A coal shipping company improved their supply chain and operations by reducing inefficiency and waste with PLC modules.
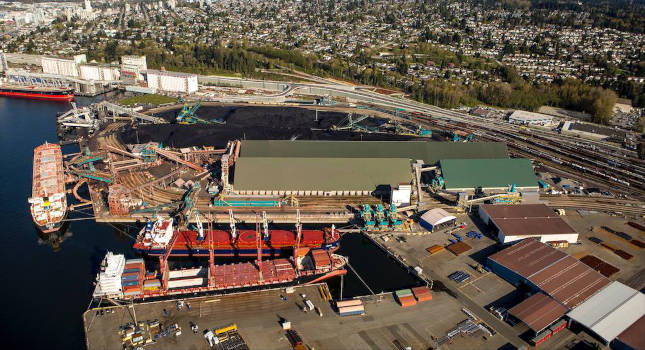
Learning Objectives
- Learn how a shipping company improved their operations efficiency using a built-for-purpose operational technology (OT) to information technology (IT) connectivity solution.
- Learn why not knowing real-time status and real-time routing can lead to inefficiencies and downtime.
PLC insights
Integrating programmable logic controllers (PLC) to business systems to manage operations used to be a manual process, but module technologies can help coordinate them and become more automated.
QCA Systems LTD selected an industrial, built-for-purpose, in-chassis PLC module that acts as the messenger between the PLC and enterprise system using structured query language (SQL).
Neptune Bulk Terminals handles a large portion of the Canadian steelmaking (metallurgical) coal exported to overseas markets annually, and it is an important contributor to the Canadian economy. Reducing environmental impact, costs and processing times are high priorities across the supply chain.
However, an inability to know or control real-time status and real-time routing can lead to inefficiencies, taking the form of missing customer commitments, lower capacities, higher costs and avoidable shutdowns. Streamlining delivery of this information often involves bridging the gap between operational technology (OT) and information technology (IT), enabling users to maximize efficiency and boost visibility across the shipping plant.
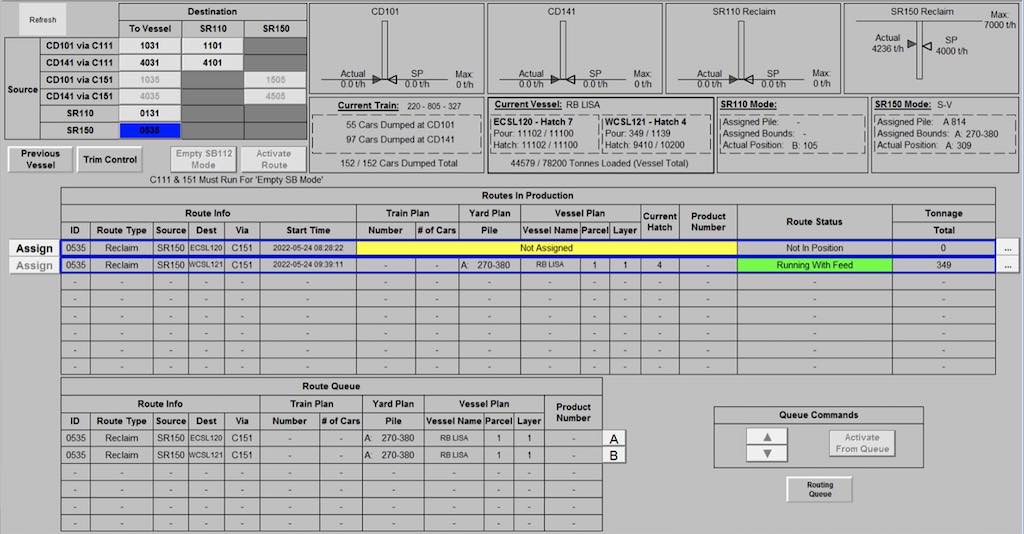
Until now, many manufacturing and shipping plants have relied on manual processes, or software and computers, to integrate programmable logic controllers (PLC) to business systems to manage operations. However, these tools come with challenges associated with hardware and software compatibility, security risks and system interdependence. Fortunately, there are industrial built-for-purpose tools that eliminate the PC and customer software code and let users seamlessly integrate IT and OT in a way that enables bi-directional data exchange between enterprise systems and PLCs, unlocking many benefits across the supply chain.
