Put analytics in the hands of the process experts who understand the data best.
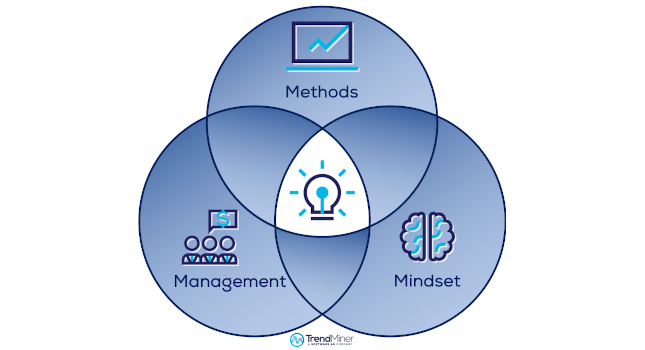
What is the best way for a company to collect and analyze the data needed to make data-driven decisions that support good business outcomes? Let’s look at some of the best ways to successfully implement advanced analytics for multiple operational stakeholders.
Many companies that monitor and control production processes store years of sensor-generated time-series data in an historian. More and more sensors are today used to monitor or predict asset performance. Besides sensor-generated time-series data, operational data is gathered in many forms, formats and systems, including batch records, product quality data, shift logbook and maintenance data.
If made accessible and ready to use for people who understand what the data means, it can improve operational performance.
Industrial analytics landscape
In addition to real-time process data, information gathering encompasses things like feed stocks and customer and supplier information, as well as other business process data. This data also can be analyzed to improve performance. Data scientists have used tools such as R, Python, Jupiter and others to do this work. Data is captured from various sources, pre-processed and prepared for use in data models.
Subject-matter experts help data scientists better understand the data’s significance, contribute to building the data model and validate its use prior to deployment and use. These projects take time and resources.
In recent years many analytics tools and applications have been introduced. The variety of data, data sources and objectives create confusion as to which tools to use for which data, by whom and for what?
For businesses, tools are available to design, measure and analyze business processes, customer behaviors and supply chain performance. Other tools are used to analyze, monitor and predict operational performance. For production processes available applications can be mapped across two axis: analytics maturity (horizontal) and fit for purpose (vertical).
In this analytics landscape (See figure 3) we see generic tools or platforms to track operational performance (descriptive analytics), such as business intelligence software (BI tools) to retrieve, analyze, transform and report data. Tools and platforms are available for all sorts of generic big data, even for higher analytics maturity levels. In many cases these tools and platforms require customization by data scientists for specific use cases.
For more specific data, such as sensor-generated time-series data of the production process, we see the various historians in the upper left corner of the figure. Historian vendors also deliver some analytics capabilities, but often require data engineers or scientists to work with analytics capabilities to bring the results towards higher analytics maturity levels such as discovery, diagnostic or predictive analytics.
Finally, another set of applications includes tools to empower subject matter experts, such as process and asset engineers, who already understand what the data means, to analyze the data themselves. We call those tools self-service industrial analytics tools.
Empowering operational teams
State-of-the-art self-service analytics applications makes it possible for non-data scientists to analyze their production processes. The solution should enable the team to analyze, monitor and predict production performance within its operational context, and at the same time give each stakeholder a personalized production cockpit to monitor operational performance related to the key performance indicators (KPIs) they are responsible for.
To be effective, we believe a self-service industrial analytics solution must be a fully web-based plug & play solution delivering value out of the box, either installed on premises or provided as a full SaaS solution. It should support a wide variety of historians and allows incorporation of non-industrial contextual data in analysis (e.g., financial database, maintenance management systems, laboratory information management system (LIMS), out-of-expectation (OOE) results, batch systems, unstructured data and others).
Process and asset engineers must be able to use high speed trend analysis to quickly search and validate production issues, based on embedded artificial intelligence/machine learning (AI/ML) capabilities. They must be able to quickly find root causes for process anomalies through pattern recognition, statistical capabilities or provided recommendations, without the need for building data models.
