Maintenance of electrical systems is a necessary process that often gets overlooked
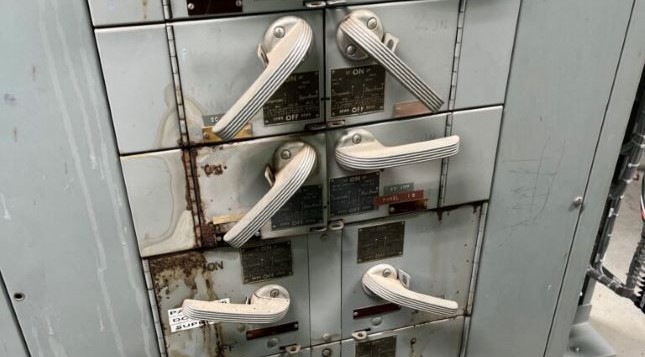
Learning Objectives
-
- Learn the proper maintenance of an electrical system.
- Understand the consequences of an improperly maintained electrical system.
- Know the codes and references to use in future design.
Maintenance insights
-
Maintenance of electrical systems is a requirement, not a suggestion. Here are things to watch.
-
A neglected power system may function normally for many years until a catastrophic event occurs.
Maintenance of electrical systems — despite significant evidence showing that is important not only for protection of personnel and equipment, but also for reducing total operating costs — has often been one of the first processes to be disregarded, forgotten about, considered not worth the cost or otherwise left for tomorrow that never arrives.
Though in recent years the importance of electrical testing and maintenance has appeared to increase and the practice be taken more seriously within the electrical industry, it is still often considered a want instead of a need. With the upgrade and adoption of NFPA 70B: Standard for Electrical Maintenance in 2023, the importance of electrical testing and maintenance has been effectively codified, becoming a requirement instead of a suggestion.
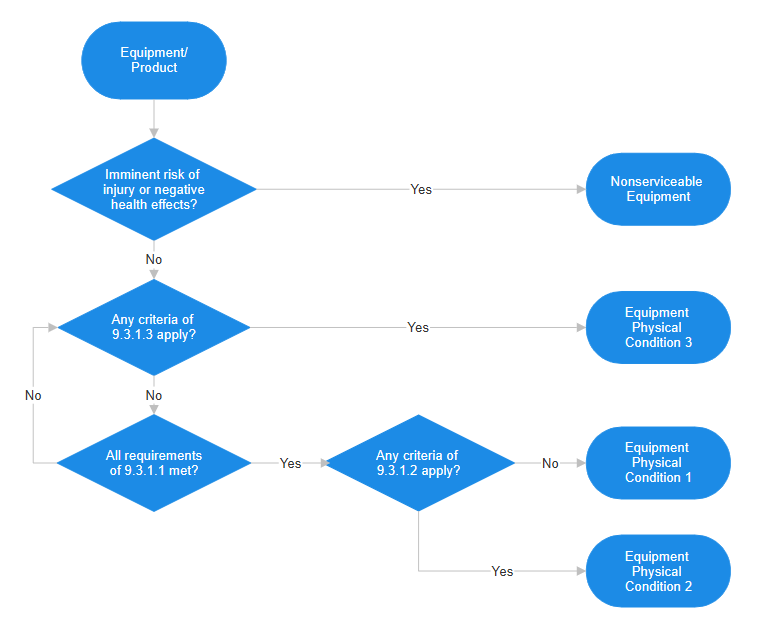
NFPA 70B has been in publication for almost 50 years as a recommended practice, but is not the only source requiring, recommending or otherwise discussing the electrical maintenance (and testing). IEEE provides guides on how to perform testing — including general test procedures for various types of equipment, calibration requirements for test equipment and other such documentation. Equipment manufacturers provide detailed instructions on the types and frequency of maintenance that should be performed on their specific types of equipment.
However, there are two overarching publications that guide the overall maintenance of electrical systems: NFPA 70B and American National Standards Institute (ANSI)/International Electrical Testing Association (NETA) Maintenance Testing Specifications (MTS) for Electrical Power Equipment and Systems. NFPA 70B approaches maintenance from a consideration for personnel and equipment, while MTS strives to ensure that electrical testing and maintenance is conducted correctly. The two publications overlap and complement each other in assisting personnel with appropriately maintaining their electrical systems.
