The innovative design of magnetic drive pumps provides 10 distinct advantages. Operations that employ these pumps benefit from enhanced reliability and productivity
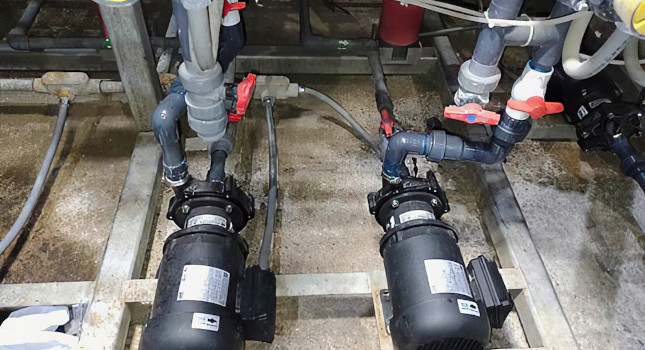
Learning Objectives
- Understand what a mag drive pump is, how it works and its main components.
- Realize the advantages of mag drive pumps and how they maximize plant reliability.
- Learn common applications for mag drive pumps.
Mag drive pump insights
- Magnetic drive pumps, also known as “mag drive” pumps, offer 10 benefits through their innovative design, resulting in enhanced reliability and productivity for various operations.
- Understanding the working principles, components and applications of these pumps can lead to improved plant performance and decreased risks.
Reliable operations are foundational to success. When processes run smoothly, production and profit can increase and costs and risks decrease. Magnetic drive pumps, commonly known as “mag drive” pumps, can play a key role in this process. These durable, efficient pumps are ideal to help maximize plant reliability.
What is a mag drive pump?
A mag drive pump features a magnetic connection between the drive and the motor. To create this type of design, a set of strong magnets is attached to the end of the motor shaft and another set is contained within the impeller assembly. As the drive shaft rotates, the magnets create a balanced field to rotate the impeller. The magnets work in synchronization to create a sealless pump operation.
This operation differs from most other pumps. Traditional centrifugal pumps feature a direct connection between the motor and the impeller. A magnetic pump eliminates the need for this direct drive mechanism. Because magnets rotate the impeller, a magnetic field replaces the mechanical seal.
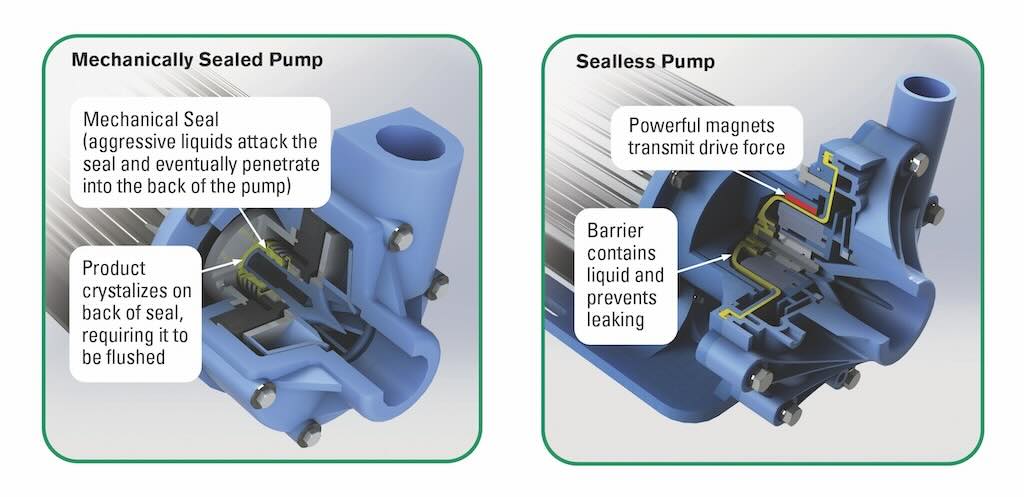
The mag-drive design includes 10 main components:
-
Housing: Also known as the casing, this component is located at the front of the pump. It contains the suction and discharge connections as well as a thrust ring.
