Develop and implement a holistic automation technology stack
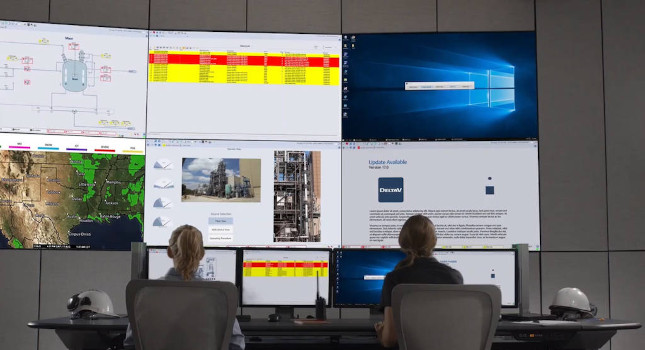
Control system insights
- Process manufacturers are making automation decisions with an enterprise information technology (IT) mindset, moving away from a collection of local systems to a single system that is deployed everywhere.
- Making the IT/OT convergence efficient, effective, affordable and sustainable requires a more holistic automation strategy using a more integrated platform.
For decades, selection of plant control and reliability technologies was frequently a matter of convenience. Individual plants across an organization selected technology based on price and local technical preference, often resulting in a wide variety of technologies across the enterprise. At the time, such decisions were convenient, reliable, and cost-effective. However, new, modern technologies — coupled with the need for increased sustainability and market agility — have changed the paradigm, driving a shift in the way engineers design automation solutions.
As the many layers of the Purdue model of industrial engineering have flattened in the cloud and edge computing age, connectivity has become more important. Today, forward-thinking process manufacturers are making automation decisions with an enterprise IT mindset, moving away from a collection of local systems to a single system that is deployed everywhere. In doing so, they unlock the capacity for improved data democratization, fleet optimization, and improved personnel productivity.
Change at the IT/OT convergence
Over the many decades that modern automation has evolved, it was typically seen as a tool to optimize a plant or single unit. As a result, each plant created its own operational technology (OT) staff, making their own decisions, leading to systems that were isolated and siloed. Historically, automation components were also isolated in their own exclusive networks through many layers of firewalls, making the data they contained hard to reach, often as a result of a defense-in-depth security strategy.
As these OT networks were being built, information technology (IT) began to morph, transitioning from disparate groups connecting individual technologies into a corporate role. This new IT structure was focused on connectivity of all systems across the enterprise into a seamless whole.
As an example, consider printing. In the not-too-distant past, each office in an enterprise had its own printing strategy. Moving from building to building meant installing new printer drivers to allow access to local equipment. Over time, however, IT developed enterprise printing, where a single print driver allowed users to access any printer in any building, removing the need to configure printers when moving among offices. The same story can be repeated for most modern IT technologies: finance systems, enterprise resource planning systems, cloud-based collaboration tools, and more.
This same evolution has been slower to launch in OT. While some technologies, such as plant historians, have moved from individual installations and instances to a more shared enterprise structure, much of the technology needed to unlock enterprise optimization is still siloed in individual plants.
But access to new technologies is generating a change. Many of the same IT systems that have operated at the enterprise level for years are becoming available in the OT space to drive better visibility, use of resources, and performance. Moreover, OT technologies are being designed with more modern IT interfaces, rather than legacy protocols defined thirty years ago. New standards—such as decoupling of I/O and control, along with better human machine interfaces via HTML5 and MQTT—are making it easier to integrate data models, analytics, and displays to access applications living in the enterprise. As a result, today’s teams are trying to converge, collect, and integrate a wide variety of OT systems into enterprise IT infrastructure.
The key solution many engineers are using is standalone edge gateways, creating a patchwork of connectivity between OT equipment and IT systems. These one-off solutions better integrate today’s technologies, but making the IT/OT convergence efficient, effective, affordable and sustainable requires a more holistic automation strategy using a more integrated platform.
A holistic vision at the OT edge
To better understand where enterprise OT can go, it helps to look at another example of success from enterprise IT. As corporations grow, they acquire different businesses of varying sizes, often running different financial systems. When bringing these new businesses into the fold, enterprise IT could create a series of translators to bring financial data from different systems into an enterprise view.
However, this is rarely, if ever, the path organizations choose. Instead, IT implements an enterprise product and slowly starts moving all satellite locations onto that platform. The result is better standardization, optimization, and ease of use. Legacy financial applications may continue to be used in the short term, but ultimately, everyone is rolled into the enterprise package.
