2023 System Integrator of the Year, NorthWind Technical Services, automation and control system integration projects help with feeding school children, delivering clean water, and manufacturing recycled building materials, among others. Related control and automation systems consume less energy, produce less waste, provide for a cleaner and safer environment and produce a better return on customer investments.
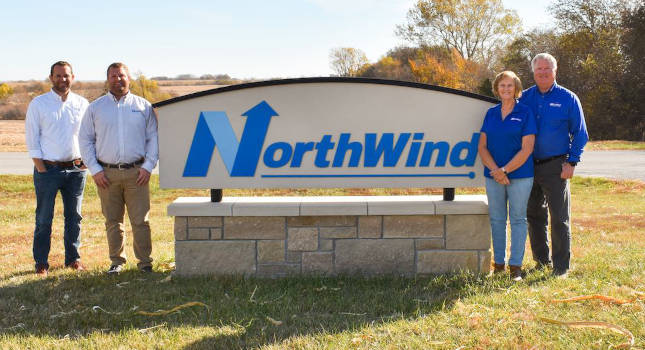
Learning Objectives
- System Integrator of the Year for 2023, NorthWind Technical Services, discusses control system integrator project that make the world a better place.
- Learn how integrating internal software systems improves cost, quality, and schedules for control system integration projects.
- Understand how intense training helps recent engineering college graduates get up to speed more quickly on control theory and system integration.
System Integrator of the Year, NorthWind Technical Services, integration insights
- Recent system integration project success at included more efficient (less waste and less energy) and cost-effective control system implementations helping to feed children, deliver clean water, and manufacture recycled building materials.
- Integrated internal software systems and supply chain planning are two areas of efficiency for NorthWind Technical Services, Control Engineering and Plant Engineering (CFE Media and Technology) System Integrator of the Year for 2023.
Control and automation systems NorthWind Technical Services builds and integrates consume less energy, produce less waste, create a cleaner and safer environment for customers and produce better return on the customer’s investment as a result. Applications include feeding (school) children, delivering clean water, manufacturing recycled building materials, and feeding people’s pets. These are among successes achieved at NorthWind Technical Services leading to its selection at 2023 System Integrator of the Year in the $5 million to $30 million in system integration revenue category.
Michael Bosworth, President of NorthWind Technical Services, answered questions from Control Engineering and Plant Engineering (CFE Media and Technology) about control system integration projects and other enabling topics.
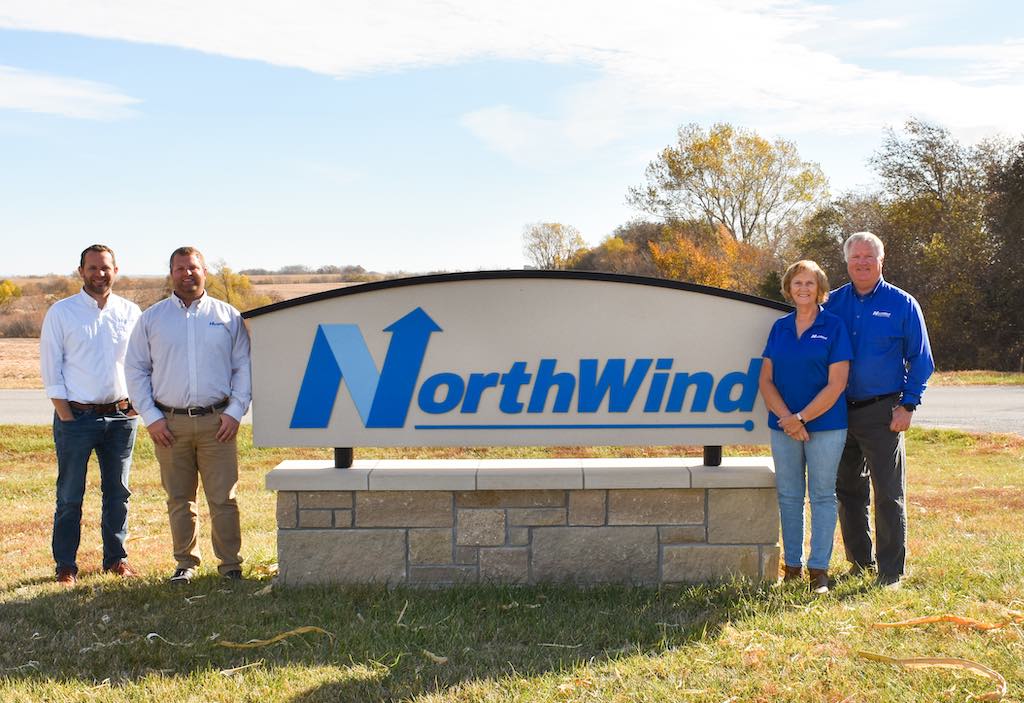
Question: Congratulations on receiving the 2023 System Integrator of the Year award: Talk about what this recognition means for NorthWind Technical Services.
One of NorthWind’s company goals is to be the recognized automation leader in the market segments we serve. Being recognized as System Integrator of the Year is a tremendous honor and validation that we are doing many things right. It is humbling to be recognized in this way as part of a very elite group of the best system integrators.
Question: Describe recent projects you’re most proud of. What has made them a success?
This is a difficult question to answer. During a recent Control Systems Integrator Association (CSIA) meeting I heard one of the companies talk about how they looked at what they did in terms of their impact on society and focusing less on programs, panels, and deliverables. That really struck a chord with me. When viewed that way, NorthWind is having a real impact on feeding school children, delivering clean water, manufacturing recycled building materials, feeding people’s pets around the world and many other really cool things. The control and automation systems we build have enabled our customers to provide these goods while consuming less energy, producing less waste in a cleaner and safer environment for their employees while producing a better return on the customer’s investment. Looking at NorthWind’s impact from that perspective is quite satisfying.
