Predictive maintenance on a hot forming press gets automotive supplier started in smart manufacturing

Smart manufacturing in the form of predictive analytics is driving manufacturers toward a production paradigm of zero downtime, zero waste and zero defects. They’re replacing traditional reactive or preventive maintenance approaches with the use of sensors, Internet of Things (IoT) devices and advanced analytics. Analytics incorporate machine learning algorithms to make sense of the data and ultimately develop better maintenance practices, reductions in unplanned downtime and improvements in productivity (see Figure 1).

From the perspective of suppliers on tight budgets, those goals may sound laudable but risky and expensive. The good news is that rather than concern oneself with modernizing an entire enterprise, a manufacturer can begin to gain the benefits of analytics and connectivity relatively quickly and easily. The solution is to start small, perhaps by networking a single piece of equipment to gather data that enables predictive maintenance, and after seeing benefits accrue, scaling up to other machines.
Hot forming at Metform
That was the approach taken by Metform, a Savannah, IL-based manufacturer that supplies parts and solutions to the automotive and heavy truck industry. Metform is a division of MacLean-Fogg, a fourth-generation family-owned manufacturing company. Metform’s products include Securex wheel nuts for heavy trucks and trailers, gear blanks for automotive and various special fasteners and special formed parts.
The company has 10 Hatebur hot forming presses. The hot forming process is “really the backbone of our business,” said John Delk, Metform director of continuous improvement. “We basically take steel bar, heat it up above the transformation stage to 2,250°F.”
A blank is cut off, then moved to the next station where it is pressed via a punch and die set into a basic form. The workpiece has some contour added at a second station and finally, at a third station, there’s a knockout of a hole in the center of the piece.
“The process happens at a rapid stroke rate per minute — the machine is moving fast, and the parts are very hot,” Delk said.
The largest of the hot forming presses is a Hatebur AMP50XL (see Figure 2). “We only have one of those,” said Metform general manager Steve Wright.
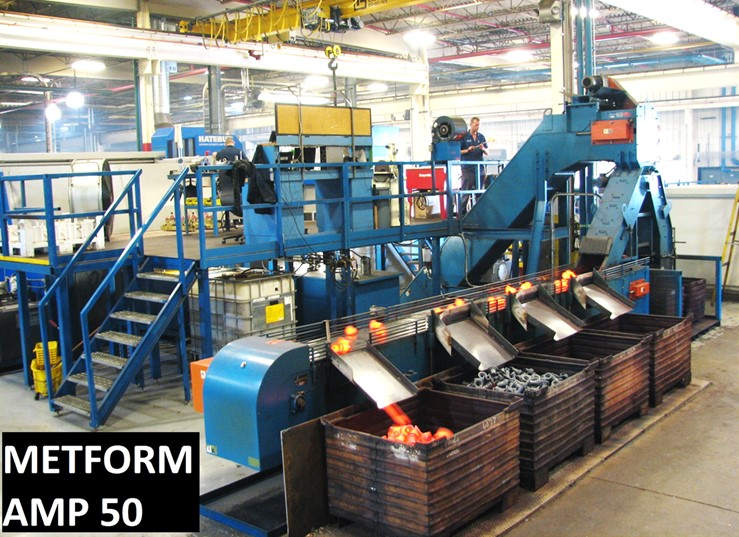
The AMP50XL was installed in 2012 and, in the ensuing nine years, “We’ve had three major unplanned maintenance events on this machine. Given that it’s the only press of that capacity we have, and that we’re using it to supply parts to the automotive industry, we just cannot have that. You can imagine the anxiety those downtimes created for our customers,” Wright said.
While the company did have what it thought was a reliable, robust preventive maintenance system in place, the planned maintenance events made it clear that a better system was needed. “We partnered with IoTco to use Predictronics (PDX),” said Wright.
IoTco LLC, Cincinnati, is a consultancy that works with companies to help create a competitive advantage through digital transformation, using Industrial Internet of Things (IIoT) and predictive analytics tools to connect and analyze complex manufacturing processes, systems and machines. Doing so identifies opportunities to reduce costs, increase efficiencies, eliminate waste and enhance productivity. Predictronics is a predictive analytics and artificial intelligence (AI)/machine-learning software solution.