NETA is a trade association that develops testing standards and specifications for electrical systems and ANSI may be a familiar entity in the electrical design world for the extensive material testing work they do. The ANSI/NETA MTS is a document of testing specifications developed by the two formerly mentioned institutions.
The MTS is a comprehensive specification guide designed to “assure tested electrical equipment and systems are operational, are within applicable standards and manufacturer’s tolerances and are suitable for continued service” (ANSI/NETA 2023).
Electrical maintenance codes, standards and guidelines
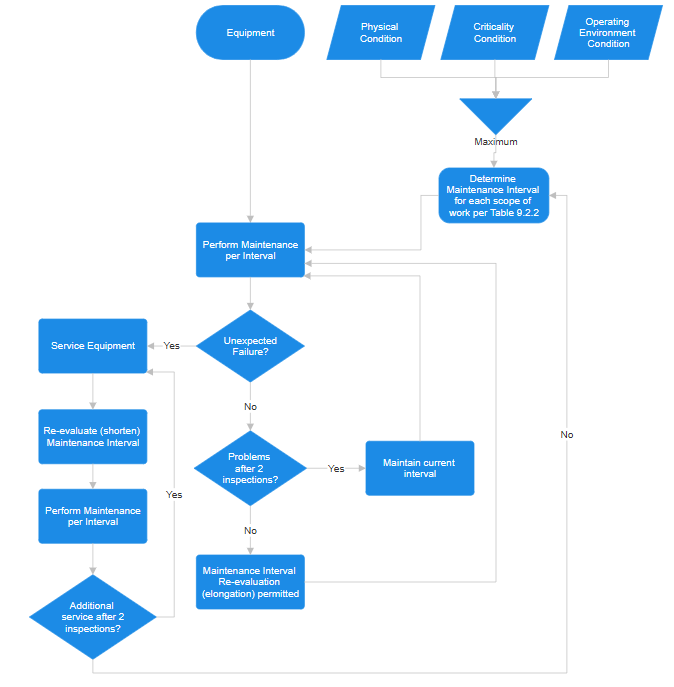
NFPA 70B was upgraded to a standard in 2023. As defined in NFPA 1: Fire Code, a recommended practice is “similar in content and structure to a code … but contains only nonmandatory provisions.” In comparison, a Standard, such as NFPA 70: National Electrical Code (NEC) “contains only mandatory provisions” in the main text and is “generally suitable … for adoption into law.” A code is “a standard that is an extensive compilation of provisions covering broad subject matter or that is suitable for adoption into law independently of other codes and standards.” In layman’s terms, a recommended practice details what should be done, whereas a standard or code details what must be done.
While an NFPA publication is not legally enforceable simply because it is a standard, it must be adopted by states or other authorities to gain legal force. However, becoming a standard strengthens the relationship between NFPA 70B and associated codes such as NEC and NFPA 70E: Standard for Electrical Safety in the Workplace.
Additionally, becoming a standard establishes a publication as an industry consensus, further reinforcing Occupational Health and Safety Administration (OSHA)’s ability to refer to NFPA 70B in determining where violations may have occurred. As discussed in an official OSHA interpretation, while OSHA does not enforce NFPA 70, NFPA 70E or NFPA 70B, it may use such industry consensus standards to “support citations for violations.”
A person reviewing NFPA 70B will notice significant overlap with portions of NEC and NFPA 70E, confirming the interconnected importance of proper installation, safety and maintenance procedures for designing and operating electrical systems efficiently and safely for personnel, equipment and processes.
The general requirements of NFPA 70B mandate that equipment “be maintained in accordance with the manufacturer’s instructions and applicable codes and standards.” In the absence of such instructions, equipment should “be maintained in accordance with industry consensus standards.” While NFPA 70B does not directly refer to ANSI/NETA acceptance testing specifications (ATS) and MTS in any standard requirements, it references both as industry consensus standards in the nonproscriptive informative annexes.