-
Impeller: This component contains a thrust ring that partners with the thrust ring inside the housing. Together, the rings guide liquid into the eye of the impeller and absorb any forward thrust in the pump.
-
Impeller drive: Connected to the impeller, the impeller drive contains the magnets that drive the pump.
-
Bushing: This component is located inside the impeller drive. In conjunction with the shaft, the bushing keeps the impeller drive centered inside the pump.
-
Shaft: This part supports the rotating impeller/impeller drive assembly. The shaft prevents the impeller from being magnetically attracted to the drive magnet assembly that is located on the outside of the pump.
-
Barrier: Located at the rear of the pump near the motor, the barrier on a magnetic sealless pump is solid. This differs from a mechanically sealed pump, which would feature an opening in the barrier.
-
Housing O-ring: This component seals the pump to prevent leaks. It is situated between the impeller housing and the barrier.
-
Drive magnet assembly: Also known as the outer drive magnet, this assembly is connected to the motor shaft and contains the magnets that rotate the impeller drive inside the pump when the motor shaft rotates.
-
Magnets: The magnets that drive the pump can be constructed of a variety of materials, including samarium cobalt, neodymium or a mixture of ceramic and neodymium.
-
Motor: There is a wide range of motor types that can potentially drive a magnetic sealless pump. The specific motor selected must be based on pump compatibility.
Mag drive pump advantages
The magnetically driven pump style offers 10 advantages that help improve plant reliability.
1. Leak-free technology. Other pump styles include a direct drive mechanism — the drive shaft is connected to the impeller. This requires the use of a seal on the shaft. However, because mag drive pumps replace this physical mechanism with a magnetic connection, the need for a seal is eliminated.
This sealless technology is a game-changer for many operations. No mechanical seal means no leaks. A mag drive pump maintains two separate contained areas for the motor and the impeller. The pumped liquid remains in a hermetically sealed housing. Even the most corrosive chemicals can be pumped without concern of leakage.
In contrast, pumps with mechanical seals inevitably leak, creating potential hazards to employees and the environment. The mag drive pump design decreases maintenance costs and can dramatically improve system uptime.
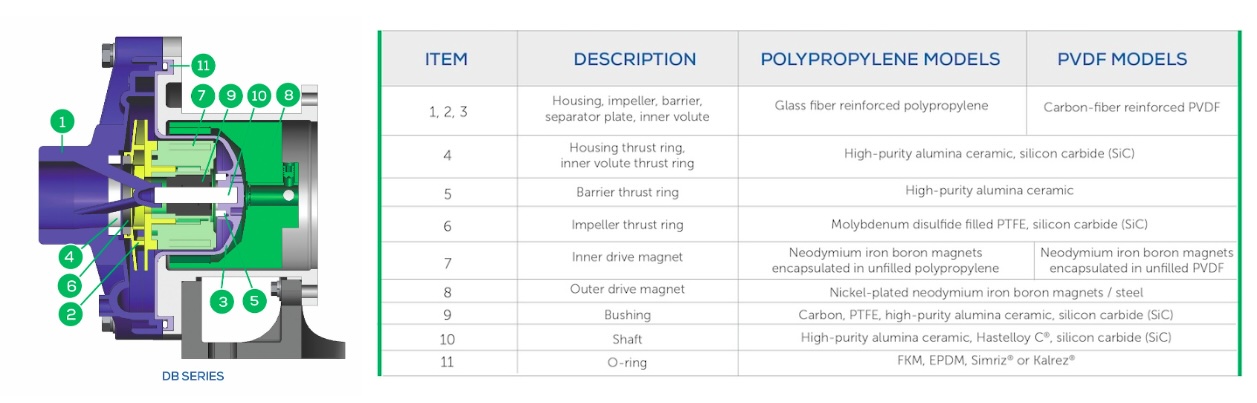
2. Run-dry capability. Many pump designs cannot withstand a run-dry situation. Running dry can quickly damage or even destroy a pump. This may happen due to operator error or an issue in another part of the system. However, this is not a problem for a mag drive pump with a carbon bushing. The innovative carbon formulation provides the pump with a low coefficient of friction.
