The food and beverage design-build process demands attention to detail and a high level of expertise to navigate a maze of regulations. Five tips to making the process easier are highlighted.
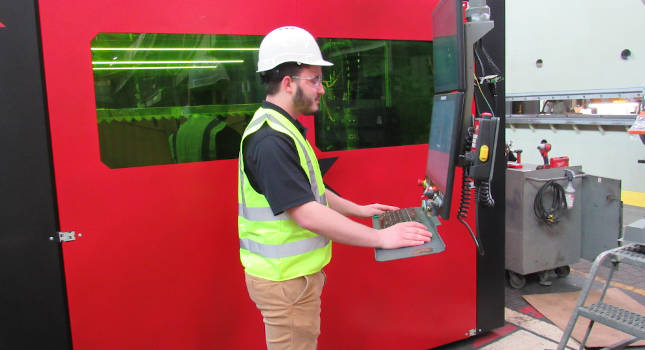
The food and beverage design-build process demands attention to detail and a high level of expertise to navigate a maze of regulations, adhere to strict food safety guidelines, stay within budget and guarantee the facility is well-equipped to meet long-term production goals.
Effectively coordinating different disciplines, vendors and subcontractors to ensure timely and on-budget execution is an ongoing challenge in construction projects that requires careful planning and communication.
The owner is in the driver’s seat and plays a pivotal role in the overall success of the project. There are several things owners can do to design and construction teams and help streamline the process.
1. Nail down a product vision
The earlier companies can make decisions about the products they’ll be producing, the better. The final product heavily influences the design of the processing areas and equipment. Even minor adjustments mid-project can threaten to derail a schedule.
For example, if building a dairy plant, the initial aim may be to produce gallons of milk. However, if companies later decide to expand the product line and also produce chocolate milk, this seemingly small addition can have a significant impact on the overall project schedule. In this case, the design-build team may need to modify the equipment and layout, taking into consideration new factors like changeovers and additional sanitation requirements to account for the sugar content in chocolate.
By deciding on the product line and recipes before or during the early stages of the project, companies can help minimize potential schedule disruptions and prevent the need for expensive redesigns or rework later on.
2. Select the right equipment
The global supply chain remains unpredictable, and equipment delivery and installation lead times continue to be volatile. Making decisions on sophisticated machinery and locking them in early can help control lead times and improve the project manager’s ability to coordinate material and equipment deliveries with worker availability.
While an experienced design-build partner, like Stellar, can serve as a consultant through the equipment procurement process, this decision is typically owner-driven. Delaying these decisions can impact a project schedule in the long term.
Off-the-shelf purchases aren’t an option when it comes to food processing equipment due to their high level of specialization. Typically, the procurement process involves working with an original equipment manufacturer (OEM) to ensure that the equipment meets the individual facility’s requirements. The sooner this process can begin, the more flexible the schedule is to adjust designs and prevent delays. Remember the chocolate milk example? That facility might need to pause the construction schedule to add a clean-in-place system to sanitize process lines between SKUs.
3. Find the ideal location
One of the most important decisions an owner will make is their site location. The final site can have a ripple effect on the overall construction project, which is why owners should have a comprehensive understanding of the site conditions before purchasing land or leasing a building.
When selecting a site, some factors companies should always consider include:
- The size of the site — The available land area will directly affect the design of the facility, particularly when retrofitting an existing structure to meet business needs. Knowing the size of the site from an early phase enables the design team to determine the optimal layout for your facility and equipment and ensure efficient operation. They can also identify opportunities for future expansion, such as adding more process lines.
- Zoning requirements — Food processing facilities must adhere to various regulations and requirements, which differ from one municipality and state to another. These requirements can heavily influence the design and construction of the facility, from the type of equipment and materials used to the layout of the building and the processes implemented. Not understanding the regulatory environment can result in unforeseen expenses and delays.
- Proximity to utilities — Knowing what utilities are available at the site can help companies plan for any necessary upgrades or modifications to ensure that the facility operates at maximum efficiency. However, suppose the utility connections do not reach the location. This can lead to significant expenses and schedule delays as the construction team adds the necessary infrastructure to connect water and electricity.
- Proximity to transportation routes — The facility needs to be easily accessible to suppliers and employees and be able to transport finished goods. Choosing a site far from major transportation routes can lead to increased transportation costs and delayed deliveries. The location will also be less appealing to prospective employees. During the construction process, accessibility is also crucial because a site that is difficult to reach may cause delays in receiving and staging necessary supplies, leading to short-term consequences that can impact the schedule and increase overall costs.
4. Identify key stakeholders
To keep a food processing project on track, start with a small group of key decision-makers who understand the project scope and goals. Then, gradually loop in additional stakeholders. This approach ensures everyone is aligned on a shared vision, reducing the likelihood of delays. It also helps manage expectations and promote effective communication throughout the project.
5. Collaborate with the right team for a smooth project journey
An owner’s active involvement, particularly in the early stages, can significantly impact a food processing project’s outcome. However, companies don’t have to carry the weight of responsibilities alone. An experienced design-build partner can provide valuable guidance and support at every step of the project lifecycle, from concept design to construction and startup.
– Stellar is a CFE Media and Technology content partner.