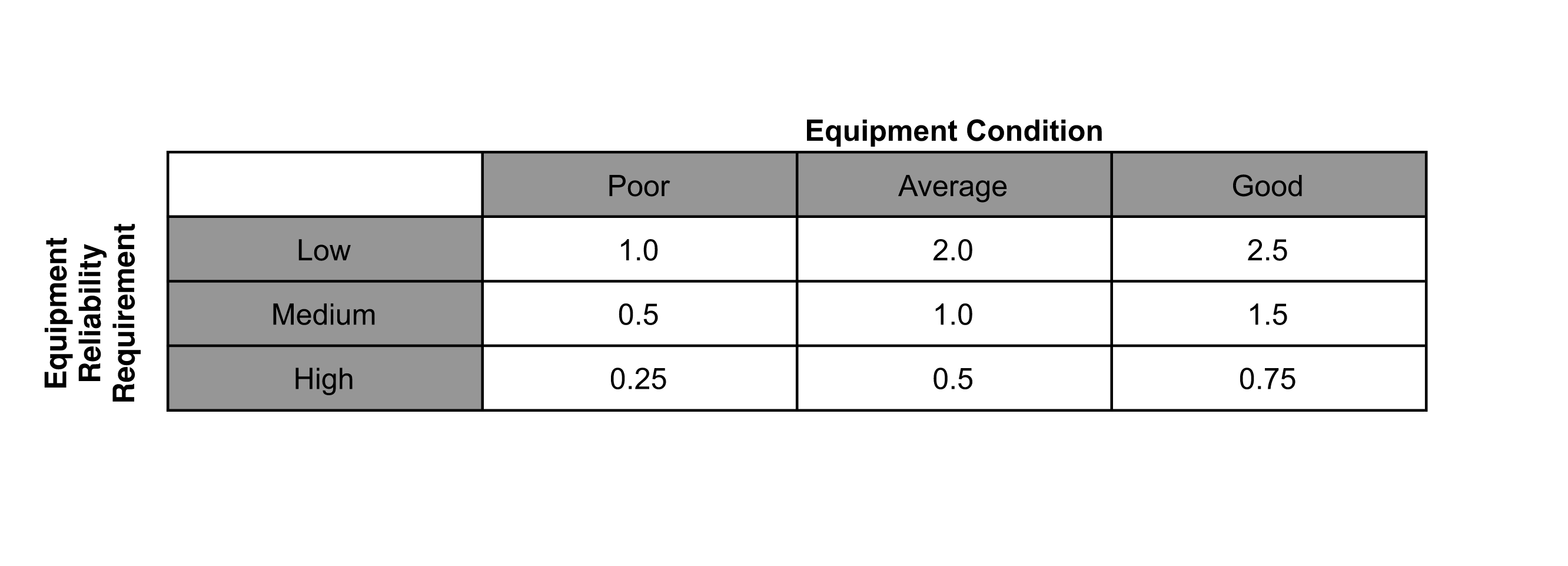
Chapter 4 of NFPA 70B provides general maintenance requirements, including that an equipment owner implement and document an electrical maintenance plan (EMP). The EMP must include and document elements such as an electrical safety program (refer to NFPA 70E), electrical maintenance and testing procedures, implementation of corrective measures and cleaning of electrical equipment. The EMP must be audited every five years or less.
Chapter 6 of NFPA 70B requires that an electrical system’s one-line diagrams be maintained up-to-date and that system studies — including short-circuit, coordination and incident energy analyses studies — be conducted and updated as necessary to support risk assessments.
Chapters 7, 8 and 9 of NFPA 70B discuss fundamental tests, field testing and test methods and recommended maintenance intervals. Fundamental tests include testing of connections and terminations and insulation resistance testing. Testing connections and terminations via infrared thermography, contact resistance testing and/or permanent heat sensors is vital to ensure connectors are not poor, which could lead to heating, sparking or failures.
Insulation resistance testing is important to confirm that the electrical equipment’s insulation is not showing signs of breaking down, which could lead to faults and flashovers. Field testing and test methods include brief discussions of general testing categories, personnel, equipment calibration and record requirements.
Chapter 9 of NFPA 70B provides recommended intervals for electrical equipment maintenance first based upon manufacturer recommendations and afterward based on the condition assessment of the equipment. The condition assessment determines the recommended interval based on the worst of a given piece of equipment’s physical condition, criticality condition and operating environment condition.
- Physical condition 1: Equipment appears in like-new condition, is clean, free from moisture intrusion and tight, has no unaddressed notifications or active recommendations and has been maintained according to the EMP.