Some mag drive pump models with this design can run dry for hours without issue. If a system malfunction or human error occurs that causes a run-dry scenario, these pumps have the robust construction to survive. In settings where pumps are not under constant supervision, this feature offers a significant advantage.
3. Chemical resistance. Not all pumps can handle harsh substances. Because a mag drive pump has no mechanical seal that could be affected by strong chemicals, this pump style is ideal for handling tough chemical applications. A mag drive pump can safely and effectively transfer liquids that other pumps cannot. This resistance to chemicals also increases plant safety, particularly for system operators and technicians.
4. Durability. The design of a mag drive pump makes it long-lasting and reliable. Applications that would quickly cause wear and tear to other designs are not an issue for these pumps. Operations that involve the transfer of harsh chemicals, the potential of running dry and other challenges do not faze mag drive pumps. They can operate under extreme conditions while delivering long-lasting performance.
5. Reduced maintenance. A mag drive pump requires little to no maintenance to deliver long-term top performance, potentially for years at a time. It has no mechanical seal that must be replaced periodically and it is resistant to chemicals, so it is not susceptible to corrosion. Pump owners can enjoy years of maintenance-free operation from a mag drive pump. These durable pumps deliver optimal return on investment with little required maintenance and long lifespans.
6. Increased productivity. Any time maintenance is required on a component, productivity suffers. Operations can come to a standstill while technicians make the necessary repairs.
With sealed pump styles, maintenance staff must remove the pump from the piping, decontaminate the unit of toxic fluids, replace the mechanical seal, then reinstall the pump. In some cases, this process could shut down operations for a full shift or longer. If a component must be ordered, the downtime could be extended even further. This downtime directly affects the company’s bottom line.
Mag drive pumps eliminate the time-consuming tasks of maintaining a mechanical seal. When this maintenance task is eliminated, productivity improves. When productivity is strong, so is the bottom line.
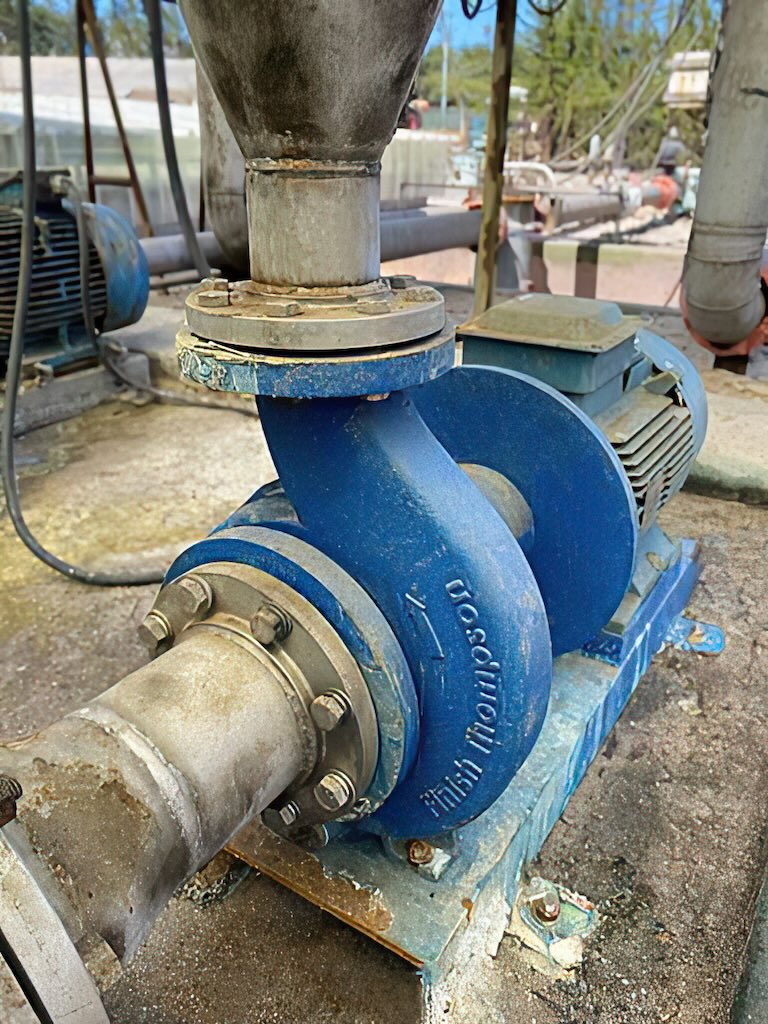
7. Smooth operations. Mag drive pumps offer smooth, accurate flow. This reduces the risk of system failure or production compromises that can be caused by pulsation. With these pumps in place, it is also likely that flow conditioners and pulsation dampeners will not be necessary, which reduces the cost and complexity of the systems involved.