QCA Systems LTD recently won an award for successfully integrating its OT and IT systems in a coal shipping plant. With more than 30 years of experience, QCA is Canada’s most dominant electrical engineering and automation company in the bulk material handling industry. To improve end users’ productivity and reduce overall manufacturing costs, the company uses its experience integrating industrial and commercial systems, making them secure and creating real-time and historical views of site process data. In one case, they used an industrial, built-for-purpose, in-chassis PLC module to improve efficiency.
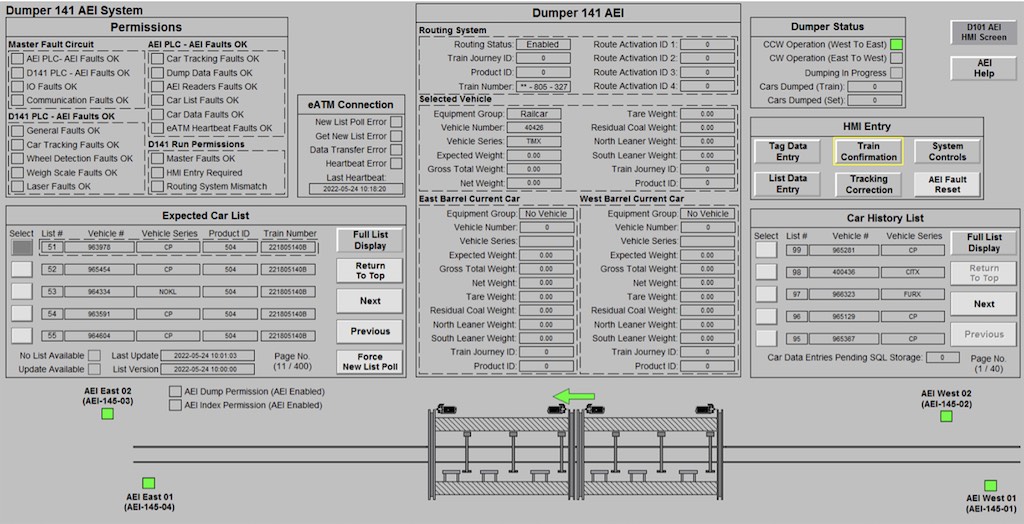
Changing conveyor routes and cargo train conditions
In this application, steelmaking coal comes in from cargo trains, is processed on-site and loaded onto large Handymax or Cape-size vessels. Inside the terminal, shipments are processed through a network of conveyors that must accurately move the coal to and from the cargo transports. The conveyor system, which consists of multiple routes, is crucial to the successful distribution of shipments to the target destinations.
However, these routes are subject to change. Variables such as the volume of imported coal, different grades or load capacity of vessels, can influence the path of a shipment, causing it to deviate from the predetermined route. The shipping plant needed the most accurate real-time information available to successfully adjust its procedures to these evolving circumstances.
Although PLCs stationed along the conveyor routes control the movement of coal, in the event of a process interruption, there was no visibility into a faulty conveyor’s real-time status. There was also no visibility into other nearby conveyors with spare capacity, and no visibility into the higher-level business system, which managed the entire process and logistics.
At this site, PLCs communicated to a single PLC that controlled the routes. In order to improve efficiency, the company needed a lean site-wide management system at the IT business level, and this site-wide management system needed to be integrated to the routing PLC at the OT control level.