System integration project management integrates systems
Question: What are some methodologies and philosophies applied to projects? How have they evolved, particularly considering COVID-19?
NorthWind has more than 150 active projects at any given time. Our project delivery system and methodology is integrated into every aspect of NorthWind design, manufacturing, software development, and commissioning. At the core is our NorthWind PlantLogix family of customer-facing software, Eplan design software, and Project IQ enterprise resource planning (ERP) software. These systems all operate on one database that also integrates our automated panel manufacturing equipment and human-machine-interface (HMI) tag names. Project IQ ties all business processes together with project deliverables and scheduling. Collectively these systems work together to enable NorthWind to provide automation solutions that optimize cost, quality, and schedules in a way that benefits everyone. In other words, we use automation within our own processes as well as providing that service to our customers. How we did things during and after COVID had to change because of the pressures of the pandemic. But, quite frankly, these changes have improved the way we do business. The future looks very promising for NorthWind.
System integration customer relations: Planning, partners
Question: How have customer expectations for projects changed due to the COVID-19 pandemic?
The collective response to COVID-19 created a lot of chaos and confusion, which complicated almost everything we do. That being said, COVID never actually changed the core principles of project delivery or what the customers need for projects to be successful. Project success starts with a well-planned scope of work and adherence to budget and schedules with the expected outcome being a fully operational production line. To deal with the complications caused by COVID, we were able to focus on these principles and devise ways to work over and around the complications of COVID to provide the successful delivery of what customers need. It was a learning experience to be sure, but we think we’ve come through the pandemic stronger and better than before.
Question: How important is it to develop long-term relationships with customers during projects and why?
Our business has always been built on a partner-centric mentality that relies on building and maintaining long-term relationships. This approach runs throughout all aspects of our business from employees to vendors and certainly to customers. Prioritizing relationships over short term issues and gains is an essential part of keeping these relationships healthy. Our customers have benefited from this directly as it applies to the quality of the work we produce. Customers also benefit indirectly when they are able to work with an employee with whom they have developed a relationship or we can call on our vendor partners to help solve a problem.
Question: Have the supply chain issues affected current and future projects in a significant way? If so, how?
Yes. Supply chain issues have impacted our panel manufacturing business and overall customer project schedules. We recognized the potential for problems early on and worked to increase our inventory to about five times pre-pandemic levels before the supply chain lead-time issues hit full force. We also began aggressively pre-ordering very early in the design phase of many projects to stay ahead of supply chain issues. Having good vendor relationships also helps a great deal in mitigating the impact of shortages. While these actions have not prevented all delays, they have helped us minimize the number of problems and enabled us to ship our panels in a timely manner.
System integration training, retraining; hiring recent graduates
Question: What do you do to help guide younger engineers along in projects so they gain valuable experience?
Training and retaining employees is one of the top priorities for NorthWind and has been for years. NorthWind’s strategy for sustained growth over the last 25 years has emphasized hiring recent graduates and providing them with training needed to perform the work we do. What has changed in recent years is the training pace, structure, and content. On-the-job training with a mentor for basic skills has been reinforced with intensive classroom training and learning exercises. This is then followed up with more advanced multiday training classes on specific controls topics. Overall, this has really helped to advance professional development and reduce the time it takes for a new controls engineer to become productive.
Question: If there is one long-term goal you have for the company, what is it?
My overarching goal for NorthWind is that we always act as good stewards of the people and resources entrusted to us. We meet this goal by continuing to invest in our people, by challenging them to expand their knowledge through hands-on experiences, as well as through hard and soft skill training. For customers, we strive to provide an excellent return on their investments by the quality of the product we provide. That means striving to deliver innovative and reliable automation solutions that are up to date with the latest technologies making manufacturers as efficient as possible. We have done our jobs well and met this goal when employees, customers and ownership are all better off because of their associations with NorthWind.
Michael Bosworth is president of NorthWind Technical Services. Edited by Mark T. Hoske, content manager, Control Engineering, CFE Media, [email protected]. Chris Vavra, web content manager, CFE Media and Technology, collaborated on questions. Amanda McLeman, director of research and awards programs, administers the System Integrator of the Year program. www.controleng.com/SIY
KEYWORDS: System Integrator of the Year, NorthWind Technical Services
CONSIDER THIS
Are your HMI tags integrated with other software systems?
ONLINE
Learn more about NorthWind Technical Services in the Control Engineering and Plant Engineering Global System Integrator Database.
https://gspplatform.cfemedia.com/si/integratorProfile/55d24321e4b020ebbc15c21c
4 system integration metrics that matter
Each System Integrator of the Year firm for 2023 was asked to quantify recent progress using a few metrics. According to NorthWind Technical Services:
-
Recruiting and employee retention: We have successfully increased full-time staff by 24% in 2022 while maintaining a turnover rate that is about ½ that of industry averages.
-
Professional advisors include 2 individuals with extensive expertise in control system integration, business management and accounting; these advisors help with the business planning process, critiquing business practices and developing strategic plans for the future.
-
Projects for global good: 4 include positive impact on feeding school children, delivering clean water, manufacturing recycled building materials, and feeding people’s pets around the world.
-
Inventory in panel shop: 5x increase: To deal with supply chain issues we increased our inventory to about five times pre-pandemic levels before supply chain lead-time issues started.