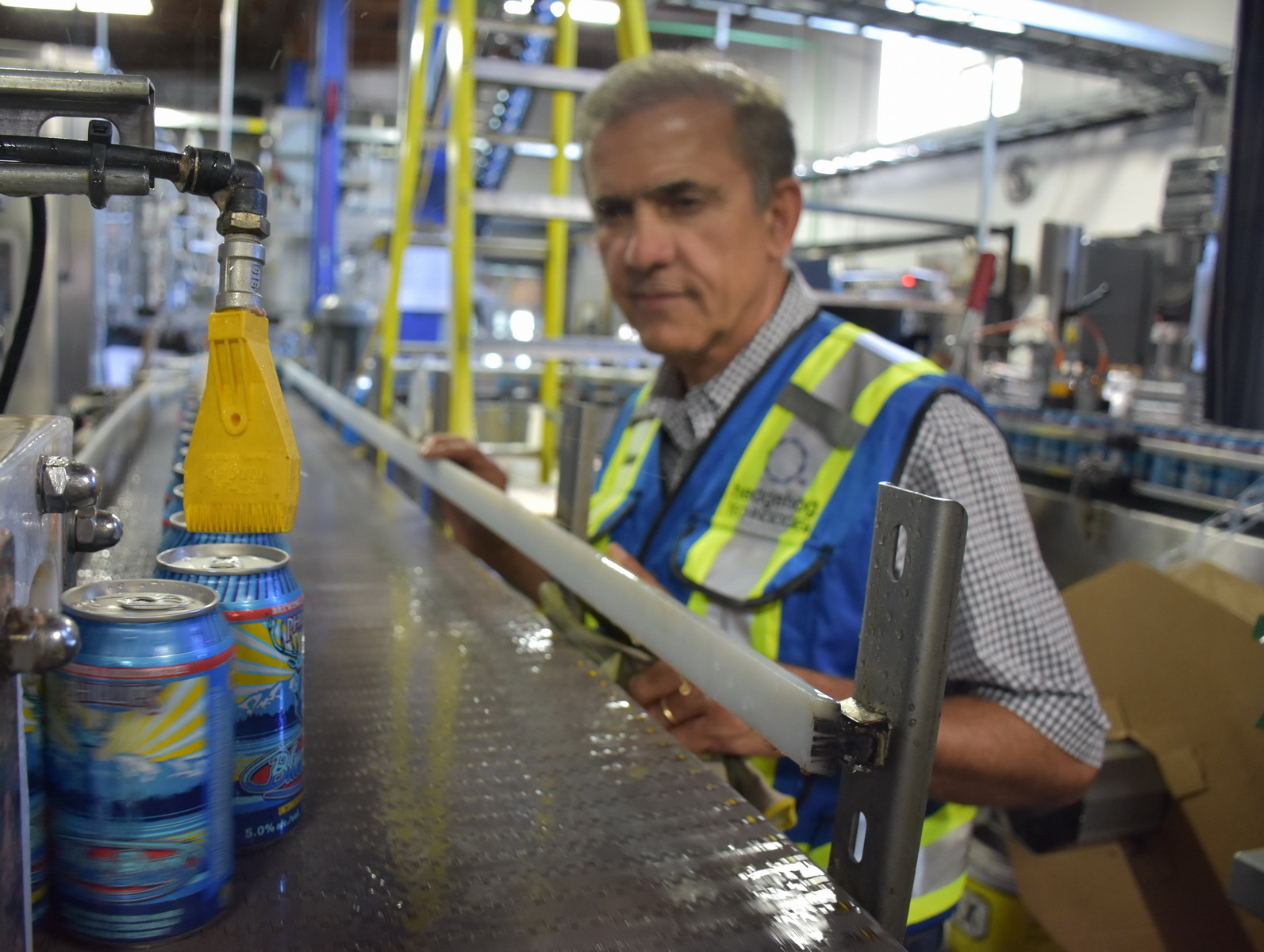
Pressure regulation
Pressure regulation is an important aspect of pneumatic controls, the primary purpose being to control the amount of compressed air delivered to pneumatic actuators and other components, ensuring that they operate at the correct pressure. This helps to maintain consistent and accurate performance, while also reducing the risk of equipment failure and injury to workers. Some common methods of pressure regulation include:
-
Mechanical pressure regulators: Mechanical pressure regulators are relatively simple and reliable, using a spring-loaded piston and a diaphragm to control the flow of compressed air. They can be prone to wear and tear over time.
