Select the right centrifugal pump for fluid transfer applications.
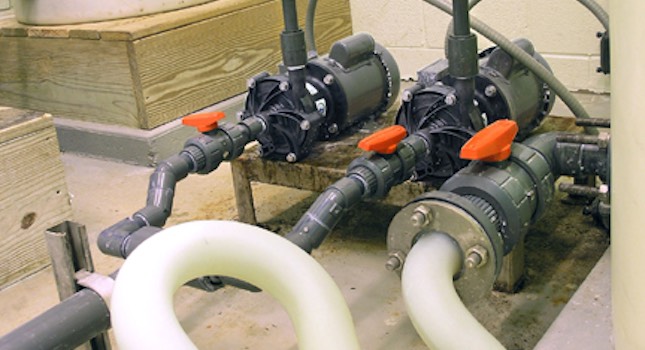
Chemicals Insights
- Select the correct centrifugal pump for fluid transfer applications to properly transfer harsh chemicals to its destination.
- Important considerations are the chemicals name, temperature, viscosity, characteristics and flammability.
There are many variables factoring into selecting the right type of centrifugal pump with the correct materials of construction for chemical or corrosive fluid transfer applications. This article provides the specific information needed for which fluids need to be pumped. Safe and reliable transfer of harsh chemicals can be a challenge in a wide range of manufacturing and processing industries, including automotive, electronics, water treatment, steel production, anodizing, air pollution control and more.
Centrifugal pumps provide a smooth flow and are ideal for numerous applications, including transferring chemicals from bulk storage, unloading tank trucks/rail cars, and for filtration and recirculation systems.
If you’re searching for a pump to transfer these types of chemicals, you’ll want to make sure to select the pump that’s the best fit for your needs.
Corrosive chemicals – an overview
Before sharing the seven fluid characteristics to know before you make a pump selection, it’s important to first understand corrosive chemicals.
Corrosive chemicals are fluids that will attack and destroy the materials they encounter. Metals, stone, glass, elastomers, and even some types of plastics can be susceptible to corrosion from various fluids like acids, bases, and solvents. Some corrosive materials can even cause physical hazards when exposed to incompatible materials. For example, when exposed to an incompatible metal, many inorganic acids can release hydrogen gas, which can pose a fire and explosion hazard.
Corrosive chemicals can be broadly defined as the following:
- Strong acids
- Weak acids
- Strong bases
- Weak bases
- Dehydrating agents
- Oxidizing agents
Some chemicals can belong to more than one category. For example, sulfuric acid, the most commonly used chemical in the world (source: World of Chemicals), frequently used as a raw material or processing agent for fertilizers, pharmaceuticals, gasoline, and others, is a strong acid, a dehydrating agent, and an oxidizer. Corrosive materials can also belong to other hazard categories such as toxic (poisonous) or flammable.
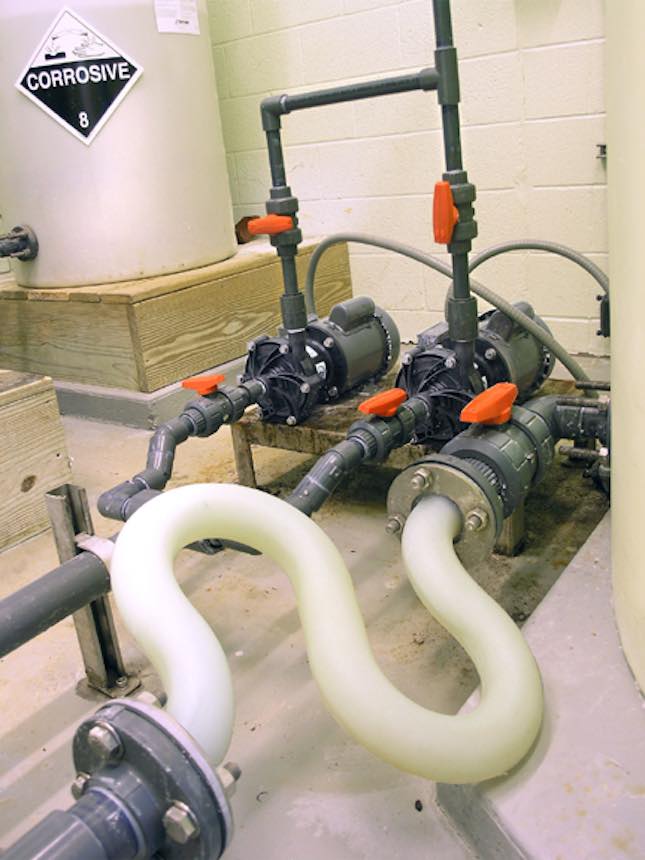
The pH is the definition of a strong or weak acid or base (strength). Anything with a pH lower than 7 is considered acidic, while anything with a pH above 7 is basic. Strong acids are considered to be atoms that readily donate protons (H+), and strong bases to be atoms that readily accept protons [donate electrons, (OH-)]. Therefore, an acid solution would contain a higher concentration of H+ ions, and a basic solution would contain a lower concentration. How readily an acid or base dissociates into its H+ and OH- ions correlates to the strength of the solution.
Numerous chemical resistance guides can be found through Internet searches, and many pump manufacturers have their own guides. Some pump manufacturers have electronic selection programs that ensure only compatible materials are selected. If there is any doubt about compatibility, consult with the pump manufacturer at the earliest possible stage in the specification process.
Seven considerations
The pump supplier needs specific information to determine the chemical resistance of the materials of its construction so they can make the proper centrifugal pump recommendation for your application.
Here’s the specific information to gather on the fluid to be pumped:
-
Fluid name: The fluid name is required to use chemical resistance guides. There may be more than one chemical listed if the fluid is a mixture. The fluid can also be listed by trade name, which can vary by manufacturer. This information should be included in the Safety Data Sheet (SDS, formerly MSDS) for the fluid.
-
Concentration: The concentration is required to use chemical resistance guides. Some materials may be suitable with lower (or higher) concentrations but not others. Again, refer to the SDS for the fluid.
-
Fluid temperature: Chemical resistance for various materials of construction can vary by temperature (typically an issue at higher than ambient temperatures).
-
Specific gravity: The specific gravity of the fluid is used to specify the correct motor power (heavier fluids require more power to pump the same volume compared to lighter fluids) and, if it’s a self-priming application, to adjust the pump’s maximum lift capability. Specific gravity is also used to calculate the maximum working pressure requirement to confirm it does not exceed the pump’s rating. Again, the SDS should have this information.
-
Viscosity at pumping temperature: The viscosity at pumping temperature is used to adjust the head, flow, and motor power on centrifugal pumps.
-
Determine solids characteristics (if present): If solids are present, what are the concentration, particle size, and hardness? Solids can affect pump material specification. Some materials, such as silicon carbide, are very hard and handle solids better.
-
Flammability: Is the material flammable or combustible? This can affect the pump components and materials of construction, such as the electric motor type and the pump’s ability to be grounded/bonded. The National Fire Protection Association publication NFPA30, Flammable Liquids Code, is a good reference in the U.S. for the handling, storage, and use of flammable liquids with a flashpoint below 200° F (93° C).
Supply the right information
By considering these seven pieces of information and consulting the experts, such as pump manufacturers or local pump distributors who are experienced in selecting centrifugal pumps for use with corrosive chemicals, you’ll be well on your way to choosing the right pump to fit your specific needs.