Canadian food & beverage company, Grober Nutrition, expanded to the U.S. with the help of Optimation Technology Inc., and keeps growing.
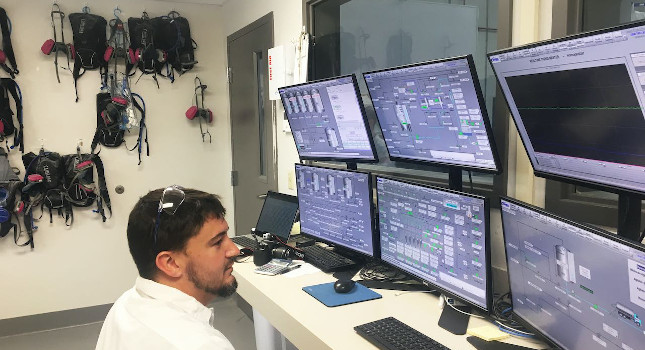
They say hindsight is 20/20. You can look back on most things in life and see what you did well and what you would do differently. Often, the wisdom that comes with years allows you to see these distinctions better. For capital projects, it’s one thing to look back on how you executed the project. What about after you’ve been operating for a few years after completion? If you knew then what you know now, what would you change?
Two years after the completion of a milk replacer production facility for Grober Nutrition, plant personnel reflect on how the new plant has met expectations and prompted for new goals for the not-so-distant future.
The beginning
Grober Nutrition is a family-owned, Canadian-based company that provides consistent, nutritional and safe products to optimize the growth and health of young animals such as calves, lambs, kids, pets and zoo animals. Looking to expand into the U.S. market, Grober Nutrition USA was formed, along with plans for a new, state-of-the-art milk replacer production facility.
Grober’s product is a powdered formula used to replace milk for young animals. Surplus whey from a skim milk manufacturer is available as a supply component for the formula. The process includes evaporating permeate to a specific concentration, which is used as an ingredient in a slurry, which is then fed to a large dryer. The permeate and other proprietary ingredients (whey, oil/fat, dairy) are blended to produce the final product. To sell this high-end product throughout the U.S., the company needed a turnkey supplier for electrical, process piping, controls and instrumentation support of a $12 million, 60,000-square-foot facility in Auburn, New York.
Enter Optimation Technology, an engineering, design and skilled trades services company that provides turnkey solutions for industrial clients. Through a formal bidding process, Grober chose Optimation to support the new plant’s build. Optimation provided engineering, controls programming and design, and skilled trade’s installation services, which included mechanical, electrical and construction management support, as well as control panel, pipe supports and frame fabrication (see Figure 1).
Figure 2: Around 10,000 feet of stainless-steel piping, some large diameter, was installed at Grober by Optimation as a part of the project. Courtesy: Optimation Technology Inc.[/caption]
Because of the complexity of the process, the software was broken down into three different ControlLogix PLCs. There was an evaporator/tank farm PLC, a batching/mixing/CIP PLC and a homogenization/dryer PLC. These breakdowns were chosen because of the input/output (I/O) required for each. It also helped make each program more manageable.
Fast forward two years
Plant manager Charles Balko and production manager Brian Crannell didn’t start working at Grober until after the project was completed in 2017. They weren’t a part of the specification development. They have the benefit of working in the plant for the past two years and the fresh perspective that comes from not being involved in the project from the beginning.
Crannell worked with Optimation during the final programming steps on the evaporator and Filtermat dryer process. He taught himself Rockwell’s Sequence Manager system using the training documents created by Optimation. Now, he’s in charge of teaching all new operators how to run the system.
“As far as the system goes, it’s user friendly,” Crannell said. “As far as a graphics standpoint, and the overall operations and programming standpoint, it is a well thought out system. The book goes into detail on how to run the sequence manager, how to skip process steps, how to manually run the process and how to pause/hold the recipe steps. This system is complex, but overall it’s a well thought-out program.”
The complexity of the system is due to the rarity of the Filtermat dryer, Balko said. “There’s a few dozen Filtermat dryers in the United States and most are drying WPC or NFDM not PEF, so this system was very much a one-off,” he said.
