Modernized FDT technology drives collaboration between control system and device suppliers to provide cloud-based monitoring for improved asset reliability.
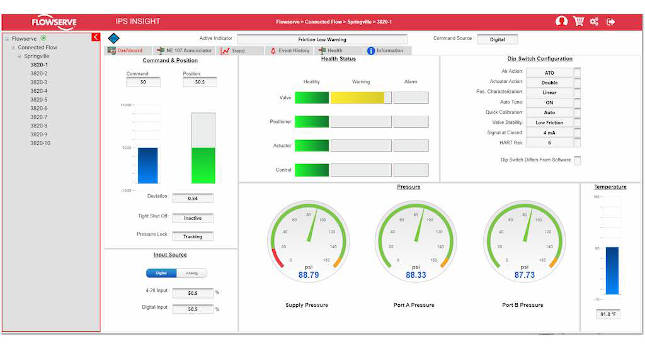
For today’s industrial organizations, effective plant and factory maintenance programs are critical to ensure the reliability and availability of vital equipment while keeping costs and operational disruptions to a minimum.
FDT Group has long focused on driving universal network and device integration, innovating the way automation architectures connect and communicate as part of asset management strategies. The organization’s latest technology developments transition its integration standard to an information exchange platform.
This enables cloud-based asset monitoring for process-centric devices and provides a flexible solution for implementing Industrial Internet of Things (IIoT)-based predictive maintenance, which can reduce support costs, improve asset reliability and provide useful information to maintenance personnel working in the field.
Balancing act
Owners/operators of industrial facilities struggle to maintain a balance between keeping costs down and asset availability up. Effective asset management plays a key role in ensuring this balance is maintained — enabling companies to comply with regulations, avoid the costs associated with unnecessary maintenance, and avoid unplanned downtime.
The IIoT, along with the Industry 4.0 initiative, is one of the most significant trends in industrial automation, enabling manufacturers to expand their capabilities for condition monitoring and asset integrity management. Predictive maintenance strongly relies on IIoT, which digitalizes the physical indicators allowing human-to-human, human-to-machine and machine-to-machine connections for intelligent data analysis.
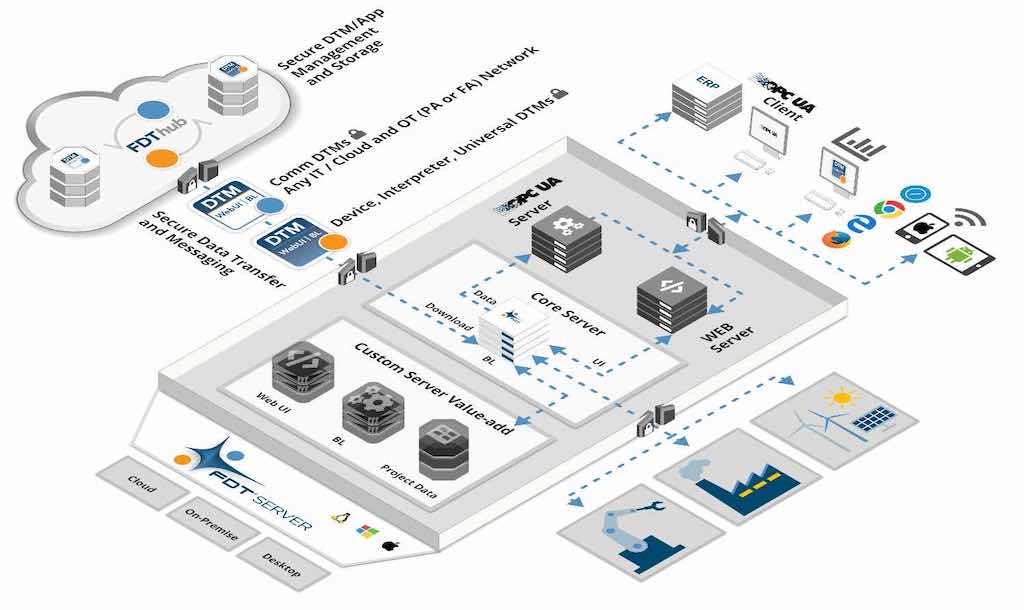
Rather than performing routine, calendar-based inspections and component replacement, smart sensors can be used to monitor equipment for pending failures and provide notifications when service activities are required. Predictive maintenance-based tools check for abnormal conditions and trigger work orders when safe operating limits are breached.
A Deloitte study found that IIoT-based predictive maintenance solutions are expected to reduce factory equipment maintenance costs by 40%. Predictive maintenance can also reduce safety, health, environment and quality risks by 14% and extend the life of an aging asset by 20%, according to PwC.
When a predictive maintenance strategy is working effectively, maintenance is only performed on machines when it is required, thus reducing the parts and labor costs associated with replacements. It allows maintenance and operations personnel to focus on core responsibilities, minimize unplanned downtime and increase maintenance efficiencies.