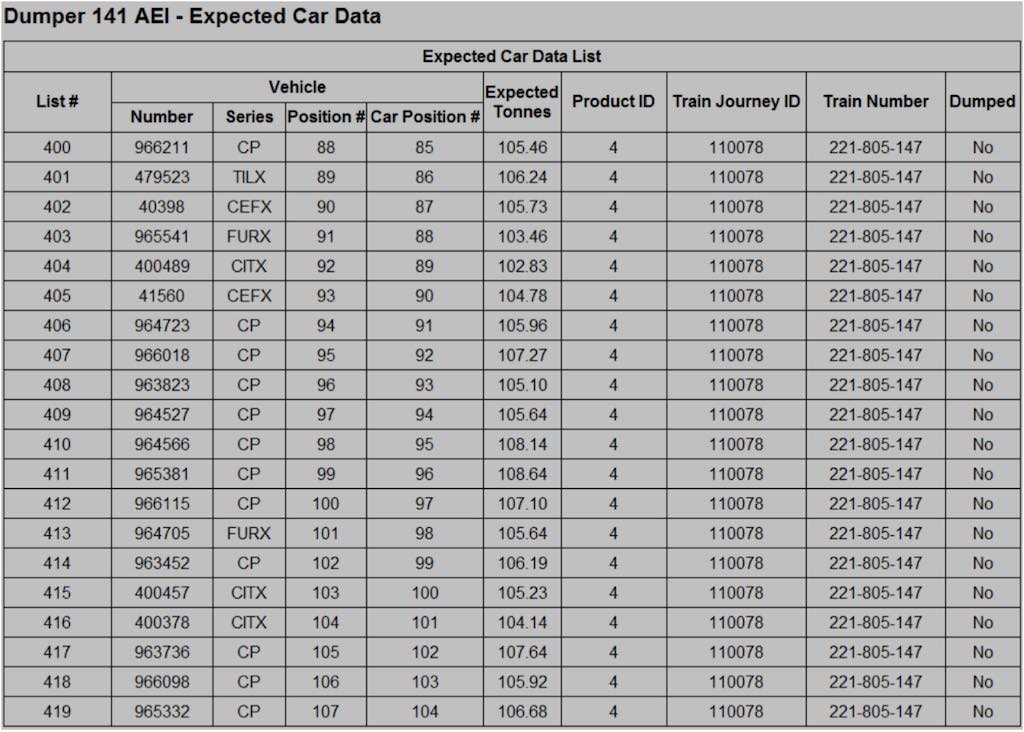
Improving operations with an in-chassis PLC module
To integrate the site-wide management system into the PLCs, QCA selected tManager, an industrial, built-for-purpose, in-chassis PLC module that installs in ControlLogix PLCs. This device acts as the messenger between the PLC and enterprise system, such as Microsoft structured query language (SQL) databases, and eliminates the PC server, software and scripting oftentimes required to orchestrate transactions between the two. By connecting the lean management software system to the enterprise SQL database and connecting the PLCs to the SQL database, it was able to transport critical information bi-directionally to PLCs, enabling personnel in the coal shipping plant to modify their plans with the most accurate and up-to-date information available.
Previously, plant operators could only monitor the expected arrival time and availability of inbound trains and outbound ships, creating operational dead spots if the wrong train arrived for drop-off or the conveyor stopped processing for a single route, for example. The module addressed these issues by providing greater operational visibility.
Routing data is moved from the PLC and stored in a database or other cloud application. In the event of a process malfunction, the module overwrites the old status information in the database to reflect the new route status. In turn, it gets new status information from the database and writes this to the PLC to reroute traffic. Not only does this strategy limit the risks associated with misplacing a product, it also provides detailed real-time information, following the product from the beginning to the end of the cycle.
Centralizing and connecting information with machine control reduces manual processes, increases overall plant efficiency, reduces risk, improves customer commitments and can even lead to valuable metrics for analyzing processes for overall process improvements.
The module also avoids potential pitfalls associated with using PCs and custom coding to integrate business systems with industrial PLCs because it requires no updates, provides better security and is tied to the controller. It also avoids relying on the complicated dance between servers, software and networks for planning and execution.