On the other hand, engineers should be able to convert multiple periods of good process behavior into fingerprints to use in monitoring operational performance. In case of deviations they can determine who to send notifications to for taking appropriate measures. When physical sensors are not available, soft sensors can be created to analyze and monitor product quality.
The solution should also allow for predictive performance scenarios, global collaboration, knowledge capturing and creation of personal production cockpits. In this way each operational team member can make better decisions, faster, and derive benefits related to their organizational role.
Introduction to the organization
A proven approach to success with industrial analytics is to start small and scale fast. By selecting some practical use cases based on time-series data can prove quickly the value of an analytics tool. Success with analytics can be gained in three main areas:
- Solve previously unsolved process performance issues
- Verify hypotheses and prove them to be either true or false, so they can be addressed or ruled out for the future
- Find new ways to improve performance, with the data providing new insights.
Some successful use cases that led to corporate rollouts for users leveraging self-service industrial analytics:
- Reduce emissions by improving off-gas treatment: Search and discovery analytics proved the engineer’s hypothesis, enabling them to reduce problematic situations with off-gas treatment by 63% and greatly reducing emissions.
- Production quality optimization: By comparing good quality periods with bad quality periods in production runs and use of “layer compare,” engineers easily identify what caused a quality problem, helping to ensure high-quality production runs in the future.
- Eliminate a potential production loss of 125 tons: Process engineers at a chemical facility were experiencing unwanted production stops. By tagging good batches as “fingerprints” they were soon able to identify deviations in production runs – leading them to a problem in the control system. Finding the root cause with fingerprints helped them eliminate a potential production loss of 125 tons, or almost $300,000.
- Energy monitoring without Excel: Energy monitoring is an important factor when addressing sustainability. In the past, one chemical company would use Excel files to manually compare energy consumption data from one year to another. Self-service analytics now allows the engineers to easily bring a certain year into focus. By adding the following years of energy consumption as layers, they are able to easily compare large periods of time — without needing to use Excel.
- Other typical cases self-service analytics can be applied to:
- Yield increase through cycle time reduction
- Predicting fouling for heat exchangers
- Monitor pump performance n distribution network
Once it’s proven analytics in the hands of the operation personnel brings success, it can be introduced into the larger organization. With the technology and its methods are proven within the smaller group, management can support wider implementations and a team must be created to introduce the tool to additional potential users and win their support.
To successfully introduce the new analytics application its value must be demonstrated to each user. When they see quick results in support of their own work, they are more receptive to change. It helps to have local champions who are thoroughly trained and can help others in case of questions or how to best address specific use cases. Internal communication about the roll out and the successes the users make, helps accelerate the introduction.
Organizational evolution
On an organizational level, the following factors must be put in place to make the introduction of state-of-the-art industrial analytics software a success:
- Create a dedicated roll-out team within the business unit to run the project in cooperation with local teams
- Create a project management team with engineering and production data analytics expertise. These experts can help the local plants and the users to become successful with the new tool
- Create an asset analytics community to exchange ideas and best practices
- Implement individual success plans, in collaboration with managers of the business units, to help users change behaviors and feel supported
- Set up a digital working group to act as a steering committee, with stakeholders from business unit production management, to help smooth the introduction and global roll-out.
Concluding thoughts
Becoming fully digitalized is a big undertaking, especially for brownfield operations. It’s best to start small in an area of the company where the chances of success are highest. The experience of a wide range of users implementing self-service analytics indicates their use of sensor-generated time-series data leads to a high success rate.
Analytics empowered process experts can make data-driven decisions to improve overall operational performance, meet short-term and long-term organizational goals and transform organizations for sustained market competitiveness.
Edwin van Dijk is a company vice president with Trendminer.
This article appears in the IIoT for Engineers supplement for Control Engineering and Plant Engineering.