Starting small, with a big press
A single hot form press, however, as physically large and important to the company as it may be, is still just one piece of equipment. The decision to delve into predictive analytics with just that press is emblematic of Metform’s strategy to achieve a quickly measurable return on investment (ROI) — and also of IoTco’s standard advice to start small.
“We wanted to define the business need for this project. We had an ROI of less than two years,” said Delk. “While starting small, we focused on our most critical asset — and only that asset.”
To calculate ROI, the company considered not just the cost of repairing the press if it went down but also the cost of the lost production time, since it is a single point asset, according to Delk. “Tool life is another area we’re going to explore with this deployment. The combination of those three things and being able to improve our OEE [overall equipment effectiveness] were the key factors that played into the ROI calculation.”
Metform chose to focus specifically on the AMP50XL’s drive train because “that was the area where we saw the biggest opportunity for improvement.” While they’d previously been gathering data from the machine for predictive-maintenance use, the old process was neither efficient nor of adequate detail, they realized. “From a data collection standpoint, there was a lot of spreadsheets, a lot of handwritten notes, a lot of tribal knowledge,” Delk said. “We wanted to make sure we could gather that information and put it into context as we were analyzing the equipment.”
Recognizing that there was a gap in the data, Delk continued, “We had some good information off the machine in terms of how it was performing — data that was captured within the PLC [programmable logic controller] — but we needed to make sure we were providing that data to the right team members at the right time, so that the operators, the maintenance team and our leadership were all getting good information on what our next steps might need to be. We recognized that there was a gap in instrumentation.”
A team that included Metform and MacLean Fogg engineers as well as those from Predictronics and Forging Equipment Solutions — a partner of Hatebur, the manufacturer of the AMP50XL press — concluded that sensors would be needed at four collection points around the drivetrain.
“One important aspect to this project was identifying the vibration sensors and where to put them,” said MacLean Fogg manufacturing engineer Roman Totten. “We discussed whether we wanted single axial or triaxial sensors and where to position them. Ultimately, remembering some of the past press failures, and where in the drive train they may have occurred, we decided that it was best to go with triaxial sensors to get all three ranges of motion for the shafts that we were monitoring,” Totten said. “Also, the locations are widely spread, and touch nearly all the main shafts within the main drive train on that machine.”
From sensor to software
The data from the four newly installed triaxial sensors, as well as data previously available via the PLC, is fed into a system running on Predictronics software, which was developed for Industry 4.0 and smart-factory types of applications, including predictive maintenance.
The software has modules for data collection and connectivity because collecting good quality data is the foundation for making better decisions about your machine health and equipment. It also includes modules for analyzing all this data.
The system leverages a combination of preprocessing techniques, extracting metrics or features from the data, as well as machine learning, Totten said.
“In terms of the architecture for how the solution was configured, we start with the machine layer, and we look at what data we can collect, which includes sensors that may be already there for the control of the machine. This could include tonnage or maybe the stroke rate of the machine and so on,” said Totten.
To this is added data from the four sensors installed to monitor the condition of the machine. “We use our data collection software to aggregate all this data, then send it to the IT server, where more in-depth analytics could be run,” said Totten.
Signal processing involves filtering, finding patterns in the data. Then, feature extraction finds the pertinent “symptoms,” of those metrics related to the health of the machine (see Figure 3).