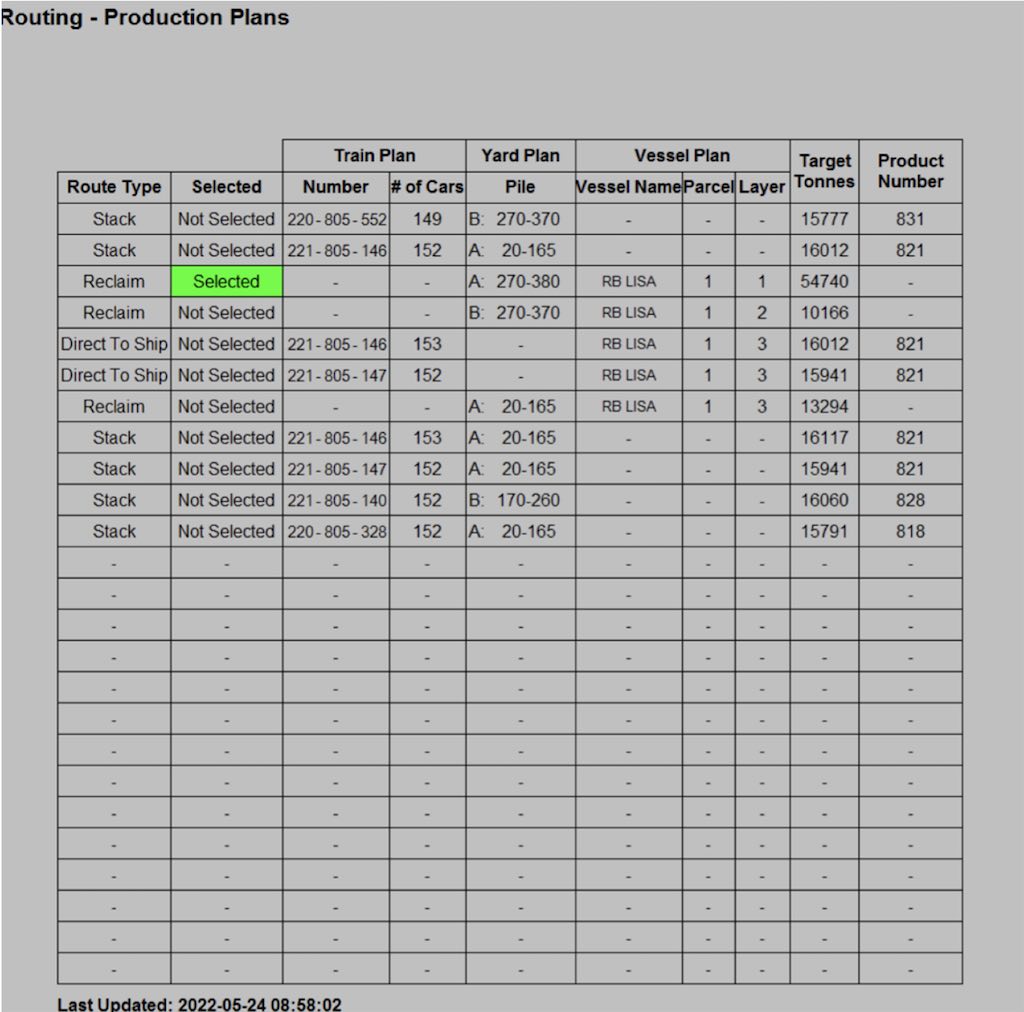
Improving operations management and supply chain
In this application, the module controls the company’s site-wide routing process, while a second and third module manage the importing train systems, as there are two railcar dumpers in this application — each with its own system. Thanks to these devices, the shipping plant now has a more holistic view of its entire shipping process, allowing it to adapt on the fly. Not only is it less complex, it requires no coding, programming or servers.
Thanks to QCA’s engineering and automation expertise in designing and implementing this intelligent routing system using a built-for-purpose OT to IT connectivity solution, the plant has improved its efficiency without having to expand its facility’s footprint that can be implemented in future projects.
Deane Horn is director of product management at Softing. Edited by Chris Vavra, web content manager, Control Engineering, CFE Media and Technology, [email protected].
MORE INSIGHTS
Keywords: programmable logic controller, I/O module
ONLINE
Learn more about tManager here.
CONSIDER THIS
How are you using real-time data to improve your operations?