Technology can be part of the ‘culture’ in plants
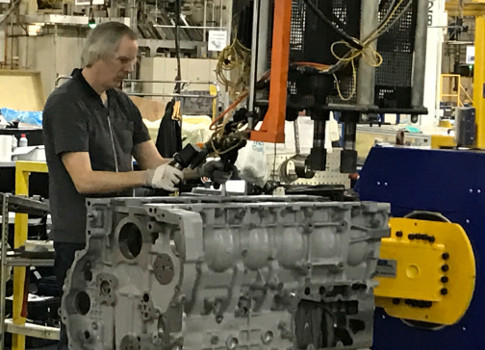
The Internet of Things (IoT) is not just about improving the production on the factory floor; it can aid in creating a safer working environment.
The U.S. Bureau of Labor Statistics reported in 2016 that within the private manufacturing sector there were more than 300 fatalities and more than 410,000 non-fatal occupation injuries. Similar statistics published by the UK-based Health and Safety Executive (HSE), there were 19 fatal injuries and 60,000 non-fatal injuries reported in 2016-17. Contact with machinery accounted for 18% of fatal injuries and 12% of non-fatal injuries, at a cost of more than $700 million.
With such significant costs associated to such incidents (both personal and financial), a consideration of how new technologies can mitigate risk for workers is a crucial consideration.
Within manufacturing, applications for how IoT can improve processes have been well covered. However, for IoT and safety, the benefits to personnel is less discussed. One application showing how IoT solutions could support preventative safety is by predicting patterns in workers on the factory floor, that would reduce the risk of injury.Â
Human factor
The benefits of safety solutions, especially connected safety solutions, have certainly been emphasised in the recent years as IoT drives industrial automation into the digital age. One benefit that is regularly mentioned is increasing profit, based on improved efficiency and productivity. However, improved safety can also reduce costs resulting from non-fatal and fatal injuries to personnel.
The HSE stated that in 2016/2017, within the manufacturing sector there were 159 court cases related to injury. The average fine per case was about $213,271, not including other legal fees.
Lack of proper safety measures can result in fines, compensation, pay for sick leave and recovery, as well as additional costs. Globally in in 2015 and 2016, there were more than 50 changes to safety directives and standards. These changes can be initially costly to implement; however, they can save lives and money in the long term
While companies may put safety measures in place for machinery to deter or prevent unsafe or unauthorised access, they can be ignored or misused due to the culture surrounding safety or the industry a worker is in. Poor practice can render a safety measure useless. This has been illustrated in some cases of zero-hour contract workers.
Some contracts are paid dependent on output rather than by hour, which can result in a sense of urgency. Safety measures can increase the time taken to do a task and it has been known for workers to disable, or work around safety procedures to save time.
Machine safety and IoT
Industrial IoT (IIoT) is increasingly influencing safety products and solutions, through improved connectivity of more intelligent devices, with vendors able to support customers with data that can provide insight on production, in addition to core safety features.
An example of smarter safety technology is laser scanners intended for outdoor and warehouse use. These products can be used to support vehicle navigation, cranes and robots; prevent collisions; and provide protrusion monitoring for storage, which checks for prohibited protruding objects that may result in improper storage, for example in warehouses. This means that laser scanners not only provide safety, but also aid in navigation, logistics, and storage management, therefore increasing efficiency and productivity.
IoT is aiding product development, which could help tackle unsafe situations. For example, RFID technology is used with safety interlock switches to allow for single monitoring of doors and provide important insight on usage. Improper use of a safety interlock switch could allow a guard or gate to be opened or unlocked, rendering the product useless. This is a dangerous (but not uncommon) practice pushed by workers chasing productivity gains rather than following safety processes.
By better understanding these behaviors, it may be that further training is given, the interlock switch design and gate is adapted, or even the worker contract itself is reviewed.