There are many benefits of switching from carbon steel piping to power the natural gas production process with compressed air via buried semi-flexible tubing.
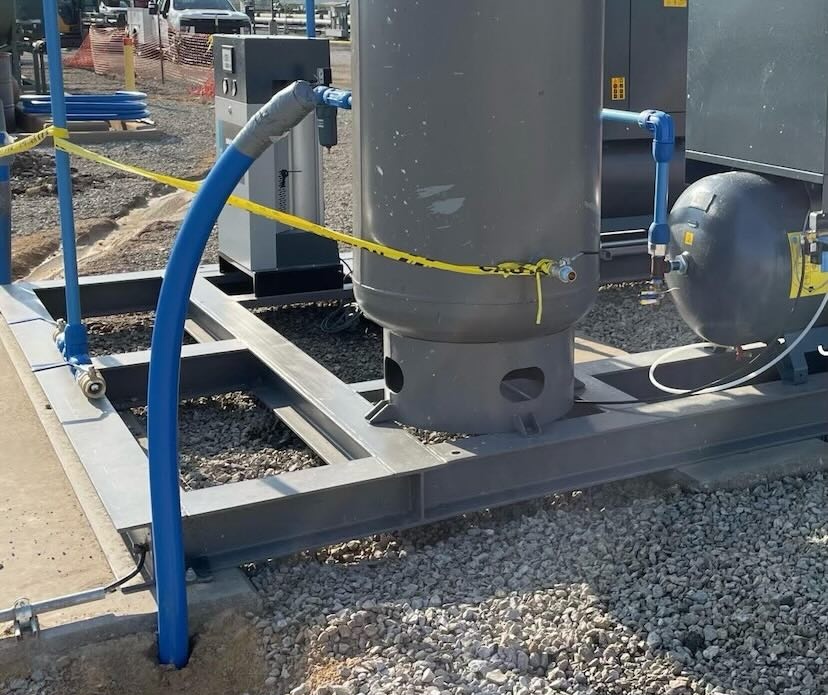
Learning Objectives
- The installation process for buried, semi-flexible piping is faster, less labor intensive and safer than traditional carbon steel pipe.
- Powering midstream pneumatic production via compressed air instead of natural gas means more product to sell and no methane leakage.
- Many organizations throughout North America have implemented this process and realized economic, time-saving and environmental benefits.
Compressed air insights
- Traditional carbon steel piping in midstream pneumatic production slows processes and leaks methane. Shifting to semi-flexible compressed air slashes installation time, emissions, and costs.
- Compressed air technology not only mitigates methane emissions but also ensures cleaner, faster operations, conserving resources and enhancing compliance.
- Despite initial higher costs, semi-flexible compressed air systems pay for themselves within months, offering substantial long-term savings and compliance incentives while boosting productivity.
The oil and gas industry is facing pressure to reduce harmful emissions and operate more efficiently while remaining compliant with ever-stricter environmental regulations. As such, companies need innovative solutions to improve their processes. One area ripe for an upgrade is the traditional use of carbon steel piping to transport pressurized natural gas in midstream pneumatic production. Replacing this system with semi-flexible compressed air piping powered by an air compressor provides a faster, cleaner, and more efficient solution.
Drawbacks of carbon steel piping installation
For decades, midstream pneumatic production has typically relied on natural gas transported through carbon steel piping to power control valves. However, carbon steel is heavy and time-consuming to install and can get very dirty. Threads must be cut or welded manually, and the pipes are thick and bulky, requiring multiple workers to position and connect. Installing carbon steel pipe requires at least seven steps:
-
Using a pipe cutter tool to cut the carbon steel pipe to the required length;
-
Cleaning and inspecting the pipe ends to ensure they’re free of debris, rust or contaminants;
-
Beveling the outside of the pipe ends to ensure strength and safety of the connection;
-
Beveling the inside of the pipe ends to ensure strength and safety of the connection;
-
Threading the pipe ends to accommodate the connection;
-
Manually lifting and placing the pipe ends in alignment;
-
Cut and manually thread the pipe ends together.
Multiply that process many times over to develop a lengthy piece of infrastructure, and you’re left with a time-consuming process. This antiquated process hampers productivity.
Moreover, pressurized natural gas also leaks or vents at various points, resulting in harmful methane emissions. Companies must calculate and report these emissions to comply with Environmental Protection Agency regulations. Not only does this painstaking process monopolize field and engineering resources, but it also results in leaked gas which is wasted product that cannot be sold.

