Detecting air and gas leaks can pay dividends.
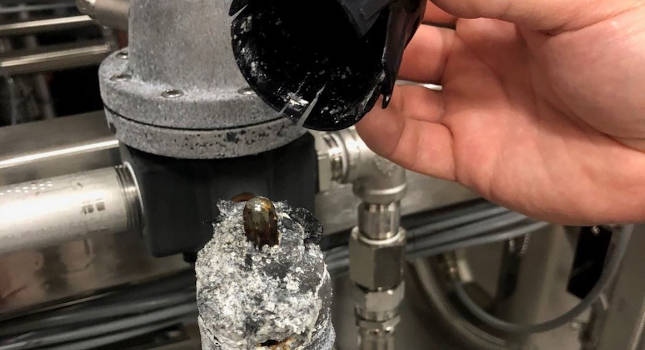
Air and gas — practically every industry in the world uses one or both. They are an integral and critical component to the processes we rely on daily. However, when not contained or used properly can cause damage to equipment, products and people. What kinds of damage? Here are a few examples of air or gas leaking from different systems and what happened.
Compressed gases
Compressed gases can cause fires, explosions and oxygen displacement, which could all be deadly. The risks of toxic gas exposure are known to cause injury to those who have long-term exposure, such as those who work with or in the vicinity of compressed gases. This is why industrial gases are regulated by the U.S. Department of Labor, Occupational Safety and Health Administration (OSHA), including permissible exposure limits (PELs), uses and transportation standards. Many states, including California, have lower PELs than OSHA.
Consider carbon dioxide, which is commonly used for refrigeration, cooling and casting. In this case, a pressure regulator was badly corroded and no longer functioning (see Figure 1). The regulator was connected to equipment that used compressed air, nitrogen and carbon dioxide. Because there were no visible or easily detectable issues with the equipment, the team continued to swap out the damaged pressure regulator for a new one, only to have that one fail shortly after.
Using an acoustic imager that could “hear” leaks beyond human capability, a small carbon dioxide leak was discovered near the pressure regulator. Over time, this type of leak can cause components to break (or corrode), negatively impacting uptime and/or quality. Compressed gas leaks like this are the root cause of many component failures that often go unnoticed.
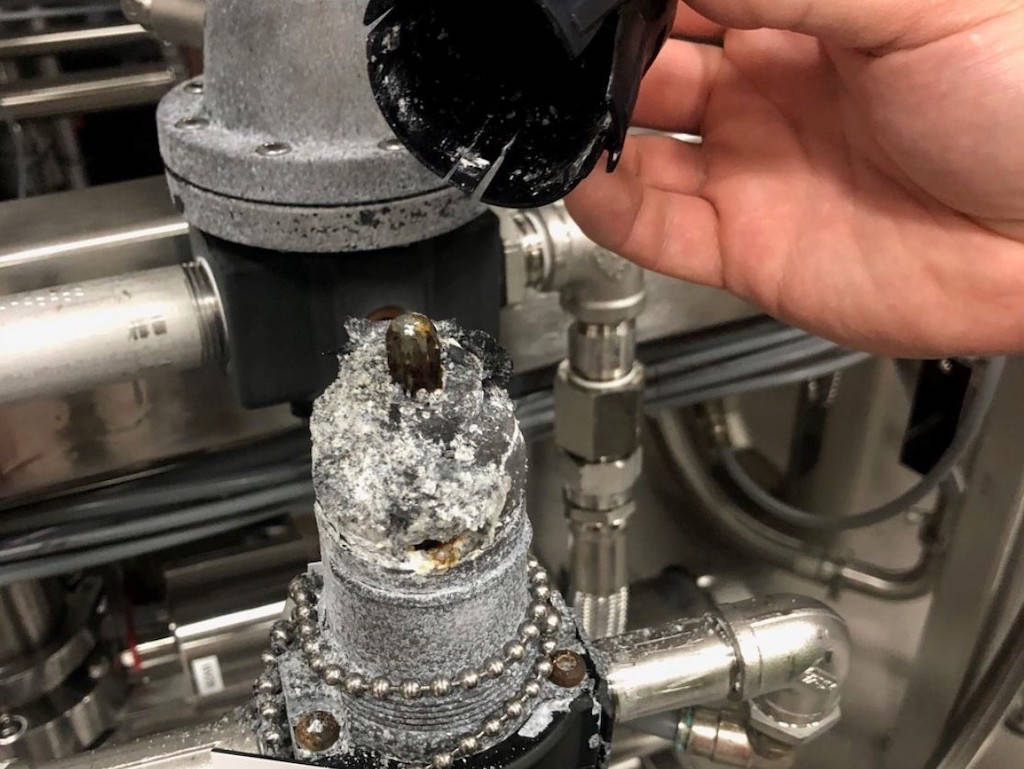
Compressed air
Compressed air lines are at the epicenter of success or failure for many factories. When compressed air lines are maximally intact, the air tools they run also function as expected. But when lines are compromised, the results can be detrimental. Pressure drop, for example, is a phenomenon seen mostly on the demand side of the compressor system, where if the standard cubic feet per minute (SCFM) volume of air isn’t supplied by the compressor, the required operating pounds per square inch (PSI) in the air supply hoses cannot be maintained.
