For data to have real value to today’s automated manufacturing plants, industrial networks need critical tools to access and deliver the data to critical operational and analytical platforms.

Learning Objectives
- Understand how digital transformation helps manufacturers realize the value of their industrial data.
- Learn how information technology and operational technology (IT/OT) convergence helps companies better manage their data.
Digital transformation insights
- Digital transformation is providing manufacturers with unprecedented amounts of data related to production system performance; however, many older manufacturing sites use platforms that keep the information siloed and separate from other systems.
- A new generation of scalable edge computing platforms is providing a critical solution to this challenge, incorporating key capabilities such as robust protocol conversion libraries and user-friendly programming interfaces that make it easier to build bridges between those data islands.
- Improving industrial data networking capabilities can also help manufacturers more fully and efficiently integrate the worlds of information technology and operational technology (IT/OT).
The promise of Industry 4.0 is rapidly being realized across many manufacturing segments. A wide range of sensors, smart components and advanced automation drives and controls are routinely integrated into production machines and processes, furthering the growth of automated manufacturing.
These systems are now generating large amounts of industrial data. The challenge for many manufacturing operations invested in this digital technology is how to efficiently access and utilize this data, leveraging its full value with networking systems that are reliable, secure and scalable to meet both current and future needs.
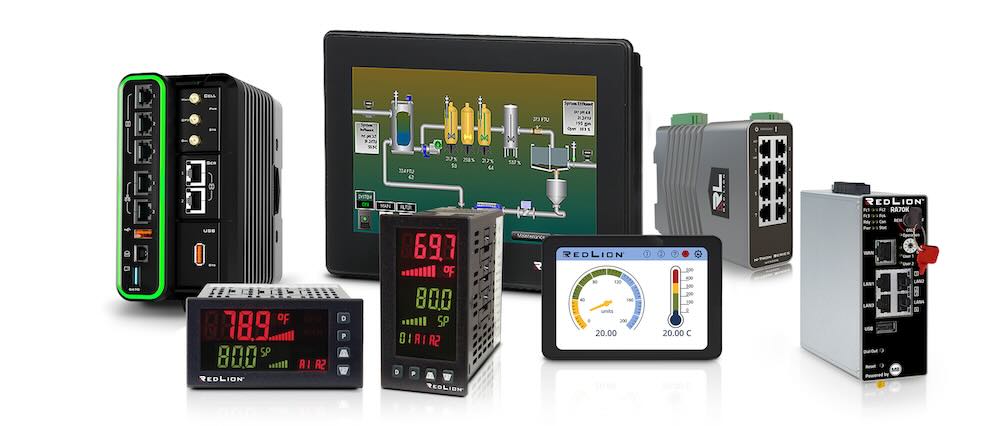
Several key technologies provide the critical building blocks of high-performance industrial data networks. Systems integrators, original equipment manufacturers (OEMs) and manufacturers are seeking strategies to use these tools to gain more complete access and control of companies’ industrial data and bridge existing gaps between information technology (IT) and operational technology (OT) within the manufacturing enterprise. The goal is accessing that data to improve operator performance, plant safety, predictive maintenance processes and manufacturing productivity.
Connecting islands of data
Today’s manufacturing platforms constantly generate mountains of data related to the performance of individual machine components, subsystems and production lines. It’s being generated by sensors, pneumatic valves, control devices, electric drives and other components. The volume of this data constantly grows.
However, in many production environments, the data is isolated. This complicates manufacturers’ efforts to use the data to improve productivity and return on investment (ROI). In many cases, this isolation is unintentional. For example, temperature and valve performance data are fed through input/output (I/O) channels to a machine controller, but may not go any further without manual intervention, limiting its value.