“Hard to say that anyone could write the specs for this project, because they hadn’t done it before,” Balko said. “Because of the rarity of the equipment. The recipe screens have good specs because it’s pretty cut and dry. The controls of the drying system were more of a theory. It’s kind of hard to write a good set of specs on how we wanted it to work, because we didn’t know. The drying screen is really confusing, because there’s a lot going on there. But could they have done it differently? Yeah, but would it have been better? No, probably not. There’s just so much information there, so when you’re trying to learn, it just overwhelms people.”
Security and training
As new operators are trained on the complex drying screen, Balko and Crannell see one thing they would have pushed for had they been involved in the project early on: different levels of security for operators, based on levels of experience. This was discussed early on by Optimation and Grober. However, Balko and Crannell’s predecessors passed on multiple levels of security. Two years into using and training new operators on the system have shown how important it can be.
“If you have a new operator who is overzealous and likes to change things that he shouldn’t be changing, the current systems allow the operator to do that, where in some cases we wouldn’t want that,” Crannell said. “Let’s say the operator makes a setpoint adjustment on a dryer/evaporator parameter, and they type in an incorrect setpoint number. The system will take it. The direct result from this can cause major issues with product quality and damage to the process equipment.”
Another possibility for the future is adding remote viewing of the system’s screens, allowing a supervisor and/or process engineer to view and make adjustments off site. “There are times when I receive calls in the middle of the night, and I don’t have access to the process screens,” Crannell said. “I’ve had to either do it through Team Viewer or through my general knowledge of the process. This system is so complex, so to try and walk an operator through an issue when you’re not right there, it’s difficult.”
In addition to adding security, Grober also is looking at getting the most of the system’s historian. This will aid the company in audits and with providing clients with specific information.
“Some auditors will come in and want to know when things were last cleaned in place and the increments of cleaning, so if you can provide the access to that via the historian, that would be phenomenal,” Crannell said.
Safety
Balko and Crannell agreed safety is priority number one at the plant. Grober has made a few programming changes to make the system more efficient and safer for the operators. It added graphics and controls for a K-Tron doser, powder knockers and frack tank. They’ve also reconfigured the recipe screen to allow for more information.
They’ve also identified the need for machine guarding in various areas of the plant. Machine guarding is a service Optimation provides for clients and has seen a high demand for recently. Often, however, a request for guarding comes through because an employee has been hurt. In Grober’s case, the company is looking to safeguard employees before an incident occurs. Crannell said these safety observations often are made while performing day-to-day operations in the plant.
“Honestly, the process is so complex, to know every little aspect of safety, it’s one of those things that you learn as you go,” Crannell said. “Knowing what we know now, if you were to build now, there would be quite a few things that we would do differently from a safety standpoint.” (All of these safety issues have been corrected as they come up; Grober has a robust safety committee).
Expansion
Grober USA has seen great success in its first two years. Production goals were projected to be 2,800 pounds per hour. After Grober made modifications to its dryer chamber, it has been able to smash that goal, producing 3,500 pounds per hour on average to a max of 4,200 pounds per hour. “Originally, this plant was built here to make enough product for us and to send to Canada,” Balko said. “Turns out, we can make more. We’re now selling the additional product to non-competitors on the west coast.”
With success comes another challenge, Balko said. Grober USA needs to expand already. “The place is too small. We don’t have enough tanks now. We’re already realizing that we need to grow, adding two more tanks and extending the building out,” he said (see Figure 3).
This will require many little changes to the overall system going forward, such as making changes to the liquefier screens.
Grober has started to penetrate the American market and has goals to continue to ramp up more sales in the U.S., as well as looking to export to other countries. To meet these goals, Balko and Crannell’s plans for continuous improvement and expansion of the plant’s operations will be key. Grober has engaged Optimation to aid in the expansion efforts, which Balko said needs to happen as soon as possible.
Jennifer Palumbo is director of marketing at Optimation Technology Inc., a certified member of the Control System Integrators Association (CSIA). For more, visit the company profile on the Industrial Automation Exchange.
This article appears in the Applied Automation supplement for Control Engineering and Plant Engineering.