Production management and predictive maintenance in one
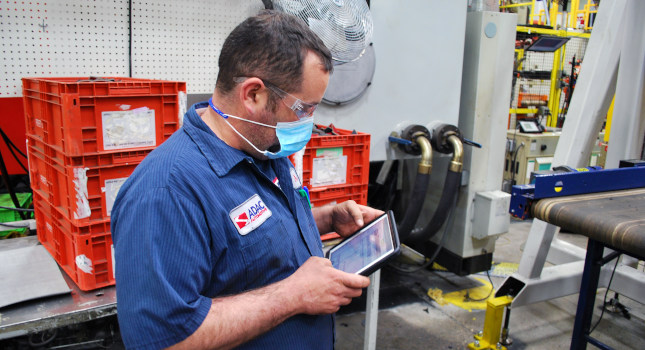
The reality manufacturers face is that equipment fails. And in just-in-time industries like automotive, lean supply chains have little time to fix product flow interruptions. Shop floor issues can wind up impacting customers. ADAC Automotive (ADAC) designs and manufactures vehicle access systems such as door handles and lift gate handles. As a supplier to several major vehicle manufacturers, equipment reliability was a source of great concern to ADAC management.
“Machine downtime has a large impact on direct and indirect labor variance and lost production throughput, so it was essential ADAC make a shift to a Smart Factory concept to maximize machine availability,” said Brent Warren, director of assembly operations.
Historically, ADAC’s process recording mechanisms were painstakingly manual. They relied on paper-based systems that wasted time and gave limited real-time visibility into its plant-floor operations. It had a clearer picture of how the plant had been operating versus how the plant was operating at the moment. And when something broke, there was no connected way to notify, triage and address the issue.
Exterior door handles and interior door handles include elements that are molded, painted and assembled. Products also include embedded electronics.
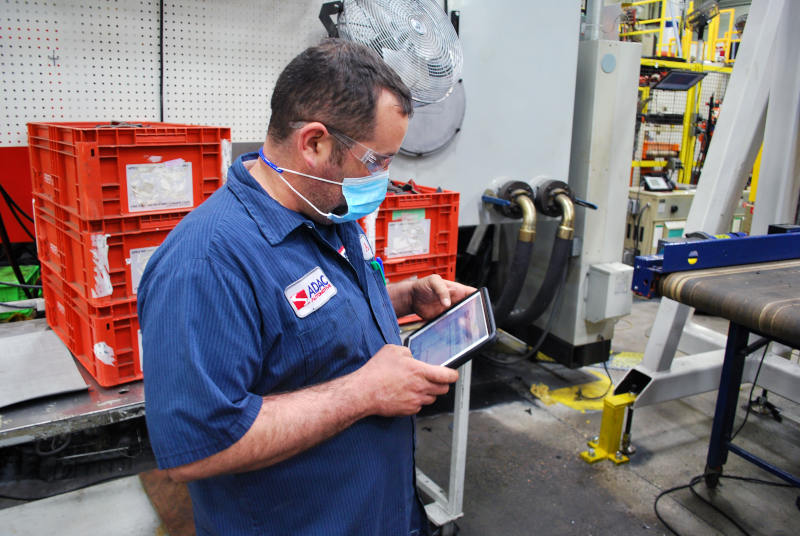
“A couple years ago we took a look at our whole organization and discovered some things that we really needed to improve. This led us to engage with L2L to provide us the operational flexibility that we needed,” said Rick Vande Kopple, vice president of global quality.
As a result, ADAC Automotive implemented L2L’s Reliability and Production system in four Michigan-based manufacturing facilities, where frontline personnel across the production and maintenance functions leverage it daily.
ADAC results speak
By integrating 287 assembly assets and 58 molding machines to automatically report descriptive machine downtime events, ADAC now has a standard real-time process across all shifts, departments and facilities for monitoring and responding to these issues quickly, on more than 200 production lines.
