Learn how manufacturers can manage the balance between connectivity and the large capital expenditures to modernize and what plants will be able to do in the future as a result.
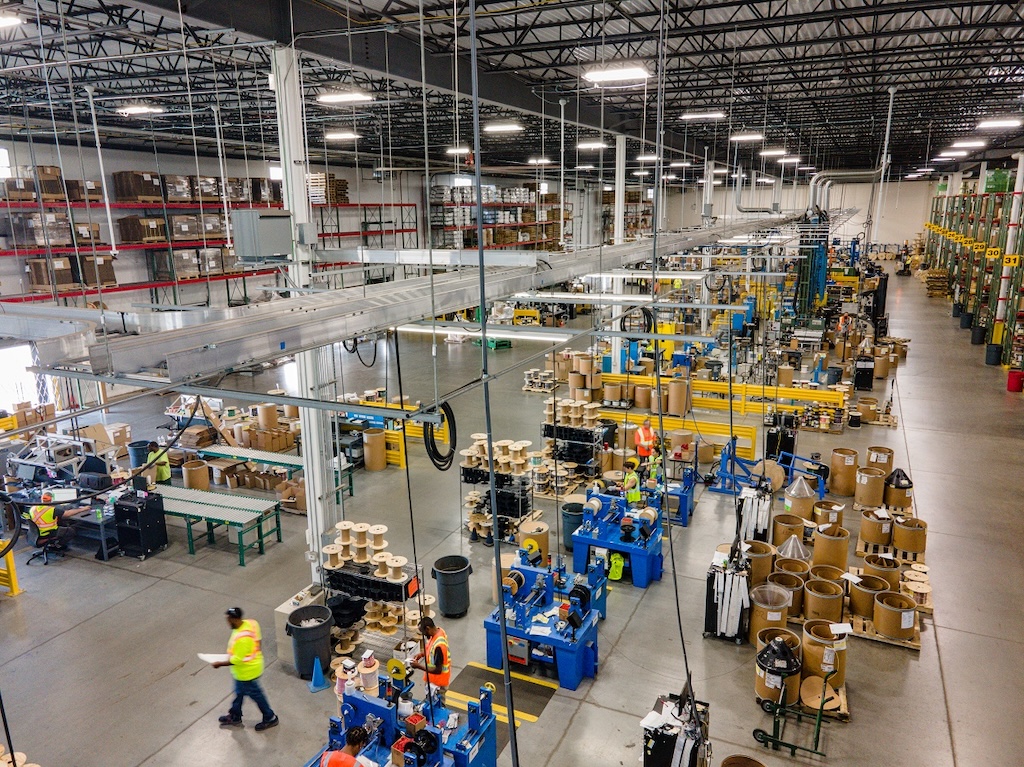
Learning Objectives
- Know the six types of data that industrial manufacturers generate and how they can be better used.
- Learn how data feeds can be unified cost effectively.
- Hear what plants that are investing in data contextualization and process optimization are achieving.
Data insights
- Manufacturers are harnessing data-driven integration of operational and information technology to break down silos, enhance automation and optimize efficiency, enabling industry 4.0 advancements while balancing cost-effective modernization.
- It’s not enough for plants to simply have assets that are “connected” if they cannot provide any real visibility needed to modify operations, enhance production, spur efficiency or avoid downtime.
Manufacturers of all sizes are in the midst of a transformation, driven in part by the emergence of new technologies that can automate, enhance and speed their operations. For almost a decade, firms have been working to incorporate operational technology (OT) with information technology (IT) and have experienced incremental benefits that are impactful but only graze the surface of what’s possible.
Plant engineers have been advocating to blend the powers of plant hardware and software to generate a more far-reaching improvement and other departments are finally sitting up and taking notice.
As companies have begun to embrace industry 4.0, it has highlighted the opportunities that automation and industrial software platforms can provide. It’s not enough to simply have assets that are “connected” if they cannot provide any real visibility needed to modify operations, enhance production, spur efficiency or avoid downtime. And the information cannot live in a silo, rather the shop floor data needs to be delivered in real time throughout the enterprise for better integration and decision-making.
By establishing the infrastructure required to connect the hardware and software applications available on the plant floor to the data flows from business applications, manufacturers can finally tap into the vast amount of data generated from machines, sensors and operational analytics to connect the shop and top floors.
But how can manufacturers embrace this shift to industry 4.0 and focus on true connectivity while balancing large capital expenditures around upgrading and modernizing your installed base production equipment? And what will this technical transition enable plants to do in the future?