- Physical condition 2: Equipment is like physical condition 1, except that maintenance results might deviate from past results, there are issues requiring repair or replacement or there are active notifications or recommendations.
- Physical condition 3: Equipment has missed the last two successive cycles required by the EMP, needs repair or replacement of major components or has active notifications or actions required.
Equipment may be in:
- Criticality condition 1 or 2: Failure of the equipment would not endanger personnel.
- Criticality condition 3: Failure of the equipment would endanger personnel.
- Operating environment condition 1 or 2: Rated for the environment where installed.
- Operating environment condition 3: Not rated for the environment where installed or where the environment has harsh chemicals, contaminants or extreme conditions.
Though there are variations, the recommended minimum interval for:
- Condition 1 equipment is five years.
- Condition 2 equipment is three years.
- Condition 3 equipment is one year.
Manufacturer’s recommendations supersede NFPA 70B recommendations. Intervals may be adjusted based on changing conditions and inspection results. Equipment that suffers unexpected failures might require more frequent servicing. Equipment that has completed more than two inspections without issues may have inspection intervals increased beyond Chapter 9 recommendations.
Chapters 11 through 38 provide additional details on the maintenance of specific types of electrical equipment and systems, including transformers (Chapter 11), cables and conductors (Chapter 18), motor control equipment (Chapter 28) and even electric vehicle charging systems (Chapter 33).
Standard for maintenance testing specifications
ANSI/NETA MTS is a guiding document that influences project design specifications and operations and maintenance manuals as well. In this article, the items highlighted from ANSI/NETA 2023 focus on establishing regular maintenance intervals for electrical systems. This is a crucial step that sets up a system for long-term success.
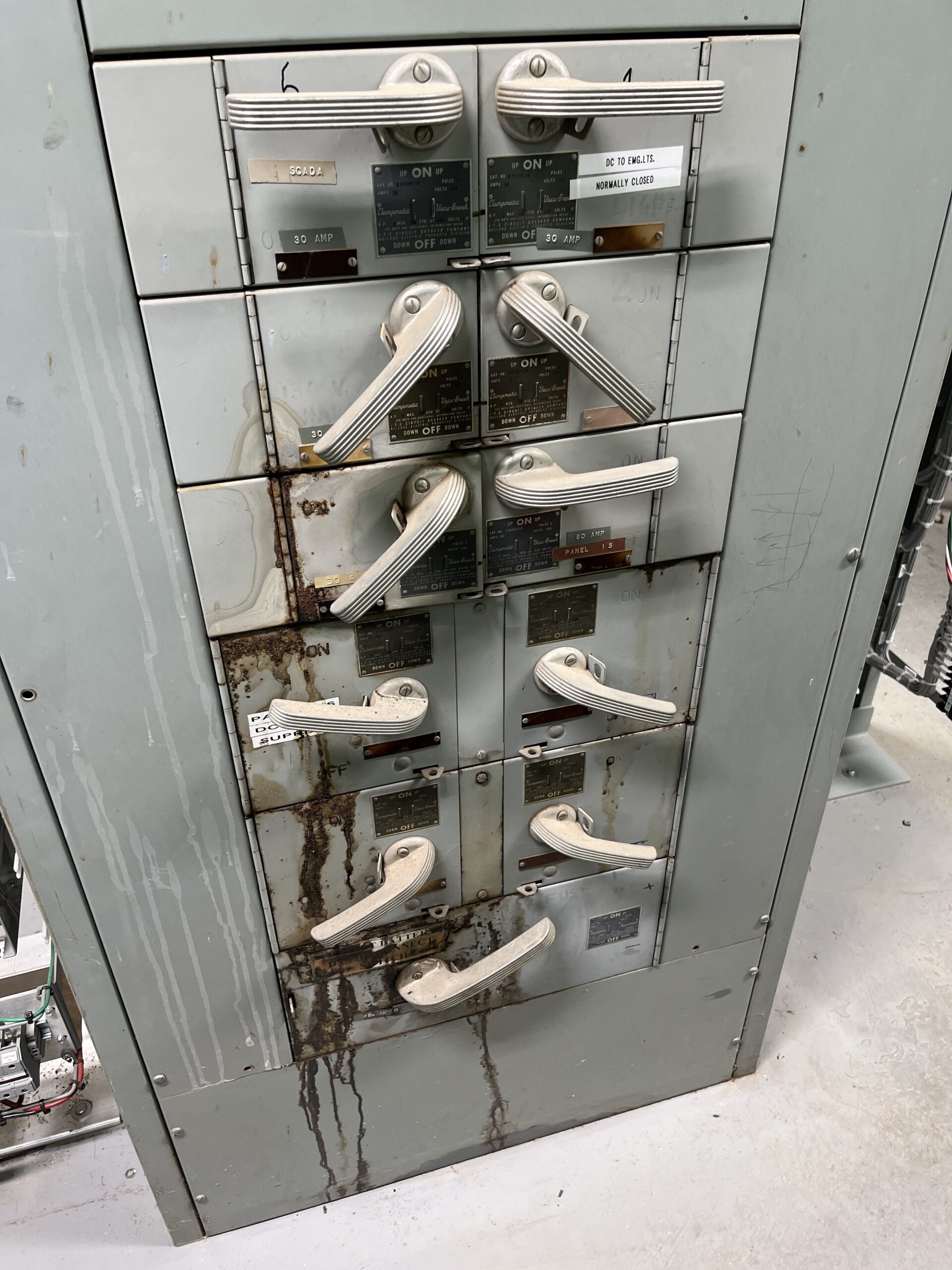
ANSI/NETA also publishes the Standard for Acceptance Testing Specifications for Electrical Power Equipment and Systems to guide testing of equipment during the installation process. While a separate publication, ANSI/NETA ATS is similar in scope and layout to ANSI/NETA MTS and while not technically related to maintenance of equipment, there is a direct correlation between the quality of an installation and the long-term life of the equipment being installed.
As will be discussed later in this article, where data trends are important to understanding the current state of equipment, the results of testing performed during commissioning in compliance with ANSI/NETA ATS form the baseline for later evaluations conducted in compliance with ANSI/NETA MTS.
