As factory owners expand their operations and invest in new technologies and systems to support expanding workloads, attention must be paid to addressing novel security issues.

Security insights
- Learn how to identify and address seven common security issues associated with the evolution of modern factory operations.
- To assist stakeholders in this process, the following explores seven security issues to address as factories evolve, including advice on how to develop future-proof security solutions.
Ensuring the safety and security of machinery, materials, inventory and employees has always been a top priority for factory owners and operators. However, while advancements in technology have enabled leaders to make many improvements, both in terms of security and productivity, the risks facing factories have become more sophisticated in recent years.
With reports suggesting cargo theft, metal theft and vehicle theft rates are rising across the U.S., many factory owners are facing the realization that their security systems may need to be updated. Leaders must also account for the rising commonality of cyberattacks, with manufacturing considered one of the most frequently targeted industries by cybercriminals.
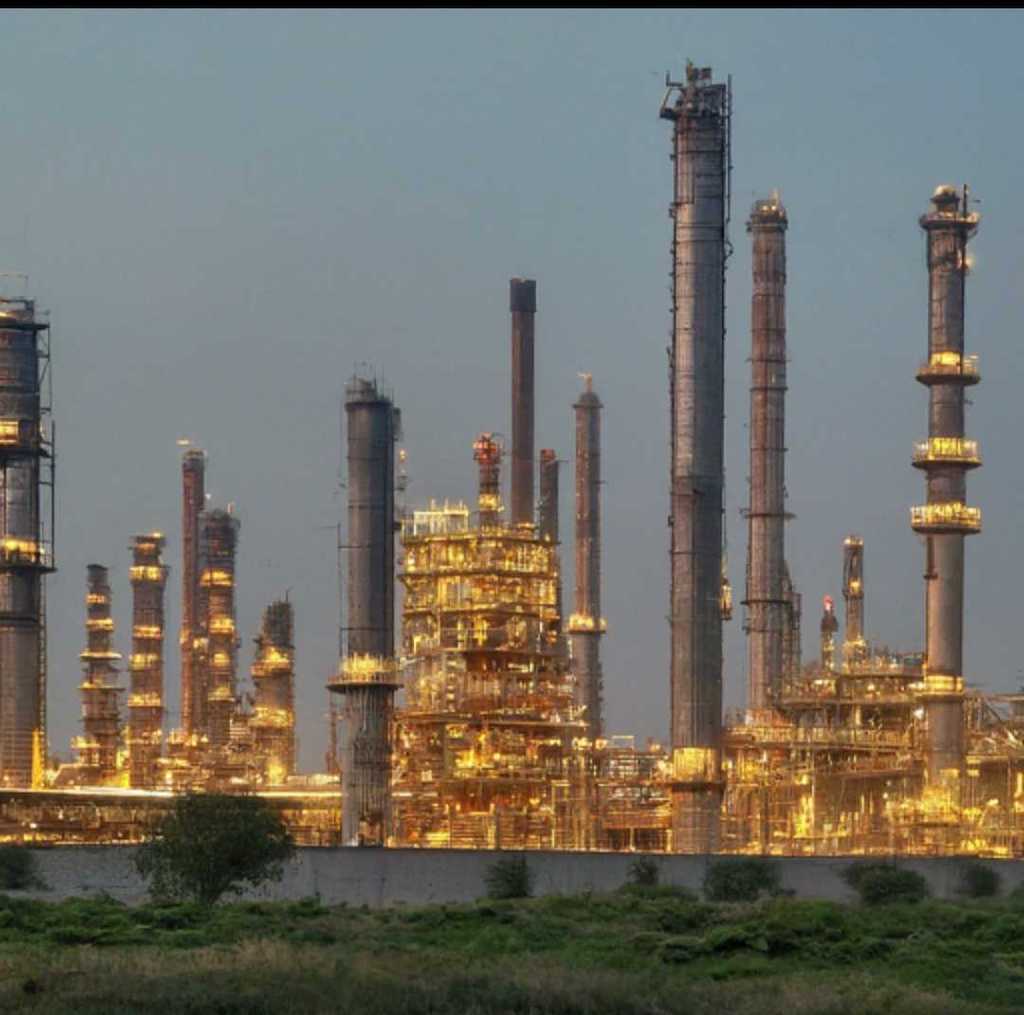
As factory owners expand their operations and invest in new technologies and systems to support expanding workloads, attention must be paid to addressing novel security issues. To assist stakeholders in this process, the following provides seven security issues to address as factories evolve, including advice on how to develop future-proof security solutions.
1. Burglary and theft
Factories contain large volumes of machinery, raw materials and saleable goods that can be viewed as valuable by criminal organizations. The presence of these assets makes factories a prime target for instances of burglary and theft, especially if appropriate security measures have not been implemented such as sensors, alarms, access systems and closed-caption TV solutions.
As factories evolve, with new technologies, processes and workstations added to an existing physical space, leaders must ensure physical security systems are enhanced and optimized to address changing needs. Stakeholders must ensure security cameras provide continuous coverage of key areas, entrances are secured and sensors are used to add context to alerts.