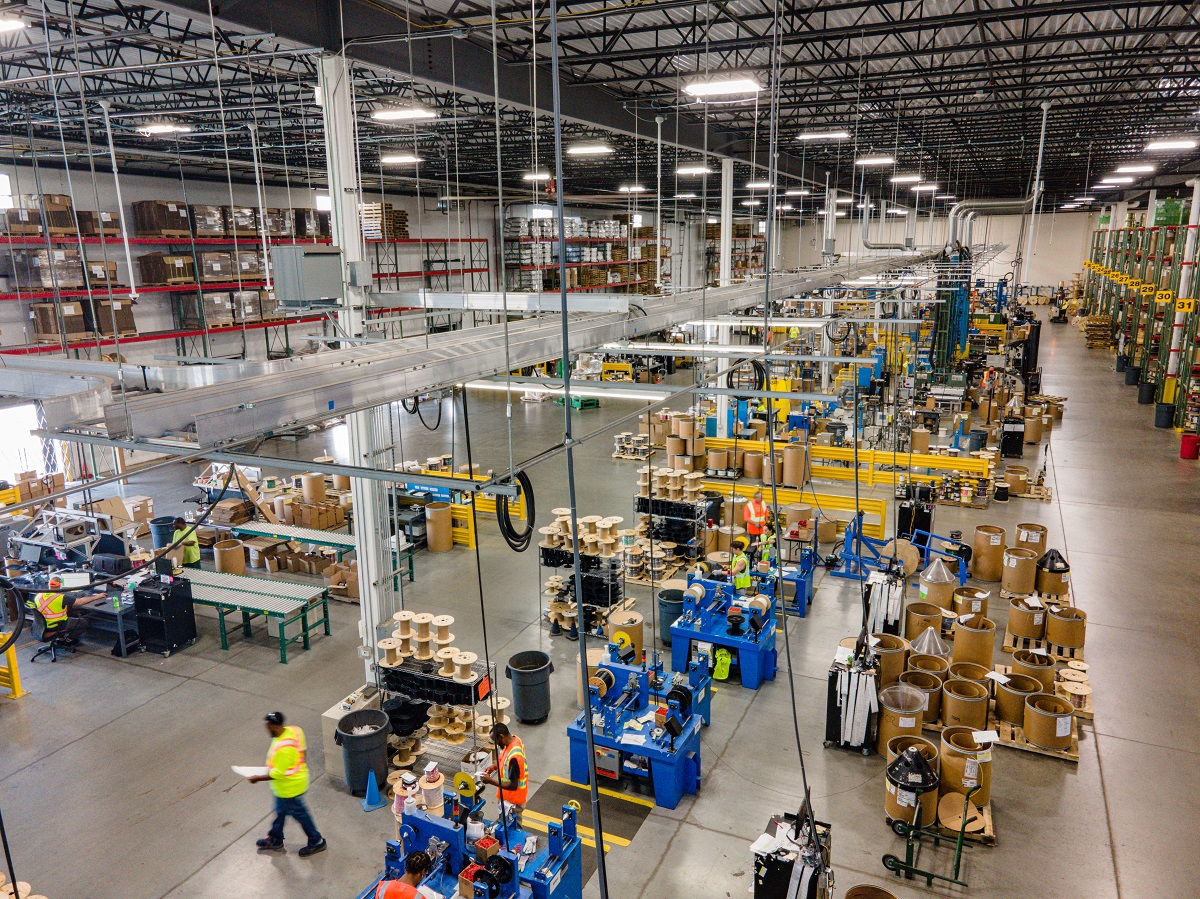
[subhead/h2] How data integration can help
Plant managers are working hard to stay on top of production, meet quality and compliance standards and maintain tight schedules, all while trying to keep costs down and capacity high. The operations side of the business is working to identify production opportunities, speed efficiency and reconcile planned production versus actual.
While collectively these two groups recognize they may not be leveraging all of the data that’s being collected from the plant floor, undergoing a digital transformation project to amplify their efforts can seem like a daunting task given all of the priorities already in play. But, leveraging all of the intelligence that’s already being collected across the plant floor and integrating it into an accessible way for all aspects of the business, is about working smarter, not harder. There’s certainly a lot of information to sift through; industrial manufacturers generate six different categories of data:
Operational data, which includes machine performance information such as speed, pressure, temperature and torque measurements from various parts of machinery.