This smooth operation is particularly crucial when transferring chemicals that require high safety measures and delicate handling. It is also key when systems must deliver precision fluid transfers. The smooth flow provided by mag drive pumps provides accurate, reliable transfer, without sacrificing speed and volume.
8. Enhanced safety. In any setting that involves harsh chemicals, safe handling is a primary concern. Mag drive pumps are designed from the ground up to handle the most corrosive and toxic chemicals —without the possibility of leakage. This leak-free design is made possible by eliminating the mechanical seal that would otherwise wear and eventually leak.
With a sealless pump, operators and maintenance personnel will not be exposed to the hazards of leaking chemicals or emissions. This lack of exposure greatly enhances workplace safety. Improved safety leads to fewer accident incidents and medical claims, which consume company resources.
Safer surroundings also improve morale, as employees feel more comfortable in their work environment. A likely result of this improved morale is an additional increase in productivity.
9. Enhanced compliance. If pumps are unable to prevent fugitive emissions, an organization may fail to adhere to local and federal health and safety standards. This not only threatens employee and public safety, but lack of compliance can result in fines or shutdown orders. These situations can prove costly.
Fortunately, magnetic drive pumps make the entire compliance process easier. The lack of mechanical seals in magnetic drive pumps makes it easier to maintain an emission-free environment. This, in turn, makes it easier to comply with emissions standards.
The elimination of emissions creates safe surroundings that comply with health and safety regulations. Pump owners can enjoy full compliance as they remove this concern from their operations.
10. Energy conservation. As facility owners seek sustainable solutions, any components that can create energy-saving operations are a win. Mag drive pumps fall into this category. Mag drive pumps rank high in energy efficiency compared to other pumping technologies.
This energy conservation offers two key benefits. First, efficiency reduces operating costs. Second, the pumps are less demanding of the energy systems involved. This is particularly important when facility managers must run multiple pumps and other equipment simultaneously. The energy-efficient mag drive pumps reduce the strain that large operations can place on energy supplies.