To drive a more holistic, enterprise automation architecture, OT’s legacy solutions should be viewed in much the same way. Building an edge infrastructure brings data together but does not fundamentally solve the problem of local disparities due to legacy technology use in each plant. Instead, thinking about automation systems on an enterprise level—the same way IT teams view solutions like Oracle and SAP—unlocks more value by creating a single, standardized automation platform across the whole corporation (See figure 1).
When teams consider a common, holistic automation platform, they begin to see that automation components are simply nodes on the IT infrastructure, bringing IT and OT together and blurring the walls between them. The nodes on this network—programmable logic controllers, communication gateways, wireless gateways, reliability and prevention tools, and even the distributed control system—create a broader network of systems OT can use to improve outcomes by integrating, analyzing, running models, and performing other actions.
Implementing this type of holistic automation platform requires the creation of a more software-defined infrastructure. Such a design allows the automation system to handle data more efficiently so it can grow into an enterprise operations platform that will also perform control functions. Technologies such as wireless communication, advanced physical layer, software-defined controllers, OPC UA data integration, module type package, and edge gateways enable teams to create expansible enterprise systems covering more plants, all while implementing uniformity and standardization that acts as a foundation for success in the future.
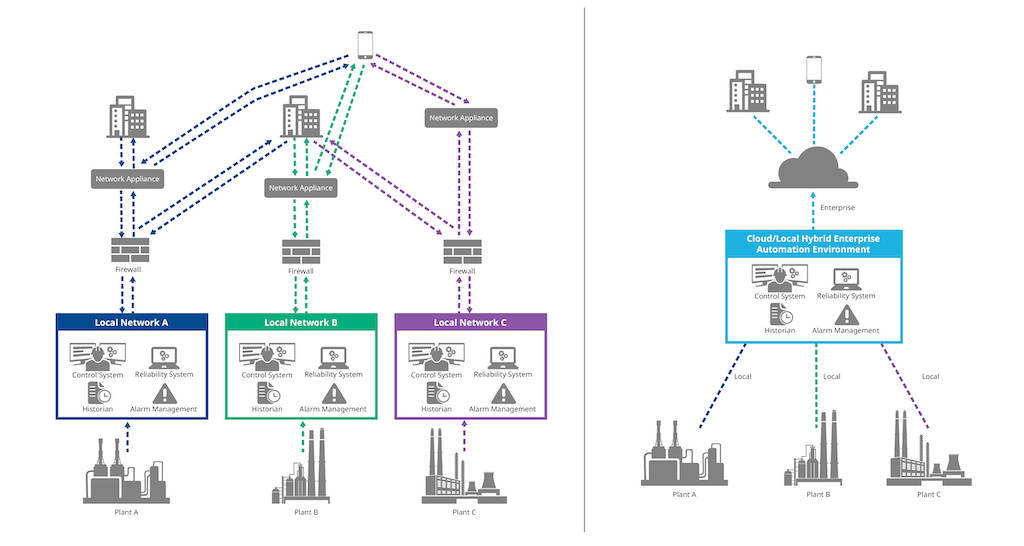
Democratizing data drives innovation
One of the primary benefits of a more holistic approach to automation is data democratization. In many cases, the addition of digital technologies into plant strategies creates “efficiency silos.” For example, as many plants move from collecting asset health data via manual rounds to automated continuous condition monitoring, they run the risk of isolating the plant’s health data from the enterprise. This gives the plant the ability to tune processes and improve performance locally, but often limits better enterprise visibility, creating a roadblock to enterprise-wide initiatives, such as improved overall sustainability and standardization, along with efficiency gains across the fleet.
Better gains and faster return on investment come when those same systems are implemented with the enterprise in mind. This can start with a step as simple as selecting a data service architecture that takes advantage of contemporary IT connectors such as MQTT, making it easier to drive local reliability data to an enterprise level. These systems are further enhanced when they are part of an integrated automation solution, such as a control system that contextualizes the data. Further gains are realized by using an integrated analytics platform that can analyze, sort, and store the data with rich metadata in a common location, such as a data lake.
When the connectors, data servers, and protocols of an automation system are designed to work together, they not only democratize access to data, but also context and knowledge, making it easier to combine information in a way that makes sense to end users. In such a scenario, the right information is always available to the right people hassle-free, enabling personnel with the right credentials to easily and securely access data for fostering insights. This flexibility of data access empowers cross-functional teams to innovate more effectively by tapping plant data to identify early indicators to downtime and other threats to production, while more easily achieving corporate performance and sustainability goals.
Influences for fleet optimization
The same digital transformation that optimizes operations locally also tends to drive a need to think about automation at an enterprise level. When reliability, maintenance, and operations teams focus on a single asset, they only have a few levers to pull to effect change. These types of improvements are important, but big-ticket efficiency gains are difficult to make at the local level. In contrast, teams looking at multiple assets installed in different plants gain many additional ways to optimize enterprise-wide key performance indicators, such as energy efficiency, output, and throughput.
