At the 2023 EASA convention, one session covered pump repair and working with close tolerances.
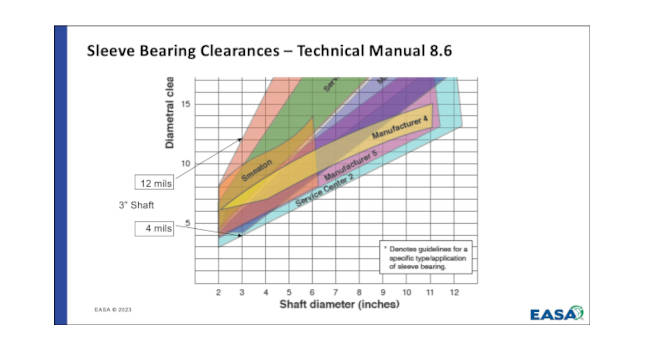
Pump repair is a critical aspect of maintaining the efficiency and longevity of pumping systems. At the 2023 Electrical Apparatus Service Association (EASA) convention, Gene Vogel, pump and vibration specialist at EASA, dove into the intricacies of working with close tolerance fits in pump repair.
Key aspects of pump repair
Pump repair involves several key aspects, including:
-
Rolling element bearings
-
Sleeve bearings (horizontal)
-
Vertical turbine pump (VTP) bearings
-
Impeller-casing wear rings
-
Casing rabbets
-
VTP motor mounting flange runout and P-flange type motor bases
-
Throttle (throat) bushings
-
Impeller-shaft fit
-
Stage bushings.
Sleeve bearing clearances
Sleeve bearing clearances are influenced by factors such as rotor weight and radial load, rotating speed, bearing length to diameter ratio, oil viscosity and oil temperature. It’s crucial to calculate load versus hydrodynamic lift and angle for accurate clearances.
Casing wear rings and impeller wear rings
The clearance of casing wear rings and impeller wear rings significantly impacts the efficiency of pumps. Greater clearance reduces efficiency. High specific speed pumps (high flow, low head) are less affected by wear ring clearances, while low specific speed pumps (high head, low flow) are more affected. For galling materials, an additional 0.005″ is recommended.
Impeller to shaft fits and stage bushings in multi-stage pumps
Impellers may be mounted on straight, tapered, or threaded shafts. Straight shafts typically have a key, and impellers are a clearance fit: 0.000″ to 0.002″ (0.0 to 0.05 mm). The key must be snug in the shaft keyway. For tapered shafts, the mounting surface must simply be smooth, about 32µin (0.8µ) Ra.
The clearance of stage bushings is critical for pump stages greater than 2. This clearance maximizes the Lomakin effect and minimizes cross-stage leakage. The Lomakin effect is based on axial flow, not radial flow (bearings). Factors influencing this include the shaft L/D ratio, stage bushing length and pressure differential. Manufacturer’s tolerances apply.
Installing wear rings
In end suction pumps, wear rings are installed with approximately 0.002″ (0.05mm) interference fit. In split case pumps, there is a 0.000 to 0.001″ (0.05mm) clearance fit, and an anti-spin retainer is needed. When installing wear rings on the impeller suction eye, the ring and impeller should have a matching alloy with a 0.003″ (0.07mm) interference. If a bronze ring is used on a ferrous alloy impeller, a 0.005″ (0.13mm) interference is recommended.
Understanding and working with close tolerance fits is a crucial aspect of effective pump repair. By adhering to these guidelines, it ensures the efficient and long-lasting operation of pump systems.