In a large factory, a compressor system can stretch hundreds of feet and sweep in and out through various other operational systems. Issues in a compressed air system can occur anywhere along those lines — including the compressor, air dryer, mainline or pneumatic tools, such as air wrenches, air drills and air sanders. Leaks reduce air flowing through a line, resulting in an inadequate amount of air pressure to properly run equipment.
Consider the example of a pick-and-place robot with pneumatic cups. The robot picks up materials or products from one location and moves it to another location for continued processing. If the suction or actuator is weak, picked parts could drop or not be placed in the right position, impacting product quality (or creating a complete loss). Often, when suction issues are reported, all components are replaced because it is too difficult to isolate the problem. Rather than needing to check each cup independently, the entire robot could be scanned with an acoustic imager to identify exactly which cups need replacing to avoid damage (see Figure 2).
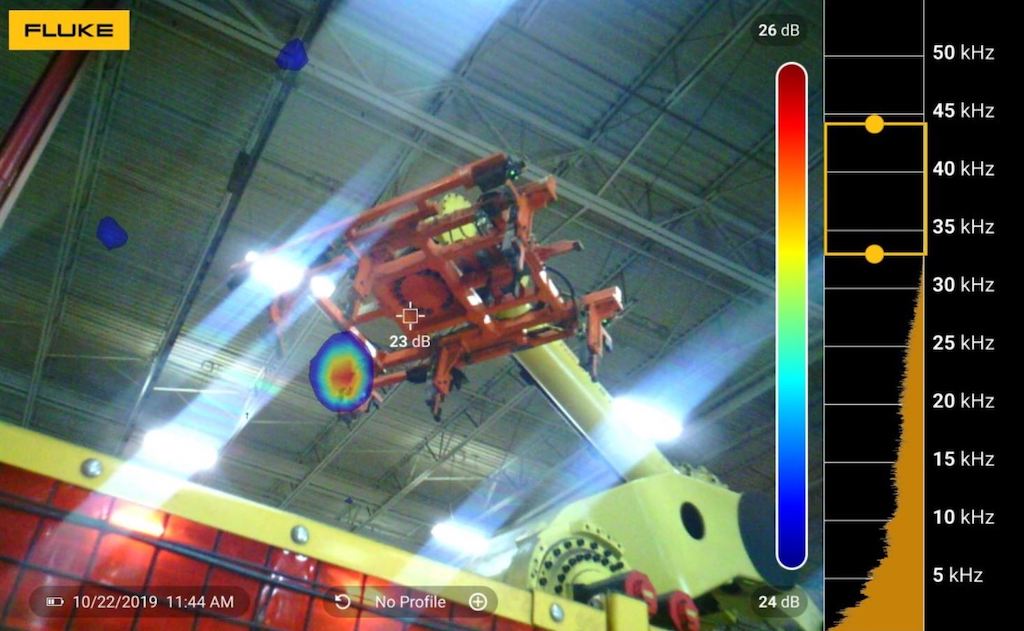
Financial damage
In addition to the potential cost of quality or downtime, there is a cost associated with leaking compressed air systems. According to the U.S. Department of Energy, a single 1/8-inch line in a compressed air system can cost as much as $2,500 a year in energy costs alone. And that’s just air. When gases are involved, the costs can skyrocket. One professional compressed air auditor found a customer’s cost for nitrogen was 65 times that of air, and argon was 335 times more than air.