From raw materials to finished goods, the data flowing between the information/operations technology (IT/OT) system layer is key to increased efficiency, quality and agility.
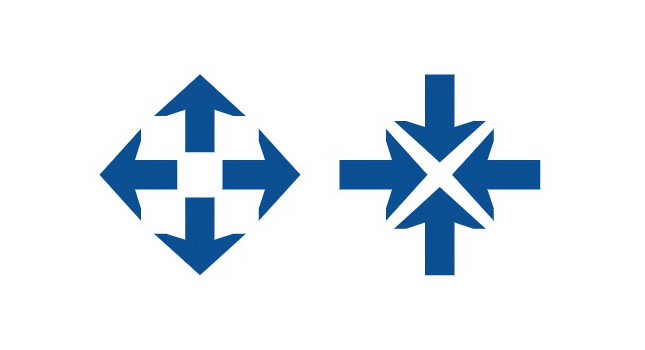
In today’s evolving industrial automation world of smarter, better, faster system and software applications, data remains a constant. For manufacturers, the most impactful source of information they have is data from the operational technology (OT) layer. The whole point of manufacturing, after all, is to produce finished goods from raw materials in the most efficient manner possible and sell those finished goods to customers. The flow of data between the OT and information technology (IT) system layers has increased in the last decade because of open system architecture and innovative software applications.
For instance, the widespread adoption of the EtherNet/IP Ethernet protocol for process control and automation systems and the migration of older protocols to operate within the Ethernet framework has moved manufacturers away from proprietary communications and hardware to open connectivity across the enterprise. The convergence of these underlying communications has increased the interoperability between the automation layer and the business layer.
This convergence also opened the door to Industrial Internet of Things (IIoT) technologies and devices, enabling the Big Data explosion and helped bring other technologies such as digital twins and artificial intelligence (AI) to the forefront. Understanding the wider integration and flow of data between the OT layer and IT applications gives manufacturers the opportunity to leverage real-time data to make more informed and timely business decisions.
IT/OT application roles
Among the most familiar of these IT/OT integrations is the interaction between the enterprise resource planning (ERP) system, process control system (PCS), manufacturing execution system (MES), laboratory information system (LIMS), computerized maintenance management system (CMMS), supervisory control and data acquisition (SCADA) and some others. When going from raw materials to finished goods, each application uses OT data to fulfill a specialized role.
The ERP is the “system of record” for maintaining the company’s books. It manages orders, inventory, production and finished goods from an accounting perspective. At a very high level, the ERP system software tells the MES what and how much of something to produce through a  production order. The MES, in turn, tells the PCS what materials it needs, the quantities and the equipment needed to fulfill the production order.
The PCS acts on the information to do the work required to produce the material while reporting its progress to the MES. During the normal course of product production, specific steps in the process may require the material being produced be sampled and analyzed in the LIMS to determine if the product meets specifications. The results of this analysis can initiate actions within the PCS that may include scrapping material, sending material back through the process for rework or sending it to be shipped.
The CMMS also may be monitoring the real-time health of the equipment, runtime, idle time, downtime, power consumed, and a host of other associated data that all originate in the OT layer. The CMMS also tracks equipment maintenance history, spare parts, parts used, spares inventory, vendors and costs, maintenance scheduling, and other attributes.
The SCADA system monitors process alarms and events, including any operator actions taken during a production process. The process historian continually collects and stores this data, along with time series process data, batch data and other measurements. The wealth of data the PCS produces and the historian captures form the foundation, which provides a holistic view of the production environment.
For PCS data and all its interacting components to be useful beyond a retrospective view, the data must be framed within the context provided by the IT layer systems. To do this, the data in these upper-level IT systems must be accessible. In today’s modern historian platforms, the historian data is available to OT and IT systems over Ethernet via universal and open interface technologies, including OLE for process control (OPC) and structured query language (SQL).
Time to innovate
By taking a closer look at the breadth of data the OT has produced and IT applications have consumed, and are contextualized within the boundaries of each application, manufacturers have the raw material from which they can construct a digital twin model.
A digital twin is a virtual model of production equipment, products and processes. The concept was described in a University of Michigan presentation at a Society of Manufacturing Engineers conference as the foundational model for product lifecycle management (PLM). Digital twins are used to optimize the operation and maintenance of physical assets, systems and manufacturing processes and product lifecycle management. If we take the contextualized data that resides in the IT applications along with real-time and historical data from the OT layer, we can construct a complete digital twin model of facilities, equipment and products from the receipt of an order through shipping and beyond.
This model can encompass the ingredients, parts used and quantities. This includes the equipment used to process them and the operators running the equipment. The equipment includes the temperatures, pressures, alarms, operator actions, quality control (QC) tests taken and the results; when the production started, completed and all the stops in between. It also can include waste, final products, amount and cost of energy, building environment conditions, if a breakdown occurred, who respondent, parts used, time for repair, if the problem happened previously, total cost of production, and other measurements.
While this wealth of information is crucial for a facility, the real promise lies in using this information to make data-driven decisions to predict possible business outcomes, such as:
- Small changes in the operating environment
- Minor differences in the quality of raw materials
- How operator actions affect the system’s efficiency
- How a series of minor process alarms can be used to determine if a major process upset may occur
- The ability to operate proactively instead of reactively.
Thanks to tighter OT and IT system integration, manufacturers are realizing the benefits of increased availability of timely and actionable data. An example of this is the reduction in time for an organization to adapt to a production event. That can include a short-term event, such as an unforeseen equipment breakdown, or a longer-term event, such as a change in product specifications. This type of manufacturing agility is a strategic component in securing and maintaining a competitive advantage.
A new era, smarter industries
Manufacturers are in the beginning phase of what is being called the fourth industrial revolution, Industry 4.0. This era will be driven not just by data, but also by the intelligence that can be derived from it and applied across the industrial landscape of equipment, processes, facilities and people. Integrating OT and IT systems is an important first step along the path. Emerging technologies such as machine learning and other aspects of AI, can revolutionize a manufacturer’s ability to use integrated IT/OT data to build and employ models that form the basis for increasing overall efficiency, quality and agility.
Tim Gellner is senior consultant, Maverick Technologies, a CFE Media content partner. Edited by Chris Vavra, production editor, Control Engineering, CFE Media, [email protected].
MORE ANSWERS
Keywords: information technology, operations technology, IT/OT convergence
Data flow between OT and IT has increased due to technology and software advances.
This convergence also opened the door to Industrial Internet of Things (IIoT) technologies and devices. IT/OT integration can help manufacturers gather intelligence about facilities, processes and people.
Consider this
What immediate benefits could your facility gain from IT/OT integration?