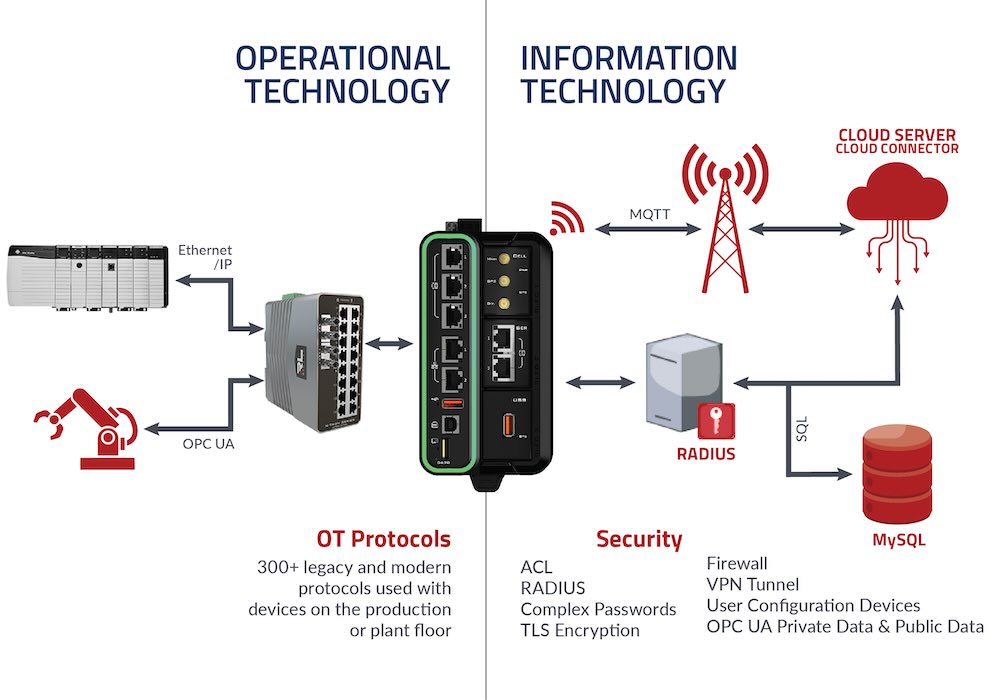
Industrial data is a manufacturer’s most valuable asset. Data’s true value is only realized when it can be easily accessed, aggregated with other machine and line data and analyzed. These “islands of data” exist because many factory automation plants have multiple generations of equipment installed — in some cases, decades-old systems that still provide productive performance.
Incompatible communications protocols are a major reason why full industrial data networking can be so challenging to implement. Many older machines will be using protocols such as Modbus RS-232. At the same time in the same plant, a newer production system added to the line will use more current, open protocols such as OPC UA. To compensate, some companies building out their networks may try to create specialized software patches on a case-by-case basis.
The most effective solution to this challenge is a robust set of protocol conversion capabilities that can be implemented as part of investments in new data access and connectivity systems.
Rise of edge computing systems
Edge computing platforms, sometimes called edge gateways, are playing a fast-growing and critical role in solving the challenges of disconnected islands of data. Edge computing often refers to hardware/software networks and devices located at or near the end user. It enables data access and processing closer to where the data is generated, for faster processing speeds and higher data volumes that supply actionable data in real time.
Edge computing platforms are widely used for critical, real-time protocol conversion to bridge legacy and current generation production systems. Leading providers of these edge platforms are designing them to be powerful networking devices, engineered to supply critical data access and management tasks.
Leading suppliers offer platforms that can simultaneously process up to 20 protocol conversions from over 300 supported drivers. These platforms are designed to be all-in-one edge devices that support other critical functions, such as data logging, easy access to MQTT-based cloud servers and remote access.
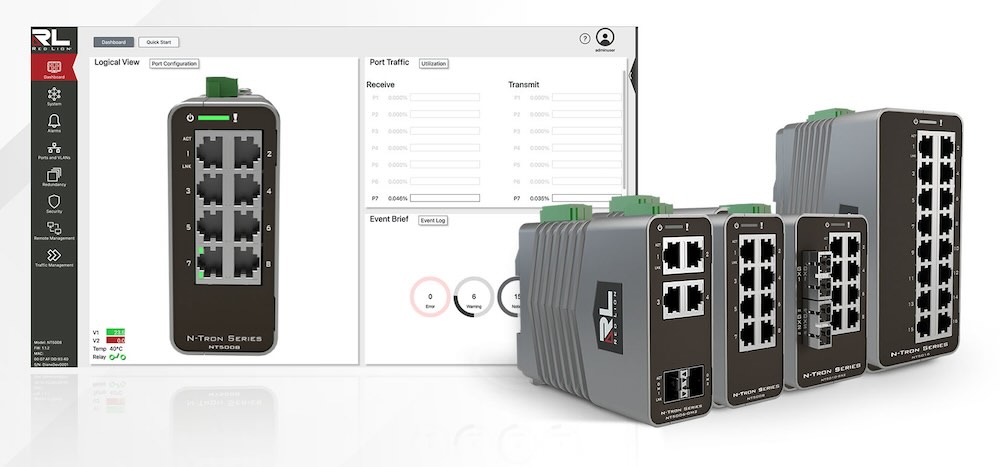
Edge systems are being offered by many different technology suppliers, so picking the right one calls for careful assessments. In some operations, manufacturers are reluctant to invest in edge platform technology out of concern that implementing these systems will be costly and time-consuming.
