Manufacturing facilities can reach zero-waste by establishing how much waste is being produced and developing a comprehensive roadmap
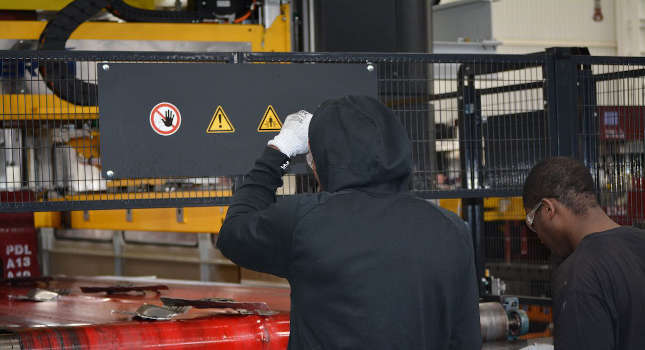
Many industries are working toward reaching a goal of zero-waste production. When it comes to the manufacturing industry, achieving this goal means retooling production processes, as well as the product’s lifecycle. If you want your manufacturing facilities to implement zero-waste practices, but fear the costs will be too high, taking the right approach to zero-waste can help save money and increase sustainability.
Identify how much waste you currently produce
If you want to set zero-waste goals that are achievable, you should first identify how much waste your manufacturing facility is producing. Once you’ve determined the amount of waste production, you can set it as the baseline for the zero-waste project.
Any facility improvements made will be compared to this baseline, which is why it’s important the initial measurements are accurate. Measure waste by amount, type and byproduct. For example, if one of your product lines results in two tons of waste being produced and another product line produces less than one ton of waste, then your most notable improvements would likely be made to the first product line.
Establish a zero-waste goal
Having a zero-waste business doesn’t mean you’ll automatically be able to reach this goal. However, it does mean you will be taking steps to reduce the amount of waste produced at your facility. In most cases, zero-waste can be achieved by ensuring more than 90% of discarded waste is diverted out of a landfill.
Different manufacturing facilities also have different guidelines for what zero-waste means. While some businesses will set a goal of less than 10% waste being sent to landfills, others will go further by setting a goal of less than 5% waste. It may even be possible to obtain complete landfill diversion over time. However, this goal can take years to reach.
There are many factors that should be considered when setting your zero-waste goals. These factors include:
-
Current production schedule
-
Local recycling infrastructure
-
Timeline
-
Budget.
Make sure any set goals don’t conflict with federal, state or local regulations. It’s also a good idea to create realistic and achievable goals
Develop a comprehensive roadmap
After a goal has been set, the next step is developing a comprehensive roadmap to help your facility reach this goal. Without a roadmap, you may not understand what it takes to be a zero-waste business.
While every roadmap can be different, most manufacturing facilities with zero-waste goals will place the largest changes at the beginning of the roadmap. Making these changes early in the process can provide the program with the positive momentum necessary to strive toward this goal.
The next focus should be on diverting additional waste streams that may be more difficult to move away from landfills. Anything that remains once these streams have been dealt with can be more effectively handled.
An effective roadmap can be something like:
-
Year 1 – Recycle around two to three of the easiest yet heaviest waste streams.
-
Year 2 – Focus on three to five extra waste streams that require additional preparation, more budget, and ample research.
-
Year 3 – Tend to any remaining waste streams. These streams are likely the most difficult of the bunch and may require making alterations to how your products are manufactured.
Make sure employees are part of this process to build trust. You can even separate employees into teams to can help your facility identify how to improve manufacturing processes. Each group should have a clear understanding of what their goals are.
Implementing a zero-waste program
At this stage of the process, all the preparation you’ve done to this point should be turned into action. Set a specific date for when your zero-waste program will go live. You might also want to meet with employees or team leads to make sure everyone understands the program and what it entails.
The initial weeks of a zero-waste program are the most critical. In the early stages, focus on making sure the program is balanced and one team isn’t being placed under more pressure. If the production process can be balanced, this will help the zero-waste program progress smoothly.
Regularly communicate goals to your employees
It’s essential employees receive communication on all goals and the program details on a regular basis. For a zero-waste program to meet its goals, every moving part must work well together. Regular communications should help your employees gain a sense of teamwork as everyone works together to achieve the same goal.
Progress should be shared on a monthly or quarterly basis. If appropriate, companies can improve employee participation by offering rewards and holding contests during these progress reports.
Tracking efforts to make consistent improvements
As is the case with any program implemented in a manufacturing facility, the only way to properly measure the program’s efficacy is through tracking. If all you had from your program was the final results, you might not understand how these results were achieved, which makes it difficult to replicate them in the future.
Key in on a facility’s key performance indicators (KPIs). These indicators should display all the changes you’ve made, which will be measured against your goals. If your landfill diversion techniques aren’t aligning with your goals and producing the intended results, you may need to make some changes to your approach. Tracking your efforts will also allow your employees to gain a better understanding of what they’ve been working toward.
Creating a zero-waste program can help move your manufacturing facility toward a more sustainable future.
– DEP is a CFE Media and Technology content partner.