Addressing manufacturing use cases that deal with unstructured inputs.
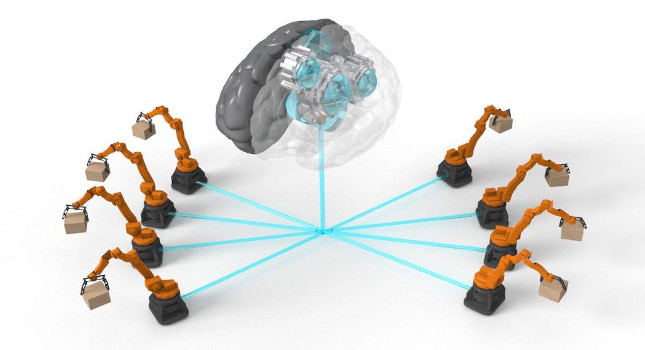
Factories around the world have long been incredible displays of engineering and operational capability, often on the cutting edge of technology. Yet today’s factories, new and old, face challenges in adapting traditional systems and processes to modern technology trends and increasingly difficult applications.
Driven by technology advances, the manufacturing industry is transforming, as identified by four emerging trends: machines as connected fleets; machines handling unstructured inputs; incorporation of AI and machine learning; and companies inviting the customer into the manufacturing process.
Machines as connected fleets
Machines on the factory floor are more connected than ever, leveraging Industry 4.0 philosophies and communication protocols to stream data for central visualization and analysis, and to enable facilities and equipment providers to monitor and support systems.
Yet equipment in factories are still relatively isolated from the broader network of equipment worldwide, and often even isolated from other facilities within the same company. There are many valid reasons for this, including security and intellectual property, but also many detriments that have become the norm for decades in manufacturing.
From a machine or component suppliers’ point of view, there are significant global install bases of the same equipment. Some machines perform the exact same task, like sealing a cardboard box, while others vary widely, as is the case with more flexible systems, like industrial robots. But these systems are by and large disconnected due to customer isolation.
There are industry-changing benefits when this global install base is viewed as a connected “fleet” of systems that can be leveraged for continuous improvement, feature enhancement, and more.
For an analogy, consider Tesla, the innovative electric car manufacturer. Aside from its car and battery technology, Tesla changed the game in the automotive industry by deploying a connected fleet strategy with their vehicles, and by breaking the mold of rigid software release cycles. Tesla’s have now become systems that are constantly improving, receiving over-the-air software updates to improve performance, and adding new functionality regularly. Many of these new capabilities are only possible due to the global fleet of systems that are constantly gathering data to help Tesla pinpoint the right features to build.
The safety and quality culture in the automotive industry resisted this sort of approach for many years, yet the benefits and results are undeniable, as seen in so many other industries. In manufacturing, a similar status quo is present, with risk-averse facilities hyper-focused on production yields and costs, stuck in the traditional release cycle of equipment and software.
Compelling paradigm shift
But the potential transformation in manufacturing that follows from the connected fleets paradigm is compelling.
Equipment manufacturers can become more competitive and increase profits by allowing customers to opt-in to their connected fleet, lowering the barrier of remote support, maintenance monitoring, and software updates, while opening monetization opportunities with new features.
Companies operating facilities will get more out of their investment in equipment, which won’t be stuck in feature stasis, but rather constantly improving as the fleet improves and new features become available.
Imagine a valve manufacturer develops a software update that decreases air consumption by 3% for a particular valve bank; or a robot manufacturer improves the Power ON time by 2 seconds after an E-Stop; or a sensor manufacturer improves the response time logic on a sensor amplifier by a few milliseconds.
Imagine a metal detector manufacturer updates their HMI to optimize setup times based on A&B testing within the fleet; or a software update on a case packer machine increases performance by 10% based on learning’s from a major installation in Spain; or an assembly work cell supplier preemptively sends new consumable components based on fleet data.
These are common improvements, that equipment and component manufacturers are constantly making to remain competitive, yet they are typically only released on new equipment. As the industry moves toward connected fleets of systems, these sorts of enhancements will be realizable in more and more factories, a trend that has the potential to fundamentally modernize the manufacturing industry.