Factory owners should consider developing integrated security systems, whereby all active devices can communicate to perform automated responses. Cameras can be equipped with artificial intelligence analytics to autonomously detect suspicious activities, with alarms and locks programmed to instantly engage in response. Such systems help to combat threats like burglary and theft.
2. Unauthorized access
The addition of new employees, roles and processes is to be expected as factories evolve, with some additions potentially exposing new vulnerabilities in existing security systems. A prime example is access security, with leaders needing to find new and manageable ways to ensure private areas, assets and digital tools can only be accessed by authorized persons.
Using access control models can help to address this issue. Rule- and role-based models apply unique criteria to the granting of access requests. For example, only credentials held by management staff can be used to access high-risk areas, with all systems programmed to lock automatically after a set time, thus mitigating the threat of unauthorized access events.
3. Industrial espionage
Industrial espionage is a significant threat facing modern factories, especially those engaged in manufacturing operations. Data shows 94% of cyberattacks targeting manufacturing sites are performed with the intent to steal sensitive intellectual property, with experts warning that state-sponsored industrial espionage attacks are becoming increasingly common at present.
Factory owners can reduce the risk of such attacks using a combination of smart security systems and well-managed organizational policies. Examples include securing information technology solutions using cybersecurity tools like firewalls and endpoint detection systems and implementing strict access policies to ensure only trusted persons have access to high-security locations.
4. Cybersecurity threats
Cyberattacks have increased across all industries by as much as 221% in recent years, with manufacturers in particular seeing a 165% increase in attacks. As factories evolve and new software tools and management solutions are added to existing infrastructure, leaders must make efforts to reevaluate and optimize existing cybersecurity provisions to mitigate threats.
This is especially important if new sites have been opened with novel security technologies and management tools operating via remote connections. Leaders must choose to develop multisite security systems featuring advanced cybersecurity protections such as encryption and endpoint detection and response tools to ensure systems remain reliably cybersecure.
5. Processes and governance
Alongside ensuring new digital systems are well-protected, factory operators must consider how the deployment of new organizational policies associated with novel workflows across new sites are implemented. Changing the processes governing the performance of key tasks can expose new vulnerabilities, meaning audits should be conducted before work can begin.
Leaders and management staff must work closely with security professionals to assess the security of newly implemented processes. Teams must walk through the performance of key tasks to ensure that the following of organizational policies does not expose flaws in security tools or contradict existing rules. Such audits will help teams to optimize security provisions.
6. Third-party security risks
As factory operations expand to cover increasing numbers of worksites and work processes, leaders may be required to outsource some key security operations to third-party providers. While this undertaking can help factory owners make more efficient use of limited resources, it is vital that prospective collaborators are reliably vetted to limit the risk of security breaches.
Data reveals third-party attack-vectors are responsible for almost 30% of recorded security breaches. Factory operators must conduct research to find out whether prospective vendors have been involved in historic data breaches. As well as liaise with their teams to conduct a third-party risk assessment and gain confirmation that they hold relevant security credentials.
7. Connected industrial systems
Industrial internet of things (IIoT) devices and systems are becoming increasingly common in factory settings, enabling operators to network various sensors and systems together to benefit from real-time data analytics. The number of IIoT connections increased by almost one billion between 2023 and 2024, but the adoption of these technologies can expose novel threats.
Most (96%) IT professionals expect to see an increase in attacks on IIoT systems in the coming years, meaning factory operators must understand best practices associated with high-level IIoT security. Effective protective measures and key security processes to consider include:
-
Passive scanning solutions: Passive scanning tools are used to identify and record all IIoT connections without impacting operations. These tools provide security teams a list of all active connections to help them ensure authorized devices are working as intended and to help them identify unauthorized connections with prompt efficiency.
-
Network vulnerability scans: Network vulnerability scans work in combination with passive scans to help teams identify potential weaknesses in network security. Once identified, exploitable vulnerabilities can be patched to prevent unauthorized access.
-
Vulnerability prioritization: It is not always financially or logistically possible to patch all potential vulnerabilities, so teams must rank possible issues by priority. Common solutions to high-risk issues include deactivating unnecessary services, restricting access using network access control tools and updating IIoT device configurations.
-
Anomalous behavior monitoring: Anomalous behavior monitoring tools can help security teams identify potential attacks before damage being done. These tools look for suspicious activities associated with server-based data, traffic from network devices and information transferred to file transfer protocol servers to help staff spot unusual actions.
The future of security
As factories evolve and operators take on new responsibilities across novel sites, processes and internal roles, previously effective security installations can begin to lose efficacy. As a matter of priority, leaders must make a commitment to auditing, analyzing and optimizing key security processes to effectively mitigate threats and ensure a safe and secure environment.
By reviewing existing security technologies and processes and considering the potential for new vulnerabilities to be exposed because of expanding operations, leaders can reduce the risk of exploits leading to security breaches. By following the advice mentioned above, owners and operators can commit to addressing security issues as their factories evolve.