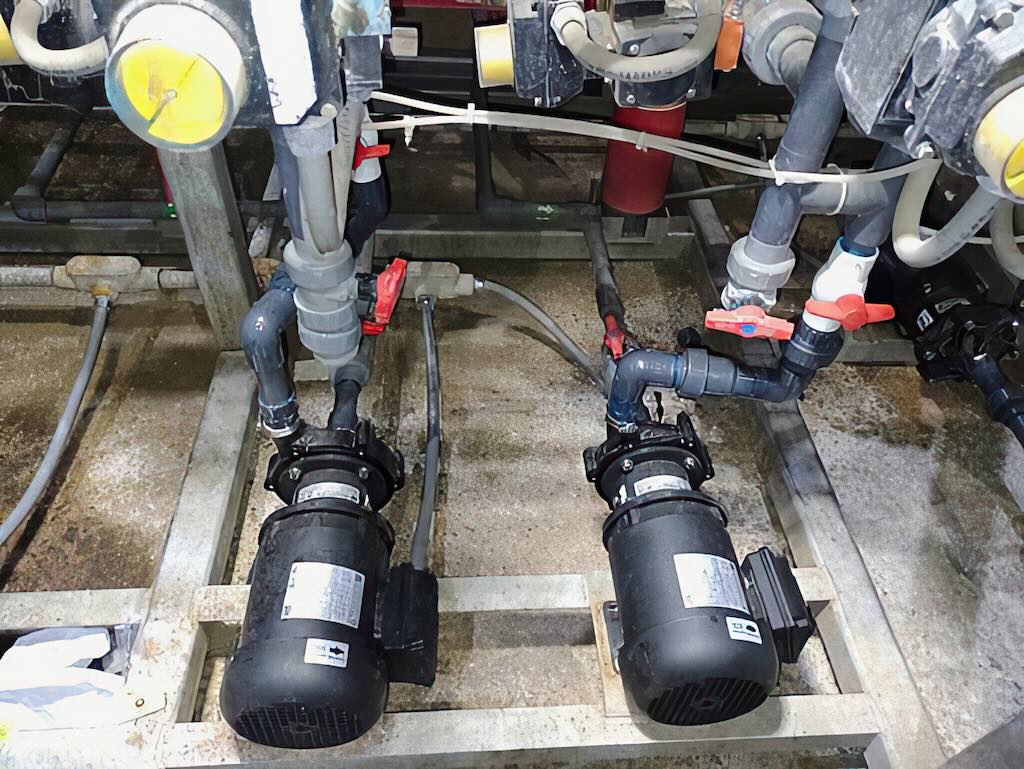
Common applications for mag drive pumps
Yet another advantage of mag drive pumps is their versatility. The benefits noted above make mag drive pumps ideal for myriad applications. The pumps are available in various configurations to suit a full range of operations. Pump owners in each setting can rely on mag drive pumps to provide robust solutions for their liquid transfer needs.
Common mag drive applications include:
-
Aquariums/aquafarming: Magnetic drive pumps provide the delicate care, diverse solutions and durability required to meet the needs of the aquarium industry. These pumps are used for focus tanks, water circulation and wastewater transfer.
-
Chemical manufacturing: When manufacturers need to circulate chemicals, transfer chemicals or provide reliable flow through heat exchangers, a mag drive pump offers a reliable solution. Operators can expose these pumps to the harshest chemicals with confidence in their robust, reliable construction.
-
Diesel exhaust fluid (DEF): Built for heavy-duty chemical transfers, mag drive pumps offer reliability that improves safety and reduces cost for DEF and diesel applications. Mag drive pumps are ideal for DEF dispensing systems, portable DEF transfer, container-to-container transfers, blending and pumping deionized water.
-
Electroplating and anodizing: In this industry, it is essential to keep plating solutions clean and a mag drive pump is ideal to provide flow for filters. Mag drive pumps are often used to provide flow-through eductors and filters, transfer wastewater and transfer chemicals.
-
Food and beverage: Mag drive pumps are ideal for transferring additives and pumping water for cleaning processes in food and beverage applications. Food and Drug Administration-compliant mag drive pumps are also used in the pumping of clean-in-place chemicals.
-
Mining: Mining involves frequent transfers of chemicals, tank unloading and chemical treatment processes. For the harsh conditions often encountered in this industry, operators can turn to a mag drive pump to handle these applications.
-
Steel processing: The steel industry must safely handle acids and acidic wastewater. Manufacturers also need heavy-duty solutions for wire processing, cleaning and steel pickling. A mag drive pump has the sealless, corrosion-resistant design that makes it a top choice for this industry.
-
Wastewater treatment: Treatment plants can use a mag drive pump throughout their facilities. A mag drive pump is perfect for transferring chemicals from bulk storage to tanks, disinfecting treated wastewater and providing flow for ion exchange tanks.
Across multiple industries, mag drive pumps offer robust technology that increases reliability and decreases costs.