Importance of mobility solutions
For a predictive maintenance program to be successful, it must enable the mobility of plant and factory workers who are responsible for maintaining industrial equipment health and preventing asset failures by planning and performing appropriate maintenance routines.
Maintenance organizations dealing with aging workforces and similarly aging equipment need to find and take every opportunity to optimize performance while attracting and retaining top talent.
Accessible from a mobile device such as a smart phone or tablet, the IIoT-based mobility solutions provide immediate awareness of performance and health issues. They allow for bidirectional data exchange, including information display, data entry, automated data collection and access to documentation while the technician is located at the asset.
While mobility software continues to become more functional and easier to use, mobile applications have also grown in capability and now provide value-added utilities that assist personnel during their workflow. The mobile device enables a worker to enter information and process the work order while he or she performs the needed work. This assures automated error checking and improves data integrity and compliance.
With mobility solutions, maintenance technicians become more empowered with access to asset history, spare parts inventory, repair instructions and more. Mobility extends asset management processes and predictive maintenance strategies to the point of action, creating enormous opportunities to optimize plant and factory performance.

Role of the FDT standard
First introduced in 1998 by FDT Group, an independent, international, not-for-profit industry association comprised of leading process and factory automation companies, FDT is the open standard for industrial automation integration of networks and devices, harnessing IIoT and Industry 4.0 for enterprise-wide connectivity.
The recently released FDT 3.0 standard will accelerate the evolutionary journey into the Fourth Industrial Revolution by enabling an ecosystem of FDT-based solutions to meet demands for IIoT and Industry 4.0 applications. The technology’s IIoT ecosystem empowers scalable, skid-to-cloud solutions and innovative business models unlocking universal device integration with mobility and remote access optimizing automated processes and connectivity in the process, hybrid, and discrete manufacturing sectors (see Figure 1).
FDT 3.0 empowers the intelligent industrial enterprise with native integration of the OPC Unified Architecture (OPC UA), as well as control and web services interfaces for mobile applications. The technology also employs robust security to safeguard critical automation information and operating data. FDT 3.0 provides enhanced protection measured via multilayered security and leverages vetted industry standards such as transport layer security (TLS), web sockets secure (WSS) and hypertext transfer protocol secure (HTTPS).
A key component of the FDT 3.0 standard is the FDT Server built around a core server, which provides a center point for a wide range of client and server interactions. It includes an OPC UA server providing access to device type manager (DTM) data with authenticated OPC UA clients and a web server enabling the use of web user interfaces on remotely connected, browser-based clients and other mobile devices such as smart phones, tablets and PCs. The solution also supports the use of apps that improve workforce productivity and plant availability.
The web user interface (UI) with FDT 3.0 allows DTMs to be opened in any browser, including mobile devices carried by field personnel. Manufacturers can use the technology’s standardized mobility platform as part of their service functionality that helps site engineers solve problems with remote assistance.
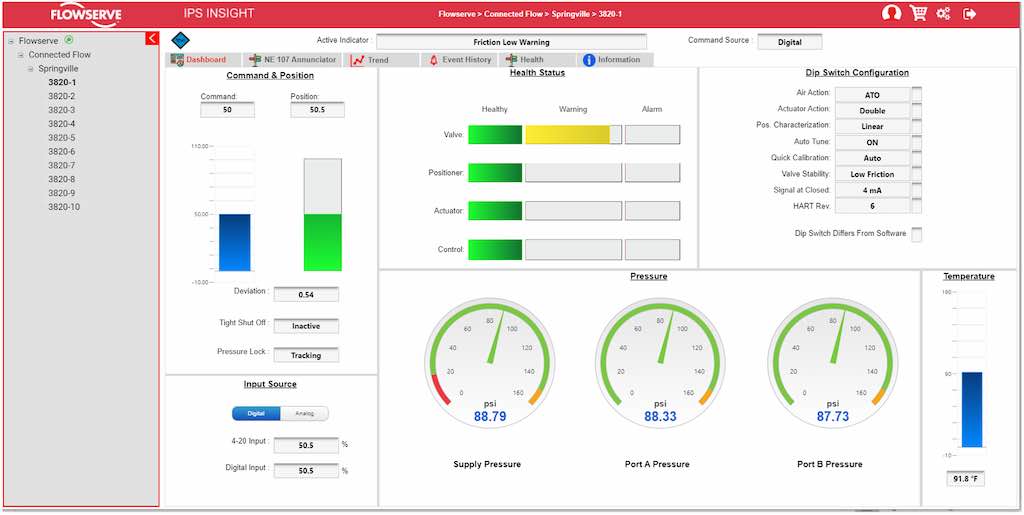
At the same time, FDT web services provides a standardized mobile access approach using browsers, apps, standalone applications or anything else capable of interfacing via web sockets.