Look for systems that feature user-friendly software and feature efficient, drag-and-drop programming platforms that make it easy to set up protocol conversion, cloud connections and data logging features. There also are advantages to utilizing scalable platforms. For example, one leading platform can serve as a protocol converter, a networking gateway or an automation controller via software upgrades.
It’s also important to weigh potential yearly software fees and costs for external support services. Costs also could escalate beyond established budget parameters unless properly accounted for when purchasing multiple systems to upgrade networks.
Expanding remote access
In many cases, today’s automated manufacturers are multi-location operations, with multiple plants situated across the globe. To be competitive and productive, they need to operate as fully integrated enterprises. This means eliminating data communications barriers between facilities and leveraging cloud-based analytical tools.
Along with edge computing platforms, a new generation of remote access systems is now being launched to meet these needs. These systems provide a dedicated platform to advance remote system monitoring, making it possible to remotely access and interact with production systems in a secure and reliable way from anywhere in the world.
Just as legacy production tools in a plant can become islands of industrial data without effective protocol conversion capabilities, geographically separated plants can also become islands. With one remote access device, users can access multiple other connected network devices and obtain real-time insights and comparisons about how similar production systems and plants are performing.
These devices are useful as more multi-location companies use cloud-based analytical tools to conduct deep dives into their industrial data, extract trends, modify production or supply chain processes, improve enterprise-wide predictive maintenance programs and guide long-term planning. It is impossible to carry out these kinds of high-level analysis without having robust remote access to help ensure real-time data is accurate and current.
Cloud-based data management and analysis depend on secure and efficient data communications from the plant to the cloud. One emerging technology in plant automation that is shaping the future of manufacturing is the message queuing telemetry transport (MQTT) protocol. MQTT was designed for connections with devices in remote locations with resource constraints or limited bandwidth, making it very lightweight and efficient at moving data to and from a data broker (either locally or in the cloud).
MQTT is capable of “report by exception,” which means data is only transmitted when it has changed. This feature can provide significant bandwidth savings for both internal and external networks. Specifically configured topics can be stored by the database during a network outage and forwarded to users once reconnected, which guarantees delivery of messages about critical topics. MQTT is not necessarily “new” but is still new to the world of manufacturing with many companies starting to adopt this powerful technology. Automation companies seeking to bridge the remote data islands between their production facilities will benefit from selecting edge computing platforms that support MQTT.
Visualization key to using real-time data
Connecting industrial data with enterprise-level analytical platforms is crucial to gaining deep insights into automation system efficiency and performance. However, that data has equal value (in some cases greater value) for operators and managers on the factory floor.
Actionable data needs to be presented in real time to help operators visualize the information they need to maximize productivity and throughput. The latest generation of human-machine interfaces (HMIs) and operator panels are designed to deliver that data in clear and compelling formats. They incorporate features that let them integrate data across multiple devices and, in conjunction with edge computing platforms, acquire and display data that has been converted from multiple legacy protocols.
Newer generation panel meters feature large, easy-to-read displays that include a broad range of user-selectable graphics and intuitive screen libraries that are simple to configure and customize to specific plant and production line requirements.
With this new generation of visualization technology, operators and line personnel are able to respond to issues faster, process critical information immediately while having one person monitor multiple machines and processes. These tools let operators see more than just information. They also see what the information means and are able to react faster with the right steps.
Integrating IT and OT and leveraging data
One of the biggest challenges factory automation companies face to leverage their industrial data is finding smarter ways to integrate the worlds of IT and OT. These two worlds have, until recently, functioned independent of each other.
OT’s goal is keeping the plant running smoothly while IT manages all the business applications within the enterprise. However, as digital transformation continues evolving in factory automation plants, these two worlds are uniting.
Successful IT and OT convergence depends on enterprise connectivity solutions between the systems that create the data and the users that consume the data. In order to extract any actionable insights from this OT manufacturing data, it needs to be packaged in an interchangeable and flexible format that can be shared between IT and OT applications.
