Learn from the experts about energy efficiency in compressed air systems
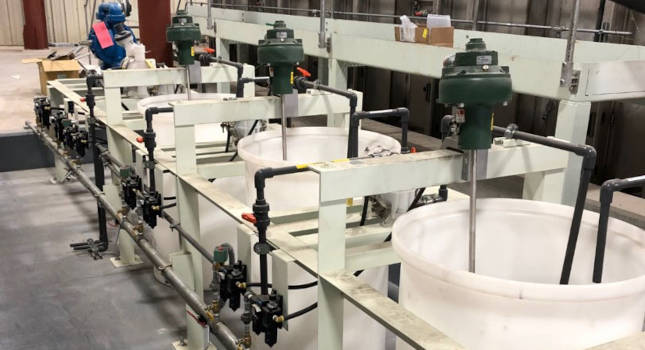
Compressed air insights
- Compressed air leaks are not only a direct source of wasted energy, they also can contribute to system pressure drops, making pneumatic equipment function less efficiently and shortening its life cycle.
- Air leaks cause equipment to cycle more frequently, thereby increasing the running time of the air compressors, which leads to additional maintenance requirements and possible increased unscheduled downtime.
There are many factors affecting the bottom line of a facility. A leak or inefficiency in a compressed air system may spell higher costs. In this expert Q&A, learn more from the presenters of the June 15, 2023, webcast about compressed air.
Experts:
- Tom Taranto, Principal Engineer and Owner, Data Power Services LLC, Baldwinsville, New York
- Eric Bessey, President, TTed Solutions, Beaverton, Oregon
Question: How effective are central controllers?
Eric Bessey: Central master control systems can be an effective and efficient way to manage the operations of compressed air supply equipment and minimize operating costs. The effectiveness of master control systems depends heavily on proper installation and commissioning, plant staff understanding of the system, and periodic tuning to sustain system efficiency.
Question: Where should dryers and storage tanks be located with respect to each other?
Tom Taranto: The location of air receiver tanks depends on the purpose of the receiver and nature of system air demand. For example, to dampen out pressure fluctuations that might impact the compressor controls, a receiver is best located at the compressor discharge, upstream of treatment equipment (air dryers and filters), often called a “wet” receiver. Also, if a wet receiver will be used to collect liquid water and/or oil that might be present in the flow stream, it is common to have the air flow through the receiver tank, entering through a lower pipe connection and exiting higher up on the tank.
Having only a wet receiver is appropriate if there are no big air demand events that would cause the airflow to exceed the air dryer capacity. For example, a 500-cubic feet per minute (cfm) compressor can do quite nicely with at 1500-to-2500-gallon wet receiver (providing 3 to 5 gallons of storage per cfm). However, suppose there are demand events that will require 1200 cfm flow rate for 20 seconds. The system would flow 500 cfm from the compressor and an additional 700 cfm from the air receiver. If it is a wet receiver, an air dryer of 1200 cfm capacity would be required. Suppose it is a 2,500-gallon air receiver (334 cubic feet). When it is supplying 700 cfm flow rate, the air pressure in the tank would be dropping by 30 psi per minute during the 20 seconds, tank pressure would fall by about 10 psi.
To eliminate the problem of surge flow through the air dryer, suppose the system has a 500-gallon (66.8 cubic feet) wet tank and a 2000-gallon (267.2 cubic feet) dry tank. With pressure falling at a rate of 30 psi per minute the airflow from the 500-gallon tank is 138 cfm and the airflow from the 2000-gallon tank is 553 cfm. Air flow through the dryer is 638 cfm (500 + 138). Plus 553 cfm from dry storage gives a system flow rate of 1191 cfm. The air dryer would need to be sized for 700 cfm rather than 1200 cfm using only wet storage.
Generally, in most systems both wet and dry storage are advisable, and by keeping 20% to 25% of the volume as wet storage, and 75% to 80% as dry storage the air treatment equipment does not have to be sized for the full air demand at the system’s peak flow rate.
