Unplanned downtime can cause problems for manufacturers, leading to production losses and safety incidents.
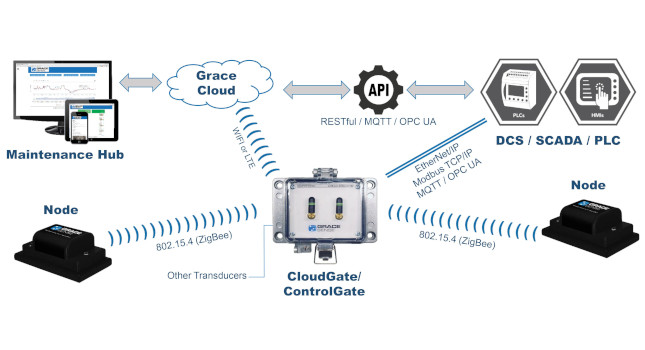
Downtime insights
- Implementing predictive maintenance system provided early warnings for temperature anomalies.
- By investing in this IIoT-driven system, manufacturers improved their operational efficiency, minimized unplanned downtimes and enhanced safety measures.
Unplanned downtime can cause problems for manufacturers, leading to production losses and safety incidents. In the nonwoven production industry, excessive heat generated during fiber processing poses a significant risk of thermal events, resulting in unplanned downtime and potential injuries to personnel. To address this challenge, a leading non-woven manufacturer invested in an industrial internet of things (iIoT)-driven equipment monitoring system to improve their maintenance insights and reduce risks during reactive maintenance scenarios.
Their challenge
Our customer, a nonwoven manufacturer, faced the challenge of the excessive heat generated by their complex machinery during the fiber processing stage. This heat could lead to thermal events, causing unplanned downtime, material loss and putting personnel at risk. They were searching for a predictive technology solution to monitor their equipment and detect potential issues before they turned into costly downtime.
Integration of a predictive maintenance system
According to the manufacturer’s maintenance manager, the integration and application of a solution was quick and simple, and the cloud-based capabilities were particularly useful. To ensure that the system could be integrated with their programmable logic controller (PLC) network, solutions can work with manufacturers to develop a solution that would allow data to be transmitted from the predictive maintenance system using both cloud and PLC networking.
To support this application, the manufacturer installed gates to communicate with their 140 vibration and temperature nodes, which are wireless sensors that monitor vibration and temperature to assess the health of rotating equipment. The IIoT application engineer team provided node and gateway installation oversight and performed a site survey to determine the best locations for the gateways. Once the hardware was installed, the application engineers worked closely with other manufacturers to provide PLC integration support.

Predictive maintenance system prevents thermal events and unplanned downtime
The nonwovens manufacturer successfully integrated the predictive maintenance system, which has provided them with advanced warnings of temperature anomalies, enabling them to prevent thermal events and unplanned downtime. The system’s alarms are configured within the manufacturing plant’s PLC infrastructure, and data pulled from the system is displayed on human machine interfaces (HMIs) when the temperature reaches a warning level. The system has already prevented six unplanned downtime scenarios that could have resulted in contaminating their production or a thermal event. Before the deployment of the system, their unplanned downtime could last for several weeks. Now, with just one hour of planned downtime, they are detecting and addressing future events.
The success of this deployment has led the parent company of the nonwoven manufacturer to consider using the system in more of their facilities. They plan to utilize the system’s vibration monitoring features on more equipment in the future, indicating their confidence in the system’s predictive capabilities.
The results
The nonwovens manufacturer was able to closely monitor their equipment and detect potential issues before they became a problem. This allowed them to prevent thermal events, minimize unplanned downtime and reduce material loss. They were able to revolutionize their nonwoven production, making it more efficient, reliable and safe.
By investing in the IIoT-driven equipment monitoring system, the nonwovens manufacturer was able to gain better insights into their equipment’s condition and take corrective action before a catastrophic event occurred. These solutions have helped them improve their operations, minimize unplanned downtime and increase safety for their personnel, which has led to the parent company’s consideration of using the system in more of their facilities.
– Grace Technologies is a CFE Media and Technology content partner.