Much has been written about leak management programs, best practices and the like, but little has been offered in terms of a proactive approach. That is, when installing a new system or expanding or rerouting an existing one, what can be done to prevent leaks? The pipe-joining method is an important decision that will impact maintenance programs down the road. Press-to-connect pipe-joining systems can be a means to prevent air loss in compressed air systems.
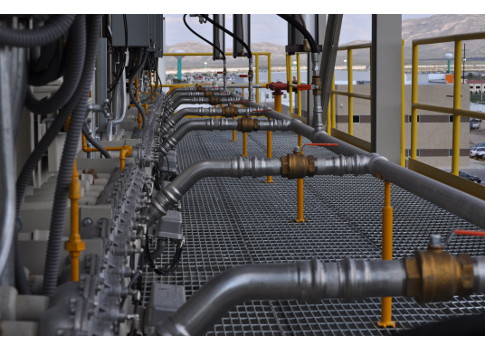
Leaks in compressed air systems are a huge problem at industrial plants. They’re expensive, detrimental to equipment, and time consuming to locate and repair. Often the solution is reactive: Only after the system is installed and in operation can leaks be detected and fixed.
Much has been written about leak management programs, best practices and the like, but little has been offered in terms of a proactive approach. That is, when installing a new system or expanding or rerouting an existing one, what can be done to prevent leaks? The pipe-joining method is an important decision that will impact maintenance programs down the road. Press-to-connect pipe-joining systems can be a means to prevent air loss in compressed air systems.
Compressed air costs
Most Plant Engineering readers are well acquainted with the issues associated with leaks in compressed air systems. First, there are the costs. Air may be free, but the electricity required to compress it most definitely is not. Compressors use more energy than any other type of plant equipment, yet around 20% to 30% of a compressor’s output is lost to leaks in facilities that have inadequately maintained compressed air systems.
In its publication Improving Compressed Air System Performance: A Sourcebook for Industry, the U.S. Department of Energy’s Office of Energy Efficiency and Renewable Energy reports that a single leak of 1/16-in. can cost $523 per year, while a 1/4-in. leak could cost $8,382 per year (calculated using an electricity rate of $0.05/kWh, and assuming constant operation and an efficient compressor).
Adjust that figure to your local industrial usage rate, then multiply by the number and size of leaks present, and it’s easy to ascertain just how much those leaks could be costing you. For many facilities, it adds up to thousands or even hundreds of thousands of dollars per year.
Compressed air leaks are also associated with problems at the point-of-use, leading to additional operational costs. Leaks cause a pressure drop in the system, which decreases the efficiency of tools that use the air. Less efficient tools mean less efficient production. Equipment service life can suffer as a result of running the equipment longer, and maintenance time and costs may increase.
Depending on the detection method and scope of the facility’s compressed air systems, finding and repairing air leaks can be a time-consuming task.
Combined, these issues make preventing leaks on the front-end a worthwhile goal.
A piping solution for leak prevention
Although leaks can occur at any point along a compressed air line, joints and connections are the most common location. Pipe joints, fittings, valves, disconnects, and the like are typical problem areas. That being said, selection and proper installation of the air distribution piping is one of the key elements in preventing leaks.
In recent years, many engineers have shifted away from specifying threaded piping to join air systems because of its tendency to leak. Often these leaks are caused by installation issues such as poor thread cuts, failure to clean the threads, or improperly applied thread sealant. Ongoing plant operations can also lead to leaks; vibration or impact, for example, can weaken the seals.
Press-to-connect pipe-joining systems have become an increasingly popular option for compressed air systems as the technology has advanced. These systems join pipe by compressing a fitting onto the pipe-ends. The joining process is quick and flame-free: Pipe is cut to size and deburred, marked for visual verification of complete insertion, then inserted into a pre-lubricated coupling, fitting, or valve. A handheld pressing tool is used to press the component—which contains elastomeric seals—onto the pipe-ends, providing a positive mechanical interlock and creating a rigid, permanent joint.
