In a summer of turmoil at GM, one Michigan plant keeps building on its second chance
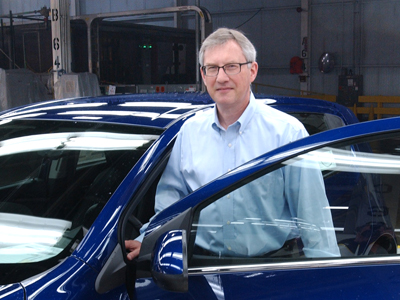
The persistent hum running through the General Motors assembly plant in Orion Township, Michigan, sounds neither like crisis nor change, even in a facility and a company that has seen plenty of both.
Before 2009-before the GM bankruptcy closed this plant, ended the production of the Chevrolet Malibu and Pontiac G6, and idled thousands of workers-this was a big place making big cars under the big rules of the way Detroit used to make cars. Today, Orion is a new plant in an old shell, making the smaller Chevrolet Sonic and Buick Verano. It’s a smaller footprint with a Lean assembly process. There are new work rules, new technology, new investment, and a new sense of what is possible when you start all over with your manufacturing plan.
But to start over, you have to stop.
Old plant, new rules
At Orion (pronounced OR-e-on), the bankruptcy wasn’t about stock prices or even the overall U.S. economy. The matter hit close to home. This was personal.
"After the plant was idled, it was a very difficult time for the entire team," said Steve Brock, plant manager of the Orion Assembly facility and the nearby Pontiac Metal Center. "The overall economy was suffering, our future was uncertain, and people were cutting back on eating out, making special purchases, which impacted local merchants. Additionally, the employees of local suppliers were directly affected because the plant no longer needed consumables, parts, or services."
For two years, Orion’s plant lay idle as GM wrestled with a way not only out of bankruptcy, but also out from the underlying competitive issues that had plagued Detroit automakers for decades. It was clear that if Orion were to reopen under a "new GM," there would need to be new rules in place. That meant a commitment from the United Auto Workers for a change in work rules and wage structures, and a commitment from GM for a stable, sustainable future for the facility. It also required a commitment of tax incentives from the state of Michigan.
The first step in that process was to make the Chevy Sonic the centerpiece of that facility. The Aveo had been manufactured in South Korea prior to the bankruptcy, and the Sonic, as its replacement in the subcompact category, seemed like another candidate for an American auto nameplate with a foreign birthplace. Instead, the Sonic came to Orion.
To make it a cost-effective move, the UAW and GM agreed to new work rules, and to the institution of the Global Manufacturing System, the company’s Lean manufacturing system. Brock said it is "designed to engage and align the team to achieve positive business results and embrace continuous improvement."
Before they could engage and align, Orion had to get the plant up and running again, with many of the same people in place, but with a whole new set of rules. "I don’t think that we lost their trust and confidence," Brock said. "I think we had to help them understand the bigger picture of our challenge of competitively building the first small car in the U.S. We had to help them understand how we were going to do that together and why change was important."
That change required a consistent joint message from the Orion management and from the UAW. "As every team member reentered the plant, we invested the time to share that message as a joint leadership, UAW and GM, and teach the principles of GMS and the importance of change or continuous improvement," Brock said. "To maintain trust and confidence, you need to walk the talk and live our values."
Those efforts continue today. "The relationship with the local is collaborative," said Orion assistant plant manager Doug Hanly. "There may be tension on how get there, but there is no disagreement on what the end game is. They want to get there. They understand why we do what we’re going to do and what their role is."
Communicating the future
Communication is one of the most crucial elements of the Orion process. "We’ve got to continue to share the story with our workers. The confrontations of the past are not there," Hanly said. "We now have meetings between the shop chairman once a week on formal basis. The more we can show a united front on floor, the more the team on the floor recognizes that."
"Communication was, and still is, a critical aspect of helping our team understand what we need to do, how we need to do it, and most importantly, why," said Brock. "Our focus has been on how we engage every member of our team to understand how their work contributes to the success of their team, the plant, the company, and most importantly, the customer.
"We are proving that engaged people executing processes do achieve positive results," Brock added.
That engagement is showing up in new ways that were less likely before Orion’s rebirth. "One avenue is the innovation and creativity of our workers," Hanly said. "They’re the best ones to come up with solutions to our problems. We’re started engaging the team. We’ve challenged them on how the product design needs to come together. We’ve challenged them to think about how we do our business, and how we do it more effectively. You’ve got to be a Lean thinker."
At the top, a year of turmoil
The process of manufacturing a car-the movement of parts from suppliers to line workers, the whirr of pneumatic wrenches and the purr of lift trucks, the marriage of chassis and powertrain-is not fundamentally different from the vision Henry Ford created a century ago. The ballet that takes a car from unassembled parts to a finished machine is still a sight to behold.
The challenge today is to make that same car more efficiently and with fewer defects. It is here where GM-though not specifically Orion-faces its greatest challenge.
The revelation came in February 2014 that 13 deaths are blamed on a manufacturing defect in the ignition switches in Chevrolet, Pontiac, and Saturn models manufactured from 2003 through 2010. The resulting firestorm has resulted in a change in management at GM, with longtime company engineer Mary Barra taking the CEO role.