With the Biden Administration championing reduced methane emissions, many oil and gas operations need to curb this waste and leakage to meet these requirements. There has never been a time where methane emissions have been scrutinized with actionable consequences, which is prompting many organizations to look at ways to change their processes.
Benefits of semi-flexible compressed air piping
One solution is using semi-flexible compressed air piping to replace carbon steel pipes. Compressed air is delivered via a surface compressor to buried multilayer pipes with an aluminum core and rugged high density polyethylene (HDPE) outer layer. This provides a direct underground path from the compressor to field equipment.
Installing semi-flexible compressed air pipe is faster with lighter materials and no threading required. In addition, a single worker can handle connections. As per the Methane Guiding Principles partnership, compressed air systems should deliver 1.7 cubic feet per minute (cfm) to each pneumatic controller. This clean compressed air powers valves and equipment instead of leaky, venting natural gas.
With government agencies like the EPA enforcing methane emission regulations, cleaner pneumatic solutions will soon become enforceable via significant fines. Getting ahead of the curve with compressed air not only alleviates reporting requirements, but it helps facilitate compliance. This technology also captures more gas to sell instead of losing it to the atmosphere, further increasing its value proposition.
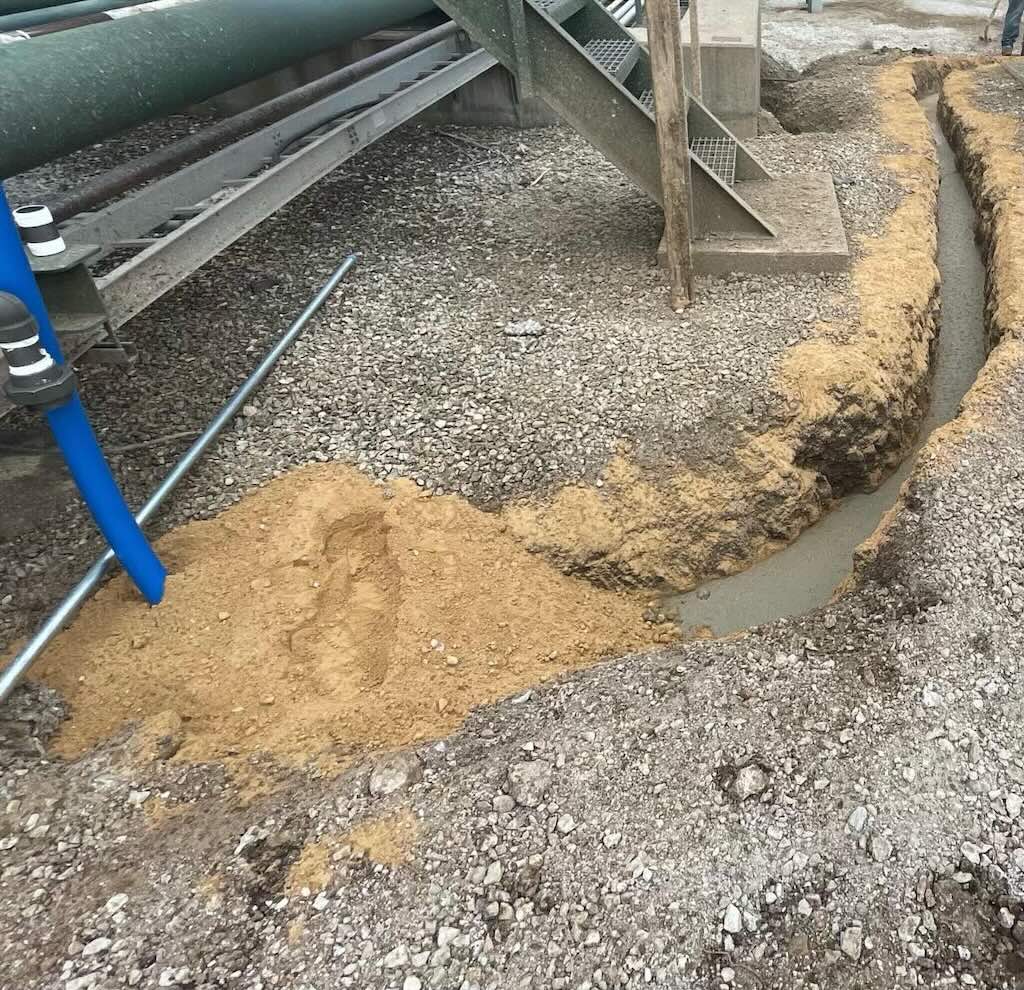
Installation implications for semi-flexible compressed air systems
While carbon steel pipe has been the historical go-to, semi-flexible compressed air piping delivers major advantages. While the upfront material cost is higher due to materials like aluminum and high-density polyethylene, the long-term savings outweigh the initial investment.