Question: Can you provide some retrofit options to different types of air compressors to optimize energy consumption, for example, preheating of intake air, retrofitting variable speed drives (VSDs) on compressors, etc.?
Tom Taranto: Generally, it is desirable to have intake air come from the cleanest, driest, and coolest air that can be supplied. Excessively cold intake air is also not desirable. Even then compressor efficiency improvement is minimal.
Retrofitting VSDs to an existing fixed-speed compressor is possible and will improve efficiency at part load operation. However, every rotary screw compression element is designed to operate through a defined speed range. The manufacturer should be consulted to determine the correct speed range. Too slow and volumetric efficiency it too low and there may be excessive heat generated by the screw element. Too fast and there can be damage to the compressor’s bearings. Also, the compressors standard fixed-speed motor may have to be replaced with a motor capable of a VSD. For these reasons, retrofit of a VSD on an existing fixed-speed compressor is not commonly done.
Question: What do I do about leaks at air regulators?
Eric Bessey: If it has been verified that there is a leak at a regulator (as opposed to the standard air bleed function), there are essentially two options to eliminate the leak: 1) repair the regulator with a repair kit if available, 2) replace the regulator.
Question: How should you calculate compressed air leaks in open circuit? How can you detect small leaks?
Eric Bessey: There are several ways to determine the total leak load of a system and how much these leaks cost in terms of energy. One way is to measure the total electrical load on the compressors when the plant is down (i.e., a nonproduction period). Airflow supplied by each compressor can determined according to each compressor’s part-load performance curve. Another way is to conduct a system bleed-down test where all compressors are shut off or unloaded when the system is fully pressurized and measuring the time it takes for the system to bleed down know amount. Leaks can then be located either by listening or using a leak detector.
Question: Have seen Bosch regulators by design constantly blow off air resulting in artificial demand. Simple fix: buy a different regulator.
Tom Taranto: Yes, it is true that some regulators bleed a small amount of air by design. These are often referred to as a precision regulator. There is a good post from June 11, 2018, on fluidpowerjournal.com “Understanding the Characteristics of Pressure Regulators.”
It describes precision regulators as follows. “Precision: Standard-grade regulators will maintain the control pressure within two to five psi during normal operation as the air flow demand varies. A precision regulator will maintain the pressure with variations of less than 0.5 psi. The precision regulator will constantly bleed off a small amount of air to keep the flow valve open and active. It also ensures that any back pressure is bled off immediately instead of having to increase the pressure above the setting to open the vent of a relieving style regulator. The precision regulator would be used in applications where the need for extreme pressure accuracy, such as a tension control for a paper roller, outweighs the cost of a small continuous air bleed.”
Before replacing a precision regulator with a standard nonbleeding style unit, consider your application’s need for the performance offered by precision regulators. The bleed flow is very low, typically 5 scf / hour. If you do not require the performance offered, replacing the regulator is a simple fix.
Question: VSD is great for control capacity. But what about maintenance concerns?
Eric Bessey: Great care must be taken when considering VSDs for use on air compressors. Drives must be installed in suitable locations where conditions are clean and not subjected to excessive heat.
Question: How can I improve compressor efficiency?
Tom Taranto: It is difficult to improve the efficiency of an existing compressor. Many design factors ultimately determine the overall compressor efficiency. Also, the thermodynamics of compression indicates that most of the input energy to an air compressor is required to overcome the heat of compression.
Total compressed air system efficiency depends much more on maintaining a good supply/demand balance and using the most efficient trim compressor that is available. Also, implementing a control strategy that will shut air compressors off when their capacity is not needed has a great impact on operating efficiency.
Question: How large of discharge piping in a header system do you consider for storage capacity?
Tom Taranto: As a general rule, compressed air pipeline velocity should be designed for 20 to 20 feet per second at the peak flow rate required by the system.
Question: Can we connect/control an air compressor to an EMC DDC system?
Eric Bessey: Air compressors as well as other compressed air equipment can often be viewed by a plant building management system/supervisory control and data acquisition (BMS/SCADA) system. Compressors must make data available to such a system. Many compressors have communications protocols available for monitoring and/or control.