NETA’s guidance on maintenance intervals is detailed in Appendix B and labeled “Frequency of Maintenance Tests.” A table and matrix are provided. The “Maintenance Frequency Matrix” offers multiplication factors that should be applied to the table depending on the current equipment condition and required reliability rating (see Figure 1).
For example, when determining the recommended visual, mechanical and electrical maintenance test frequency for a small dry-type transformer, a base number of 36 months is gleaned from the table. If the transformer in question is determined to be in good condition but has a reliability requirement of “high” (e.g., a piece of a critical system), the matrix provides a multiplication factor of 0.75. This factor times the 36 months base number means the recommended frequency of full maintenance tests is every 27 months.
NETA/ANSI details the recommended approach to perform these maintenance tests in Sections 5 and 7. All facility technicians or maintenance teams should be aware of the ANSI/NETA specification when taking control of an electrical power system.
Results of improper maintenance
Properly installed electrical systems are reliable and can remain so with minimal hands-on maintenance for years. This reliability is a testament to the quality of name-brand products purchased under certification from a testing facility.
However, a single weak point in the system can cause catastrophic damage to itself and the surrounding environment, potentially putting human life at risk. Therefore, regular inspections are crucial and awareness of common failure points is essential.
Two commonly cited points of failure are distribution transformers and loose connections. Distribution transformers serving campuses or individual customers can quickly become overloaded in areas experiencing rapid growth. If calculations are not adjusted for additional loads on existing transformers, the only way to catch a potential catastrophic overload is through visual, physical or like electrical inspection. Maintenance inspections on a transformer involve checking the remaining insulation material. If this material breaks down before being replaced, a short circuit is highly likely, which could even cause an arc flash. Arc flashes may destroy equipment, cause fires and injure personnel or bystanders.
Loose connections are a classic wear and tear issue that develops over time. This mainly applies to branch circuits that are frequently being unplugged, replugged, moved or otherwise disturbed from a permanent connection. Copper and aluminum wires wear over time, especially if they are repeatedly manipulated.
Wires can come loose or come into contact with other wires, causing open and short circuits. Loose wires may expose conductors to flammable environments, which can cause fires in some scenarios. Loose connections should be inspected on every operable piece of equipment in an electrical system during a maintenance check. Properly referencing NFPA 70B and NETA/ANSI ensures this step is never missed.