Semi-flexible air piping lasts more than twice as long as carbon steel in underground applications — up to 50 years versus 20. The connections are simple compression or press fittings rather than welded or threaded joints. This allows fast installation without power tools or skilled manual labor to thread and weld pipe segments.
Workers can maneuver the flexible, lightweight pipes into position by hand due to the thin aluminum core and plastic exterior. By comparison, thick carbon steel requires heavy machinery to position and insert segments precisely to enable joining. It also poses cumbersome, time-consuming challenges when turns and bends are needed.
Overall, semi-flexible air piping cuts installation time by 50 to 70%. Instead of a week per site, connections take 1-2 days. It’s no secret an extra day on-site with a full crew has major cost implications. With semi-flexible piping, installation time is done in less than half the time. Falling behind schedule can cause ripple-effects that extend far beyond just a day’s work that went on too long. Switching to semi-flexible compressed air piping minimizes the time spent on the job, ensuring schedules stay on-track and goals are delivered upon.
A single worker also can handle the simple compression or press fittings instead of needing multiple welders and threaders. More workers occupied with complex carbon steel installation means fewer workers available to make progress on other important aspects of the job, reducing the chances of coming in on time and on budget.
Organizations are also able to accommodate the installation pivots or adjustments that often occur in the midstream industry due to pipe locations not matching up as planned or proving difficult to locate. Semi-flexible pipe’s increased installation flexibility alleviates the potential for added time and cost.
Semi-flexible compressed air piping savings add up, providing rapid return on investment (ROI) beyond the product price tag.

Environmental and operational implications
Beyond faster installation, powering pneumatic devices with compressed air removes methane emissions associated with natural gas systems. Compressed air is captured within the leak-proof pipe and delivered cleanly to operate valves and equipment. With the aluminum and high-density polyethylene materials, corrosion is also no longer a concern – a significant advantage compared to the steady degradation of carbon steel.
This removal of methane leakage provides substantial climate benefits, as methane has 80 times the warming power of carbon dioxide. Compressed air systems also conserve finite natural gas resources, while reducing air pollution from venting emissions. Switching to compressed air allows operators to maintain familiar pneumatic field devices while transitioning to a cleaner process.
Other advantages include the delivery of contamination-free air to extend equipment life, withstand rugged conditions via buried piping underground, and piping around obstructions due to flexibility. Compressed air piping upgrades midstream production with modern, efficient and environmentally intelligent solutions.
The risks associated with carbon steel piping include corrosion resulting from liquid transfer and oxidation — non-factors with semi-flexible compressed air piping — that can lead to leaks and eventually a system failure. In a midstream natural gas system, equipment failure on this level leads to days wasted and dollars lost. Repair also is more complex and unsafe with the more cumbersome and heavy carbon steel pipe. The end result is more laborers have to take more time in less safe conditions to make things right and return to business as usual.
These risks, combined with the increased longevity of semi-flexible compressed air piping when compared to carbon steel, further strengthens the case to switch to compressed air.