Question: Why do we need to provide a refrigeration-type air dryer in a compressor system?
Tom Taranto: The first concern for eliminating water from the compressed air is to have a good effective aftercooler, and 65% to 80% of the water vapor that enters the air compressor is typically removed by the aftercooler, whether air cooled or water cooled.
For example, a 500-cfm compressor operating with a 90-degree F inlet temperature and 75% relative humidity has 138 gallons per day of water vapor entering the compressor intake. With a 15-degree F approach aftercooler and 100-degree F air through the radiator, it will remove 89 gallons per day of condensate.
From that point, a refrigerated air dryer delivering a 38-degree F pressure dew point will remove an additional 46 gallons of condensate per day. NOTE that the dryer performance must be corrected for the 115-degree F inlet temperature that it will experience at the job site. A refrigerated air dryer’s standard catalog performance is rated for a 100-degree F maximum inlet temperature.
If the compressed air lines are not exposed to temperatures less than 38 degrees F, there will be no additional condensation of water vapor to liquid water in the system.
Question: How do we calculate and design to determine the air compressor required cfm?
Tom Taranto: Working on a greenfield project without any similar comparative information for compressed air demand in a similar production process can be very tedious and difficult to determine the system’s normal air demand.
A mistake that is often made is calculating air demand without considering the frequency of use for various pneumatic tools and machinery. For example, a metalworking shop plans to have 10 compressed air-powered grinders that consume 22 cfm each. If all the grinders operate simultaneously, that is 220 cfm, requiring the capacity of a 50 hp air compressor. However, consider that each grinder only consumes air when the operator is actually pressing the tool’s trigger button. It is uncommon for all grinders to operate continually for hours at a time. In fact, it is common to observe that grinders may operate at most for 20 or 30 seconds out of a minute. Operators also have other work responsibilities that do not involve using the grinder.
A group of 10 grinding tools may have a random use diversity factor of 25% or 30% utilization. Therefore, the compressor capacity needed to support all grinders is 55 to 60 cfm, not 220 cfm.
Question: Where is the typical usage of an air compressor in building design?
Tom Taranto: There are three general classifications of compressed air use: to perform work, to control machinery or process equipment, or process applications where the oxygen content of the air is part of a chemical process.
Work is performed by rotating air motors to drive tools such as drills, grinders, jackhammers, etc.
Control functions might operate dampers or other HVAC controls. There may be other pneumatically powered valves, linear, or rotary actuators.
Oxygen in the air may be used as an oxidizer in chemical processes, or perhaps as an oxygen source for fermentation processes. Since air is a mixture of gases with Nitrogen being the major gas present, compressed air can be supplied to Nitrogen generators that concentrate nitrogen for various process uses.
Question: Is there a benefit to a pressure/flow controller if we operate a variable speed drive (VSD) compressor that meets demand and holds a constant pressure at the minimum required pressure?
Tom Taranto: Operating compressor discharge pressure at the system’s minimum required pressure eliminates any pneumatic energy storage. We discussed that pneumatic energy storage is a function of receiver volume and pressure differential between storage pressure and minimum required system pressure. Therefore, a system operating at the required pressure has no usable pneumatic energy in storage. If the VSD is the only compressor in the system, and peak air demand never exceeds the output flow capacity of the compressor, air demand is constantly supplied by the rotating on-line compressor horsepower. Theoretically, the system will operate just fine.
However, if there are multiple compressors in the system, storage is necessary to restart a compressor after a low demand period when the compressor could be shut off. We discussed permissive start-up time for a compressor. During that time, pneumatic energy storage supplies system air demand, allowing the compressor the time it takes to start up and begin compressing air. Similarly, if the system has a reserve compressor that is normally stopped in standby mode, and an operating compressor unexpectedly shuts down, storage is necessary to allow the standby compressor time to start up without interrupting the production process.
Systems with little or no pneumatic energy storage tend to be very unreliable in their ability to support production without frequent interruptions of manufacturing processes.
