As certain processes and steam turbines demand the use of higher pressure and higher temperature boilers, superheated steam may be too hot for equipment with structural temperature limitations. Therefore reversing that process becomes just as important because there will always be cases where superheated steam is too hot and too dry especially in power and process applications.
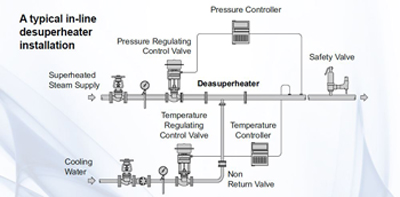
As certain processes and steam turbines demand the use of higher pressure and higher temperature boilers, superheated steam may be too hot for equipment with structural temperature limitations. Therefore reversing that process becomes just as important because there will always be cases where superheated steam is too hot and too dry especially in power and process applications. For example in process plants that produce their own power by utilizing a steam driven turbine, they also use steam within their production process directly or indirectly within heat exchangers to heat various gases. The superheated steam required by the process needs to be desuperheated so that other processes and associated downstream piping and equipment are not damaged.
Effective desuperheater design
Most all desuperheaters work on the same principle of operation; cooling water is brought into contact with the superheated steam so that it evaporates and ultimately cools the steam to a temperature closer to the saturation point. While a desuperheater is capable of cooling down to the system saturation temperature, typically they are designed to produce outlet steam temperature 5 – 10 °F above that point. This design effectively limits the amount of condensate that is created and must be removed. The amount of residual superheat left in the output steam needs to be determined by process requirements.
Steam flow turndown
A common error with desuperheater design that can affect initial system cost and have performance consequences is to specify more flow turndown capability than is required. While designing a system to meet future anticipated plant growth is insightful, a desuperheater should operate between 10% and 100% of its maximum flow rate to be efficient. An oversized desuperheater design can generate much more water droplet fallout due to inadequate flashing and mixing of the cooling water. The extra water fallout can collect in the bottom of the pipe with the condensate. The desired temperature and residual superheat is therefore not maintained.
Residual superheat
Residual superheat is the amount of remaining superheat in the output steam at the desuperheater outlet. Generally process system requirements fall into one of three categories:
-
No residual superheated steam, saturated steam from the desuperheater is acceptable. This is the easiest system to design for and the least expensive
-
Critical control of the amount of residual superheat is not required. A range of temperatures above saturation is acceptable
-
Residual superheat must be controlled very accurately.
-
By paying close attention to specific design components such as using an electronic temperature controller, correctly sized valves, correct pipe sizing and orientation, etc., 3-5° F of superheat above saturation is required to meet downstream equipment needs
Use the correct componentsThe desuperheater itself is only one component within a correctly designed system. It is common to have ten or more individual components in the system that all work together! So it is easy to see why systems engineering and understanding how the system components interact are paramount to efficient performance. An inlet steam control valve with pressure controller, cooling water control valve and temperature controller, temperature sensing element, piping, and desuperheater are all commonly used components within a desuperheating station which must work together.
A typical mistake that is made in component selection is the under sizing or oversizing of control valves. For example, if a desuperheating station is designed for a 30:1 steam flow turndown, its associated steam control valve must be sized to closely match this flow. If a control valve with a 20:1 turndown is used, it will not allow the system to work properly. Steam temperatures may never be reached as well.
Attention to system design
Correctly sizing the downstream steam line piping will insure adequate low-pressure steam velocity and water evaporation. Superheated steam has a recommended velocity of 100 feet per second to 300 feet per second within a steam distribution system. Because steam is considered a compressible fluid, capacity depends on pipe size and steam pressure and there will always be an associated steam pressure drop for a given size diameter and length of piping. When sizing and selecting steam piping remember to choose the pipe size according to the additional steam flow as a result of added superheat otherwise there will be capacity restraints.
Additional design considerations include spray nozzle cooling water characteristics such as water source, quality, pressure, temperature, and exposure time. The cooling water should come from the boiler feed water (BFW) taken from the pressure side of the boiler feedwater pump. It should be demineralized and deionized so return condensate is an acceptable source also. (Municipal water may be too hard). Water pressure must be equal to or greater than system steam pressure but that amount will vary based upon the type of desuperheater selected. The temperature of the cooling water determines how long it will take for the water to reach its saturation temperature before flashing, how long the droplets remain suspended in the steam, probability of droplet fallout before flashing, and the amount of turndown. Ideally, water temperatures should be as close as possible to the vaporization point so the higher the better. This improves enthalpy transfer efficiency and the generation of the least amount of additional condensate loading to the distribution system.
Online desuperheater sizing software is now available from various manufacturers to aid in designing desuperheating systems. Consulting a steam system specialist is always recommended before specifying and ordering a desuperheater no matter what technology is used. Like an improperly sized steam control valve or steam trap, the wrong desuperheater will either not allow superheated steam to reach the optimal residual superheat temperature or add water to the condensate system. A good desuperheater system design limits those risks and will ultimately save on improved energy costs gained through efficiency.
Content provided by Spirax Sarco, originally published in Steam News. Edited by Anisa Samarxhiu, Digital Project Manager, CFE Media, [email protected]