Shirley Ike from Wood Americas offers advice on predictive and prescriptive maintenance
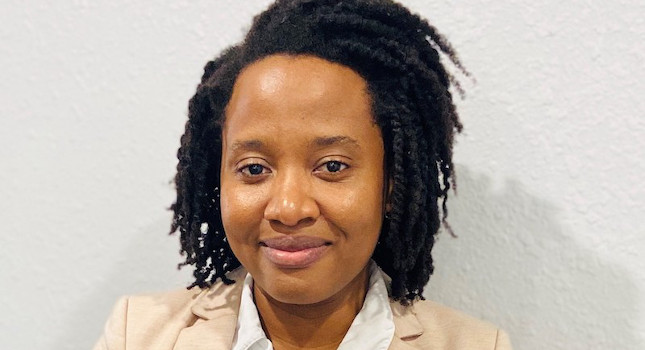
Preventive maintenance involves periodic inspection and maintenance of equipment based on a manufacturer’s recommendation. Predictive maintenance monitors the degradation of performance by analyzing collected data that describes an asset’s condition. However, going beyond preventive maintenance, Shirley Ike, flow assurance and process business manager for Wood Americas, discusses how system integrators can support predictive and prescriptive maintenance efforts.
CFE MEDIA: What is the difference between predictive and prescriptive maintenance?
Shirley Ike: Historically, people have maintained equipment on a regular schedule, such as regular oil changes and tire rotations for cars. Predictive maintenance is where sensors monitor the performance of equipment on a continuous basis to detect degradation in performance, which leads to maintenance. A variety of data analysis techniques are used in understanding the degradation. Prescriptive maintenance goes one step further in not only identifying the degradation, but also identifies the cause of the degradation as well potential remedies to course correct.
Predictive and prescriptive maintenance falls within the five general types of data analytics that can be split between “doing the right things” where cognitive maintenance falls into, which assesses what needs to be done for optimized outcomes versus “doing things the right way,” which involves descriptive, predictive, prescriptive and preventive. Predictive maintenance monitors the degradation of performance by analyzing collected data that describes the asset’s condition. Machine learning (ML) and artificial intelligence (AI) can be used to identify patterns associated with past failure events to predict potential future failures. Prescriptive maintenance identifies what needs to be done in the form of recommended actions to be taken. This is achieved by identifying the root cause of the underlying failure pattern.
CFE MEDIA: What role does preventive maintenance (PM) play in either predictive and/or prescriptive maintenance?
Ike: Preventive maintenance involves periodic inspection and maintenance of equipment based on the manufacturer’s recommendation. Preventive maintenance can become unnecessary if it is too conservative and it also can become reactive (run-to-failure) if not made at the right time. It is designed to keep parts in good condition, but it doesn’t take the state of a component or process into account. This is like taking one’s car for an oil change every 5,000 miles regardless of the condition of the oil while predictive maintenance takes the condition of the oil, measured on a periodic basis, into account while determining when the oil change should be done.
CFE MEDIA: What are the specific “pain points” of predictive and prescriptive maintenance that must be dealt with to ensure plant reliability?
Ike: Data analytics is an important way we use the data collected from our oil and gas systems’ Internet of Things (IoT) devices to find insights to help us make valuable decisions. Some of the key issues faced with predictive and prescriptive maintenance includes:
- Unstructured data (such as manufacturing records, maintenance records, production histories, logs, reports, studies, video, audio) that haven’t been analyzed and processed into more usable formats during observation or for better use later when identifying correlations.
- Sensor data quality and frequency also can be a challenge due to outdated calibration and infrequent data measurements, which makes pattern recognition increasingly challenging. This is specially observed in old/aging assets.
- The general conservative approach across the industry to new technologies when directly linked to plant performance and safety.
- Breaking the silos: Maintenance using digital transformation requires a combination of process, reliability, integrity, software, system engineering and data science to work together to come up with the optimum solution.
- Scalability of solutions is another issue only a few software systems have solved.
CFE MEDIA: How can system integrators support predictive and prescriptive maintenance?
Ike: “The largest single controllable expenditure in a plant today is maintenance, and in many plants the maintenance budget exceeds annual net profit.” This quote from DuPont is a good reminder of the value of better maintenance.
System integrators can help reduce costs associated with asset operations, inspections and maintenance. They combine domain knowledge with analytics and commercially available software and offer configuration services to asset owners and operators wanting to improve operational and data efficiency as well as to predict operational or safety issues and drive down costs associated with inspection and maintenance. They allow the asset owners to harness the full value of data for challenging decision-making. System integrators help solutions scale at enterprise level and support operations teams to adopt new solutions in such a way that real impact can be made to operation. Management of change is a key part of digital transformation.