This is one of the key capabilities that edge computing platforms are providing. Software that collects, organizes and contextualizes OT data — and then makes it available to higher-level IT applications and databases — can unlock actionable plant- and enterprise-level insights to guide critical decisions about ways to improve manufacturing processes, increase energy efficiency, reduce machine downtime and provide a more flexible and productive manufacturing enterprise.
This data exchange between IT and OT also needs to be as secure as possible. Hackers and ransomware criminals will try and target industrial systems for vulnerabilities so they can access enterprise IT networks through OT systems. It is critical to select edge computing platforms with top-of-the-line security features, including a stateful firewall, access control list capabilities, packet filtering and fully secured virtual private network (VPN) connections.
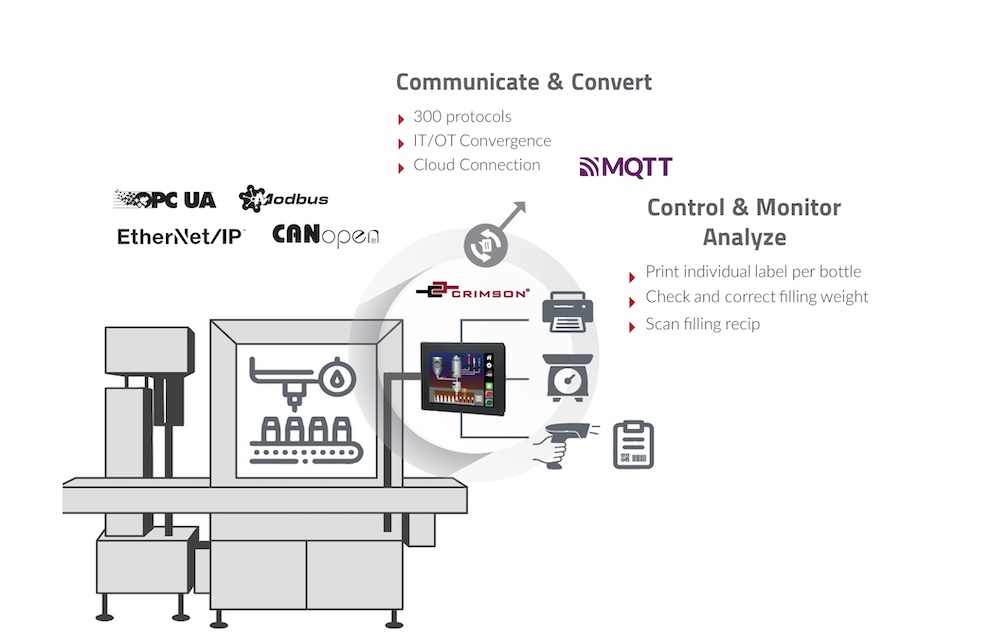
These edge devices deliver valuable, long-term insights into plant floor operations. With the data collected from OT, operations can transition to proactive and develop predictive and prescriptive maintenance strategies.
For example, these devices can automatically alert operators to any changes or events that could lead to a machine shutdown, allowing them to stay ahead of — and avoid — costly production issues. Finally, thanks to powerful remote access capabilities, users from anywhere in the world can add alarms or improve logic and data collection processes or even monitor traffic on the OT network.
Maximizing industrial data’s value
Digital transformation has woven a wide range of data-generating components and systems into automated manufacturing systems. Many manufacturers continue to struggle with accessing that data, particularly from older legacy equipment.
Sophisticated edge computing, remote access systems and smart visualization systems can provide solutions to these challenges, bridging persistent “data islands” so that each company’s most valuable resource — its industrial data — can be accessed, connected, visualized and analyzed to help drive operational improvements and long-term decision-making.
Finding and implementing the right technology for each plant and manufacturer can be challenging. Today’s leading industrial data networking suppliers are experienced at analyzing each plant’s unique infrastructure and a company’s data needs. They can apply their expertise to develop strategies to meet those needs, based on an in-depth appreciation of where data is isolated, as well as insights into future needs as companies grow and evolve.
Industrial data is a company’s most valuable and useful asset. The right technologies, combined with smart approaches for using those technologies to improve day-to-day operations and long-term business strategies, can play a critical role in helping realize the full potential of digital transformation in factory automation.