-
Electro-pneumatic pressure regulators: Electro-pneumatic pressure regulators use electrical signals to control the flow of compressed air. They are more precise and flexible than mechanical pressure regulators and can be integrated into automated control systems.
-
Proportional pressure regulators: Proportional pressure regulators use electronic sensors and feedback to control the flow of compressed air, providing highly accurate pressure control. They are typically used in applications where precise control is critical, such as in robotics and high-speed manufacturing processes.
As with safety considerations, regular maintenance is important in the proper function of pressure regulators. All regulators require calibration and inspection at specific intervals to ensure that they continue to perform accurately and reliably. Regular maintenance can help extend the life of pressure regulators and reduce the risk of equipment failure.
What are the other maintenance risks and considerations?
A potential risk involved with using compressed air in pneumatic controls is the buildup of flammable gas. In systems that use oil-lubricated compressors, the oil can mix with compressed air and create a flammable gas mixture which can ignite under certain conditions.
The buildup of flammable gas is somewhat inevitable in any compressed air system, but the risks can be minimized. As with other risk factors, proper maintenance of oil-lubricated compressors will reduce the risk of oil mixing with compressed air. Oil-free compressors can also be used to eliminate flammable oils from the system; however they tend to require more regular maintenance and replacement than their oil-lubricated counterparts.
Finally, proper ventilation of compressed air lines will reduce the amount of accumulated flammable gas in the system.
Temperature regulation is another consideration for the use of hydraulics and pneumatics. When the working fluid temperature fluctuates significantly from what is specified, it will cause the viscosity to change, reduce the effectiveness of seals and increase the chance of fluid degradation and contamination. These changes can lead to losses in performance, reduction in efficiency and equipment failure. The seals used throughout hydraulic and pneumatic control systems are sensitive to temperature and significant deviation from the manufacturer’s specifications will reduce the performance of the seals and increase the risk of failure. Something as seemingly harmless as a worn-out O-ring can lead to much more significant failures and potential injury if left alone.
There are methods of regulating the temperature in these systems, such as heat sinks and cooling mechanisms, as well as temperature sensors to monitor system temperature. With compressed air, it is also important to implement an air-drying system, which will remove moisture from the air and reduce the risk of condensation in the lines.
Corrosion in pneumatic systems is influenced by a few factors. Corrosion can occur as a result of exposure to moisture, acids or contaminants being present in the system. A few common methods of mitigating this are:
-
Air drying: Like temperature regulation above, dry air will limit the moisture present in the system, reducing the risk of corrosion
-
Lubrication: In addition to reducing wear, lubricants can create a barrier to protect components from corrosive substances.
-
Materials selection: As with other fields, materials selection plays an important role in postponing corrosion in pneumatics. It is important to consider materials that will both be compatible with the manufacturing environment and the controls system
-
Positive pressure: Holding positive pressure in the pneumatic system will ensure that contaminants are forced out if any leaks should form.
Different operating fluids will also affect the rate of corrosion. In pneumatics, the most common operating fluids are air, nitrogen and carbon dioxide. Corrosion is less of a concern in hydraulic controls, as the operating fluid serves to lubricate the system and provides a barrier to corrosive substances.
In summary, hydraulic and pneumatic control systems offer many benefits in manufacturing, but it is important to understand several aspects of their operation so that they can be addressed during implementation. Between safety considerations, maintenance and pressure regulation, there are any number of ways that pressurized systems can affect other areas of a plant, so proper planning and maintenance in accordance with relevant standards and regulations is essential.