Machinery can increase production with less labor, but heavy machinery also presents safety hazards and workers must be fully trained and aware of the machine operations to avoid injuries
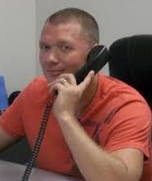
Machinery in the workplace provides benefits of increased production and less labor. Heavy machinery also presents safety hazards and workers must be fully trained and aware of the machine operations to avoid injuries. There are several safety tips to follow to help prevent accidents in manufacturing plants.
Never remove machine guards
Machinery guards come in many types, but they are all designed to protect the operator. Guards prevent debris and sparks from flying out of the equipment. Barriers are also designed to prevent a worker from coming into contact with cutting tools or getting trapped in moving parts.
The only time guards can be removed safely is when the machinery is taken out of service for maintenance or repairs. This work must be done by trained, authorized personnel. Workers must report any damage to barrier systems and the equipment must not be used until the guard is inspected or replaced.
Accidents frequently occur when a worker thinks a job will only take a second and bypasses the barrier system. Injuries also come from employees reaching around a guard to dislodge a jam in the machinery. Full training is necessary to prevent these kinds of accidents.
Use Personal Protective Equipment (PPE)
Even with machinery guards, many operations require the use of personal safety equipment. Common equipment for most manufacturing plants includes safety glasses, gloves and closed-toe shoes. Full wrap goggles give the best protection, as this style eliminates the entry of debris through the side of the glasses.
Gloves should fit well, but not too snugly. Loose gloves can become caught in equipment. Cut-resistant gloves should be utilized by anyone working around cutting equipment or sharp edges. Workers must be reminded the cut-resistant gloves only reduce the chance for injury; they do not completely prevent it.
Proper footwear is required for a couple of reasons. Workers need to protect their feet from dropped or falling objects. Slip-resistant soles reduce the likelihood of accident falls in wet or slippery locations. Job specific PPE must be used when required. These items can include face shields for welding operations or breathing masks for working with airborne hazards.
Proper training
All workers must be properly trained on any plant equipment before they start operating it. All machinery has different safety features and techniques for operation. No employee should ever be allowed to operate equipment without instruction. The person providing the training should assess the worker’s skills and make recommendations for any modifications needed to make the process easier and safer for the trainee.
Awareness of surroundings
Safety requires being aware of the surroundings. Workers must know what other equipment or machinery is operating in the immediate area. Awareness also means the workers should never operate equipment under the influence of alcohol or other substances than can delay reaction times or interfere with clarity.
In addition to working on their own machinery safely, employees must be discouraged from distracting other workers during operations. Talking to, or otherwise distracting an operator, can quickly lead to an accident.
Forklift paths should be marked and workers should avoid these paths while walking through a plant. Lift operators may not always see an individual if their line of sight is blocked. Workers must avoid the use of headphones while walking, as these can interfere with their ability to hear an equipment warning. While workers can have fun while working, horseplay should never be tolerated.
Follow maintenance schedules
Plant machinery has maintenance schedules for a reason. By following the required procedures, equipment will be kept operating at peak performance. When servicing is not completed correctly, machinery can overheat due to lack of lubrication, or suddenly jam due to a broken belt or drive gear.
If filtration equipment is in use, the filters must be periodically inspected and replaced. Blocked filters will not perform properly and can lead to undesirable exposure to workers or environment. Blades and bits must be sharp to provide clean and safe cutting. When cutting equipment dulls, it is more likely to snag than cut through the material.
Accidents are expensive in many ways, by following basic safety guidelines, you can make sure that your employees avoid injuries.
Jeff Maree is the Product Specialist at Eaton Filtration Online a leading online supplier of Eaton filtration products for a wide range of liquid handling and filtration needs. Jeff assists plant managers and makes sure they are getting the correct product to keep their machines and workers safe.
Update: As of May 1, 2016, Eaton Filtration Online re-branded to Commercial Filtration Supply. The company has remained the same, including staff and products offered. The new website is linked here:
Commercial Filtration Supply – Authorized Eaton Distributor.