Question: What is the ballpark kilowatt load per cubic feet per minute (CFM) for a Variable Frequency Drive (VFD) driven screw compressor?
Eric Bessey: Specific efficacy for a rotary screw compressor is typically given as kilowatts (kW) per 100 standard cubic feet per minute (scfm). The specific efficiency of a VFD screw compressor depends on several factors including size, operating discharge pressure, and operating percentage load. A typical range for a lubricant-injected compressor is 15-18 kW per 100 scfm, while that of a lubricant-free compressor is 18-19 kW per 100 scfm. This only refers to the specific efficiency of an electric motor-driven compressor and does not include ancillary equipment such as cooling fans for air-cooled compressors.
Question: From a controls standpoint, is it better to have a fixed-speed unit for baseload and a VFD trim compressor, or is it better to have two VFD compressors?
Eric Bessey: Although there are exceptions from efficiency and operational standpoints, it is typically preferred to base load a fixed-speed compressor and trim with a VFD model. Care must be taken to size the VFD compressor appropriately in comparison to the fixed-speed compressor.
Question: I have old Sullair screw compressors at 400 horsepower (hp). Which curve on your performance curves graph would they follow?
Tom Taranto: Your Sullair compressor would follow one of two control styles, either inlet modulation with unloading, or variable displacement.
The Sullair engineering data sheet from September 1991 described the inlet modulation control as follows.
Capacity modulation range from 100 to 40 percent. Operating pressure can be set from 50 to 125 pounds per square inch gauge (PSIG) with control. The inlet butterfly valve is controlled by a diaphragm and pressure regulator holding constant pressure. Below 40 percent air demand, the machine will unload by use of pressure signal and pneumatic blowdown valve, reducing receiver pressure and minimizing no-load power consumption.
Sullair’s variable displacement control was introduced in 1984, named “Sullair Spiral Valve Technology.” The performance would follow the variable displacement capacity control performance curve.
Question: Should inlet guide vanes always be installed with centrifugal compressors since there is always a chance for partial loading at any given time?
Eric Bessey: Inlet guide vanes (IGVs) offer improved part-load efficiency over butterfly inlet valves within a centrifugal compressor turndown range. IGVs should be considered whenever there is a possibility of prolonged periods of partial loading of a compressor. IGVs must be installed properly with an adequate length of straight pipe from the IGV to the inlet of the compressor.
Question: Can you put a variable frequency drive (VFD) on a centrifugal compressor?
Eric Bessey: VFD retrofits on centrifugal compressors are extremely rare. Unlike positive displacement compressors, the ability for a centrifugal compressor to generate pressure, or “head,” is a function of the square of the rotational speed. Therefore, as the rotational speed is reduced, the ability for the compressor to generate pressure is greatly reduced. This limits the amount speed can be reduced, typically making a VFD cost-prohibitive for retrofitting.
Tom Taranto: Centrifugal compressor performance for volume flow capacity, head or pressure, and power with a change in wheel velocity RPM follows the Fan Affinity Laws. A good explanation can be found on engineeringtoolbox.com “Fan Affinity Laws.”
Question: Can you bring in a third party yearly (or more frequently) to do acoustic monitoring for leakage? Rather than have something you must purchase?
Tom Taranto: Yes, there are service providers who provide leak detection service. They will use leak detection instruments (either ultrasonic or acoustic) to locate and tag compressed air leakages. Some also provide service to repair leaks or act as project managers to coordinate with a contractor to repair leaks.
Before investing in leak detection equipment, I recommend that you consider the availability of in-house personnel to do leak detection surveillance. It is common for plant personnel to have knowledge and skills that are unique to the production process. Even with the best intention to complete leakage surveillance, there are often work orders having a higher priority and leak detection does not get done. Expensive equipment ends up sitting in a maintenance cabinet unused. Having a third party come in once or twice a year is the only way to get the work done.
Question: Have either of you two read “1984”?
Answer: Yes. The Physics Police are an elite, highly specialized unit.