Getting better at unstructured inputs
Factories are traditionally some of the most well organized and structured settings in the world. With costs and yields paramount, structured inputs have been historically the key to optimize the performance of automated machines.
But many manufacturing use cases aren’t so lucky and must deal with unstructured inputs. Think of anything from the natural world – fruits and vegetables, for instance – or machines that deal with anything of varying size and shape, like recycling trash or handling soft goods. Building a facility with automation that can deal with unstructured inputs while maintaining efficiencies is an extremely difficult thing to do.
Many of these applications have been solved with humans in the past, but with advancements in new technologies in robotics and computer vision, an increasing number of less structured manufacturing use cases are now cost effective with a combination of humans and automation.
Semi-automated stations that leverage humans for their inherent strengths and layer automation and software for their strengths is an increasingly common strategy. Collaborative robots and other sensor-assisted processes are effective solutions for many use cases. These stations are also excellent sources of data to help make data-driven decisions when considering adding additional automation in the future.
“Rules-based” computer vision approaches are the norm in automation for inspection or pick and place systems, yet these systems are fragile when dealt a highly variable input. Machine learning-based vision systems are a critical technology needed to robustly handle variable inputs and guide automation.
Additionally, facilities that deal with unstructured input must maintain a flexible manufacturing floor and leverage data to make predictive or real-time optimization decisions. In other words, they must be flexible enough to know what kind of content is coming through their supply chain or facility, plan accordingly, route that content appropriately, and then process it as efficiently as possible.
AI and machine learning
Most industries are just starting to scratch the surface when it comes to AI and machine learning (ML), and manufacturing is no exception.
Factories and equipment manufacturers around the world have more data than ever before, and as more and more machines get connected, turning this data into actionable insights is critical to remain competitive. But with so much data available, and overwhelming hype around AI, choosing the right applications is key.
Vision inspection is a great example of an area where ML is already making a major impact in manufacturing facilities. As discussed above, “rules-based” vision approaches are time consuming to build and fragile when trying to look for anything unstructured. Defects on a structured part or ideal pick locations on a fruit, are examples of historically challenging use cases. However, the ability for ML models to be trained on hundreds or thousands of examples of simply what “good” and “bad” look like, or where the center of a blob is, and then create a robust model that analyzes features no human would ever train as a “rule,” is transformative. Many manufacturing facilities are already creating this labelled training data on existing systems that have cameras, it just needs to be stored and leveraged appropriately.
Considering the trend towards fleets of systems and more frequent software updates being available, factories that align with technology providers that are globally collecting data and improving vision models for common part types and use cases, will gain a strategic advantage over companies that rely on isolated vision tools. Of course, for customized use cases this may not apply, but for many common use cases, like food product inspection, why reinvent the wheel?
Big data use cases are on the rise under the Industry 4.0 banner, which certainly open exciting opportunities for AI and ML. The increasing availability of historical and real-time production, machine, and supply-chain data is the key to unlock future insights using ML.
Whether it’s deep learning-based vision systems, predictive maintenance, or automated supply chain decisions, AI will continue to transform manufacturing as we know it, enabling companies and manufacturers to enhance performance, decrease costs, and drive profits.
Inviting customers into the manufacturing process
In this future state, with connected fleets of rapidly improving machines in distributed manufacturing facilities across the world, where does the end customer come in? What visibility does the customer have into the process? Today, not much. But in the future, with increased personalization of products and customer demand for real-time updates, manufacturers should look to take advantage of their process and data to engage with customers.
Understandably, consumer applications are already heavily engaged with customer’s providing real-time update dashboards for orders or tracking information on where a delivery is in real-time. But for an average end-customer, they will have little to no idea where or how a manufactured product was made. Other than the “Made in ____” line on the product or potentially episodes of “How It’s Made,” consumers aren’t exposed to the incredible supply-chain of people, machines, and factories that it takes to produce the products we use every day.
Inviting customers into this process, will increase engagement and visibility of all the work necessary by manufacturing companies to deliver products, which will in turn lead to better awareness and customer loyalty.
These are just a few of the exciting trends to look out for as manufacturing continues to evolve with technology.