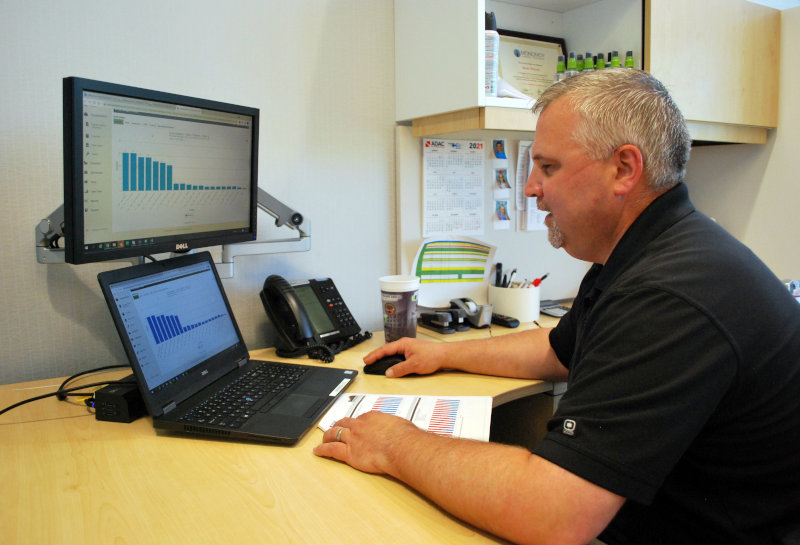
ADAC captures and details hundreds of operational activities every day: from lab samples and first part checks to preventative and reactive equipment maintenance, calibrations, and other key processes.
“With preventive maintenance (PM) systems I’ve used in the past, it’s paper based. You fill it out, turn it in, it gets filed. No one ever sees that piece of paper again. Having a digital system saves a ton of time on the analysis of problems,” said Colton Burmeister, maintenance manager. The technical team is equipped with tablets that have L2L on them. They can walk to their area and do what’s needed on the tablet through L2L. They can get notifications through their email or on an app on their phone.
“A lot of the guys like it better because it’s really user friendly. It’s real time. They have the ability to pull up previous PMs and CMs (corrective maintenance), so it puts a lot more knowledge in their hands. And in turn it gives them more power to do their job,” said Burmeister.
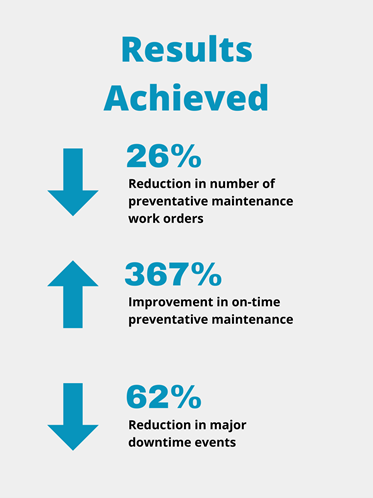
Over a period of six months, for example, ADAC’s Keating assembly operations was able to increase OEE by 15 percentage points. PMs required per week dropped by 26%.
A common data set
Now we have one common data set that all of us can get into, all of us can see and understand,” said Brent Warren, assembly operations director.
L2L provided ADAC with a way to reduce downtime and to easily notify, escalate and resolve issues. It has transformed their approach to maintenance by enabling the transition to cycle-based preventative maintenance. This ensures that equipment is regularly assessed and maintained based on usage or throughput instead of by time period, during which machine utilization can vary greatly.
“A lot of programs and software out there drive you down one path and solve one issue. We started with a target of four or five business processes, and today we do over 50. Those opportunities have gone well beyond what we ever thought we could do,” said Vande Kopple.
For assembly operations director, Brent Warren, what’s distinctive is the engagement of the workforce at the technician level, the team leader level and even the operator level. Everyone understands what’s needed to be successful.
“Continuous improvement is the name of the game. Automotive is so tight, so competitive that we just must be the best. L2L ensures that our activities on the plant floor are conducive toward that end,” concluded Jorge Martell, VP of Manufacturing Operations for ADAC Automotive.
For more information, go to www.L2L.com