With the latest developments, FDT technology is mobilizing the monitoring of industrial facilities and processes, as well as specific networks and devices, as part of modern asset management strategies. Lifecycle monitoring and predictive maintenance can now be done with FDT’s new standardized mobile interface or via web browsers in a way that’s fully integrated with distributed control systems (DCSs), programmable logic controllers (PLCs) and other control assets.
FDT can communicate with all the industrial device networks in use today, regardless of their architecture and provides a level of abstraction, so all information is presented in a consistent and standardized manner.
Regardless of the network protocol or device vendor, users will receive the same information for use in predictive maintenance activities. This, in turn, provides the freedom to use the networks and devices that are best suited to a particular operating environment.
With the FDT 3.0 solution, predictive maintenance becomes much more empowered thanks to a customized asset view, better diagnostics and easier access to network and device information — helping reduce downtime and improve meantime to repair (MTTR).
Users can take advantage of secure and seamless data exchange and interrogation from sensor to cloud and achieve new levels of information technology/operational technology (IT/OT) integration. For device vendors, FDT 3.0-compliant DTMs provide fit-for-purpose solutions for tasks such as deep inspection diagnostics driven by artificial intelligence (AI).
All DTMs based on the FDT 3.0 specifications comply with the NAMUR NE-107 recommendation, which stipulates operators need a view of the process, including the status of the instrumentation, in a simple and uniform way — regardless of the source device — to support predictive maintenance strategies. The DTMs are an important enabler for apps intended to view the health of field devices, and subsequently, improve maintenance workflows.
In the past, end users had to examine the DTM to identify equipment requiring service attention or repair. FDT 3.0 technology enables this function to be initiated from a mass data perspective where the user no longer needs to open the DTM but rather is automatically alerted upon the change of device health status.
Apps can be written to notify appropriate personnel when an issue arises in their area of the plant, allowing them to execute maintenance activities based on meaningful data. FDT 3.0 makes it much easier to leverage asset information through OPC UA and mobile apps to meet critical plant and factory maintenance requirements.
The same asset data is seamlessly available through OPC UA for integration with high-level systems, including maintenance management solutions such as SAP, to establish automated predictive maintenance workflows. For example, the data can assist with issuing work orders based on accurate equipment health status readings, enabling maintenance departments to avoid potential failures and allowing service work to be performed at the optimum time.
With a wealth of asset data sets now readily exposed, automation stakeholders can create applications employing artificial intelligence and machine learning to examine the full scope of machine functionality. They can also use advanced prognostics to identify and correct network and device performance issues. Without the standardization provided by FDT, and its rich source of data across the enterprise, these predictive solutions become more complex and difficult to implement.
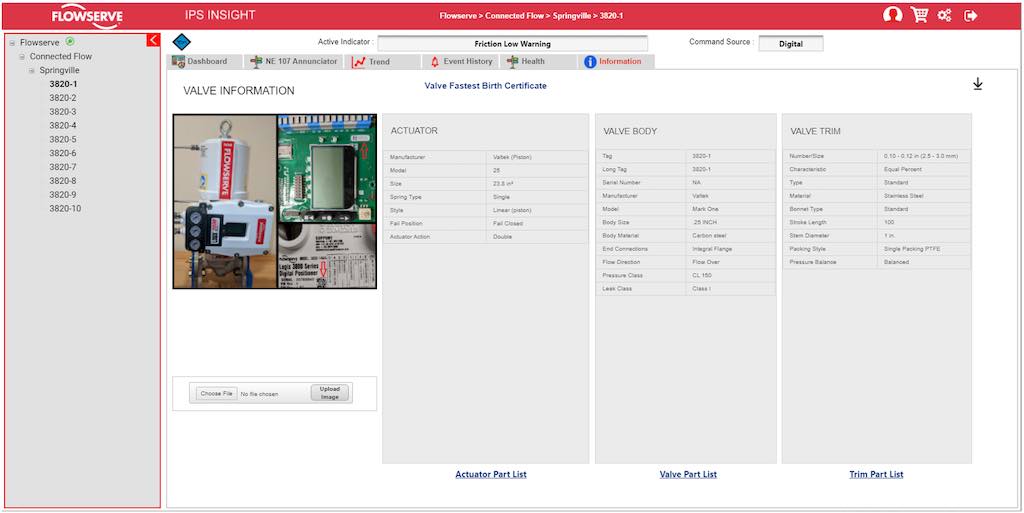
Perspective of major suppliers
Suppliers of industrial control systems and devices want to seize emerging opportunities for IIoT and Industry 4.0 solutions. By adopting the FDT 3.0 standard, they can enhance their product offerings with standards-based, platform-independent, information-driven business models for the new era of automation and industrial asset management.