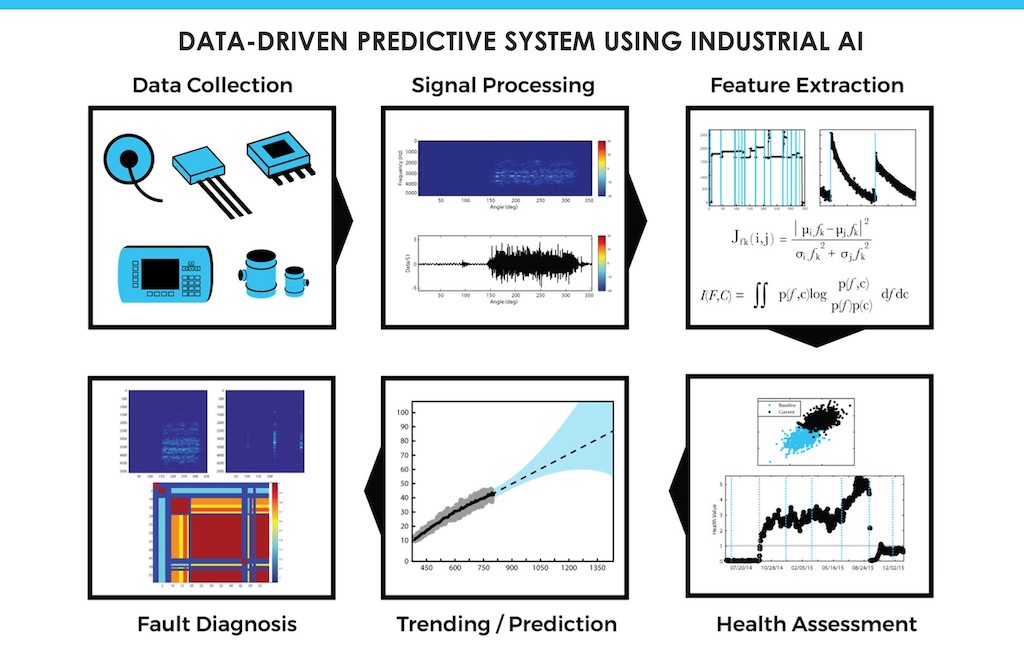
“Those results can then be displayed on a dashboard as well as presented to the end user,” Totten explained. “The idea is to track those over time and use machine learning to compare those to reference conditions, usually initially a baseline condition. And then as you have assessment of the machine or process over time, you can then take additional steps for diagnosis and prediction as needed.”
A picture of health
With the system now in place on the AMP50XL, “every 20 minutes during a production run, we are gathering 10 seconds worth of data at 10,000 Hz. A lot of data being collected,” said Delk. “Our PDX solution is doing some analytics in the background and providing us with a health index.”
Early in the process, the team used about three weeks’ worth of data to establish a baseline of health, Delk said: “Now, the system’s dashboard can show if and how we are deviating from that baseline.”
Delk cautioned that these are still early days on the project but that they are already finding the now-visible data to be useful. “We’re very early in our journey but the process is really generating conversations between our maintenance team, our operations team and [manufacturing engineer] Roman [Totten] and myself,” he said.
“As we see change in the data, we’re asking, ‘what are we seeing here?’ It’s also important to understand what we’re seeing in the data as evidenced on the plant floor. As a result, we have a good snapshot of machine health over time,” Delk said. The business case for the project assumed achieving ROI in two years and on one asset — the AMP50.
“We’re remaining true to our roadmap,” Delk said. “There’s always an urge to engage in mission creep, to expand further, faster, before we’re ready, or to get more out of what’s already accomplished. We need to take the time on the front end and understand the data before we make assumptions regarding the machine’s health.” (See Figure 4).