The company hired former federal prosecutor Anton Valukas to conduct an investigation into GM’s handling of concerns over the ignition switch defect reports, and the general culture around safety and accountability at GM.
In prepared remarks before Congress on June 18, Barra was unsparing in her criticism of the problems GM now faces. "Two weeks ago, I purposefully addressed the entire global workforce about the report. I told our team as bluntly as I knew how, that the series of questionable actions and inactions uncovered in the investigation were inexcusable," Barra said. "I also told them that while I want to solve the problems as quickly as possible, I never want anyone associated with GM to forget what happened. I want this terrible experience permanently etched into our collective memories. This isn’t just another business challenge. This is a tragic problem that should never have happened. And it must never happen again."
But Congress has been just as unsparing in its criticism. Barra twice has been called before Congressional committees both to testify and to answer pointed questions about the failure of the GM culture before and after bankruptcy to address and correct such defects. Perhaps just as bad, the problem has turned GM into a punchline for late-night comedians.
It has been made worse by the continuing litany of recalls GM has issued since the February ignition switch scandal first broke. As of July 1, there were more than 40 individual recalls of GM products manufactured in the last decade. Some were minor fixes in small quantities that normally wouldn’t have caused much of an uproar. Many have occurred as GM itself has uncovered other problems in its internal investigation and is being proactive-something that wasn’t done as a result of past GM defects, according to the Valukas report.
Taken in aggregate, those recalls have painted a dim picture of GM. Yet even as Barra announces sweeping changes within the company in between congressional testimony and the recalls notices drone on, the business of making cars and the business of the business continues as usual.
The world’s second largest manufacturer of automobiles makes 10 million cars a year. Sales remain strong, and the stock price has been relatively unaffected. In October 2007, GM stock closed at $42.64 a share. By June of 2009, the company was in bankruptcy and shares were frozen at 75 cents a share. The company emerged from bankruptcy in November of 2009 and the stock price rose to more than $34 a share. It nearly touched the $41 mark before Christmas of 2013, just before the ignition switch crisis began, In July 2014, the stock hovered around $36 a share.
Reinvestment in Orion
Only about 40 miles separate GM’s corporate headquarters (ironically located at Renaissance Drive) from the Orion Township plant. The distance from the current GM troubles seems farther away. Of the 44 GM recall notices in the United States since the beginning of 2014, just two have involved cars manufactured at Orion. On June 5, 31,000 vehicles, including not just the Sonic and Verano but also the Chevrolet Camaro and Chevrolet Cruze, were recalled for repair of a driver’s side air bag bar. On June 11, 21,000 Sonics from 2012 were recalled to repair a possible fracture of the transmission turbine shaft. That’s less than 50,000 cars compared with the almost 18 million GM models recalled this year.
The success the team at Orion has enjoyed has earned it a reinvestment from the company in new technology and new processes to further streamline costs and improve productivity. A new automated guided vehicle (AGV) system allows production materials to be kitted and delivered to line workers without the use of lift trucks. The AGV processes also delivers the chassis and drivetrain on time and in sequence, and raises the chassis to the proper height for the worker, improving ergonomics and safety.
A new paint shop was installed inside the walls of the Orion plant. "The new paint shop turned a three-coat process into one step and reduced the footprint of the paint shop by 250,000 sq ft." Hanly said. "It’s now being used as a model for other facilities."
The changes are not limited to the assembly line. At the rear of the facility, you get a full view of the landscape around Orion. You can see the coal bins and coal field that used to provide power for the plant. The old days of coal, like the old days of the old work rules, are gone. "We’re completely done with coal," Hanly said.
The plant sits between two landfills, and later this year the landfill gas will begin fueling eight new generators that are expected to generate about half of the power necessary to run the plant. A solar array delivers another 350 kW of power for the plant, part of an overall effort at GM to expand the use of solar power at plant sites.
All of this reinvestment in Orion, just five years removed from bankruptcy, has turned the facility into a proving ground for new GM initiatives. Brock thinks it’s a proving ground for his team as well. He said his team has earned the investments "by providing the results or payback on the investment with the right methods and behaviors. An engaged team of people that embraces innovation and finds ways to do things differently or better results in continuous improvements that help execute our processes, ultimately resulting in positive business results."
Fueling the future
It has been a year of unbelievable turmoil within General Motors, and the impact of that turmoil is not lost on the team at Orion. But they also remain focused on making the Sonic and Verano, and to continue to earn the benefits of this new opportunity. The plant leadership at Orion sees it as a very personal process.
"I think about the bankruptcy, and then to come back to where we are today," Hanly said. "Relationships matter; it’s how we got here today."
"I am proud of the team and their commitment to the customer and working hard every day to be better than the day before," Brock said. "Our mission statement is, ‘Build it like we own it,’ and we all take that to heart as we perform our work every day."
By reducing the manufacturing footprint by 36%, the Orion team has opened up the room for manufacturing expansion. That was an impossible dream in 2009; the workforce and the community would have settled for just getting the plant reopened. Now there is room for growth and room for optimism.
"A lot of factors go into defining the future for a manufacturing operation. For the near term, we can help the future of Orion by staying focused on the things that we have the ability to directly control and influence," said Brock. "In the longer term, we will continue to create a culture that is supportive of being a very Lean, efficient, and flexible factory with a team that is creative, innovative, and embraces change in all we do."