According to Suriya Selvaraj, senior manager for Yokogawa, a major global provider of process automation solutions, FDT 3.0 provides the freedom for control system suppliers and device vendors to work together to provide a truly integration solution. “There are many tools now available for use in asset management and predictive maintenance, but in most cases, they are not sufficiently integrated across the supplier community,” Selvaraj said. “I believe FDT 3.0 brings a balance, whereby control system suppliers and device vendors can provide a tightly integrated solution to their customers by using OPC UA interfaces and other open platforms.
“With FDT 3.0’s robust information model, the industrial automation industry can provide an integrated solution supporting IT/OT convergence. The information model enables device vendors to move beyond specific rules and provides freedom from certain defined interfaces, mathematical formulas and device parameters. With other technologies, the vendor must wait for a specification update before making a change to their device. FDT, on the other hand, simply defines the mechanism of interoperability rather than every individual step needed to implement a function. It offers the best of both worlds by allowing device vendors to expose parameters in electronic device descriptions (EDDs), and at the same time, read or write any other required parameters. They can expose the parameters of their choosing through FDT’s versatile DTM interface.”
Selvaraj said, “FDT technology provides the impetus for control system and device suppliers to collaborate on an equal footing to solve the end customer’s problems. This approach protects the know-how of individual vendors while providing the best value from a business point of view.”
Ed Silva, global digital technology manager for Flowserve, a leading supplier of industrial and environmental machinery, considers FDT 3.0 a game-changer for the industrial automation sector (see Figures 2 and 3). He said, “The focus of industrial organizations is evolving. They have an urgent need to increase uptime and ensure stable operations. The only way to do this is to determine how devices are performing and predict faults before they cause unplanned downtime. However, with the retirement of experienced personnel, plant operating companies must find ways to use technology to bring a new generation of workers up to speed on operations and maintenance strategies.”
“In the current business environment, production facilities are seeking to monitor their assets remotely, predict equipment failures before they happen and take preventive measures to avoid disruptions. Companies want to realize the full benefits of IIoT and predictive analytics without major infrastructure changes [see Figure 4].”
“The latest industry trends center around advanced data analytics, digital twins and cloud computing. The FDT 3.0 standard supports these solutions by delivering network and device information to enable improved diagnostics and predictive analytics. The technology provides a tool to not only monitor and predict asset health, but also remotely configure and manage assets for the highest level of reliability.”
Silva said, “From my perspective, there are two sides to the FDT IIoT solution: The predictive and diagnostic side, which uses data from field devices through the OPC UA server in a vendor-agnostic way; and the configuration and calibration side, which employs the DTM/web server/browser to allow diagnostic signatures and configurations to be performed remotely on valves and other equipment without the need for a technician to be onsite. With the FDT server, asset data is now available in the cloud for trending and predictive analytics to avoid failures.”
Silva indicated that Flowserve is about to launch an IIoT service suite to help production facilities monitor their assets remotely, predict equipment failures before they happen and take preventive measures to avoid business disruptions. The new platform supports any flow control equipment regardless of manufacturer, opening the door for companies to quickly realize the full benefits of IIoT and predictive analytics without major infrastructure changes.
Benefits of the FDT 3.0 technology
As an open, platform-independent standard, FDT 3.0 will benefit companies that operate industrial facilities with a diverse array (or brands) of automation systems and devices. It supports real-time monitoring and predictive maintenance applications requiring uniform access to field devices across platforms.
The technology also supports enterprise control so that a single cloud instance can address multiple facilities to reduce costs, minimize overhead and centralize administrative tasks.
With the latest FDT technology developments, field device data and information can be automatically provided for transport into cloud-based applications. This paves the way for condition monitoring functions to be realized as cloud-based applications — independent of the automation system. The collected data can also be transferred using an export function for further processing in enterprise asset management or cloud-based condition monitoring systems.
The FDT 3.0 solution will enable plants and factories to realize important benefits such as:
- Low total cost of ownership via truly open technology.
- Robust device configuration, commissioning and diagnostic support.
- Simplified engineering and increased productivity.
- Reduced downtime (no more wasted maintenance).
- Predictive device maintenance approach to help identify problems before they become severe.
Going forward, adoption of the versatile FDT 3.0 platform will create opportunities for asset management as a service, with service providers completely managing the cloud environment and implementing a variable cost model based on the number of users and assets to be covered. This capability will be supported by consolidated asset monitoring dashboards across sites with analysis provided from a centralized location.
Looking ahead
FDT Group’s technology, as advanced by its FDT 3.0 standard, holds the key to monitoring critical plant and factory operations to reduce costs associated with facility maintenance and installed smart devices. The technology makes network and device data available when and where it’s needed, delivering important performance information to support predictive maintenance and operational excellence strategies.
Glenn Schulz is Managing Director of FDT Group, a CFE Media content partner.