Machine health and status data generated from sensors that can report on the overall operational status of equipment, such as wear and tear, heat generation and system integrity.
Quality control data generated from production lines, sensors and vision systems as they collect information to ensure quality control and compliance with specifications.
Safety data including details on safety interlocks, operator presence and access control to ensure workplace safety and compliance.
Energy consumption data that relies on smart sensors and devices to track energy. This data is used to identify energy-saving opportunities and to ensure sustainable operations.
Network and communication data, which includes information about the performance and integrity of network communications within smart devices and components.
Much of that data goes unnoticed or underused because the right systems aren’t in place to make use of the information. As software continues to become a bigger part of the network infrastructure (OT environment), solutions are more refined and bundled to more seamlessly bring hardware and software together. Capitalizing on these advancements can allow you to replace the haphazardly connected assets and first-generation OT networks that many plants have today.
For some manufacturers, this may mean embedding industrial software on top of existing product lines or machines, while others may need to update an entire production line. Smaller, more modular application software and hardware platforms built on open architectures allow plants to work in an app-like environment with data that resides on the edge or in the cloud as part of the plant’s connected environment. This low-code option can help bring plants online more quickly, with modules built out for various functions, like plant performance or scheduling.
However, the infrastructure is architected for your plant, truly connecting data and creating a solid operational foundation can deliver the insights needed to make industry 4.0 a reality. This can help expand the visibility and control of the plant’s operations and enable the business to better understand and predict orders, address inventory needs and develop more realistic financial forecasts.
So, now for the million-dollar question: How can data feeds be unified in a cost-effective way?

Putting a cap on the capital needed to unify data feeds
Many manufacturers may be wary of making a major purchase that might fail to deliver. But advanced technical innovations have driven down the costs associated with these solutions, without the need for an extensive or expensive IT burden.
That’s good news given the complexity is one thing that hasn’t changed. Industrial environments have a wide range of devices, vendors, network protocols and time series datasets that grow rapidly over time. This has driven the need for that information to be available to users in a self-service model.
As such, industrial data operations is a growing category of data management designed to address the agility required to manage industrial data at scale and rapidly deploy new data applications. What this means practically is that in many cases, instead of processing data on external servers, data is being processed at the “industrial edge” — close to where it is generated near the plant floor itself. Custom solutions that work at the edge can be built quickly and easily and don’t require heavy investment.
This new approach is a cost-effective way to break down data silos, improve data quality and glean better insights for critical decision making. These platforms simplify complex industrial data by making it easier to access from various sources, understand the context and use it in various applications and analytics that can drive operational value.
For plants that have already begun this journey of data contextualization and process optimization, what have they achieved?
Removing pain points
The biggest pain points that have been alleviated are in four key areas: assets, production, workforce and data analytics.
- Assets: From maintenance to inventory management, use to energy efficiency, plants are dealing with a number of asset-level pain points. Some are financial — rising energy costs and high life cycle and maintenance costs and others are operational — inadequate planning, lack of inventory, unplanned down time due to machine failures and poor tracking. Automation and software integration have helped solve a number of these issues, including lowering energy usage and associated cost savings, optimizing resources and alleviating capacity constraints, streamlining operations and reducing unplanned downtime.
- Production: Plants are dealing with several production priorities, including improving throughput and quality control, while also reducing waste, which can impact the overall bottom line. Integrating software and automation can help ensure steady production output, enhance product quality by reducing error rates in production, improve uniform quality across production batches and scale operations efficiently.
- Workforce: Labor shortages continue to impact plant operations and many of the issues plants face around workforce are closely linked — poor training and unsafe work sites lead to unsatisfied workers, high turnover and workforce shortages that hinder production. With automation, plants can invest in quality training programs for skills enhancements, provide a safe workplace with improved morale, address workforce shortages so that operations aren’t impacted and ultimately reduce turnover.
- Data analytics: One of the most significant areas of improvement is the ability to bring data out of the silos, speed decision making and improve predictive maintenance and data security. Automation has helped plants make more accurate decisions based on current insights through real-time data access, identify problems in the plant before they lead to major disruptions, bring together data sources for cohesive insights and build secure infrastructure to withstand cyber threats.
We’ve come a long way from the old network protocols. Today, manufacturers have the opportunity to make industry 4.0 a reality by capitalizing on technology innovations that can help them achieve their goals. With a focus on the continuous improvement of these integrations, industrial manufacturers can also ensure their business is prepared for the digital future and the integration of more capabilities in the years to come.