Eliminating leaks and energy recovery are two good places to start
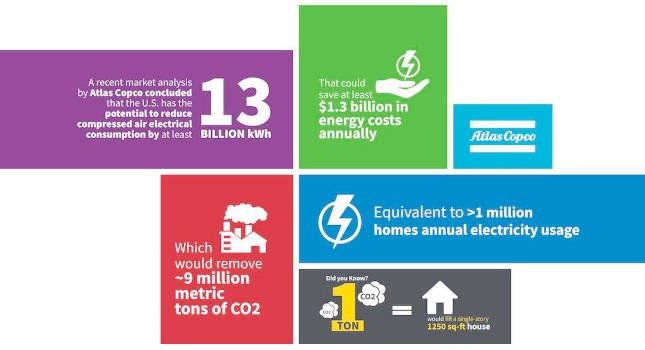
Users of compressed air system in the United States have the means at hand to can save energy costs while supporting sustainability goals, according to a recent report issued by Atlas Copco. Doing so could mean an estimated $1 billion in annual energy savings and nine million less metric tons of CO2 released.
With U.S. headquarters in Auburn Hills, MI, Atlas Copco is a multi-national provider of compressors, vacuum solutions and other type industrial equipment.
The primary avenue for industry to achieve sustainability-based production focuses on reducing electricity consumption to both cut CO2 emissions and generate substantial savings for the enterprises that implement it.
Further, the company believes optimized compressed air can be a big step toward making it happen. Atlas Copco Compressors took a more in-depth look at the U.S. market when it comes to compressed air. The market analysis concluded that U.S. manufacturing has a compressed air installed base of at least 15 million horsepower.
It’s well known that industrial usage of compressed air wastes energy due to air-line leaks that go unattended and for other reasons. Based on looking at various air audits across different customer types, sizes and segments, Atlas Copco Compressor’s analysis concluded that the U.S. could save around 13 billion kWh annually in electricity associated with compressed air — which would save U.S. manufacturers over $1 billion in energy costs annually. As important, this would remove ~9 million metric tons of CO2 annually — equivalent to >1 million homes’ annual electricity usage.
“With our European roots, saving energy has been a long-time concern of ours,” said Robert Eshelman, president and general manager, Atlas Copco Compressors USA. “What we see is an opportunity. There are still many inefficient systems out there. We want our customers to be aware as well.”
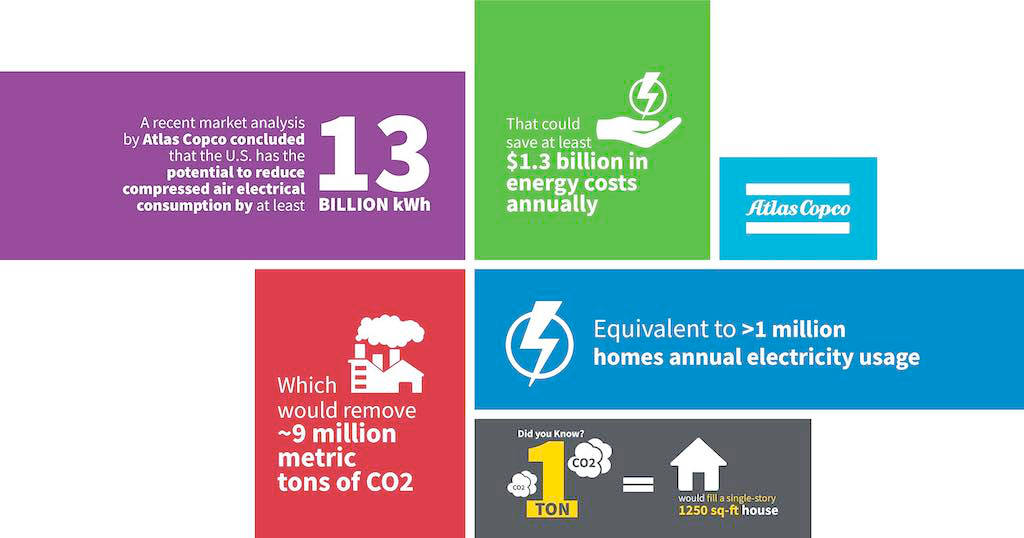
Two good suggestions
In fact, in a 2021 survey regarding compressed air usage of more than 50,000 engineers, contractors and plant personnel throughout the U.S., benchmarking compressed air systems for efficiency tied for second place among respondents’ leading concerns, with 16% ranking it as their top consideration.
The Atlas Copco Compressors repot included information on two additional possible methods for energy savings related to air compressor use. These include energy recovery and switching from a water-cooled to an air-cooled compressor.
An already efficient air compressor system can be improved by utilizing energy recovery modules, which can now also be supplied built into the products. The potential for energy recovery lies in the fact that heat is formed when air is compressed. In most cases, the heat energy is extracted — and becomes waste heat — before the compressed air is distributed into a facility’s pipe system. But substantial amounts of waste heat, even representing as much as 94% of the energy supplied to a compressor, can be recovered via hot air or hot water, depending on whether the unit is air cooled or water cooled.
This can provide a substantial return on investment for companies that capture the heat energy. Further, when energy is recovered via a closed cooling system, it enhances compressor operating conditions, reliability and service life thanks to — among other advantages — an equalized temperature level and high cooling water quality. Most major suppliers with their medium to large compressors now offer adaptations for fitting with standard waste heat recovery equipment.
In addition, in applications where a company can switch from a water-cooled air compressor to an air-cooled compressor, the cooling water used by a water-cooled compressor can be eliminated. A water-cooled, 200-horsepower air compressor could easily use more than seven million gallons of water annually, and with treatment and processes could cost close to $50,000 per year. With air-cooled compressors there is no need for using gallons of water.
Making the switch to an air-cooled compressors eliminates the need for cooling towers and water pumping skids, while eliminating maintenance of auxiliaries used for water.
Of course, water-cooled compressors are essential for certain applications, and there are ways to optimize the process when this is the case.
Back in the U.S.
Here in the United States, to help ensure nationwide energy efficiency in the compressed air industry, the U.S. Department of Energy has established soon-to-be-enforced minimum efficiency standards for compressors.
Set to become mandatory in January 2025, the new regulations were established with input from all major compressor manufacturers. During the three decades starting with the first full year of their enforcement, it’s estimated the updated regulations will deliver a lifetime energy savings of more than 15 billion kilowatt-hours — which equates to the amount of energy needed to power 1.6 million homes for a year.
In 2019, California’s state energy commission set its own new requirements for commercial and industrial air compressors, with the new rules becoming effective in January 2022. The new regulations effectively mimic the previously referenced federal regulations set to be enforced starting in 2025, more quickly setting stricter standards for any large, lubricated, rotary air compressors sold in California.
Of course, water-cooled compressors are essential for certain applications, and there are ways to optimize the process when this is the case.