Most systems feature some kind of press detection technology, which enables the installer to identify any unpressed joints when the system is pressure tested. The mechanical strength of the joint is achieved through the crimping process. Sealing is achieved by a combination of the mechanical interference between the component and pipe and the compression of the seal material.
Recent advancements have made press technology available for off-the-shelf Schedule 10S stainless steel pipe. Stainless steel is advantageous for compressed air systems installed in corrosive environments, and ANSI Schedule 10S offers a number of advantages over Schedule 5S or light-wall tube: the pipe-wall is up to twice as thick, resulting in up to three times the end-load performance, twice the bend-load performance, a 52% increase in available flow, and a 23% reduction in pressure drop per 100 linear feet of pipe. The use of Schedule 10S stainless steel results in stronger, more durable distribution piping.
In terms of leak prevention, press-to-connect systems have been tested and shown to reduce the likelihood of leaks compared to threaded systems. In fact, in third-party accelerated aging and thermal cycling performance testing comparing a threaded system to a press-to-connect system, deviations from the original test plan had to be made because of frequent leaks in the threaded flow loop. The research team reported that nearly every threaded joint leaked at some point during the test and that, as a rule, the larger the pipe diameter, the more difficult the task of obtaining a satisfactory seal. The repair and rework of threaded joint leaks extended the test program considerably.
While seven cycles were planned, a total of 18 cycles between test conditions and ambient were recorded during the tests. The test report concluded: “It is the test engineer’s opinion that the (press system) couplings offered distinct advantages over conventional threaded pipe components.”
A plant’s pressing success
Actual installations also demonstrate the leak-free operation that can be achieved with press-to-connect systems. A consumer-products manufacturer planning the extension of a compressed air line at its eastern Pennsylvania plant offers one such case study.
When the need arose to extend an existing air service line to install an air hose reel for a stock prep area, the company evaluated its options for joining the 1-in. line. The system was specified stainless steel to withstand the semi-corrosive environment, so company officials considered two joining methods: welding and press systems.
The plant primarily produces paper-based products, so safety is the first concern. Plant maintenance personnel sought a pipe-joining method that would reduce the risk of fire and injuries.
“Because it’s a paper plant, if you’re going to solder or weld anything, you have to go through a series of approvals depending on where you’re working,” the plant’s compressed air system manager said. “There’s an area where we store big rolls of paper, and it’s almost like an Act of Congress to get permission to weld there.”
Press systems’ ability to join pipe without flame was a considerable benefit, and ultimately the reason the plant opted for and installed the line using the press-to-connect joining method. To ensure optimal pressure would be available throughout the system and that it would stand up to the rigor of plant operations, a Schedule 10S system was specified.
“Schedule 5 is pretty thin; it’s almost like conduit. So if we can go with thicker piping, it’s going to increase the longevity of the system,” noted the system manager.
The plant also had a goal to prevent as much leakage as possible, and the performance of the press system surpassed expectations.
“We have absolutely no leaks,” the compressed air system manager reported. “We went through with an ultrasonic leak detector and checked the whole line, and we have no leaks at all. We’re very happy with it.”
Press systems offer additional benefits, including installation that is much faster than other pipe-joining methods, and simple installation that does not require highly specialized skills. In the case of the consumer-products plant, the system’s ease-of-installation meant the plant’s in-house maintenance personnel were able to install the compressed air line extension. Press systems can also reduce total installed costs in comparison to other joining methods.
When installing, expanding, or rerouting a compressed air system, one of the most important considerations should be leak prevention. While no press piping system can guarantee leak-free operation for the life of the compressed air system, such systems been shown to significantly reduce the likelihood of leaks at pipe joints in comparison to other joining methods, and as a result, should be strongly considered for joining compressed air systems.
Susan Schierwagen is director of coupling & suppression systems at Victaulic. For more information, visit www.victaulic.com.