For example, consider a chemical processing facility. Operations in the facility typically have feedstocks and product moving from process unit to process unit. Perhaps the team has implemented advanced process control on individual units, and production, efficiency, and sustainable operations are optimized in each one. The units operate well, but are still siloed from one another, particularly if there is no commonality among automation systems in each unit.
In contrast, a highly-integrated, holistic control architecture empowers the chemical manufacturer to combine those well-performing units and evaluate the process orchestration. By combining the advanced process control on individual units into an overarching control strategy, teams can drive the best throughput from the whole facility at all exit points.
Optimizing and empowering talent
Even in a facility not driving toward an enterprise strategy, a uniform automation technology stack still has great value. Today’s plants are running with fewer expert staff than ever before. A process manufacturer may have only a few experts in certain areas because it is too expensive to have this level of talent in every facility.
For many plants, the solution is to raise the mean skill of the average operator. This is a difficult task when operators are required to learn a variety of different control system interfaces, mobile technologies, and automation architectures. A more standardized technology stack provides a unified approach that streamlines decision making. When every plant operates just like all the others, any operator can function at their best, regardless of location.
But when process manufacturers apply a holistic approach to automation, the benefits multiply. Enterprise historians and the ability to move contextualized data out of plants and into data lakes enables teams to move automation optimization from a localized function to an enterprise-wide integrated operations vision. Process manufacturers can operate a central team of experts that monitors every plant across the fleet at an enterprise level. Instead of needing a hard-to-find and hard-to-retain expert at each site, local technicians are supported by global experts with full visibility to plant operations in real-time (See figure 2).
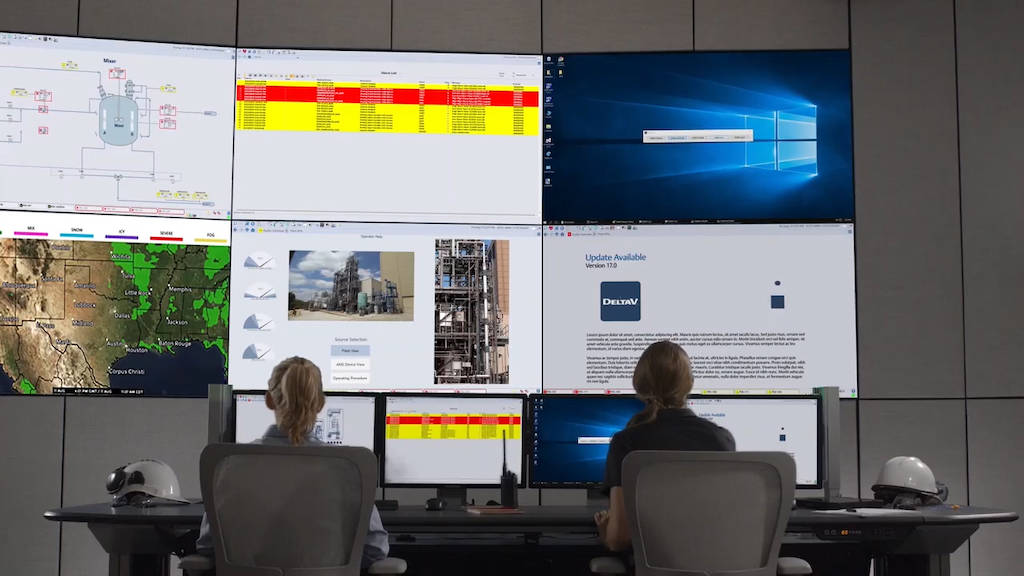
Making the shift to a holistic strategy
Moving from local, plant centric automation technology strategies to an overarching mission focused on OT/IT convergence is not a project that happens overnight. Establishing such a project and selling it to management requires planning. Modernization teams need a roadmap clearly laying out where they want to go and showing how they will standardize technology as they invest in nodes or systems that aren’t automated today and need to be. They will also need to determine the layers that must overlay existing systems to enable easier integration—finding ways to collect data and drive it to a more IT-friendly architecture.
Fortunately, the strategy itself comes with a built-in support structure. The most forward-thinking automation suppliers are creating a more software-defined infrastructure that allows the control system to handle data more efficiently. This type of infrastructure empowers modernization teams to grow their solutions from local control systems into enterprise operations platforms.
Some technologies, such as real-time control, will be best deployed locally. Others will work best at the industrial edge, and still others will fit best in the cloud, depending on a plant’s individual OT/IT strategy. Partnering with automation experts who can help define those technologies and their most successful architectures will help process manufacturers expand their reach to develop holistic solutions.