Maintenance is valued, but aging equipment puts pressure on plants.
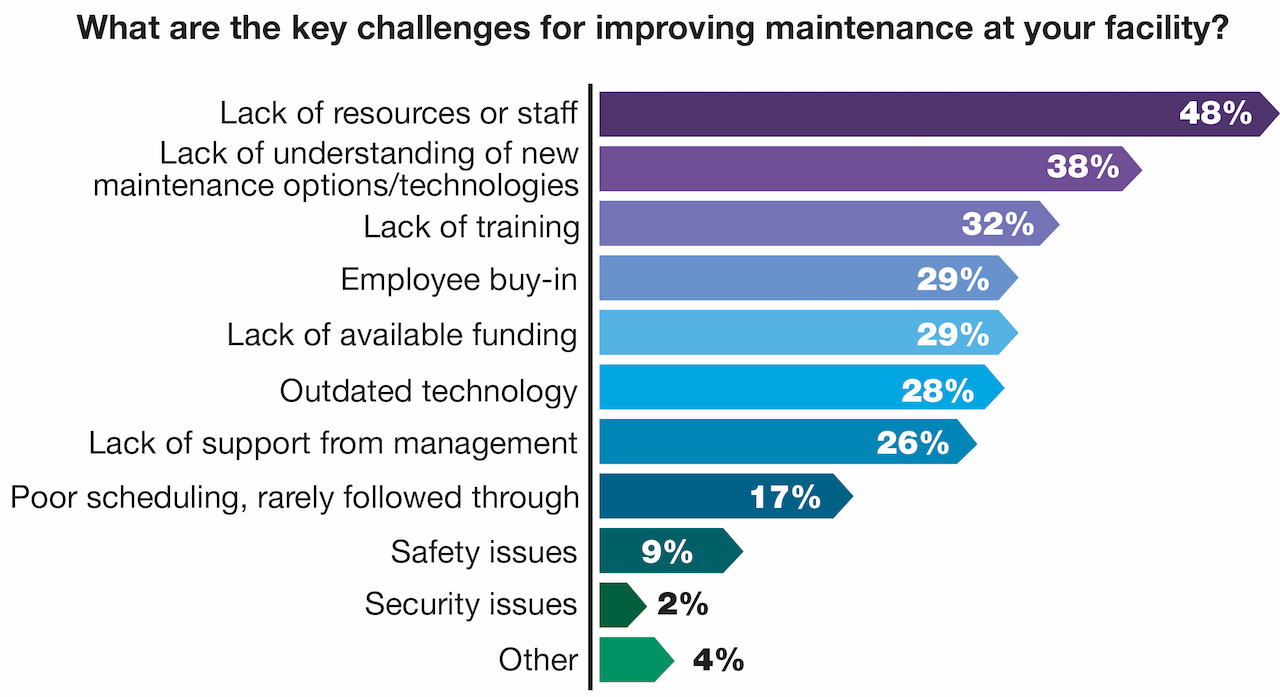
Maintenance systems and strategies continue to slowly transition to a digital process, with greater use of technology to evaluate machine health and develop repair and maintenance schedules.
But it’s a race against time. Aging equipment is the single biggest factor in unscheduled downtime, and equipment failure is a close second.
Those are the conclusions of the 2019 Plant Engineering Maintenance Report, an annual survey sponsored by Advanced Technology Services (ATS). Maintenance professionals in process, discrete and hybrid industries responded to the survey and offered their views on where their operations are today—and where they are headed.
Maintenance managers and plant leaders use a variety of strategies on the plant floor to maintain a safe and productive operation. While preventive maintenance remains the most often-employed strategy (78% of respondents utilize it in some way), the use of a computerized maintenance management system (CMMS) jumped into second place among the strategies, supplanting both reactive (run to failure) maintenance and predictive maintenance. Some combination of these maintenance strategies is used by at least 40% of respondents.
Each strategy has its own merits:
- Preventive maintenance is seen as decreasing downtime, improving safety and energy management, and in being a more flexible strategy,
- Reactive maintenance is seen as cost-effective and easy-to-use
- Predictive maintenance has a lower initial cost
- A CMMS reduces the probability of failure while decreasing downtime and improving overall equipment effectiveness.
Even as technology plays a greater role in maintenance in particular and manufacturing in general, there are still many barriers to adoption. The survey found that 48% of maintenance managers say a lack of resources or staff keeps them from improving their maintenance success, and 38% cite a lack of understanding of new technology options. Other issues, including training, employee buy-in, maintenance funding and a lack of support by management were cited by at least 25% of respondents.
Courtesy: CFE Media, ATS[/caption]
“We continue to see a bright future for technicians, reliability engineers, programmers, and system integrators, especially those who understand the technologies and power systems that are common in manufacturing,” said Owens. “The industrial skills gap and the never-ending evolution in digital technology are creating huge opportunities for young, growth-minded workers to see the advancements a career in manufacturing offers.”
The technology employed in maintenance is varied—and may not even be all that technical. While CMMS and in-house designed spreadsheets and schedules are the two most often used systems, paper and clipboards are still employed in 39% of respondents’ plants. The use of the in-house technology did drop over the past year, from 55% in 2018 to 45% in 2019.
Among the other results from the 2019 Maintenance Study:
- Scheduled maintenance: The average facility spends 20 hours each week on scheduled maintenance, with 53% allocating up to 10% of their annual operating costs to maintenance processes and 30% devoting more than 10% of this budget on maintenance.
- Attention to systems: Rotating equipment (motors, power transmission, etc.), fluid power systems (air, hydraulic, etc.) and plant automation systems are the three areas where facilities dedicate the most maintenance support, followed by internal electrical distribution systems and material handling equipment.
- Training: Maintenance teams are mostly trained on basic mechanical (73%) and electrical skills (72%), as well as safety (72%). Other types of training include lubrication and motors (55%), gearboxes and bearings (52%).
Whether maintenance is seen as a cost center (59% said spending keeps equipment running even while managing costs) or a profit center (34% said maintenance delivers greater capacity to the plant), it remains crucial to plant uptime, productivity and operational excellence.