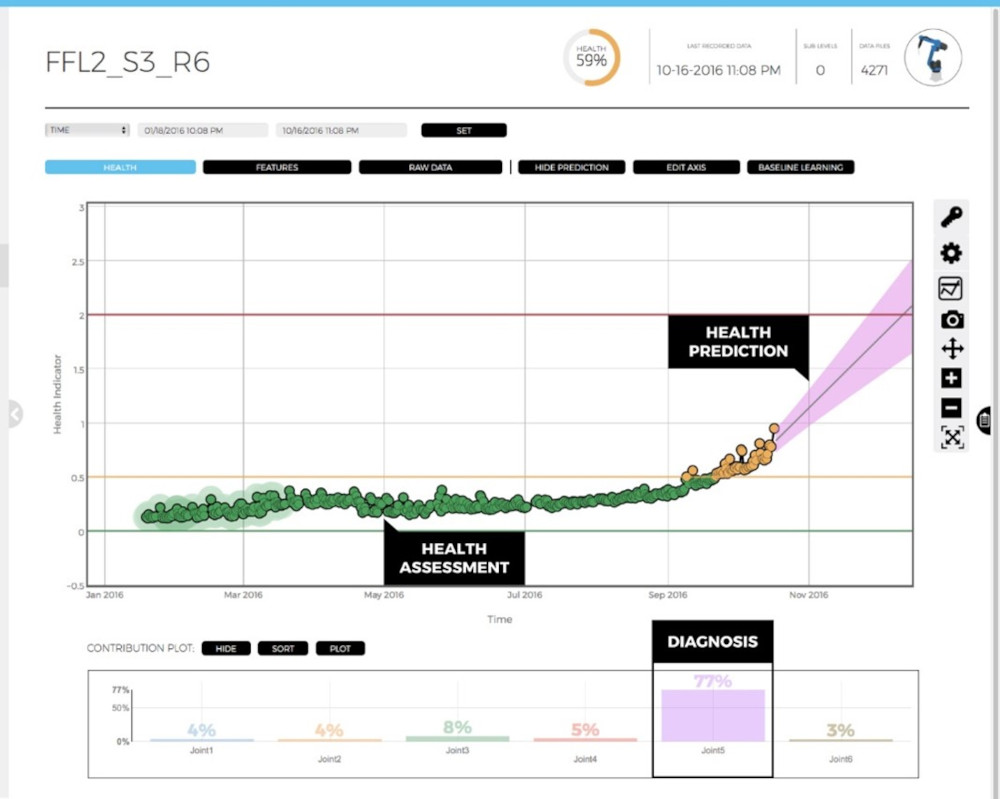
At the same time, the team is excited to — eventually — scale up the process within the facility.
“I’d say as a general manager, I like what I see so far,” said Wright. “We’re able to monitor the machine health, see in real time how the machine is doing and see a signal of a problem before it becomes a major problem. We have a long way to go in terms of learning how to better use the system and gain further confidence in the system, but at this point, I’m really pleased with the progress we made. I’m anxious to expand this to the other nine Hatebur presses.”
Beyond predictive maintenance
Metform is focusing on predictive maintenance and on a single machine — for now. However, there is a lot more that can be done with such a system.
“If you look at the approach to building these predictive systems, using machine learning and artificial intelligence, there are six ‘pillars’ of data we consider when we set up a data collection system,” Siegel said. “They are data collection, signal processing, feature extraction, fault diagnosis, trending/prediction and health assessment.
“Information from controllers using protocols like MT Connect, as well as from additional instrumentation such as the four triaxial sensors added to the Metform machine can be combined together with an appropriate triggering and sampling rate to enable useful data of those six categories to be made visible,” Siegel said. “When you have good quality data, you can make better decisions about your machine processes.”
“And there are also opportunities for enterprises to tie these predictive systems into their maintenance systems or engineering asset management systems that they might be running — SAP, Infor, Oracle, whatever that might be,” said Abuali.
Eventually, Metform will order spare parts in a more predictable fashion. It will optimize preventive maintenance schedules in a more elaborate way. It will eliminate overhead maintenance and shift the operation from a reactive mode to a predictive and preventive, and even prescriptive mode of doing maintenance.
This not only improves OEE but also impacts mean time between failure, mean time to repair and labor and scheduling of maintenance resources.
Predictive quality — actually correlating machine and process data with quality of the products and the lots being produced is also a future possibility. It will be possible to be prescriptive in detecting and predicting scrap that might be produced on the machine due to process parameter deviation or maintenance issues on the machine.
The ability to measure, record and use such data enables benefits to accrue across the production floor and beyond. It’s good to smart small, but the important thing is to start.
ONLINE extra
Dr. Mo Abuali is the CEO and managing partner at IoTco, a CFE Media content partner. He is an Engineering Leader Under 40 winner. Learn more about him here.