Direct-drive servomotors are becoming more common as range and availability expands for use in many machine and motor applications.
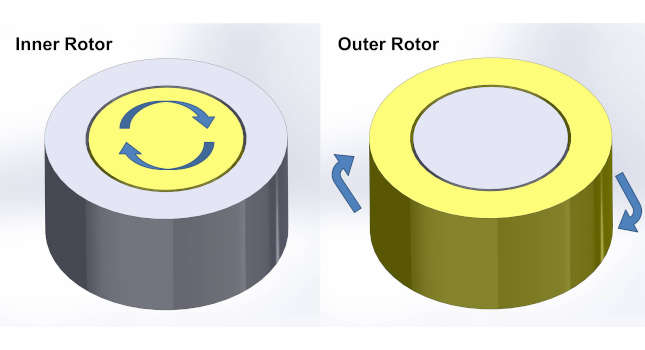
In the world of industrial automation, direct-drive motors and gear servomotors are frequently quoted against one another for similar applications. This overlap often causes confusion about which motor type is best suited for a particular axis. As direct-drive servomotors become more common, with a wider range of sizes and features, direct-drive servomotors are finding homes in more applications.
Defining characteristics of direct-drive servomotors
A direct-drive servomotor is designed to accommodate the load mounted directly to the rotating flange of the motor. To accomplish this, the motors are designed with large, high-capacity bearings designed to carry the load without using additional support or bearings. Directly coupling the load to the motor also eliminates the backlash and torsional flex that can negatively impact the performance of a traditional rotary servomotor and gearbox combination.
This simplified mechanical design, seen in Figure 1, lends itself to space-constrained situations such as robotic arms or a 4th or 5th axis on a computer numerical control (CNC) or additive manufacturing machine, where the space savings can reduce overall size and mass, improving system performance and reducing cost.
Most rotary servomotors are capable of much higher speeds than most applications require, but they often lack sufficient torque. As a result, gearboxes or timing belts are used to convert the excess speed capacity into usable torque and to reduce the reflected inertia to improve tuning. Instead, the direct-drive design uses a much higher pole count within the motor and windings optimized to provide high torque at lower speeds, similar to the torques and speeds exhibited by a highly-geared servomotor. Since the gearbox is eliminated, backlash is eliminated and efficiency is improved.
Match reflected inertia to motor inertia
Matching the reflected inertia to the motor’s inertia is important in increasing the frequency response of the system. A poorly-matched system cannot be tuned for optimal performance and may, in extreme cases, oscillate or become unstable. While a gearbox reduces the reflected inertia in a geared rotary servomotor system by the square of the gear ratio, direct-drive servomotors must handle the full inertial load without mechanical assistance.
Direct-drive servomotors use a two-pronged approach for improving frequency response: increased rotor inertia, and high mechanical stiffness. The high mass and large diameter of the rotor provide sufficient inertia to damp disturbances at the load, reducing settling times, and improving system performance. On the other hand, the high mechanical stiffness associated with coupling the load to the rotor flange reduces the potential for stored energy, which can lead to oscillations and instability upon release.
Faster settling, fewer load disturbances
When properly sized, a direct-drive servomotor can offer better tuning performance with faster settling and increased resistance to load disturbances than a comparable geared servomotor. This reduction in backlash, high torque, and excellent inertia handling are reasons that direct-drive motors have become commonplace in indexing table applications, where the rapid and repeatable movement of a large load is critical.
The large rotor and bearings provide another benefit as well; shifting the mass outward opens up the center of the motor, leaving a large hollow bore. This hollow bore that gives the direct-drive motor its signature shape can be used to pass through cables and plumbing to equipment located at the load. The hollow bore is critically important in many robotic applications, where peripheral cables on the arm are passed through the center of the motor to reduce cable strain.
Types of direct-drive servomotors
Three basic designs of direct-drive motors are: coreless with an inner rotor, iron core with an inner rotor and iron core with an outer rotor. Each offers an inherent advantage towards common industrial automation applications.
The first distinguishing feature among these motor types is whether or not the direct-drive motor has an inner rotor or an outer rotor; this refers to whether or not the rotor is inside the stator or outside of the stator. Outer rotor motors are well-suited for applications with high load inertia, as the larger radius of the outer rotor increases the rotor inertia. On the other hand, inner rotor motors have lower rotor inertia, and are best suited to applications with low load inertia and where high acceleration is required.
The other common difference is whether or not the motor uses an iron core in the stator windings. The iron core is used to concentrate the magnetic flux from the stator windings and align it with the magnets in the rotor. The coreless direct-drive motor design foregoes the iron core, which reduces the magnetic efficiency, but also eliminates the cogging forces caused by the magnets passing by the iron core. The coreless design is used in semiconductor and coating equipment applications where the load inertia is typically small and the smoothest motion is required. While the iron-core motors are not quite as smooth, the difference is minimal, and the iron-core design offers the benefit of improved torque density.
Direct-drive servomotors offer similar torque and speed characteristics to geared servomotors; however, the direct-drive motor’s design advantages make it the clear choice for many applications. Industrial automation applications such as semiconductor handling and machine tools benefit from the small size and low mechanical complexity of the direct-drive motor, whereas end-of-arm robot and additive manufacturing applications often take advantage of the direct-drive servo’s hollow bore for routing of cables and pneumatics. Furthermore, the exceptional inertia handling of a direct-drive motor excels at moving large inertial loads, such as those seen on an indexing table, improving performance and return on investment (ROI) versus an equivalent gear motor.
Direct-drive servomotors can be applied nearly anywhere a geared rotary servomotor is used, and the added direct-drive servomotor benefits of smaller size, higher efficiency, improved tuning performance and easy integration may provide design advantages.
Bryan Knight is product marketing manager, Yaskawa America; Dakota Miller is automation product specialist, Yaskawa America. Edited by Chris Vavra, web content manager, Control Engineering, CFE Media and Technology, [email protected].
MORE INSIGHTS
Keywords: direct-drive motors, servomotors
ONLINE
Read this article online at www.controleng.com for links to parts 1 and 2 of this series.
CONSIDER THIS
What applications on your plant floor would benefit from direct-drive servomotors?