Shop floor maintenance software gives manufacturers information on how things operate and the right program will improve efficiency.
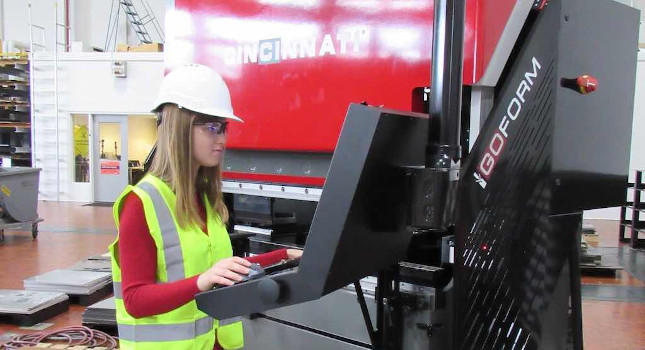
Despite all the obstacles 2020 has thrown, many manufacturing teams have risen to the challenge. Many had to do more, often with less, which made achievements all the more unique and noteworthy. As companies pivot to something resembling normalcy, there are many ways they can achieve even greater success going forward. Finding the right tools and communication methods has always been tricky, but there are more tools than ever to help companies achieve success. Shop floor management software, for example, has become a key asset for companies that have had to work in silos or apart on the plant floor rather than together. For some, it may even be essential.
The realities of 2020 have brought this truth home to roost: you can’t be everywhere at the same time. You can’t work remotely and be physically present on the shop floor at the same time. You have to be able to immediately assess performance, at a glance, and so must your team. The show must go on: It has never been more apparent that you must be able to gauge how your teams are doing even when you can’t see them in person.
Five essentials of shop floor software
Shop floor software that tells you where potential hold ups may occur. Does your team have the materials and tools to perform their jobs? Will finished goods be ready to ship on time? Do you have the right people where they need to be, fully trained so everything keeps running? Do you have the right number of people, today, tomorrow, next week, and next month? This is where the rubber meets the road, so make sure the shop floor software addresses these five essentials:
- Does your team have the necessary raw materials, sub-assemblies, and tools to perform their jobs?
- Track spare parts consumption, costs, and trends
- Satisfy calibration dates and requirements for calibration performed both inside and outside your facility
- Connect all people and processes digitally (without paper)
- Capture and record material shortages and trends
- (If we’ve learned anything from 2020, it’s how vital our supply chains are)
- Will your finished goods be ready to ship on time?
- Satisfy customer delivery requirements
- Notification and escalation of all concerns and victories.
- Avoid expedited freight charges
- Are you turning goods at your targeted rate?
- Do you have the right people in the right places?
- Are they fully trained in the skills for that area, line, machine to keep everything running
- Do you have enough skilled people to train others
- Can you provide evidence of satisfactorily completing training?
- Complete history of documentation, including dates
- Work forces are in flux like never before
- Do you have enough people?
- Today, tomorrow, next week, next month, over the next six months
- Can work and checks be monitored and performed remotely?
- Does your team have immediate access to checklists and necessary documents?
- Can people be moved when shortages arise?
- Do you have enough people?
- Can you plan and monitor production events in real time?
- Know at a glance if you’re on schedule, ahead, or behind
- Are you trending in the right direction
- Are you hitting your targets
- Are you building good product
- Actual throughput number of good parts
- Reject, defect, scrap, rework quantities
- Easily monitor and display all production metrics
- OA, OEE, PPM, Downtime
- Ensure correct product and product orders are being run
- Schedule and deliver reports directly to your inbox on a regular basis. Include all the people who need to be kept apprised: your shop floor leaders, your boss, accounting, your internal customers and internal suppliers.
- Know at a glance if you’re on schedule, ahead, or behind
How shop floor management software enables success in 2021
How does having the right shop floor management software change everything, when it seems like everything has already changed? There was a time when a clipboard and some mimeographed pages were enough for you to keep it all together.
Instead, companies can embrace the technology that allows for much easier input of information. Shop production software should make it a snap for everyone to input data related to the work they’re performing, not just you. How many times during 2020 did you wish you could ditch that clipboard? It’s hard to hold up your clipboard and share a spreadsheet with folks who are in a different building, or a different city entirely.
What we’re all after is to make operations management easier, even with the need to work remotely. And not just easier. Safer, too. People in separate locations, different departments, and across various shifts have been able to share and analyze data. Without having to meet face to face, as much of this has been accomplished remotely. Talk about successfully social distancing.
No one can predict how manufacturing practices will continue to change and evolve going forward. 2020 drove home the need for effective and timely communication. Make sure your shop floor software is flexible and adapts to the company’s needs instead of acting like a workaround. A software solution should lead that charge and not expect the users to ferret out additional software.
This article originally appeared on Leading2Lean’s website. Leading2Lean is a CFE Media content partner.