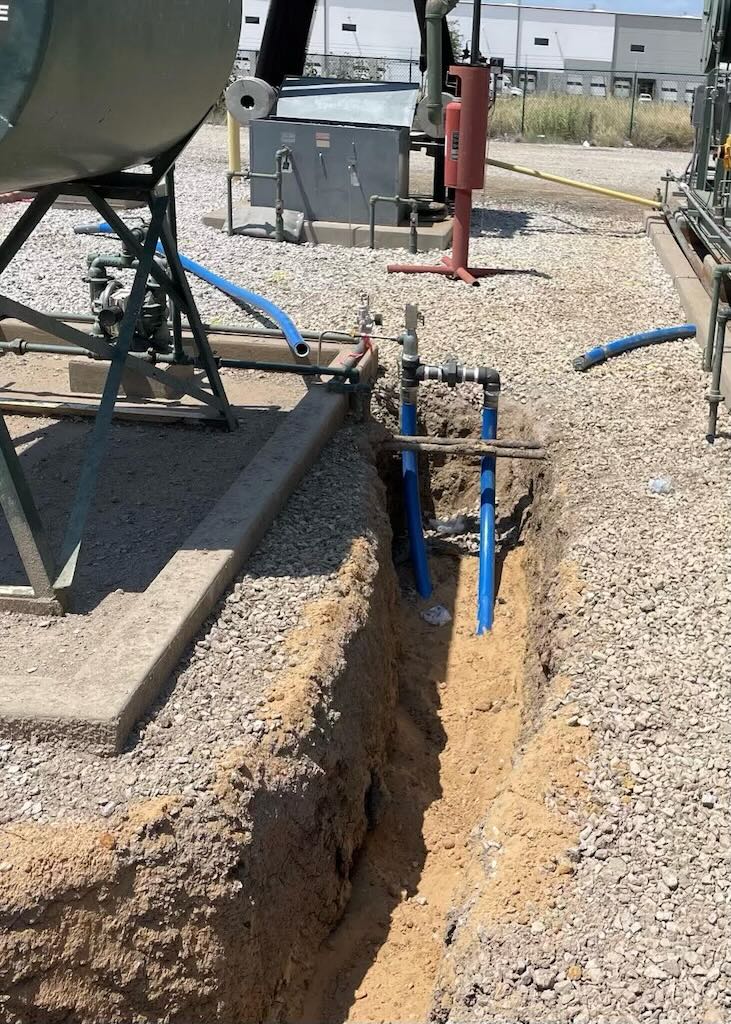
Cost implications and benefits to compressed air systems
The numbers illustrate the value proposition of adopting semi-flexible compressed air systems despite higher upfront costs of materials. According to Natural Gas Star partners, by replacing the natural gas equivalent with systems that provide 60scm to more than 1500 scm per hour of compressed air equivalent of natural gas, priced at $0.25 per scm, compressed air systems can pay for themselves within two to seven months.
In addition, semi-flexible air piping helps organizations qualify for substantial carbon credits by eliminating pneumatic controller emissions. These reduced methane emissions would help each facility earn approximately $100,000+ in carbon credits annually — approximately 33,350 carbon credits per year. When natural gas is no longer lost through leakage, it can be sold instead. Producers also can operate cleaner while increasing field productivity and profits.
Estimated savings reach up to $490,000+ per site when factoring in installation labor, maintenance, methane capture, and regulatory reporting. Over 20 years, the savings could multiply to an estimated $9.8 million with no corrosion maintenance required. With the EPA methane emissions crackdown looming, these systems provide financial and compliance incentives.
The solution in action
Many organizations have realized the advantages of semi-flexible compressed air piping and have implemented the solution across their operations, demonstrating why compressed air systems are the future. They are proving how producers can increase productivity and efficiency while implementing methane-reduction solutions that broaden sustainability commitments across their organizations.
For example, one U.S. natural gas producer switched from carbon steel to compressed air powered by a 2-in. diameter buried semi-flexible pipe. They chose a semi-flexible buried line for its durable HDPE outer wall and efficiency-enhancing aluminum core. Installation was much faster by digging a narrow trench rather than assembling, threading and welding carbon steel sections. This method was much faster, efficient and helped prevent leaks.
Compared to leaky pneumatic valves, their new compressed air system removed methane emissions from the process. It was a clear solution to meet pending EPA regulations and further support ongoing sustainability efforts. The semi-flexible tubing’s leak-proof, underground design withstands site conditions while delivering air securely to equipment. By ditching carbon steel, their methane is now accounted for as captured product to sell rather than as accidental leakage.
Another company converted dozens of sites from pneumatics to compressed air. In addition to saving time and money, the company leveraged these operational changes for inclusion in their annual sustainability reports and environmental, social and governance (ESG) reporting.
Fast, successful fulfillment with less labor
Powering midstream production with compressed air is a sustainable, financially beneficial upgrade to replace dated, inefficient carbon steel piping. As environmental regulations tighten, compressed air allows operators to meet emission targets while capturing more gas to sell. With rapid payback periods, it is a financially astute investment.
Top producers are already adopting this technology for its productivity and compliance benefits. As carbon steel piping’s excessive installation and maintenance demands prove cumbersome, operationally inefficient and taxing on the environment, semi-flexible compressed air piping systems offer the greatest value proposition.
Oil and gas companies can install faster, enhance efficiency, reduce emissions and position themselves ahead of the curve by exploring compressed air.